In the past, when LEDs could only be used as status indicators, heat dissipation of LED packages was never a problem. However, in recent years, the brightness and power of LEDs have been actively improved, and they have begun to be used in backlight and electronic lighting applications. The problem of heat dissipation of LED packages has quietly emerged. The above statement sounds a bit confusing. Isn't the emphasis on LED brightness breakthroughs today? In 2003, Mr. Roland Haitz of Lumileds Lighting Company worked out an empirical technical inference law based on past observations. Starting from the first commercialized LED in 1965, in the past 30 years of development, the brightness of LEDs can be doubled every 18 to 24 months. In the next 10 years, it is expected that the brightness can be increased by another 20 times, and the cost will be reduced to 1/10 of the current level. This is also the Haitz law that has become popular in recent years and is considered to be Moore's law in the LED industry.
According to the inference of Haitz's law, LEDs with a brightness of 100lm/W (100 lumens per watt) will appear around 2008 or 2010. However, actual development seems to have surpassed the law. In June 2006, Nichia Chemical Industry (Nichia) began to provide engineering samples of white light LEDs with a brightness of up to 100lm/W, and it is expected to be put into mass production by the end of the year.
Haitz's law can be said to be the Moore's law in the field of LED. According to Roland Haitz, the luminous efficiency of LED has doubled almost every 18 or 24 months in the past 30 years. Therefore, it is estimated that the brightness will grow 20 times in the next 10 years (2003; 2013), but the price will be only 1/10 of the current price. Not only the brightness is constantly increasing, but the heat dissipation technology of LED has also been improving. In 1992, the thermal resistance of an LED was 360℃/W, and then it dropped to 125℃/W, 75℃/W, 15℃/W, and now it has reached 6℃/W~10℃/W per LED. To put it simply, in the past, the temperature of LED would increase by 360℃ for every 1 watt of electricity consumed, but now the temperature only rises by 6℃~10℃ for the same 1 watt of electricity consumed.
A small number of high brightness and a large number of densely arranged stars are the culprits of heat increase.
Since the brightness efficiency is improved, the heat dissipation efficiency is improved, isn't that more contradictory? There should be no heat dissipation problem, right? In fact, it should be more strictly said that the aggravation of the heat dissipation problem is not due to high brightness, but to high power; not in traditional packaging, but in new packaging and new applications.
First, in the past, LEDs were only used as indicator lights, and the lighting (forward conduction) current of each single LED was mostly between 5mA and 30mA, and typically 20mA. However, today's high-power LEDs (Note 1) have a current of 330mA and 1A per single LED, and the "power consumption per LED" has increased tenfold or even dozens of times (Note 2).
Note 1: In addition to increasing the area of a single light-emitting bare die, the current high-power LED method also includes packaging multiple bare die together. In fact, some white light LEDs mix white light by placing bare die of three primary colors, red, green, and blue, in the same package.
Note 2: Although the lighting (forward conduction) voltage of various LEDs is different, this difference is ignored for now.
When doubled current is fed into the same single package, the heat generation will naturally double, and the heat dissipation will of course worsen. Unfortunately, since white light LEDs are used as flashlights for camera phones, small lighting bulbs, and lighting bulbs in projectors, high brightness alone is not enough, and high power is also required, and heat dissipation becomes a problem. The above-mentioned LED application method only uses a few high-power LEDs, about 1 to 4 flashlights, about 1 to 8 lighting bulbs, and more than 10 in projectors. However, flashlights are rarely used and the lighting time is not long. Single lighting bulbs have more ample surrounding heat dissipation space, and although there is no ample heat dissipation space in the projector, a cooling fan can be installed.
The figure shows the external quantum efficiency of InGaN and AlInGaP, two semiconductor materials used for LEDs, at each peak wavelength (light color). Although it can be close to 40% in the most ideal case, if the light extraction efficiency is taken into consideration, it is actually between 15% and 25%. Moreover, the higher efficiency parts of the two materials are not within the range of human eye sensitivity, and only 20% are below the range. However, there are still many applications that require high brightness, but require high-brightness LEDs to be densely arranged, such as traffic lights, message billboards, and TV walls composed of LEDs. The result of dense arrangement is that it is not easy to dissipate heat, which is a heat dissipation problem caused by the application. What's more, on the backlight of LCD TVs, high-brightness LEDs are used, and they must be densely arranged. In order to be short, light and thin, the available heat dissipation design space on the back is more restricted. If high standards are required, cooling fans should not be used because the noise of the fan will affect the taste and mood of TV viewing.
What are the side effects if the heat dissipation problem is not solved?
Good! If the heat dissipation problem is not solved, and the heat of the LED cannot be dissipated, and the operating temperature of the LED increases, what will happen? There are two main effects: (1) reduced brightness and (2) reduced service life. For example, when the pn junction temperature of the LED is 25℃ (typical operating temperature), the brightness is 100, and when the temperature rises to 75℃, the brightness decreases to 80, and at 125℃ it is only 60, and at 175℃ it is only 40. Obviously, the junction temperature and the brightness are inversely proportional. The higher the temperature, the dimmer the LED brightness.
The effect of temperature on brightness is linear, but the effect on life is exponential. Based on the junction temperature, if the LED is kept below 50℃, its life will be nearly 20,000 hours. At 75℃, it will only be 10,000 hours, at 100℃, it will be 5,000 hours, at 125℃, it will be 2,000 hours, and at 150℃, it will be 1,000 hours. When the temperature is doubled from 50℃ to 100℃, the life will be reduced from 20,000 hours to 1/4 of 5,000 hours, which is extremely harmful.
Bare crystal layer: The source of the radiation from both sides of the optical and thermal system: pn junction
Regarding the heat dissipation of LED, we also discuss it from the core layer by layer, starting from the pn junction. The solution is to convert as much electrical energy as possible into light energy and less into heat energy, that is, as light energy increases, heat energy decreases, thereby reducing heat generation. If we discuss it further, the electro-optical conversion efficiency is the internal quantum efficiency (Internal Quantum Efficiency; IQE), which is generally 70% to 90% today. The real crux lies in the low external quantum efficiency (External Quantum Efficiency; EQE). Taking Lumileds Lighting's Luxeon series LED as an example, the Tj junction temperature is 25°C and the forward drive current is 350mA. For InGaN, the efficiency varies from 5% to 27% depending on the wavelength (light color). The higher the wavelength, the lower the efficiency (grass green is only 5%, blue can reach 27%). AlInGaP also varies with wavelength, but the higher the wavelength, the higher the efficiency, generally ranging from 8% to 40% (light yellow is the lowest and orange is the highest).
From the cross-section of Lumileds' Luxeon series LEDs, we can see that the silicon encapsulant fixes the LED die and the phosphor on the die (if phosphor is used), and then a lens is placed on top of the encapsulant. The die is connected to the silicon sub-mount chip by welding (or thermal paste) at the bottom. This chip can also enhance ESD protection and is then connected to the heat sink. Some LEDs are also directly connected to the heat sink at the bottom of the die.
Lumileds' Luxeon series LEDs are flip-chip mounted, so the sapphire substrate is on the top, and a layer of silver is added as a light reflection layer to increase the amount of light extraction. In addition, two Zener diodes are made in the Silicon Submount to stabilize the LED voltage and make the operation more stable. Increasing the light extraction efficiency (Extraction Efficiency, also known as light absorption efficiency, light extraction efficiency) is equivalent to reducing the heat dissipation rate, which is equivalent to two sides of the same issue.
Bare die layer: substrate material, flip chip damascene
How to increase heat dissipation at the bare crystal level, changing the material and geometric structure has become a necessary means again. The two most commonly used methods are: 1. Replace the substrate (Substrate, also known as: bottom plate, substrate, sometimes also called: Carrier) material. 2. Replace the bare crystal with a flip-chip (also known as: inverted crystal) mount. Let's first explain the substrate part. The substrate material cannot be changed at will. It must match the bare crystal material. The commonly used substrate materials for AlGaInP are GaAs and Si, and those for InGaN are SiC and Sapphire (and AlN is used as a buffer layer).
In order to enhance the heat dissipation of LEDs, the previous FR4 printed circuit boards are no longer sufficient, so a printed circuit board with a metal core, called MCPCB, is proposed. It uses metals with better thermal conductivity such as aluminum or copper at the bottom to accelerate heat dissipation, but the characteristics of the insulating layer also limit its thermal conductivity. For light, the substrate must be transparent enough so that it does not block the light, or a reflective material layer is added between the light-emitting layer and the substrate to prevent the "light energy" from being blocked and absorbed by the substrate, resulting in waste. For example, the GaAs substrate is opaque, so a DBR (Distributed Bragg Reflector) reflective layer is added to reflect light. The Sapphire substrate can directly reflect light, or the transparent GaP substrate can be transparent. In addition, the substrate material must also have good thermal conductivity, responsible for quickly conducting the heat released by the bare die to the lower heat sink (Heat Slug), but the substrate and the heat sink must also use a good thermal conductive interface, such as solder or thermal paste. At the same time, the epoxy resin or silicone resin (i.e., the sealing layer) on the bare die must also have a certain heat resistance to cope with the temperature transmitted from the pn junction to the bare die surface. In addition to strengthening the substrate, another method is flip-chip inlay, which turns the bare die electrode that used to be located on the top to the bottom, and the electrode is directly connected to the wire foil at the bottom, so that the heat can be transmitted to the bottom faster. This heat dissipation method is not only used in LEDs, but also in today's high-temperature CPUs and GPUs. It has long been implemented to accelerate heat dissipation.
From traditional FR4 PCB to metal core MCPCB
After conducting the heat to the lower layer, in the past, copper foil printed circuit boards (PCBs) were used to dissipate the heat directly, which is the most common FR4 printed circuit substrate. However, as the heat generated by LEDs becomes higher and higher, FR4 printed circuit substrates have gradually become difficult to bear because of their insufficient thermal conductivity (only 0.36W/mK).
In order to improve the heat dissipation at the circuit board level, the so-called metal core printed circuit board (l Core PCB; MCPCB) was proposed. That is, the original printed circuit board is attached to another metal with better thermal conductivity (such as aluminum, copper) to enhance the heat dissipation effect. This piece of metal is located inside the printed circuit board, so it is called "l Core". The thermal conductivity efficiency of MCPCB is higher than that of traditional FR4 PCB, reaching 1W/mK~2.2W/mK.
However, MCPCB also has some limitations. The temperature cannot exceed 140℃ when the circuit system is operating. This is mainly due to the characteristics of the dielectric layer (also called insulated layer). In addition, the temperature during the manufacturing process must not exceed 250℃ or 300℃. This must be understood in advance before passing through the tin furnace.
Note: Although aluminum and copper are both suitable thermally conductive metals, aluminum is often chosen due to cost constraints.
IMS strengthens the thermal conduction of MCPCB on the insulation layer
Although MCPCB has better heat dissipation effect than FR4 PCB, the dielectric layer of MCPCB does not have very good thermal conductivity, which is roughly the same as FR4 PCB, only 0.3W/mK, becoming a conduction bottleneck between the heat sink and the metal core board. In order to improve this situation, some industry insiders have proposed the improvement method of IMS (Insulated l Substrate, insulated metal substrate), which directly connects the polymer insulation layer and copper foil circuit with aluminum and copper plates in an epoxy manner, and then configures the LED on the insulating substrate. The thermal conductivity of this insulating substrate is relatively high, reaching 1.1;2W/mK, which is 3;7 times higher than before. Furthermore, if the insulation layer is still considered to have poor thermal conductivity, there is also a method of directly allowing the heat sink at the bottom of the LED to directly contact the core metal through the through hole on the printed circuit board to accelerate heat dissipation. This method is very intriguing, because in the past, printed circuit boards were either chiseled for plug-in component soldering or for circuit bypassing, but now they are chiseled for heat dissipation design.
In addition to MCPCB and MCPCB+IMS, some people have proposed using ceramic substrates, or so-called direct copper bonded substrates (DBC), or metal composite substrates. Both ceramic substrates and direct copper bonded substrates have high conductivity of 24-170W/mK, and direct copper bonded substrates allow process and operating temperatures to reach over 800℃, but these technologies need further maturity observation.
Previous article:Array LED micro projector: creating a new differentiation for smartphones
Next article:Design of LED landscape lighting control system based on wireless sensor network
Recommended ReadingLatest update time:2024-11-16 15:42
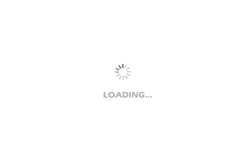
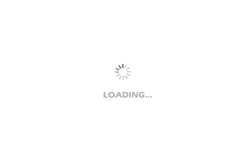
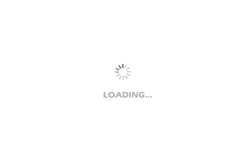
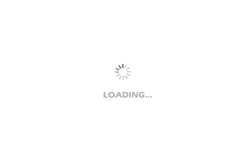
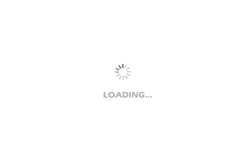
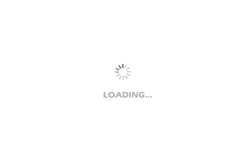
- Popular Resources
- Popular amplifiers
- MathWorks and NXP Collaborate to Launch Model-Based Design Toolbox for Battery Management Systems
- STMicroelectronics' advanced galvanically isolated gate driver STGAP3S provides flexible protection for IGBTs and SiC MOSFETs
- New diaphragm-free solid-state lithium battery technology is launched: the distance between the positive and negative electrodes is less than 0.000001 meters
- [“Source” Observe the Autumn Series] Application and testing of the next generation of semiconductor gallium oxide device photodetectors
- 采用自主设计封装,绝缘电阻显著提高!ROHM开发出更高电压xEV系统的SiC肖特基势垒二极管
- Will GaN replace SiC? PI's disruptive 1700V InnoMux2 is here to demonstrate
- From Isolation to the Third and a Half Generation: Understanding Naxinwei's Gate Driver IC in One Article
- The appeal of 48 V technology: importance, benefits and key factors in system-level applications
- Important breakthrough in recycling of used lithium-ion batteries
- Innolux's intelligent steer-by-wire solution makes cars smarter and safer
- 8051 MCU - Parity Check
- How to efficiently balance the sensitivity of tactile sensing interfaces
- What should I do if the servo motor shakes? What causes the servo motor to shake quickly?
- 【Brushless Motor】Analysis of three-phase BLDC motor and sharing of two popular development boards
- Midea Industrial Technology's subsidiaries Clou Electronics and Hekang New Energy jointly appeared at the Munich Battery Energy Storage Exhibition and Solar Energy Exhibition
- Guoxin Sichen | Application of ferroelectric memory PB85RS2MC in power battery management, with a capacity of 2M
- Analysis of common faults of frequency converter
- In a head-on competition with Qualcomm, what kind of cockpit products has Intel come up with?
- Dalian Rongke's all-vanadium liquid flow battery energy storage equipment industrialization project has entered the sprint stage before production
- Allegro MicroSystems Introduces Advanced Magnetic and Inductive Position Sensing Solutions at Electronica 2024
- Car key in the left hand, liveness detection radar in the right hand, UWB is imperative for cars!
- After a decade of rapid development, domestic CIS has entered the market
- Aegis Dagger Battery + Thor EM-i Super Hybrid, Geely New Energy has thrown out two "king bombs"
- A brief discussion on functional safety - fault, error, and failure
- In the smart car 2.0 cycle, these core industry chains are facing major opportunities!
- The United States and Japan are developing new batteries. CATL faces challenges? How should China's new energy battery industry respond?
- Murata launches high-precision 6-axis inertial sensor for automobiles
- Ford patents pre-charge alarm to help save costs and respond to emergencies
- New real-time microcontroller system from Texas Instruments enables smarter processing in automotive and industrial applications
- CCS compiles and generates binary files
- Mobile phone calculators are all dead: What is 10% + 10%? [Have you ever calculated it?]
- When the serial port is connected, if the host receives wrong data, it will return to the initial state.
- How to set the temperature of the battery temperature detection pin TS of BQ24650 to -10℃-50℃
- Summary of DSP CMD file writing method
- IC WKN Driver Laser Diode
- [Live broadcast on May 9] Discussing solutions to reduce downtime in the new manufacturing era, ADI live broadcast expert Zhao Yanhui is here again
- MOS tube isolation drive circuit, if we drive high voltage MOS tube, we need to use transformer drive and integrated...
- Watch NXP LPC55S69 live broadcast and get the book "Embedded Security Processor Application and Practice" for free
- EEWORLD University ---- SimpleLink Academy: Develop your Bluetooth? Low Energy project