To understand how and why OLED power supply affects display image quality, you must first understand OLED display technology and power supply requirements. This article will explain the latest OLED display technology and explore the main power supply requirements and solutions. It will also introduce innovative power supply architectures specifically designed for OLED power supply requirements.
Market environment
All major mobile phone companies have now launched one or more models using OLED displays. Sony has taken the lead in mass-producing OLED TVs, and many other companies have also launched their first prototype models. OLED displays have wide color gamut, high contrast, wide viewing angles, and fast response times, which make them very suitable for multimedia applications. Self-luminous OLED technology does not require backlighting, and its power consumption depends on the display content, which is much lower than that of LCDs using backlighting. As the panel size increases, the high-quality characteristics of OLED become more obvious, so more and more OLED panels have display sizes greater than 3, and the future application level will still be dominated by TV panels. Another OLED display market is flexible displays. At present, the prospects for OLED and electrophoretic display technology are quite promising. Electrophoretic or bistable displays used in e-readers need to improve color quality. On the other hand, when using completely flexible materials, OLED displays are still not suitable for mass production, which mainly depends on the development of backplane technology.
Backplane technology enables flexible displays
High-resolution color active-matrix organic light-emitting diode (AMOLED) displays require an active-matrix backplane that uses active switches to turn each pixel on and off. Liquid crystal (LC) display amorphous silicon processes are now mature enough to provide low-cost active-matrix backplanes that can be used for OLEDs. Many companies are currently developing organic thin-film transistor (OTFT) backplane processes for flexible displays, which can also be used for OLED displays to enable full-color flexible displays. Whether standard or flexible OLED, the same power supply and drive technology are required. To understand OLED technology, its capabilities, and its interaction with the power supply, it is necessary to look deeper into the technology itself. OLED displays are a self-luminous display technology that does not require any backlight at all. The materials used in OLEDs are organic materials with a suitable chemical structure.
OLED technology requires current-controlled driving method
Figure 1 is a simplified circuit diagram showing only one pixel. OLEDs have electrical characteristics quite similar to standard organic light-emitting diodes (LEDs), and the brightness depends on the LED current. To turn the OLED on and off and control the OLED current, a control circuit using a thin-film transistor (TFT) is required.
Figure 1. Simple example of active matrix OLED single pixel control (ITO transparent conductive film)
In Figure 1, transistor T2 is the pixel control transistor that turns the pixel on and off, similar to any other active matrix LCD technology. T1 is treated as a current source, and the current is driven by this gate voltage source. The storage capacitor is Cs, which is used to maintain a stable T1 gate voltage and lock the supply current until the pixel is reconfigured. In Figure 1, the simple single transistor current source has a significant cost advantage because only two transistors are required. The disadvantage of this simple circuit is that the current will vary, which factors include process variations and Vdd voltage variations. OLED power supply circuits usually provide two voltage supply rails, Vdd and Vss. The voltage rail Vdd must achieve very tight regulation to achieve the best picture quality and avoid image flicker. Vss is usually a negative voltage, and its voltage regulation accuracy can be reduced because this voltage is less likely to affect the LED current. Figure 2 shows the effect of voltage fluctuations caused by Vdd on OLED displays.
Figure 2. Voltage fluctuations on the power rails create horizontal streaks
When the voltage supply Vdd changes, the OLED brightness also changes. Superimposed voltage ripples on Vdd can cause horizontal stripes in the image due to different brightness. Depending on the display, voltage ripples greater than 20mV may cause this phenomenon. The degree of appearance of horizontal stripes depends on the amplitude and frequency of the superimposed voltage ripples. Once the frequency interferes with the frame frequency, stripes will appear. In general experimental environments, the superimposed voltage ripples on Vdd are usually less than 20mV. This problem will occur when the display and power supply are integrated into a system. Once any subcircuit in the system draws pulsating current from the system power supply, voltage ripples will appear. This is true for all circuits connected to the system power supply. Subcircuits that typically draw pulsating current include GSM power amplifiers, motor drivers, audio power amplifiers, etc. in mobile phones. In these systems, superimposed voltage ripples will appear on the system supply power rail. If the AMOLED power supply does not suppress this ripple, the ripple will appear at the output and cause the image distortion mentioned above. To avoid such problems, the power supply of AMOLED needs to have extremely high power supply rejection ratio and line transient response.
For the power supply of AMOLED, the positive voltage power rail Vdd requires a boost converter, and the negative voltage power rail Vss requires a buck-boost converter or inverter. This is a big challenge for IC manufacturers who provide suitable power supplies, because manufacturers need to provide quite accurate positive voltage power rail Vdd and negative voltage power rail Vss to achieve the lowest component height and smallest solution size.
To meet all these requirements, a new power supply topology is needed to provide both positive and negative voltage rails from the Li-Ion battery using only a single inductor. SIMO regulator technology enables best-in-class image quality
Figure 3. TPS65136 buck-boost converter topology with dual input support
Figure 3 shows a general application circuit using the TPS65136, which uses single inductor multiple output (SIMO) regulator technology and operates in a four-switch buck-boost converter topology. SIMO technology achieves best-in-class line transient regulation, buck-boost mode for both outputs, and highest efficiency over the entire load current range.
Advanced energy-saving mode for maximum efficiency
As with any battery-powered device, long battery standby times can only be achieved when the converter operates at maximum efficiency over the entire load current range, which is particularly important for OLED displays. OLED displays consume the most power when displaying full white, and less current for any other displayed color, because only white requires all red, green, and blue sub-pixels to be fully illuminated. For example, a 2.7 display requires 80mA to display a full white image, but only 5mA to display other icons or graphics. Therefore, OLED power supplies require high converter efficiency for all load currents. To achieve such efficiency, advanced power-saving mode techniques are used to reduce the load current to reduce the converter switching frequency. Because this is done through a voltage-controlled oscillator (VCO), possible EMI issues are minimized and the minimum switching frequency can be controlled outside the typical 40kHz audio range, which avoids noise generation from ceramic input or output capacitors. This is particularly important when using these devices in mobile phone applications and simplifies the design process.
in conclusion
As OLEDs mature, they can be applied to architectural lighting or LCD display backlighting. Compared with traditional lighting solutions, OLEDs offer lower power consumption and higher design flexibility for both applications.
Previous article:Analysis of High Efficiency Driving Circuit for LED
Next article:High-quality LED manufacturing technology analysis
Recommended ReadingLatest update time:2024-11-16 17:45
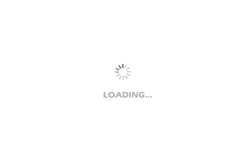
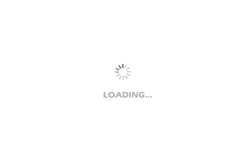
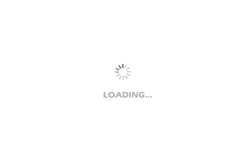
- Popular Resources
- Popular amplifiers
- MathWorks and NXP Collaborate to Launch Model-Based Design Toolbox for Battery Management Systems
- STMicroelectronics' advanced galvanically isolated gate driver STGAP3S provides flexible protection for IGBTs and SiC MOSFETs
- New diaphragm-free solid-state lithium battery technology is launched: the distance between the positive and negative electrodes is less than 0.000001 meters
- [“Source” Observe the Autumn Series] Application and testing of the next generation of semiconductor gallium oxide device photodetectors
- 采用自主设计封装,绝缘电阻显著提高!ROHM开发出更高电压xEV系统的SiC肖特基势垒二极管
- Will GaN replace SiC? PI's disruptive 1700V InnoMux2 is here to demonstrate
- From Isolation to the Third and a Half Generation: Understanding Naxinwei's Gate Driver IC in One Article
- The appeal of 48 V technology: importance, benefits and key factors in system-level applications
- Important breakthrough in recycling of used lithium-ion batteries
- Innolux's intelligent steer-by-wire solution makes cars smarter and safer
- 8051 MCU - Parity Check
- How to efficiently balance the sensitivity of tactile sensing interfaces
- What should I do if the servo motor shakes? What causes the servo motor to shake quickly?
- 【Brushless Motor】Analysis of three-phase BLDC motor and sharing of two popular development boards
- Midea Industrial Technology's subsidiaries Clou Electronics and Hekang New Energy jointly appeared at the Munich Battery Energy Storage Exhibition and Solar Energy Exhibition
- Guoxin Sichen | Application of ferroelectric memory PB85RS2MC in power battery management, with a capacity of 2M
- Analysis of common faults of frequency converter
- In a head-on competition with Qualcomm, what kind of cockpit products has Intel come up with?
- Dalian Rongke's all-vanadium liquid flow battery energy storage equipment industrialization project has entered the sprint stage before production
- Allegro MicroSystems Introduces Advanced Magnetic and Inductive Position Sensing Solutions at Electronica 2024
- Car key in the left hand, liveness detection radar in the right hand, UWB is imperative for cars!
- After a decade of rapid development, domestic CIS has entered the market
- Aegis Dagger Battery + Thor EM-i Super Hybrid, Geely New Energy has thrown out two "king bombs"
- A brief discussion on functional safety - fault, error, and failure
- In the smart car 2.0 cycle, these core industry chains are facing major opportunities!
- The United States and Japan are developing new batteries. CATL faces challenges? How should China's new energy battery industry respond?
- Murata launches high-precision 6-axis inertial sensor for automobiles
- Ford patents pre-charge alarm to help save costs and respond to emergencies
- New real-time microcontroller system from Texas Instruments enables smarter processing in automotive and industrial applications
- Openmv3 photography
- [2022 Digi-Key Innovation Design Competition] Distributed Temperature and Humidity Acquisition System-STM32H745I-DISCO Basic Learning
- Start at 2pm: TI MSP430 development training, online hands-on demo + analysis by frontline experts
- Chip Manufacturing: A Practical Tutorial on Semiconductor Process Technology (Sixth Edition)
- CircuitPython 6.0.0 Beta 2 released
- July 21 Live Replay: Microchip Timberwolf Audio Processor Online Seminar (including video, PPT, QA)
- MSP430 FAQ: FLASH storage
- [RISC-V MCU CH32V103 Review] Driving OLED Display
- Experience in using TI DSP/BIOS and CCS
- Four-layer PCB proofing matters needing attention