1 System solution demonstration and selection
1.1 Overall Solution
Solution ①: Digital solution. After the input signal is conditioned by the preamplifier, it is collected by the A/D and processed by the microcontroller. The triangular wave generation and the comparison with the audio signal are completed by the software part. Then the microcontroller outputs two completely opposite PWM waves to the post-stage power amplifier for amplification. This solution has a simple hardware circuit, but it will introduce large digital noise.
Solution ②: Hardware circuit solution. The triangular wave generation and comparison, PWM generation are still realized by hardware circuit. This solution has less noise, and the amplitude can be larger, and the effect is better, so this solution is adopted.
1.2 Triangle wave generation circuit design
Solution ①: Use NE555 to generate triangular wave. The characteristics of this circuit are that it uses a constant current source to linearly charge and discharge the capacitor to generate a triangular wave. The waveform linearity is good, the frequency control is simple, and the signal amplitude can be controlled by adding an attenuation potentiometer.
Solution ②: Integrate the square wave to generate a triangular wave. The integrator and comparator are cascaded, and the triangular wave is obtained by integrating the square wave generated by the comparator. The frequency and amplitude control only need to adjust certain resistance values, and the control is simple. However, the integration circuit has integration drift.
Here we adopt option ①.
1.3 PWM wave generation scheme design
Solution ①: Direct comparison. Take a triangle wave signal with the same weight as the input audio signal and slightly larger amplitude and compare it directly with the audio signal to generate a PWM wave, and then generate a PWM wave signal that is completely opposite to the input audio signal through an inverter to send to the subsequent amplifier circuit.
Solution ②: Dual-channel comparison. Use two triangular wave signals with different biases to compare the upper and lower halves of the audio signal. This solution can reduce the number of times the CMOS tube is opened and closed in the suffix H-bridge circuit, reduce power loss, and improve efficiency.
Solution ③: Directly reverse the audio signal. Directly reverse the audio input signal after amplification and conditioning, and then perform triangle wave comparison on the processed signal to generate two reverse PWM waves.
Since solution ② has higher efficiency and has a certain effect on suppressing common-mode noise, solution ② is selected.
1.4 Short-circuit protection scheme design
Solution ①: Current transformer method. Use a current transformer to sense the current passing through the load resistor, and then process this current to determine whether the circuit is over-current or not.
Solution ②: Sampling resistor method. A small resistor is connected in series to the circuit to sample the current flowing through the load of the system to determine whether the circuit is over-current or not. This solution is simple to implement, and the connection of a small resistor has little effect on the system, so this solution is adopted.
2 System overall design and implementation block diagram
As shown in Figure 1, the overall implementation block diagram of the system consists of four main modules: high-efficiency power amplifier, signal conversion circuit, overcurrent protection and power measurement . The core high-efficiency power amplifier consists of five parts: preamplifier, triangle wave generation circuit, comparator circuit, drive circuit, and H-bridge complementary symmetrical amplifier. After the input audio signal is amplified and conditioned by the preamplifier circuit, it is divided into upper and lower parts and compared with two triangle wave signals to obtain two corresponding PWM waves; that is, the audio signal is pulse-width modulated, and then the driving ability of the signal is increased by the drive circuit, and then fed into the H-bridge module, and the power switch is controlled by the change of duty cycle to achieve power amplification, and then the output on the load is low-pass filtered to filter out the original audio signal. The signal is fed into the signal change circuit on the load, and the double-ended signal is converted into a single-ended signal, and then connected to the test instrument after a cutoff frequency of 20 kHz. At the same time, the true effective value of the single-ended signal is detected here, and after AD sampling, it is sent to the single-chip microcomputer for power calculation and display . The system also has an overcurrent protection function. A 0.1Ω sampling resistor is connected in series with the load to sample the current value flowing through the load. After amplification and comparison, a relay is used to control the power supply of the power amplifier part, thereby achieving protection. The maximum undistorted output power of the system is greater than or equal to 1 W, and the voltage amplification factor can be continuously adjusted from 1 to 20. Due to the use of a Class D amplification solution, a higher efficiency can be achieved, the output noise is very small, and the power display error is very small.
Figure 1 System overall block diagram
3 Main Function Circuit Design
3.1 Preamplifier module
The preamplifier circuit uses the high-efficiency, rail-to-rail, low-noise op amp chip OPA350 to form a common-phase broadband amplifier circuit. The signal input terminal is connected in series with a capacitor to achieve DC isolation and coupling. At the same time, due to the single power supply, a 2.5V bias is given to the common-phase end of the op amp. The feedback resistor is set as a potentiometer, which can dynamically change the gain of the amplifier from 1 to 20 times and the gain is continuously adjustable.
3.2 Triangle wave generation circuit
The triangle wave generating circuit is shown in Figure 2. The NE555 chip is used to form a triangle wave circuit, and the constant current source is used to linearly charge and discharge the capacitor C1 to obtain a triangle wave. When the work starts, the pin 3 of the 555 chip is high, the diode D4 is turned on, and D3 is turned off, so that D1 is turned on and D2 is turned off. The constant current source composed of T1, T2, and R1 charges C1 linearly through D1. When the charging makes the voltage across C1 reach 2/3Vcc, the output level of pin 3 is reversed and becomes low. At this time, the conduction state of D1, D2, D3, and D4 is completely opposite. The constant current source composed of T3, T4, and R2 below discharges C1 linearly through D2. When the discharge makes the voltage across C1 reach 1/3Vcc, pin 3 is reversed to a high level again. This cycle is repeated to achieve the generation of a periodic triangle wave signal. The output is drawn from both ends of C1 to obtain a triangle wave signal with good linearity. A first-level in-phase follower is connected to achieve the purpose of isolation between the front and rear stages. C1 uses a polystyrene capacitor with low leakage current and fast response speed to ensure better performance.
Figure 2 Triangle wave generating circuit
The frequency and amplitude of the triangular wave are calculated as follows: Let the charge and discharge current through the resistors R1 and R2 be Io, where Io=Vbe/R (where Vbe is the conduction voltage of the transistor), then
The triangle wave period is T=t1+t2, and the frequency is f=1/T. The measured triangle wave frequency of this circuit is 120 kHz (it will deviate from the calculated value because the transistor conduction voltage drop is not strictly 0.7 V).
3.3 Dual comparator circuit (PWM wave generation circuit)
The dual comparator circuit is composed of a low-power dual comparator chip LM393 that can work with a single power supply. In order to improve system efficiency and reduce unnecessary opening and closing of the CMOS tube in the subsequent H-bridge, two triangular waves with different biases are used to compare with the upper and lower halves of the audio signal, respectively, to generate two corresponding PWM wave signals for processing by the subsequent drive circuit. The dual comparison waveform is shown in Figure 3. It is worth noting that the upper half is compared and processed as the audio signal connected to the negative end of the comparator and the triangular wave signal connected to the positive end; the lower half is compared in the opposite way, so that a mutual correspondence is formed. When the corresponding PWM wave is formed in one half of the audio signal, the other half is at a low level, which can ensure that the CMOS tube in the subsequent H-bridge does not open and close unnecessarily, thereby reducing system power loss. Use the potentiometer to adjust the upper comparison triangle wave bias to 3 V, and the lower comparison triangle wave bias to 2 V. It should also be noted that the triangle wave signal should be slightly larger than the audio signal amplitude within the comparison range, and the bias adjustment should be more accurate to prevent certain points of the audio signal from not being compared, resulting in distortion when the subsequent filtering restores the original signal.
Figure 3 Dual-channel comparison waveform
3. 4 H-bridge complementary symmetrical output circuit (followed by fourth-order Butterworth filter)
The H-bridge complementary symmetrical circuit is shown in Figure 4. The complementary push-pull amplifier circuit is composed of field effect tubes IRF9540 and IRF540 with low on-resistance, fast switching rate and little temperature influence. The symmetrical output mode is used to make full use of the power supply voltage. The peak-to-peak value of the floating output carrier can reach 10 V, which effectively improves the output power.
Figure 4 H-bridge complementary symmetrical output circuit
The two signals amplified by the H-car complementary symmetry circuit are respectively low-pass filtered by a fourth-order Butterworth filter to filter out the high-frequency carrier, and the amplified audio signal is added to both ends of the 8 Ω load. The upper cutoff frequency of the filter is about 20 kHz, and the characteristics are flat within the passband, with good results. Note that a high-power inductor should be selected here , otherwise it will reduce the signal amplitude and cannot achieve higher power.
3.5 Short circuit protection module
The short-circuit protection circuit is shown in Figure 5. A 0.1Ω small resistor is connected to the system and connected in series with an 8Ω load resistor. The voltage sampled at both ends of the sampling resistor is amplified and then compared with the set reference voltage to control the power supply and power failure of the functional part, which plays a protective role. The amplification part uses the chip NE5532 to form a subtraction amplifier. While amplifying, the two-end signal at both ends of the resistor can be converted into a single-end signal. The amplifier gain is:
The amplified signal passes through the peak detection part composed of D1, C1, and R5, and the detected signal amplitude value is sent to the comparator for comparison with the set reference voltage. The comparator uses the low-power, fast-response dual-channel comparison chip LM393. The negative end of the comparator is set to 5.1V using the voltage regulator D6 and C3 and R7. The comparator is connected in a hysteresis comparison mode. Once overcurrent occurs, it can be self-locked. At this time, the high level output by the comparator turns on the transistor T1, the ground control end of the relay is connected to the ground, the relay is energized, and the power supply of the power amplifier part is cut off to achieve the protection purpose. Because the comparator is self-locking, after solving the overcurrent problem, the power supply of the protection module is turned off to re-enter the protection state. D2, D3, R6, and C2 form a power-on delay circuit. After power failure, C2 quickly discharges through D2 to prevent the residual voltage on C2 at the beginning from affecting pin 3, and prevent the comparator from entering the self-locking state under abnormal conditions, so that the protection module cannot function normally.
Figure 5 Short circuit protection circuit
3.6 Power measurement and display circuit (effective value detection and AD conversion circuit)
The power measurement circuit uses the true RMS detection chip AD637 to detect the true RMS value of the signal, and then samples it through the 12-bit serial interface and 20kHz sampling rate AD chip ADS1286 and invites it to the FPGA for processing by the program to calculate the power and display it. As shown in Figure 6.
Figure 6 Power measurement and display circuit
The input is suffixed with OPA604 to form an emitter follower to achieve the effect of isolating the front and rear stages. Changing the value of the average capacitor can set the average time constant and determine the low-frequency accuracy, the size of the output ripple and the stabilization time. The AC ripple component can be reduced by increasing the value of this capacitor, but this will increase the settling time, so a second-order active low-pass filter is used to reduce the output ripple . After the true effective value is obtained, it is directly fed into the ADS1286 for analog-to-digital conversion, and then processed by the FPGA to calculate the output power of the system and display it.
4 System Software Design
According to the requirements of the topic, the system power measurement and display functions are realized. The hardware uses 8-bit CPU AT89S52 and is implemented through C51 programming. The single-chip microcomputer is responsible for controlling ADS1286, collecting data, calculating power and sending it for display. The FPGA (using Atera's Cyclone series EP1C6QC240) is used as a bus controller to manage the data exchange between the LCD and A/D and the single-chip microcomputer. The programming is implemented in the environment of Quartus9.1 using VerilogHDL language.
5 Test methods and results
5.1 Test Equipment
15 MHz function signal generator Model: Agilent33120A
Digital Oscilloscope Model: Tektronix TDS 1002, dual channel, 60 MHz
DC power supply model: SG173SB3, voltage and current stabilized type
Fluke 45 dual display multimeter
5.2 Test plan and results analysis
1) Power display error measurement: Agilent signal source is used to provide input audio signal. The oscilloscope measures the peak voltage Vo on the load at the single-ended output test point. The actual power is calculated according to the formula, and then the display error is calculated. The results are shown in Table 1.
Table 1 Amplifier circuit passband performance test data table
From the data in the table, it can be seen that the system power display module has a 4-digit display, an accuracy better than 5%, and a small error.
2) Noise Use the Agilent signal source to provide an input audio signal (ensuring that the signal frequency is below 20 kHz), use a 0.1μF capacitor to short-circuit the input terminal to the ground, and use an oscilloscope to measure the noise level at the output terminal. The noise measured at this time is 2.96mV.
3) Efficiency measurement Use a DC power supply to power the power amplifier circuit separately to test the efficiency. The power supply voltage is +5 V. Use the same method as the passband measurement to give the input signal, use an oscilloscope to observe the output signal amplitude, adjust the output to 200 mW and 500 mW, connect a 4.5-digit digital multimeter in series to the amplifier circuit, and measure the circuit current I. Calculate the power amplifier efficiency according to the formula, and the results are shown in Table 2.
Table 2 Power amplifier circuit efficiency test data table
It can be seen from the table that when the output power is 500mW, the efficiency of the power amplifier circuit is as high as 64.10%, which greatly meets the requirements of the question; when the output is 200mW, the efficiency also reaches 43.96%. The system can achieve high-efficiency audio amplification.
4) For overcurrent protection measurement, the same method as the passband measurement is used to give the input signal, and the output signal amplitude is observed with an oscilloscope. When the two ends of the load are short-circuited, the short-circuit module warning light will light up, the power supply of the power amplifier will be cut off, and the output will become zero, thus achieving the purpose of overcurrent protection.
6 Conclusion
The system realizes the amplification of audio signals and completes functions such as high-efficiency power amplification, signal conversion, power measurement and display, and overcurrent protection. The system has good performance and high indicators in terms of power and efficiency. The amplification circuit, signal conversion, power measurement and short-circuit protection have achieved good results. In particular, the power can reach 1.16 W, the efficiency can reach 64%, the noise is very low, and the power measurement display error is small. The operation is simple and the human-computer interaction is flexible.
Previous article:Discussion on a processor-based video encoder platform
Next article:PLC power module maintenance training
Recommended ReadingLatest update time:2024-11-16 21:34
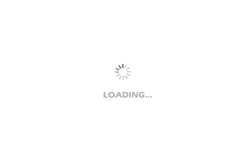
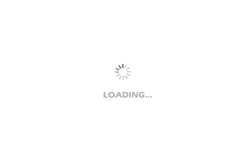
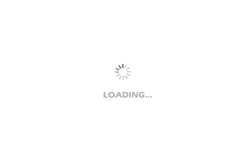
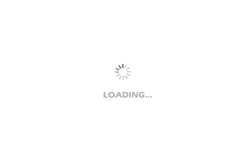
- Popular Resources
- Popular amplifiers
-
西门子S7-12001500 PLC SCL语言编程从入门到精通 (北岛李工)
-
Siemens Motion Control Technology and Engineering Applications (Tongxue, edited by Wu Xiaojun)
-
How to read electrical control circuit diagrams (Classic best-selling books on electronics and electrical engineering) (Zheng Fengyi)
-
MCU C language programming and Proteus simulation technology (Xu Aijun)
- MathWorks and NXP Collaborate to Launch Model-Based Design Toolbox for Battery Management Systems
- STMicroelectronics' advanced galvanically isolated gate driver STGAP3S provides flexible protection for IGBTs and SiC MOSFETs
- New diaphragm-free solid-state lithium battery technology is launched: the distance between the positive and negative electrodes is less than 0.000001 meters
- [“Source” Observe the Autumn Series] Application and testing of the next generation of semiconductor gallium oxide device photodetectors
- 采用自主设计封装,绝缘电阻显著提高!ROHM开发出更高电压xEV系统的SiC肖特基势垒二极管
- Will GaN replace SiC? PI's disruptive 1700V InnoMux2 is here to demonstrate
- From Isolation to the Third and a Half Generation: Understanding Naxinwei's Gate Driver IC in One Article
- The appeal of 48 V technology: importance, benefits and key factors in system-level applications
- Important breakthrough in recycling of used lithium-ion batteries
- Innolux's intelligent steer-by-wire solution makes cars smarter and safer
- 8051 MCU - Parity Check
- How to efficiently balance the sensitivity of tactile sensing interfaces
- What should I do if the servo motor shakes? What causes the servo motor to shake quickly?
- 【Brushless Motor】Analysis of three-phase BLDC motor and sharing of two popular development boards
- Midea Industrial Technology's subsidiaries Clou Electronics and Hekang New Energy jointly appeared at the Munich Battery Energy Storage Exhibition and Solar Energy Exhibition
- Guoxin Sichen | Application of ferroelectric memory PB85RS2MC in power battery management, with a capacity of 2M
- Analysis of common faults of frequency converter
- In a head-on competition with Qualcomm, what kind of cockpit products has Intel come up with?
- Dalian Rongke's all-vanadium liquid flow battery energy storage equipment industrialization project has entered the sprint stage before production
- Allegro MicroSystems Introduces Advanced Magnetic and Inductive Position Sensing Solutions at Electronica 2024
- Car key in the left hand, liveness detection radar in the right hand, UWB is imperative for cars!
- After a decade of rapid development, domestic CIS has entered the market
- Aegis Dagger Battery + Thor EM-i Super Hybrid, Geely New Energy has thrown out two "king bombs"
- A brief discussion on functional safety - fault, error, and failure
- In the smart car 2.0 cycle, these core industry chains are facing major opportunities!
- The United States and Japan are developing new batteries. CATL faces challenges? How should China's new energy battery industry respond?
- Murata launches high-precision 6-axis inertial sensor for automobiles
- Ford patents pre-charge alarm to help save costs and respond to emergencies
- New real-time microcontroller system from Texas Instruments enables smarter processing in automotive and industrial applications
- TI official website cannot be accessed! ? ?
- Everyone, is it harder to be a hardware engineer or a software engineer?
- Discussion: Can the COVID-19 pandemic help companies related to 5G and wifi6 technology? Get 5-20 Chip Points!
- How to use arrays in C language for microcontrollers
- [GD32L233C-START Review] 17. CMSIS-RTOS2 RTX5 ported to GD32L233 (kernel, multithreading)
- Switching power supply interest group recruitment, just for learning switching power supply! Ps: People without perseverance please bypass!
- [Perf-V Review] Pengfeng Development Board Unboxing Experience
- Download the topics of the National Undergraduate Electronic Design Competition over the years
- Regarding the abnormal problem of nrf52810 sending and receiving multiple times, I hope the experts can help
- Programmable system-level chips are developing strongly, and Cypress is promoting it