From the electrical characteristics of LED, we know that the average forward current of LED increases linearly with the increase of forward voltage. After the LED is forward-conducted, a small change in its forward voltage will cause a large change in the LED current. The current has a great influence on the junction temperature of the LED. Excessive current can easily cause the junction temperature of the LED lamp bead to rise and damage. In addition, from the optical characteristics of LED, we know that as the forward current increases, the LED luminous flux increases, that is, the brightness increases. Therefore, in order to keep the LED brightness constant, it is necessary to ensure the stability of the LED forward current. Therefore, it is very important to design a reasonable drive power supply for LED lighting fixtures.
This paper proposes a LED linear constant current drive circuit, which has the characteristics of low cost, simple structure, high efficiency and small size. It is very suitable as a driving power supply for indoor lighting LED lamps (such as LED fluorescent lamps).
1 LED linear constant current drive circuit
When using LED lights, multiple lamp beads need to be connected in series or in parallel to work. Although the voltage required to drive multiple LEDs in parallel is lower, the brightness of each LED is different due to the different forward voltage drops of each LED, unless a separate adjustment method is used to ensure that each LED has the same brightness. Therefore, the parallel method must ensure uniform brightness, which is more complicated to implement. The series method can ensure that the current flowing through each LED is the same and the brightness is consistent, which is currently a commonly used structure.
When using the series drive mode, if one or more LEDs fail and open the circuit (the short circuit has a small impact on the circuit and can be ignored), the circuit will be open and cannot work properly. In order to avoid this defect, a voltage regulator can be connected in reverse parallel at both ends of each LED (as shown in Figure 1). When a certain LED lamp bead is open, the parallel voltage regulator will be put into operation to ensure that the current of the series lamp bead remains unchanged. It should be noted that the voltage regulator value of the voltage regulator should be higher than the conduction voltage of the LED, otherwise the parallel voltage regulator will shunt part of the current and make the LED dim or even not light up.
Figure 1 LED series drive circuit
This article adopts a series drive method, and its LED linear constant current control circuit is shown in Figure 2.
Figure 2 LED linear constant current control circuit
In the figure, Vz1, Vz2, VQ1, VQ2, R1, and R2 form a linear constant current source, which ensures that the current flowing through each white light LED is the same, so as to obtain uniform brightness. The LED driving power supply uses the mains direct rectification and filtering to obtain the DC working voltage for controlling the LED, without the need for boost or buck processing, so the power driving circuit is simple and the power efficiency is high. The LED used is a high-brightness white light LED (operating voltage range: 3.0~3.2V), and 94 LED lamp beads are used to form an LED fluorescent lamp.
Next, the working principle of the linear constant current source circuit is analyzed. The circuit adopts a complementary two-terminal constant current source structure, as shown in Figure 3.
Figure 3 Complementary two-terminal constant current source circuit
Transistor VQ1, voltage regulator tube Vz1 and R1 form a constant current source, which provides a stable working current to voltage regulator tube Z2, while transistor VQ2, voltage regulator tube Vz2 and R2 form another constant current source to provide a stable working current to voltage regulator tube Vz1. Since the two constant current sources stabilize each other's voltage regulator tube working point, the stable voltages Vz1 and Vz2 and the total current flowing through the constant current unit no longer change, so the constant working current flowing through the LED can be guaranteed.
The relationship between the current and voltage in the figure is as follows:
The total operating current flowing through the LED, ILED, is:
The LED lamp beads we use are 0.06 W LEDs with an operating current of 20mA. For the convenience of design, the circuit components selected are completely symmetrical, and the parameters are:
Substituting the above parameters into formula (1) we can obtain:
The constant current source circuit provides a working current of 20mA, which meets the requirements of the lamp beads used.
2 Test results and analysis
The test wiring is shown in Figure 2. The voltage is changed by adjusting the autotransformer to simulate the change of the grid voltage. By simulating the fluctuation of the grid voltage, the working characteristics of this constant current control circuit in the actual grid are tested to observe whether the working current of the LED will fluctuate greatly with the fluctuation of the external voltage, and the efficiency of this circuit under different voltages and the junction temperature of the LED are actually tested.
2.1 Characteristics of LED forward current changing with input voltage
FIG. 4 is a curve showing the relationship between the operating current and the power supply voltage of the LED lamp string.
Figure 4 Relationship curve between power supply voltage and LED current
When the power supply voltage Ui increases from 220V to 250V, the rectified DC voltage changes from 310V to 350V, while the working current of the LED lamp string, If, changes from 20mA to 21.5mA, which only changes by 1.5mA. Therefore, it can be seen that the circuit has a good constant current effect, ensuring the basic stability of the brightness of the LED eye lamp.
2.2 Effect of input voltage change on drive circuit parameters
Figures 5 and 6 show the changes in the DC voltage added to the LED working circuit, the voltage added to the LED lamp string, and the voltage borne by the constant current source as the input voltage changes. From Figures 5 and 6, it can be seen that after the input voltage is rectified, the DC voltage formed is divided by the LED lamp string and the linear constant current source. The more divided voltage on the LED lamp string, the higher the efficiency of the input voltage. Therefore, through the analysis of Figure 6, it can be seen that the power efficiency of this LED drive circuit is high.
Figure 5 Effect of input voltage change on the circuit
Figure 6 Relationship between input voltage change and power efficiency
As can be seen from Figure 5, when the power input voltage is in the range of 200-220 V, most of the DC voltage Ui (DC) after rectification and filtering is loaded on both ends of the LED, and the voltage division of the constant current control circuit is small; as can be seen from Figure 6, when the power input voltage is less than or equal to 220 V, the power efficiency is relatively high, reaching 98.31% at 220 V.
When the power input voltage Ui (AC) is higher than 220 V, as the input voltage increases, the voltage U (led) across the LED remains basically unchanged (about 291 V), and the increased input voltage is basically borne by the voltage U (constant) of the constant current control circuit, which ensures that the forward voltage of a single LED remains basically unchanged (3.1 V), and is in a constant power working state, and the current and light emission remain stable.
2.3 Effect of input voltage change on LED junction temperature
The light decay of LED is closely related to the junction temperature. When the junction temperature rises, the forward voltage decreases. The decrease in junction voltage leads to an increase in current. The increased current in turn causes the junction voltage to decrease, forming a vicious cycle. Junction temperature is an important cause of light decay. The higher the junction temperature, the earlier the light decay occurs and the shorter the life. Therefore, the change in junction temperature is also an important indicator for examining a driving circuit. Here, the method in the literature is used to measure the junction temperature:
Where, Tj(LED) is the LED junction temperature, TO is the test ambient temperature (20°C), VO is the initial forward voltage of the LED, VT is the forward voltage of the LED after thermal equilibrium (measured after 1 hour), and K is the temperature coefficient of the LED (-2mV/°C). The specific measurement is to change the input voltage. Under different input voltages, the LED lamp is first allowed to fully cool down and the total voltage across the LED is measured. This voltage is U(led initial). After 1 hour, the total voltage of the LED is measured again under the same input voltage condition. This voltage is U(led end). The initial forward voltage VT of a single LED can be obtained by dividing U(led initial) by the total number of LEDs. The forward voltage VO of a single LED after thermal equilibrium can be obtained by dividing U(led end) by the total number of LEDs. Substituting it into formula (2) can obtain the junction temperature of the LED. The experimental results are shown in Figures 7 and 8.
Figure 7 LED voltage changes under different input voltages
Figure 8 LED junction temperature changes under different input voltages
As can be seen from Figures 7 and 8, the power input voltage Ui (AC) is different, but the voltage across the LED remains basically unchanged. After one hour, the voltage change is also very small. During this period of time, the junction temperature is low, and the junction temperature of a single LED remains basically unchanged or changes slightly. Therefore, this constant current source control circuit can ensure that the junction temperature of the LED is basically stable and small, which can reduce light decay and effectively increase the service life of the LED fluorescent lamp.
3 Conclusion
The circuit structure given in this paper is simple and reliable. The innovation lies in applying the complementary constant current circuit to the constant current drive circuit of the LED. The experimental results show that when the input of the circuit changes from 200 to 250 V, the drive current changes by only 1.5 mA, and the LED junction temperature is lower than 37°C. These are the two most prominent key parameters affecting the operation of LED lamp beads, indicating that the circuit can provide a good working condition for the LED. In addition, the experimental results show that the circuit has a high power efficiency under normal mains power supply (220 V). The circuit has been used on a 1.2 m LED fluorescent tube with good results. In the design process, attention should be paid to matching the circuit parameters according to the working current of the specific circuit.
Previous article:IntersilISL97691 single lithium battery 4-way LED driver solution
Next article:Protection measures for LED drive circuit
Recommended ReadingLatest update time:2024-11-16 15:45
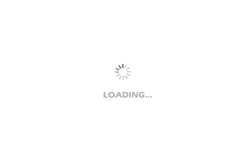
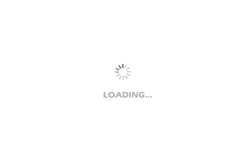
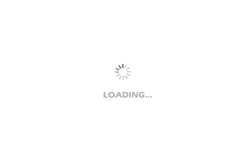
- Popular Resources
- Popular amplifiers
- MathWorks and NXP Collaborate to Launch Model-Based Design Toolbox for Battery Management Systems
- STMicroelectronics' advanced galvanically isolated gate driver STGAP3S provides flexible protection for IGBTs and SiC MOSFETs
- New diaphragm-free solid-state lithium battery technology is launched: the distance between the positive and negative electrodes is less than 0.000001 meters
- [“Source” Observe the Autumn Series] Application and testing of the next generation of semiconductor gallium oxide device photodetectors
- 采用自主设计封装,绝缘电阻显著提高!ROHM开发出更高电压xEV系统的SiC肖特基势垒二极管
- Will GaN replace SiC? PI's disruptive 1700V InnoMux2 is here to demonstrate
- From Isolation to the Third and a Half Generation: Understanding Naxinwei's Gate Driver IC in One Article
- The appeal of 48 V technology: importance, benefits and key factors in system-level applications
- Important breakthrough in recycling of used lithium-ion batteries
- Innolux's intelligent steer-by-wire solution makes cars smarter and safer
- 8051 MCU - Parity Check
- How to efficiently balance the sensitivity of tactile sensing interfaces
- What should I do if the servo motor shakes? What causes the servo motor to shake quickly?
- 【Brushless Motor】Analysis of three-phase BLDC motor and sharing of two popular development boards
- Midea Industrial Technology's subsidiaries Clou Electronics and Hekang New Energy jointly appeared at the Munich Battery Energy Storage Exhibition and Solar Energy Exhibition
- Guoxin Sichen | Application of ferroelectric memory PB85RS2MC in power battery management, with a capacity of 2M
- Analysis of common faults of frequency converter
- In a head-on competition with Qualcomm, what kind of cockpit products has Intel come up with?
- Dalian Rongke's all-vanadium liquid flow battery energy storage equipment industrialization project has entered the sprint stage before production
- Allegro MicroSystems Introduces Advanced Magnetic and Inductive Position Sensing Solutions at Electronica 2024
- Car key in the left hand, liveness detection radar in the right hand, UWB is imperative for cars!
- After a decade of rapid development, domestic CIS has entered the market
- Aegis Dagger Battery + Thor EM-i Super Hybrid, Geely New Energy has thrown out two "king bombs"
- A brief discussion on functional safety - fault, error, and failure
- In the smart car 2.0 cycle, these core industry chains are facing major opportunities!
- The United States and Japan are developing new batteries. CATL faces challenges? How should China's new energy battery industry respond?
- Murata launches high-precision 6-axis inertial sensor for automobiles
- Ford patents pre-charge alarm to help save costs and respond to emergencies
- New real-time microcontroller system from Texas Instruments enables smarter processing in automotive and industrial applications
- Application example of using 555 to realize timing function
- Network Camera Data/Port Forwarding Hardware Design Solution
- [Comic] Confession of a PCB layout engineer!
- How to distinguish between pads and vias_Differences between vias and pads
- Input protection design and fast acquisition issues of 0-10V input ADC circuit based on TI ADS1115
- Zero-knowledge ESP8266 Blynk mobile APP tutorial: monitoring indoor temperature and humidity
- Iar7.3 builds the project and reports an error: cannot open the source file "XXXxxx.h
- Smart speakers ignite the "lazy economy" AWE2019 highlights
- Experience of using C28x Filter Library!
- GD32E231 simulates IIC driving STTS751