There are several types of LED packaging: bracket row packaging, surface mount packaging, and module packaging. These packaging methods are common and commonly used. 1. Conventional existing packaging methods and application fields Bracket row packaging was the first to be used to produce single LED devices. This is the common lead-type light-emitting diode (including piranha packaging). It is suitable for instrument indicator lights, urban lighting projects, advertising screens, guardrails, traffic lights, and some products and fields that are currently commonly used in my country. SMD is a leadless package with small size and thinness. It is very suitable for keyboard display lighting of mobile phones, backlight lighting of TV sets, and electronic products that need lighting or indication. In recent years, SMD packaging has developed in the direction of large size and high power. Three or four LED chips are packaged in one SMD, which can be used to assemble lighting products. Module packaging is also a multi-chip package. Dozens or hundreds of LED chips are packaged on an alumina or aluminum nitride substrate with a smaller size and high packaging density. The internal connection is a mixed type, that is, there are multiple chips in series and several parallel connections. This type of package is mainly used to expand power and is used for lighting products. Due to the high density of the module package, the heat generated during application is large, and heat dissipation is the primary problem to solve the application. Devices produced by the above packaging methods have a common feature for the production of lighting fixtures: the number of thermal resistance channels is large, it is difficult to produce high-quality lighting fixtures, and the connection processing requirements between the module itself and the radiator are relatively high. At present, all packaging methods are to mix yellow phosphor (YAG) and epoxy resin in different proportions, directly apply them to the blue LED chip, and then heat and cure. The advantage of this common method is that it saves materials, but the disadvantage is that it is not conducive to heat dissipation and the phosphor will also age. Because epoxy resin and phosphor are not good thermal conductive materials, and wrapping the entire chip will affect heat dissipation. This method is obviously not the best solution for manufacturing LED lighting fixtures. [page] At present, high-power chips produced abroad, white light chips above 0.5 watts, are coated with a uniform layer of YAG phosphor paste on the blue light chip, and the appearance is a yellow cube. (Except for the two gold pads used for welding, there is no phosphor. This method can improve the light efficiency compared with the previous commonly used method, so it is widely used abroad.) When packaging, just weld this white light chip on the designed circuit board, eliminating the process of coating phosphor. It brings convenience to lamp manufacturers, but domestic chip suppliers are currently unable to mass-produce such LED white light chips. [page] my country is one of the earliest countries to develop LED street lights. Currently, it is also used well in China. The reason is that the country attaches great importance to the "low-carbon economy". In 2009, my country promoted 10,000 LED street lights in 10 cities. Many cities have experimental sections to test the feasibility of LED street lights. my country is based on the application of street lights, while foreign countries (Osram, Nichia, Samsung and other companies) are based on indoor lighting. It is still unclear which of these two routes has more advantages. As far as my country is concerned, it is due to national conditions that LED street lighting is the first application direction. The reason is that my country's national income is low, and the cost of LED indoor lighting is high, which is unacceptable to ordinary people. The use of LED street lights is funded by the government, and LED street light manufacturers have taken a fancy to this point. In fact, the working conditions of LED street lights are more stringent and demanding than indoor LED lighting fixtures. If the quality can be achieved (heat dissipation, service life, color rendering, reliability, etc.), then it will be easier to make indoor LED lighting. At present, foreign LED giants are launching hundreds or even thousands of LED indoor lighting fixtures, with prices ranging from US$20 to US$75 and power ranging from a few watts to 20 watts. However, the packaging methods they use are all mentioned above. Only Philips, which uses phosphor coating on the LED lampshade, was rated as one of the most innovative LED lighting products in 2009. The author believes that all LED lighting fixtures should be manufactured using multi-chip packaging and module packaging (module packaging is a high-density multi-chip packaging), and it is best to package the LED chip directly on the main body of the lamp, so that the number of thermal resistance is the least and a better heat dissipation effect can be achieved. Or a circuit body coated with copper foil is made on the main body of the lamp, and its thermal resistance is also low. The power of LED lighting must be at least several watts, so multiple chips are used, and the previous packaging process is not applicable. New methods and processes must be adopted. It is difficult to produce high-quality and highly reliable LED lamps by assembling multiple packaged LED devices. I hope that technicians engaged in the manufacture of LED lamps can understand this. 2. Innovation of phosphor coating process The phosphor coating of module packaging is currently seen to be directly coating the phosphor paste on the chip. The phosphor of the same module is relatively consistent, but for mass production, different modules may have color differences. A better way is to use LED phosphor film or diaphragm. Film and diaphragm can be mass-produced with good consistency. LED lamps are multi-chip packaged, and the light emitted is mixed. After being converted into white light through phosphor film or diaphragm, the color difference can be eliminated. The requirements for film and diaphragm are: 1. Able to transmit light, with a thickness between 0.1 and 0.5 mm, uniform phosphor and smooth appearance. 2 The light conversion efficiency should be high, the stability should be good, the life should be long and the anti-aging performance should be good. 3 It can be made with or without a base, or made into a thin sheet, depending on the implementation conditions and cost. The base should be colorless, transparent and aging resistant. 4. Easy to process and shape, can be cut to any size, and has low cost. Another method is to mix fluorescent powder and transparent plastic in proportion, and directly produce a lampshade with fluorescent powder through an injection molding machine and a mold, so that the lampshade can convert blue light into white light. This is more convenient and easier, because the lampshade converts mixed blue light, so the output white light has no color difference, and the light is softer and does not produce glare. Third, in order to better solve the problem of LED heat dissipation, the lamp design and packaging should be considered together, and the packaging and the heat sink for LED heat dissipation should be made into a whole to effectively reduce the number of thermal resistance paths. This is a very effective way to improve the heat dissipation of lamps. Currently, LED fluorescent lamps on the market do not have heat sinks, so such lamps cannot achieve high power, high quality and long life. Correct product design should take heat sinks into consideration. Industrial production is to use a mold to extrude a semicircular aluminum profile with fins for the heat sink of the LED fluorescent lamp, and then cut the required length according to the power. Then, an aluminum-based copper foil circuit is made, and the chip is fixed on the copper foil, connected with gold wire or bonded with a bonding machine. Such lamps have good heat dissipation effect, with only two thermal resistances, which is one or two less than the commonly used packaging method. It effectively reduces the temperature of the chip and plays a role in improving the quality and life of LED fluorescent lamps. Another method is to design a protrusion on the aluminum profile, mill out many rectangles as needed, and use a common (0.8-1.0mm thick) PCB circuit board to open a rectangular hole according to the rectangle of the aluminum profile, paste or rivet the PCB circuit board on the aluminum profile, and fix the LED chip on the rectangular protrusion on the aluminum profile, and then use gold wire to connect the circuit on the PCB board and the chip. This production process is the best, with only one thermal resistance and the best heat dissipation effect. Manufacturers of LED lamps should give priority to this solution, followed by the method of making copper foil circuits on aluminum profiles. Only such innovation can effectively solve the heat dissipation problem of LED long strip lamps and improve the quality and life of LED fluorescent lamps. With the continuous exploration and improvement of technology, the future development of LED lighting is showing a bright future. |
Previous article:MAX1870 Introduction and Application
Next article:High-speed PCB design solution based on Cadence
Recommended ReadingLatest update time:2024-11-16 18:08
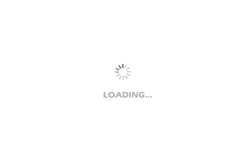
- MathWorks and NXP Collaborate to Launch Model-Based Design Toolbox for Battery Management Systems
- STMicroelectronics' advanced galvanically isolated gate driver STGAP3S provides flexible protection for IGBTs and SiC MOSFETs
- New diaphragm-free solid-state lithium battery technology is launched: the distance between the positive and negative electrodes is less than 0.000001 meters
- [“Source” Observe the Autumn Series] Application and testing of the next generation of semiconductor gallium oxide device photodetectors
- 采用自主设计封装,绝缘电阻显著提高!ROHM开发出更高电压xEV系统的SiC肖特基势垒二极管
- Will GaN replace SiC? PI's disruptive 1700V InnoMux2 is here to demonstrate
- From Isolation to the Third and a Half Generation: Understanding Naxinwei's Gate Driver IC in One Article
- The appeal of 48 V technology: importance, benefits and key factors in system-level applications
- Important breakthrough in recycling of used lithium-ion batteries
- Innolux's intelligent steer-by-wire solution makes cars smarter and safer
- 8051 MCU - Parity Check
- How to efficiently balance the sensitivity of tactile sensing interfaces
- What should I do if the servo motor shakes? What causes the servo motor to shake quickly?
- 【Brushless Motor】Analysis of three-phase BLDC motor and sharing of two popular development boards
- Midea Industrial Technology's subsidiaries Clou Electronics and Hekang New Energy jointly appeared at the Munich Battery Energy Storage Exhibition and Solar Energy Exhibition
- Guoxin Sichen | Application of ferroelectric memory PB85RS2MC in power battery management, with a capacity of 2M
- Analysis of common faults of frequency converter
- In a head-on competition with Qualcomm, what kind of cockpit products has Intel come up with?
- Dalian Rongke's all-vanadium liquid flow battery energy storage equipment industrialization project has entered the sprint stage before production
- Allegro MicroSystems Introduces Advanced Magnetic and Inductive Position Sensing Solutions at Electronica 2024
- Car key in the left hand, liveness detection radar in the right hand, UWB is imperative for cars!
- After a decade of rapid development, domestic CIS has entered the market
- Aegis Dagger Battery + Thor EM-i Super Hybrid, Geely New Energy has thrown out two "king bombs"
- A brief discussion on functional safety - fault, error, and failure
- In the smart car 2.0 cycle, these core industry chains are facing major opportunities!
- The United States and Japan are developing new batteries. CATL faces challenges? How should China's new energy battery industry respond?
- Murata launches high-precision 6-axis inertial sensor for automobiles
- Ford patents pre-charge alarm to help save costs and respond to emergencies
- New real-time microcontroller system from Texas Instruments enables smarter processing in automotive and industrial applications
- In the information age, how to protect information security?
- [GD32L233C-START Review] RTX operating system
- Bluetooth controlled stepper motor driver and firmware - Seeking paid technical assistance
- BAT chip industry procurement recruitment
- A look at hybrid electric vehicles from the perspective of driving methods and related main technologies
- Power module viewing operation
- NUCLEO-G431RB review -> ADC basic configuration (without oversampling)
- Design of Phase Detection Broadband Frequency Measurement System Based on FPGA
- EEWORLD University Hall----Challenges and solutions for ultrasonic water and gas meter design
- Wi-Fi 6E FEM, unleashing the full performance of the 6GHz band