Taking the Buck PWM DC/DC converter as an example, the working principle of the PWM DC/DC converter is introduced.
The working principle of the Buck PWM DC/DC converter in continuous conduction mode (COM) can be illustrated as shown in Figure 2 (a): In one switching cycle, the switching process of the switch tube chops the DC input voltage u to form a square wave with a pulse width of TON (Ton is the switch tube conduction time). When the switch tube is turned on, the diode is turned off, and the input DC power supply Ui transfers power to the negative
The load is connected to the inductor, and the inductor stores energy (the inductor current increases); when the switch is turned off, the diode conducts and the energy stored in the inductor is released to the load (the inductor current decreases). In one switching cycle, the average value of the inductor current is equal to the load current r. (The ESR of the filter capacitor C is ignored). The same method can be used to analyze the working principle of Boost, Buck-BccGt PWM BC/DC converters.
The output/input voltage conversion ratio of the PWM DC/DC converter operating in CCM mode is derived below. The starting point is that in steady-state operation, the volt-second area of the switch tube during the on and off time is balanced within one switching cycle of the PWM DC/DC converter, that is, the integral of the voltage borne by the inductor over time within one switching cycle is zero:
Where uL is the voltage that the inductor bears;
Ts——switching period;
Where fa is the switching frequency;
Ton, Toff - the on-time and off-time of the switch tube in one switching cycle.
Duty Cycle Ratio or conduction ratio:
Taking the CCM Buck PWM DC/DC converter as an example, as shown in Figure 2 (a), we can get
Ui and Uo are the input voltage and output voltage of the Buck PWM DC/DC converter respectively.
From formula (2-1), we get
or (Ui-Uo)Ton=UoToff
(Ui-Uo)DuTs=Uo(1-Du)Ts
Therefore, the conversion ratio of the output/input voltage of the Buck PWM DC/DC converter working in COM mode is
Uo/Ui=Du
The duty cycle Du is always less than 1, so the Buck converter is a step-down converter. The efficiency of the ideal Buch converter is 1, so it can be considered
Ui/Ii=UoIo
From formula (2-2) and formula (2-3), we can get
Io/Ii=1/DU
It can be seen that the Buck converter is a current-boosting converter, and Io and Ii represent the average output current and input current of the PWM converter respectively.
Using the same method, it can be deduced that the output/input voltage conversion ratios of the Boost and Buck-Boost PWM DC/DC converters operating in COM mode are
Uo/Ui=1/(1-Du)
Buck-Boost PWM DC/DC Converter
Uo/Ui=Du/(1-Du)
From equations (2-5) and (2-6), we can see that the Boost converter is a step-up converter, which proves that the ideal Boost converter is a step-down converter. The Buck-Boost converter is a step-up/step-down converter. Whether it is step-up or step-down depends on the duty cycle Du. When Du>0.5, Du/(1-Du)>1, the Buck Boost converter is a step-up converter. When Du<0.5, Du/(1-Du)<1, it is a step-down converter.
In DCM mode, the output/input voltage conversion ratio of Buck, Boost, and Buck-Boost converters is different from that of Equation (2-2), Equation (2-5), and Equation (2-6). They can be obtained using the same method, but the calculation process is more complicated.
Buck, Boost, and Buck Boost PWM DC/DC converters are the most basic circuits (Basic topological configuration) of PWM DC/DC converters. Other forms of PWM DC/DC converter circuits can be derived from these three basic circuits.
Previous article:Active Clamp Forward Converter
Next article:Equivalent circuit of PWM DC/DC converter
Recommended ReadingLatest update time:2024-11-17 01:55
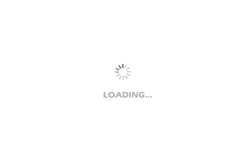
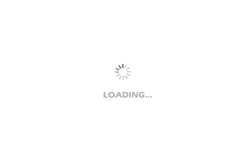
- Popular Resources
- Popular amplifiers
-
西门子S7-12001500 PLC SCL语言编程从入门到精通 (北岛李工)
-
Small AC Servo Motor Control Circuit Design (by Masaru Ishijima; translated by Xue Liang and Zhu Jianjun, by Masaru Ishijima, Xue Liang, and Zhu Jianjun)
-
New Energy Vehicle Detection and Diagnosis Experiment (Edited by Mao Caiyun, Zhou Xien, and Long Jiwen)
-
Virtualization Technology Practice Guide - High-efficiency and low-cost solutions for small and medium-sized enterprises (Wang Chunhai)
- MathWorks and NXP Collaborate to Launch Model-Based Design Toolbox for Battery Management Systems
- STMicroelectronics' advanced galvanically isolated gate driver STGAP3S provides flexible protection for IGBTs and SiC MOSFETs
- New diaphragm-free solid-state lithium battery technology is launched: the distance between the positive and negative electrodes is less than 0.000001 meters
- [“Source” Observe the Autumn Series] Application and testing of the next generation of semiconductor gallium oxide device photodetectors
- 采用自主设计封装,绝缘电阻显著提高!ROHM开发出更高电压xEV系统的SiC肖特基势垒二极管
- Will GaN replace SiC? PI's disruptive 1700V InnoMux2 is here to demonstrate
- From Isolation to the Third and a Half Generation: Understanding Naxinwei's Gate Driver IC in One Article
- The appeal of 48 V technology: importance, benefits and key factors in system-level applications
- Important breakthrough in recycling of used lithium-ion batteries
- Innolux's intelligent steer-by-wire solution makes cars smarter and safer
- 8051 MCU - Parity Check
- How to efficiently balance the sensitivity of tactile sensing interfaces
- What should I do if the servo motor shakes? What causes the servo motor to shake quickly?
- 【Brushless Motor】Analysis of three-phase BLDC motor and sharing of two popular development boards
- Midea Industrial Technology's subsidiaries Clou Electronics and Hekang New Energy jointly appeared at the Munich Battery Energy Storage Exhibition and Solar Energy Exhibition
- Guoxin Sichen | Application of ferroelectric memory PB85RS2MC in power battery management, with a capacity of 2M
- Analysis of common faults of frequency converter
- In a head-on competition with Qualcomm, what kind of cockpit products has Intel come up with?
- Dalian Rongke's all-vanadium liquid flow battery energy storage equipment industrialization project has entered the sprint stage before production
- Allegro MicroSystems Introduces Advanced Magnetic and Inductive Position Sensing Solutions at Electronica 2024
- Car key in the left hand, liveness detection radar in the right hand, UWB is imperative for cars!
- After a decade of rapid development, domestic CIS has entered the market
- Aegis Dagger Battery + Thor EM-i Super Hybrid, Geely New Energy has thrown out two "king bombs"
- A brief discussion on functional safety - fault, error, and failure
- In the smart car 2.0 cycle, these core industry chains are facing major opportunities!
- Rambus Launches Industry's First HBM 4 Controller IP: What Are the Technical Details Behind It?
- The United States and Japan are developing new batteries. CATL faces challenges? How should China's new energy battery industry respond?
- Murata launches high-precision 6-axis inertial sensor for automobiles
- Ford patents pre-charge alarm to help save costs and respond to emergencies
- USB OTG connection method
- Have you been affected by the price increase? Share the best pin-compatible alternative solution under the wave of price increase#, a certain brand?
- Request: DC-DC small package chip similar to LM2596
- What is the reason! Another wind turbine fire accident! And caused a ground wildfire
- 【Iprober 520 current probe】Practical use in motor control
- Can you please help me find out where is the problem with the program?
- What are the basic units of Weber Wb and Tesla T?
- How to add c files in esp32 idf components to compile
- Have you noticed the LPDSP32 audio codec inside RSL10? Does your project use this resource?
- Will the push-pull circuit be straight through?