OLED is regarded as the next generation of display technology. It has been applied in small-size fields such as mobile phones, and is ready to be applied in TVs. Since OLED is the focus of attention, do you know enough about OLED? Whether the answer is yes or no, I hope you can read this article carefully, and I believe it will give you a deeper understanding of OLED.
The father of OLED is a Chinese scientist
Since there are not many reports on the history of OLED, and most of the OLED products in recent years have been launched by Japan and South Korea, such as Sony's 11-inch OLED TV XEL-1 in 2007 and Samsung and LG's 55-inch OLED TVs at CES 2012, everyone seems to think that OLED was invented by the Japanese. In fact, the father of OLED is Chinese-American scientist Dr. Ching-Yun Deng.
Dr. Ching-Wan Tang was born in Hong Kong in 1947. He received his Bachelor of Science degree in Chemistry from the University of British Columbia in 1970 and his PhD in Physical Chemistry from Cornell University in 1975. He then became a research scientist at Kodak Research Laboratories in Rochester, New York, and began his career in the development of organic semiconductor materials and electronic applications. In 2006, Dr. Ching-Wan Tang was elected a member of the National Academy of Engineering for his pioneering achievements in organic light-emitting diodes and heterojunction organic solar cells. In 2011, Professor Tang, together with Professor Stuart Rice of the University of Chicago and Professor Krzysztof Matjazewski of Carnegie Mellon University, received the Wolf Prize in Chemistry from the Wolf Foundation, an international award second only to the Nobel Prize in chemistry.
Most scientific discoveries start with unexpected small events, and the discovery of OLED is no exception. One night in 1979, Dr. Qingyun Deng, a Chinese scientist working in scientific research at Kodak, suddenly remembered that he had forgotten something in the laboratory on his way home. When he returned to the laboratory, he found an organic battery used in the experiment glowing in the dark! This unexpected surprise marked the beginning of the birth of OLED, and Dr. Deng was therefore called the "Father of OLED."
"Father of OLED"——Chinese-American scientist Dr. Ching-Yun Deng
In the early days of OLED, organic electroluminescent technology was stuck at high driving voltage, low brightness, and low efficiency. These difficulties made OLED impractical, which led to a lack of attention for OLED research. It was not until 1987 that Dr. Qingyun Deng and others from Kodak invented a multi-layer OLED component made by vacuum evaporation, which greatly improved the performance of the component. Its commercial application potential with low operating voltage and high brightness attracted global attention.
In 1990, Burroughes, Friend and others from Cambridge University in the UK found that the conductive polymer material PPV has good electroluminescence properties, and successfully developed a coating method to apply the polymer material to OLED to make a polymer OLED device, namely Polymer LED, also known as PLED. Since the thermal stability, flexibility and mechanical processing properties of polymer materials are superior to those of organic small molecule materials, and the device manufacturing process is simpler, polymers are gradually becoming a new research hotspot in the field of organic EL.
PLED
In 1992, Heeger and others invented the first flexible display using plastic as a substrate, showing the most fascinating side of organic electroluminescent displays to people. In 1997, Forrest and others discovered the phenomenon of phosphorescent electroluminescence, breaking the limit of organic electron light quantum efficiency of less than 25%. Since then, OLED technology has bid farewell to the stage dominated by basic scientific research and entered a period dominated by commercial applications.
Philips Fluid concept OLED phone
The full name of OLED is Organic Light-Emitting Diode, also known as Organic Electroluminesence Display (OELD) in some foreign countries. Unlike traditional LCD display, it does not require a backlight and has the characteristics of self-luminescence. It uses a very thin organic material coating and a glass substrate. When current passes through, these organic materials will emit light. In addition, OLED display screens can be made lighter and thinner, with a wider viewing angle, and can significantly save electricity.
OLED technology has been developed to a great extent, but their structures are similar and relatively simple. To illustrate the structure of OLED, each OLED unit can be compared to a hamburger, and the luminescent material is the vegetable in the middle. Each OLED display unit can produce three different colors of light in a controlled manner.
OLED structure
According to the light-emitting material, it can be divided into low-molecular OLED (Japanese companies have mastered the core technology, which is easier to colorize) and high-molecular OLED (the core technology is mastered by the British CDT company); according to the driving method, OLED can be divided into passive drive OLED (PM-OLED) and active drive OLED (AM-OLED); according to the substrate material, the substrate material of OLED can be divided into glass, plastic and metal film, etc. Plastic and metal film are mainly used to manufacture flexible OLED.
OLED is mainly classified by driving technology
Among the many classifications, one of the most important classification methods is based on different driving technologies. In active mode, there is a thin film transistor (TFT) behind the OLED unit, and the light-emitting unit is lit under the drive of TFT. In passive mode, the unit selected by the row and column address is lit. In active mode, there is a thin film transistor (TFT) behind the OLED unit, and the light-emitting unit is lit under the drive of TFT. Active OLED should save power and have better display performance than passive OLED.
OLED production line is the most expensive but the theoretical cost is low
OLED production line investment is the most expensive, which is probably what everyone can guess. Indeed, it is not only higher than CRT, plasma, but also higher than LCD display technology. We know that LG's largest investment project in China is LGD Guangzhou 8.5-generation LCD panel line, with an investment of up to US$4 billion, but the investment in OLED production line of the same scale may be as high as more than US$5 billion. The main reason for its high cost is the difficulty of the production process - OLED technology is mainly composed of solid materials, and the coating of these materials must be carried out in liquid, dissolved or vaporized state.
OLED production line investment is the most expensive
Although the production line is the most expensive, this is the calculation of rebuilding, while the OLED production line can be transformed from the LCD panel production line, so its overall industry investment is almost the lowest. If an almost complete 8.5-generation LCD production line is converted to produce OLED panels, the investment is usually more than US$2 billion, which is much lower than the investment of a new 8.5-generation LCD panel line.
Samsung OLED panel
In addition, as mentioned above, the structure of OLED is relatively simple, much simpler than that of LCD. This shows that if OLED display technology is applied on a large scale, it will inevitably show certain advantages in cost. In fact, in theory, OLED display technology may also be the lowest cost display device so far.
Compared with LCD, the cost of OLED is relatively low. First, LCD requires a light source system, including light-emitting devices, driving circuits and light guide plates, while OLED does not. Second, the packaging of liquid crystal needs to consider the characteristics of liquid materials, such as fluidity and unsupportability, while OLED does not have these problems. The most controversial is the coating of materials. With the development of OLED technology and material applications, its cost will never be significantly higher than that of LCD products.
OLED has a simple structure and has certain cost advantages
From a comprehensive perspective, theoretically, OLED products have certain cost advantages when they are mass-produced. Of course, OLED is still in its early stages and the cost is still quite high, so we hear that the price of a 55-inch TV will be as high as 70,000 yuan.
Development status of OLED in China and abroad
At present, it can be said that large-size OLED is still in its infancy, and large-size products have only been launched in the last two or three years. However, we can foresee that after 2012, both large-size and small-size OLED will show explosive growth.
In terms of small size (mobile phones, tablets, etc.), OLED display technology has been widely used and is relatively mature. It has great advantages in color, contrast, viewing angle, etc., and consumers are more inclined to OLED products when purchasing. In terms of large size (TV, etc.), Samsung and LG have demonstrated 55-inch OLED at CES2012, and it is said that it will be launched in the second half of this year. These OLED screens will be produced from the new 8.5-generation line, which can meet the production needs of any display product size within 100 inches.
Samsung 55-inch OLED TV
Samsung has a 4.5-generation line and has an absolute advantage in the small-size OLED market. It is generally believed in the industry that panel manufacturers such as Samsung and LG are ready to transform LCD production lines in South Korea and Taiwan into OLED production lines, and future LCD panels will be supplied by production lines located in mainland China.
Samsung flexible OLED screen
Domestic panel manufacturers seem to be a little slow in responding to OLED, and their core technology still lags behind that of foreign companies. In terms of small size, domestic companies have kept up with the pace. Companies such as BOE, Huaxing Optoelectronics, and Rainbow have investment plans for small-size OLED. In terms of large size, domestic companies lag behind even more. Although BOE has mastered large-size LCD panel technology, its performance has always been poor. Investment is mainly completed with government support and financial market financing. In addition, the 8.5-generation line that was just put into production last year faces huge market pressure from overcapacity in the panel industry. However, the transition from LCD to OLED is inevitable, so BOE may prepare OLED panel line projects of more than 8 generations in the future.
BOE actively deploys AMOLED
At present, the core material technology of the OLED industry is in the hands of American and British companies; the process and equipment are similar to LCD and are mainly in the hands of Japanese, European and American companies. At the same time, the main material science involved in OLED technology is also mostly in the hands of European, American and Japanese companies. The main production areas of intermediate screen products are Japan, South Korea, Taiwan and mainland China.
Previous article:Design method of colorful backlight LED lamp for consumer electronic products
Next article:Introduction, Application and Development of Spectroscopic Technology
Recommended ReadingLatest update time:2024-11-16 19:44
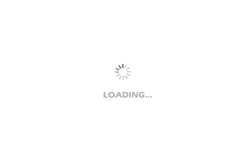
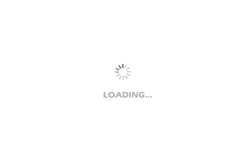
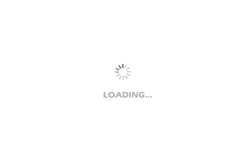
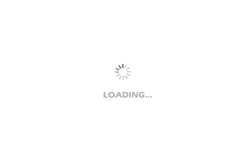
- Popular Resources
- Popular amplifiers
- MathWorks and NXP Collaborate to Launch Model-Based Design Toolbox for Battery Management Systems
- STMicroelectronics' advanced galvanically isolated gate driver STGAP3S provides flexible protection for IGBTs and SiC MOSFETs
- New diaphragm-free solid-state lithium battery technology is launched: the distance between the positive and negative electrodes is less than 0.000001 meters
- [“Source” Observe the Autumn Series] Application and testing of the next generation of semiconductor gallium oxide device photodetectors
- 采用自主设计封装,绝缘电阻显著提高!ROHM开发出更高电压xEV系统的SiC肖特基势垒二极管
- Will GaN replace SiC? PI's disruptive 1700V InnoMux2 is here to demonstrate
- From Isolation to the Third and a Half Generation: Understanding Naxinwei's Gate Driver IC in One Article
- The appeal of 48 V technology: importance, benefits and key factors in system-level applications
- Important breakthrough in recycling of used lithium-ion batteries
- Innolux's intelligent steer-by-wire solution makes cars smarter and safer
- 8051 MCU - Parity Check
- How to efficiently balance the sensitivity of tactile sensing interfaces
- What should I do if the servo motor shakes? What causes the servo motor to shake quickly?
- 【Brushless Motor】Analysis of three-phase BLDC motor and sharing of two popular development boards
- Midea Industrial Technology's subsidiaries Clou Electronics and Hekang New Energy jointly appeared at the Munich Battery Energy Storage Exhibition and Solar Energy Exhibition
- Guoxin Sichen | Application of ferroelectric memory PB85RS2MC in power battery management, with a capacity of 2M
- Analysis of common faults of frequency converter
- In a head-on competition with Qualcomm, what kind of cockpit products has Intel come up with?
- Dalian Rongke's all-vanadium liquid flow battery energy storage equipment industrialization project has entered the sprint stage before production
- Allegro MicroSystems Introduces Advanced Magnetic and Inductive Position Sensing Solutions at Electronica 2024
- Car key in the left hand, liveness detection radar in the right hand, UWB is imperative for cars!
- After a decade of rapid development, domestic CIS has entered the market
- Aegis Dagger Battery + Thor EM-i Super Hybrid, Geely New Energy has thrown out two "king bombs"
- A brief discussion on functional safety - fault, error, and failure
- In the smart car 2.0 cycle, these core industry chains are facing major opportunities!
- The United States and Japan are developing new batteries. CATL faces challenges? How should China's new energy battery industry respond?
- Murata launches high-precision 6-axis inertial sensor for automobiles
- Ford patents pre-charge alarm to help save costs and respond to emergencies
- New real-time microcontroller system from Texas Instruments enables smarter processing in automotive and industrial applications
- For example, for a 24-bit ADC, we only know the accuracy. How is the sampling speed/sampling rate of the microcontroller calculated?
- #Idle Market#Selling Texas Instruments Tiva C Series TM4C123G Development Board
- A Preliminary Study on the Working Principle of PCIe
- FAQ_ How to set up the allocation of memory to the dynamic memory area
- 【Running posture training shoes】No.003-Data collection and real-time display
- [Open Source] FPGA-based binocular camera adapter board
- 13. "Wanli" Raspberry Pi Car - Accessories Preparation
- [Survey] What is the most convenient tool for PCB design?
- stm32f103rct6 serial port 485 can receive, send error
- How to achieve constant temperature between 2 and 8 degrees