introduction
Due to the oil crisis and increasingly serious environmental pollution, the development of electric vehicles has become an inevitable trend. Batteries provide power for electric vehicles, and the charging performance of batteries directly affects the use and life of batteries. Batteries are generally divided into lead-acid batteries, nickel-cadmium batteries, nickel-metal hydride batteries and lithium-ion batteries. Due to the wide variety of batteries and different capacities, batteries of different types and capacities often require different chargers to match. If the battery chargers are not well matched, unsafe phenomena such as overcharging and overheating will occur, thereby affecting the normal use of the battery and shortening the battery life. Therefore, it is very necessary to design a multifunctional charging system based on single-chip microcomputer control that can charge various types of batteries. The multifunctional charging system can quickly and stably charge batteries of different types and capacities. We have designed corresponding charging methods for different types of batteries in the software, so that each battery can be charged under the best charging method. For batteries of different capacities, when choosing a good charging method, you only need to set the charging parameters to charge the battery quickly and stably.
1 Hardware Circuit Design
This system adopts a phase-shifted full-bridge soft switching circuit, that is, the Boost circuit and the full-bridge converter are combined to form a single-stage PFC circuit. The circuit has a simple structure and high efficiency. It can realize the adjustment of the input current and can work in higher power occasions, giving full play to the advantages of the full-bridge circuit.
The system is mainly composed of a charging main circuit and a charging control circuit. Figure 1 is a hardware schematic diagram of the multifunctional charging system.
1.1 System Working Principle
This design uses switching power supply technology with a maximum power of 3500W. First, the 220V single-phase industrial frequency AC power is rectified by a full-bridge circuit composed of 4 diodes, and then filtered by a large capacitor to obtain a DC power of about 300V. At this time, the ripple in the DC power is relatively large. The DC power passes through a full-bridge inverter composed of 4 insulated gate bipolar transistors (IGBTs) to obtain a high-frequency AC power with adjustable voltage, which is coupled to the secondary side through a high-frequency transformer, and then rectified by a full bridge. Finally, it is filtered by an inductor and capacitor to obtain a DC power with very small ripple to charge the battery. The multifunctional charging system can charge different types of batteries and batteries with different capacities. The charging voltage and current during the charging process are controlled in real time by a single-chip microcomputer. The entire charging system is a feedback control system. The single-chip microcomputer monitors the entire charging process by real-time detection of the current, voltage and temperature during the charging process, effectively avoiding overcurrent, overvoltage and overheating during the charging process, so that the charging process is safe and stable.
The air switch before the inverter bridge is to prevent short circuit or high current from damaging the battery or electronic devices. The microcontroller detects the charging current, voltage and temperature and compares them with the set values before charging, and controls the output of 4 PWM waves to the gates of 4 IGBTs, thereby controlling the on-off time of the collector to emitter current to achieve the purpose of controlling the output voltage.
Since IGBT needs to be isolated and driven, this design uses Mitsubishi's IBGT dedicated driver chip M57962L. Figure 2 is its application circuit.
Since four IGBTs are selected to form a full-bridge inverter, each IGBT needs an M57962L chip to drive it, and each M57662L chip requires three voltage levels, namely 15V, l0V, and 5V to power it. The 5V voltage also powers the MC9S12XS128 microcontroller. This paper designs a 50W transformer to power the microcontroller and four M57962L chips. Its secondary winding outputs three groups of voltages. After rectification, filtering and voltage stabilization, the three required voltages are obtained.
1.2 Charging Control Circuit
Freescale MC9S12XS128 microcontroller is selected as the control core for data acquisition and control. It has an internal data memory of 8KB, a program memory of 128KB, 2 SCI, 1 SPI, 1 IIC, 1 CAN, 16-channel A/D, 8-channel PWM, and 8-channel ECT modules. Its operating frequency is 80MHz, and its operation speed is fast, and its processing capacity is greatly improved. The chip integrates 16-channel 12-bit high-precision A/D converters, which can directly detect the charging voltage, current and temperature of the battery. The 8-channel PWM can be directly output to the M57962L chip to control the on and off of the IGBT, simplifying the design of the microcontroller peripheral circuit.
1.2.1 Voltage Detection
This system uses a resistor voltage divider structure, which is connected in parallel in the charging circuit to monitor the voltage signal. The voltage signal is transmitted from the PAD0 port to the microcontroller through the microcontroller's built-in A/D converter for processing. This structure can automatically select the corresponding range detection voltage according to the actual voltage outside, so that the smaller the voltage, the higher the detected voltage accuracy, which helps to more accurately control the change of charging voltage during the charging process.
1.2.2 Current Detection
This system uses a Hall-type current sensor to detect the charging current signal, and after a certain conversion process, transmits the detected current signal from the PAD1 port to the microcontroller through the microcontroller's built-in A/D converter for processing. The sensor has high precision and can accurately detect changes in the charging current of 0.1A.
1.2.3 Temperature detection
This system uses a thermistor to detect the battery temperature signal during the charging process. In actual application, the thermistor is attached to the battery to detect the battery temperature. The thermistor can accurately detect the change in battery temperature during the charging process. The temperature signal is transmitted to the microcontroller through the PAD2 port for processing to prevent the battery from overheating during the charging process, so that the charging process can be carried out smoothly and safely.
1.2.4 LCD Module
This system uses a 12864 LCD screen with a Chinese character library, and the LCD screen module is connected to the PA and PB ports of the microcontroller.
It can display the charging voltage, charging current, terminal voltage and temperature of the battery in real time during the charging process, and can display the calendar, duty cycle of 4-channel PWM waves, etc. when idle.
1.2.5 Key Input
A 4x4 matrix keyboard is used. By pressing the buttons, you can switch to the battery charging method selection, charging parameter setting, calendar adjustment, 4-way PWM wave duty cycle display, charging voltage, charging current, battery terminal voltage and temperature display and other interfaces.
1.2.6 PWM Output
The output frequency of PWM is determined by the high-frequency AC alternating cycle set by a timer/counter. The PWM waveform of this system uses the left-aligned method. The duty cycle of each PWM channel is: [(PWMPERx-PWMDTYx)/PWMPERx]×100%, where PWMPERx represents the PWM channel register and PWMDTYx represents the PWM channel duty cycle register.
2 Software Design
The system software of the multifunctional charging system is written in C language and written into the internal program memory of the microcontroller after assembly, simulation and debugging, so as to realize the hierarchical structure and modular functions of the system software, and the readability, maintainability and scalability of the software are strong.
The multifunctional charging system is designed with corresponding charging methods for different types of batteries. The software mainly consists of initialization, battery quality detection before charging, charging stage and charging protection.
This system mainly uses lithium iron phosphate for testing. Its charging stage consists of three parts: low current charging stage, constant current charging stage, and constant voltage charging stage. Its program flow chart is shown in Figure 3.
Charging stage: After the battery detection program is completed, the battery starts to be charged with a small current, and the charging rate is about 1/5C; when the small current is charged until the battery voltage reaches the reference value, the system enters the constant current charging stage, which is the fast charging stage of the battery, and the charging rate is 1-2C; when the charging voltage reaches the set maximum charging voltage of the battery, the system enters the constant voltage charging stage, and as the battery voltage gradually rises, the charging current gradually decreases; when the charging current decreases to the set reference value, the system determines that the battery is sufficient and stops charging.
Charging protection part: During the charging process, the battery voltage is constantly monitored to see if it exceeds the safety value, and the temperature or temperature change rate reaches the limit value. If the above situation occurs, charging will be terminated immediately. The battery voltage is detected to prevent lithium-ion batteries and lead-acid batteries from overcharging, and the temperature and temperature change rate are detected to see if they reach the limit value to prevent nickel-metal hydride and nickel-cadmium batteries from overcharging.
The above charging stages are designed for lithium-ion batteries. In practice, lithium iron phosphate battery packs are mainly used for experiments. For other types of batteries, corresponding charging methods are set in the software: the charging stage of lead-acid batteries is the same as that of lithium-ion batteries, that is, first pre-charge with a small current, then charge with a constant current, and finally charge with a constant voltage. When the constant-voltage charging current is small to a certain extent, the system determines that the battery is sufficient and stops charging; for nickel-cadmium batteries, first pre-charge with a small current, then charge with a fast constant current. When the battery voltage drops for the first time, the system determines that the battery is sufficient and stops charging; for nickel-metal hydride batteries, first pre-charge with a small current, then charge with a fast constant current. When the battery voltage shows zero growth, the battery is determined to be sufficient and stops charging.
Lead-acid batteries and lithium-ion batteries have low self-discharge rates, and charging can be stopped directly after the battery is fully charged. NiMH and NiCd batteries have high self-discharge rates. If they are unattended for charging at night, trickle charging can be used to replenish the battery after the battery is fully charged to keep the battery fully charged.
3 Conclusion
The experimental results show that the designed multifunctional charging system can work normally, the output DC voltage is stable and the ripple is small, the charging process control precision is high, it can charge various types of batteries quickly and stably, and stop charging in time after the battery is fully charged, which has practical application and promotion value.
Previous article:A PFC converter input voltage feedforward control method
Next article:【Photovoltaic Technology】High-efficiency crystalline silicon cell technology-surface passivation
Recommended ReadingLatest update time:2024-11-16 15:20
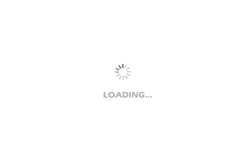
- MathWorks and NXP Collaborate to Launch Model-Based Design Toolbox for Battery Management Systems
- STMicroelectronics' advanced galvanically isolated gate driver STGAP3S provides flexible protection for IGBTs and SiC MOSFETs
- New diaphragm-free solid-state lithium battery technology is launched: the distance between the positive and negative electrodes is less than 0.000001 meters
- [“Source” Observe the Autumn Series] Application and testing of the next generation of semiconductor gallium oxide device photodetectors
- 采用自主设计封装,绝缘电阻显著提高!ROHM开发出更高电压xEV系统的SiC肖特基势垒二极管
- Will GaN replace SiC? PI's disruptive 1700V InnoMux2 is here to demonstrate
- From Isolation to the Third and a Half Generation: Understanding Naxinwei's Gate Driver IC in One Article
- The appeal of 48 V technology: importance, benefits and key factors in system-level applications
- Important breakthrough in recycling of used lithium-ion batteries
- Innolux's intelligent steer-by-wire solution makes cars smarter and safer
- 8051 MCU - Parity Check
- How to efficiently balance the sensitivity of tactile sensing interfaces
- What should I do if the servo motor shakes? What causes the servo motor to shake quickly?
- 【Brushless Motor】Analysis of three-phase BLDC motor and sharing of two popular development boards
- Midea Industrial Technology's subsidiaries Clou Electronics and Hekang New Energy jointly appeared at the Munich Battery Energy Storage Exhibition and Solar Energy Exhibition
- Guoxin Sichen | Application of ferroelectric memory PB85RS2MC in power battery management, with a capacity of 2M
- Analysis of common faults of frequency converter
- In a head-on competition with Qualcomm, what kind of cockpit products has Intel come up with?
- Dalian Rongke's all-vanadium liquid flow battery energy storage equipment industrialization project has entered the sprint stage before production
- Allegro MicroSystems Introduces Advanced Magnetic and Inductive Position Sensing Solutions at Electronica 2024
- Car key in the left hand, liveness detection radar in the right hand, UWB is imperative for cars!
- After a decade of rapid development, domestic CIS has entered the market
- Aegis Dagger Battery + Thor EM-i Super Hybrid, Geely New Energy has thrown out two "king bombs"
- A brief discussion on functional safety - fault, error, and failure
- In the smart car 2.0 cycle, these core industry chains are facing major opportunities!
- The United States and Japan are developing new batteries. CATL faces challenges? How should China's new energy battery industry respond?
- Murata launches high-precision 6-axis inertial sensor for automobiles
- Ford patents pre-charge alarm to help save costs and respond to emergencies
- New real-time microcontroller system from Texas Instruments enables smarter processing in automotive and industrial applications
- Theoretical speed calculation of WiFi protocols
- BQ76930: Design help needed for BQ76930 based BMS
- Application of the concepts of virtual short and virtual disconnect in operational amplifiers in actual product circuits
- What is the application of PWM
- Guess the questions in the electronic competition and win prizes!
- MSP430f5529
- What is Full SRT?
- Introduction to MSP430 development tools (JTAG SBW BS)
- The experiment got me all greasy:lol
- EEWORLD University Hall----Live Replay: Supporting 'Dual Carbon' - ADI Smart Factory Solution