Traditional DC/DC converters generally use analog control, which has the advantages of small size and low power consumption, but is easily affected by noise. Digitally controlled DC/DC converters are insensitive to process parameters and environment, control algorithms can be implemented through programming, are easy to integrate, and can greatly shorten the product development cycle.
1 DC/DC converter structure
The digital controller is mainly composed of an analog-to-digital converter (ADC), a digital compensator, and a digital pulse width modulator (DPWM). A commonly used digital controller is shown in Figure 1. The output voltage of the main circuit is compared with the reference voltage by the ADC and converted into a corresponding digital error signal. The digital compensator compensates for the error to obtain a given digital signal. The DPWM converts it into a time signal to control the on and off of the main circuit switch.
2 Delay Line ADC
The delay td of a logic gate in a standard CMOS process has the following relationship with the power supply voltage VDD:
Where K is a constant related to the device and process, and Vth is the threshold voltage of the MOS device. When VDD is greater than Vth, td can be regarded as inversely proportional to VDD.
The delay line ADC consists of a delay chain, a register group and a decoding circuit, and the structure is shown in Figure 2. A series of delay units constitute the delay chain. The structure of a feasible delay unit is shown in Figure 3. It is obtained by cascading an inverter and a NOR gate. Each delay unit has an input terminal, a reset terminal and an output terminal.
Given a start signal AD_Stan, a sampling pulse signal sample is generated after a certain time interval as the control signal of the D flip-flop. When the sampling signal is valid, the input signal of the D flip-flop is latched, and the output signal of the D flip-flop is sent to the decoding circuit to obtain the final error signal. Figure 4 is a timing diagram of the delay line ADC, assuming that n=8 in Figure 2. When the sampling signal is valid, the AD_Start signal is transmitted to the fifth delay unit, so q1~q5 outputs are 1, and q6~q8 outputs are 0. The larger the sampling voltage, the smaller the delay time td, the faster the signal propagates, and the more 1s in the output thermometer code. The decoding circuit then converts the thermometer code into the required binary code. The delay line ADC powers the delay chain through the input power supply, and determines the input size according to the delay time of the delay chain.
3 Differential Delay Line ADC
3.1 Differential Delay Line ADC Structure Analysis
The delay line ADC has a simple structure and low power consumption, but is easily affected by the process and temperature environment, and the sampling signal needs to be generated externally, which increases the complexity of the circuit. In addition, the delay of the sampling signal will affect the size of the ADC quantization level, making the system output difficult to stabilize.
The differential delay line structure is an improvement on the delay line structure, and the structure diagram is shown in Figure 5. The differential delay line ADC consists of two identical delay chains, the primary delay chain (Primary delay-line) and the reference delay chain (Reference delay-line). The reference delay chain can be copied from the primary delay chain. The two differential delay chains share a start signal AD_Start, so that the working states of the two delay chains are exactly the same. The two inputs of the differential delay chain are the sampling voltage Vsense and the reference.
The voltage Vref and Vsense must be less than Vref. According to the principle that the larger the voltage, the smaller the delay, the reference delay chain is propagated before the main delay chain. The D flip-flop connected to the main delay chain is turned on to sample the Vsense on the main delay chain. In this way, the sampled voltage is compared with the reference voltage, and the digital error signal required by the system is obtained through the decoding circuit.
The control signal of the differential delay line ADC is generated internally, which further simplifies the circuit structure. The differential input makes the sampling voltage and the reference voltage simultaneously affected by temperature and process deviation, reducing the delay deviation of the main delay chain.
3.2 Differential Delay Line ADC Modeling
Assume the number of delay units in the delay chain is N, and the delay time td is a function of VDD: td=td(VDD), then
That is, the conversion time Tc is a function of the resolution Vq, the delay time td and the slope of the delay function.
FIG6 is a curve showing the relationship between a single delay unit and VDD in a 0.13 μm CMOS process.
4 Design Method and Simulation Results
The delay unit has high requirements on precision and adopts a fully customized design, while the decoding circuit has low requirements on precision and adopts a design based on standard library units. The overall circuit uses Hsim for mixed analog-digital simulation.
During the design, the reference voltage is 1.5V, the operating frequency is 1.5MHz, the input voltage rises linearly from 0.7 to 1.5V, and the output is the decoded result, that is, the 6-bit digital signal e. For every 12.5mV increase or decrease in Vsense, e increases or decreases by "1", but the maximum value of e is 63. Figure 7 shows the input and output curves of the differential delay line ADC under the 0.13μm CMOS process. It can be seen that the output of the differential delay line ADC has no obvious offset, zero input corresponds to zero output, and the linearity is good.
5 Conclusion
The differential delay line ADC circuit has a simple structure, does not require an external circuit to generate a control signal, and can offset some process deviations. The ADC has a fast conversion rate and low power consumption, and is suitable for use in high-frequency digital DC/DC converters.
Previous article:Research on 28V DC input overvoltage surge circuit suppression method
Next article:A New Solution for Regulating Voltage Value in Digital Control DC Stabilized Power Supply
Recommended ReadingLatest update time:2024-11-16 20:40
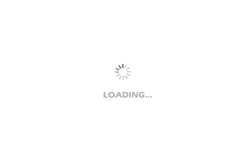
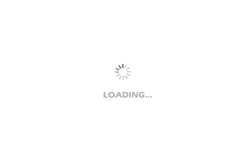
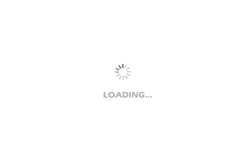
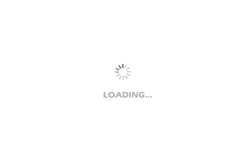
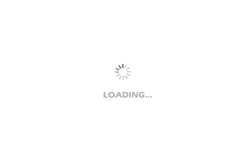
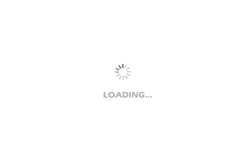
- Popular Resources
- Popular amplifiers
-
西门子S7-12001500 PLC SCL语言编程从入门到精通 (北岛李工)
-
New Energy Vehicle Detection and Diagnosis Experiment (Edited by Mao Caiyun, Zhou Xien, and Long Jiwen)
-
Virtualization Technology Practice Guide - High-efficiency and low-cost solutions for small and medium-sized enterprises (Wang Chunhai)
-
ESP32-S3 source code
- MathWorks and NXP Collaborate to Launch Model-Based Design Toolbox for Battery Management Systems
- STMicroelectronics' advanced galvanically isolated gate driver STGAP3S provides flexible protection for IGBTs and SiC MOSFETs
- New diaphragm-free solid-state lithium battery technology is launched: the distance between the positive and negative electrodes is less than 0.000001 meters
- [“Source” Observe the Autumn Series] Application and testing of the next generation of semiconductor gallium oxide device photodetectors
- 采用自主设计封装,绝缘电阻显著提高!ROHM开发出更高电压xEV系统的SiC肖特基势垒二极管
- Will GaN replace SiC? PI's disruptive 1700V InnoMux2 is here to demonstrate
- From Isolation to the Third and a Half Generation: Understanding Naxinwei's Gate Driver IC in One Article
- The appeal of 48 V technology: importance, benefits and key factors in system-level applications
- Important breakthrough in recycling of used lithium-ion batteries
- Innolux's intelligent steer-by-wire solution makes cars smarter and safer
- 8051 MCU - Parity Check
- How to efficiently balance the sensitivity of tactile sensing interfaces
- What should I do if the servo motor shakes? What causes the servo motor to shake quickly?
- 【Brushless Motor】Analysis of three-phase BLDC motor and sharing of two popular development boards
- Midea Industrial Technology's subsidiaries Clou Electronics and Hekang New Energy jointly appeared at the Munich Battery Energy Storage Exhibition and Solar Energy Exhibition
- Guoxin Sichen | Application of ferroelectric memory PB85RS2MC in power battery management, with a capacity of 2M
- Analysis of common faults of frequency converter
- In a head-on competition with Qualcomm, what kind of cockpit products has Intel come up with?
- Dalian Rongke's all-vanadium liquid flow battery energy storage equipment industrialization project has entered the sprint stage before production
- Allegro MicroSystems Introduces Advanced Magnetic and Inductive Position Sensing Solutions at Electronica 2024
- Car key in the left hand, liveness detection radar in the right hand, UWB is imperative for cars!
- After a decade of rapid development, domestic CIS has entered the market
- Aegis Dagger Battery + Thor EM-i Super Hybrid, Geely New Energy has thrown out two "king bombs"
- A brief discussion on functional safety - fault, error, and failure
- In the smart car 2.0 cycle, these core industry chains are facing major opportunities!
- The United States and Japan are developing new batteries. CATL faces challenges? How should China's new energy battery industry respond?
- Murata launches high-precision 6-axis inertial sensor for automobiles
- Ford patents pre-charge alarm to help save costs and respond to emergencies
- New real-time microcontroller system from Texas Instruments enables smarter processing in automotive and industrial applications
- Soldering example of SMA coaxial connector to PCB board
- 100% duty design of buck chip
- Image Processing Based on FPGA
- Limited time download gift: "What you need to know about USB3.1"
- Bluetooth host and slave address mutual binding communication test
- [Evaluation and experience of Zhongke Yihaiwei EQ6HL45 development platform] + ip_pll routine and eLinx software debugging
- Let’s discuss the development trend and direction of RF GaN
- Today's live broadcast prize addition: Introduction to Keysight's new optical communication test solution
- Chat with Vicor engineers about how to improve throughput and uptime of automated test equipment?
- Questions about the waveform generated by amplitude modulation by AD9106