As we all know, VRLA battery (valve-regulated sealed lead-acid battery) is also a lead-acid battery. Since it is a lead-acid battery, it should have the same working principle as the open lead-acid battery. This means that the carriers for energy conversion and energy storage of VBLA batteries are the same as those of the open type, and the substances participating in the electrochemical reaction are also the same. When charging, the positive electrode is converted from lead sulfate (PbSO4) to lead dioxide (Pb02), and then the electrical energy is converted into chemical energy and stored in the positive plate; the negative electrode is converted from lead sulfate (PbSO4) to spongy lead (spongy Pb), and then the electrical energy is converted into chemical energy and stored in the negative plate. When discharging, the positive electrode is converted from lead dioxide (PbO2) to lead sulfate (PbSO4) and the chemical energy is converted into electrical energy to supply power to the load, and the negative electrode is converted from spongy lead (spongy Pb) to lead sulfate (PbSO4) and the chemical energy is converted into electrical energy to supply power to the load. Of course, the above charging or discharging process can only be achieved when the positive and negative electrodes simultaneously carry out electrochemical reactions in the same equivalent and state (such as charging or discharging state). It is impossible for the positive electrode alone or the negative electrode alone to complete the above electrochemical reaction at any time and under any circumstances. It can be seen from this that if the positive plate in a battery is good and the negative plate is broken, it is equivalent to the battery becoming a scrapped battery. Similarly, if the negative plate in a battery is good and the positive plate is broken, the battery can only be a scrapped battery. In addition, the amount of substances that can participate in energy conversion in the positive plate (the amount of active substances) and the amount of substances that can participate in energy conversion in the negative plate (the amount of active substances) must match each other. If they do not match, one is more and the other is less, the extra part is a waste, and the amount of each substance participating in the electrochemical reaction that matches the other substance is different. Scientists call the amount of each substance that can convert one ampere-hour of electricity (1 from) into chemical energy and store it as electrochemical equivalent (that is, the amount of equivalent substance that can convert electrical energy and chemical energy into each other). The electrochemical equivalent of each active substance is calculated from its electrochemical reaction equation. The entire working principle of the lead-acid battery mentioned above (including the electrochemical equivalent) can be expressed by the following electrochemical reaction equation: PbO2+Pb+2H2S04←→2PBS04+2H20
When the electrochemical reaction formula is carried out from left to right, it is the discharge reaction of the battery. When the electrochemical reaction formula is carried out from right to left, it is the charge reaction of the battery.
It can be seen from the electrochemical reaction formula that when the battery is discharged, the positive electrode must have 1 gram molecular weight of lead dioxide, the negative electrode must have 1 gram molecular weight of sponge lead, and 2 gram molecular weights of sulfuric acid should also participate in the discharge process in order to proceed smoothly. Using the Faraday constant in Faraday's law, through the above electrochemical reaction equation, it is calculated that the electrochemical equivalent of lead dioxide is 41.46g/Ah, and the electrochemical equivalent of sponge lead is 33.87s/Ah. That is to say: in order for the VRLA battery to discharge one ampere-hour of electricity, the positive electrode must have 41.46g of lead dioxide active material, and the negative electrode must have 33.87g of sponge lead active material in the presence of sufficient sulfuric acid to achieve the desired result. In order for the VRLA battery to discharge 100Ah of electricity, the positive electrode must have 4146g of lead dioxide and the negative electrode must have 3387g of sponge lead. This explains in principle why the capacity of the battery is determined by the amount of active material. This is also the fundamental reason why users say that heavy batteries are of better quality than light batteries when buying batteries. Of course, the electrochemical equivalent listed here is only a theoretical value. In addition to the same working principle as the electrochemical reaction mode of the open lead-acid battery, the VRLA battery also has a different working principle from the open lead-acid battery, that is, the cathode absorption principle. The so-called cathode absorption principle refers to the fact that when the battery is charging, especially at the end of charging, the positive electrode will produce oxygen. Since the VRLA battery is fully sealed, the gas generated will not be released to the battery body through the opening at any time like the open battery, and the generated gas will accumulate in the battery slot. As the amount of gas accumulated inside the battery continues to increase, the pressure inside the battery gradually rises. Because there is a certain internal pressure inside the battery, the oxygen generated by the positive electrode will run to the negative electrode. Since oxygen atoms are generated on the positive electrode, and oxygen atoms have strong oxidizing properties, these oxygen atoms with strong oxidizing power will oxidize the sponge-like lead that has just been generated at the negative electrode during charging and has great activity to generate lead oxide. The lead oxide then reacts with sulfuric acid to generate lead sulfate and water. Lead sulfate is the product of negative electrode discharge. Lead sulfate generates sponge-like lead during charging. Sponge-like lead absorbs the oxygen generated at the positive electrode to generate lead oxide. This reaction is repeated over and over again. The oxygen generated at the positive electrode is absorbed by the negative electrode. No oxygen will be generated no matter how much it is charged. The internal pressure of the battery will not continue to rise, and there is no need to worry about the battery exploding. In order to prevent the battery from exploding due to the accumulation of gas inside the battery under special circumstances, a safety valve is specially set in the upper cover of the battery during design. When the internal pressure of the battery reaches a certain value, the safety valve will automatically open. After releasing a certain amount of gas to reduce the internal pressure, the safety valve will automatically close. The above is the cathode absorption principle of the ⅧIA battery. It is precisely because of the discovery and invention of the cathode absorption principle of this battery that the open lead-acid battery can be made fully sealed, and the VRLA battery came into being.
Of course, in order to maintain the cathode absorption principle of VRLA batteries, the first prerequisite is that the battery must be sealed. If it is not sealed, there is no certain internal pressure inside the battery, and the oxygen generated by the positive electrode cannot run to the negative electrode and be absorbed by the negative electrode, and the oxygen will run out. The oxygen that runs away is equivalent to the water inside the battery running away. If the battery loses water, it should be replenished. If it needs to be replenished, it is no longer called a VRLA battery, and it becomes an open battery. It can be seen that the sealing performance of VRLA batteries is a very critical technical indicator. Users should attach great importance to this issue when selecting batteries. Even a slight leakage or seepage will directly affect the service life of the battery. If there is such a battery in the battery pack, it will affect the comprehensive performance of the entire battery pack because this battery will become a backward battery first, and it will also cause the voltage of each battery in the battery pack to be unbalanced, forming a vicious circle. This is why the YD/T799 standard of the Ministry of Posts and Telecommunications stipulates that the gas recombination rate of the battery should be above 95%.
Of course, in order to make the cathode absorption of VRLA battery go well, it is necessary to ensure that its gas recombination rate is high, and the generated gas basically generates water and returns to the battery. In addition to airtightness being a very important issue, it is also necessary to consider whether the supporting measures are effective. For example: In terms of structure, VRLA batteries must be lean type, and sufficient space and channels must be left to allow the oxygen generated by the positive electrode to quickly and smoothly run to the negative electrode and be absorbed by the negative electrode. This is why VRLA batteries do not have excess electrolyte. Another example: The ultra-fine glass fiber separator used should have a large enough porosity to ensure that the oxygen generated by the positive electrode can run to the negative electrode through the small holes of the separator and be absorbed. Therefore, the quality of the separator used in VBLA batteries is also a crucial issue.
When charging VRLA batteries, the oxygen generated by the positive electrode is absorbed by the negative electrode, so the open battery can be made into a sealed battery. Then, does the hydrogen generated by the negative electrode when charging still exist? Doesn't the battery still have the risk of dehydration and explosion? Scientists have solved this problem by changing the negative electrode alloy formula and using new alloy materials (such as lead-calcium alloy) to increase the potential of hydrogen discharge (obtaining electrons to generate hydrogen) on this material (called increasing the overpotential of hydrogen). Originally, when the charging voltage reaches a certain value, hydrogen ions will discharge on the cathode to generate hydrogen. Due to the use of lead-calcium alloy, when the charging voltage reaches the original value, hydrogen ions will not discharge and hydrogen will not be generated. However, no matter how the alloy formula is changed, and no matter how the overpotential of hydrogen is increased, when the charging voltage reaches the potential of hydrogen ion discharge, hydrogen will always be generated. Why do manufacturers specify a floating charge voltage value within a certain range for their batteries? The reason is to control the generation of hydrogen and prevent the battery from losing water.
Previous article:How to deal with internal short circuit of battery
Next article:Design of a battery graded constant current charging power supply
Recommended ReadingLatest update time:2024-11-16 21:41
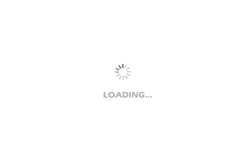
- Popular Resources
- Popular amplifiers
- MathWorks and NXP Collaborate to Launch Model-Based Design Toolbox for Battery Management Systems
- STMicroelectronics' advanced galvanically isolated gate driver STGAP3S provides flexible protection for IGBTs and SiC MOSFETs
- New diaphragm-free solid-state lithium battery technology is launched: the distance between the positive and negative electrodes is less than 0.000001 meters
- [“Source” Observe the Autumn Series] Application and testing of the next generation of semiconductor gallium oxide device photodetectors
- 采用自主设计封装,绝缘电阻显著提高!ROHM开发出更高电压xEV系统的SiC肖特基势垒二极管
- Will GaN replace SiC? PI's disruptive 1700V InnoMux2 is here to demonstrate
- From Isolation to the Third and a Half Generation: Understanding Naxinwei's Gate Driver IC in One Article
- The appeal of 48 V technology: importance, benefits and key factors in system-level applications
- Important breakthrough in recycling of used lithium-ion batteries
- Innolux's intelligent steer-by-wire solution makes cars smarter and safer
- 8051 MCU - Parity Check
- How to efficiently balance the sensitivity of tactile sensing interfaces
- What should I do if the servo motor shakes? What causes the servo motor to shake quickly?
- 【Brushless Motor】Analysis of three-phase BLDC motor and sharing of two popular development boards
- Midea Industrial Technology's subsidiaries Clou Electronics and Hekang New Energy jointly appeared at the Munich Battery Energy Storage Exhibition and Solar Energy Exhibition
- Guoxin Sichen | Application of ferroelectric memory PB85RS2MC in power battery management, with a capacity of 2M
- Analysis of common faults of frequency converter
- In a head-on competition with Qualcomm, what kind of cockpit products has Intel come up with?
- Dalian Rongke's all-vanadium liquid flow battery energy storage equipment industrialization project has entered the sprint stage before production
- Allegro MicroSystems Introduces Advanced Magnetic and Inductive Position Sensing Solutions at Electronica 2024
- Car key in the left hand, liveness detection radar in the right hand, UWB is imperative for cars!
- After a decade of rapid development, domestic CIS has entered the market
- Aegis Dagger Battery + Thor EM-i Super Hybrid, Geely New Energy has thrown out two "king bombs"
- A brief discussion on functional safety - fault, error, and failure
- In the smart car 2.0 cycle, these core industry chains are facing major opportunities!
- The United States and Japan are developing new batteries. CATL faces challenges? How should China's new energy battery industry respond?
- Murata launches high-precision 6-axis inertial sensor for automobiles
- Ford patents pre-charge alarm to help save costs and respond to emergencies
- New real-time microcontroller system from Texas Instruments enables smarter processing in automotive and industrial applications
- What is an ISO Connector?
- Power consumption of CCFL driver circuit based on Royer topology
- MSP432E401Y Motor Encoder QEI Module
- i.MX8 Mini series chip core board (MYC-C8MMX) data sharing
- BQ34Z100 operation process
- Power adapter indoor use symbol requirements and pictures
- How to use the single-cell battery charging chip TP4054 with a single-cell fuel gauge chip to achieve accurate power monitoring and reliable charging...
- Limitations of Flash_API for C2000 Series (28335) DSP
- This single-power supply to dual-power supply op amp
- Ultrasonic transducer drive and impedance matching circuit design