1 Introduction
The accurate measurement of the remaining capacity of the battery has always been a very critical issue in the development of electric vehicles. An effective battery management system is conducive to improving the life of the battery. Therefore, the accurate estimation of the battery SOC has become the central issue of the battery energy management system of electric vehicles. If the battery SOC can be correctly estimated, the power provided by the battery can be reasonably utilized and the service life of the battery pack can be extended.
The solution adopts bus networking and uses fieldbus to complete data exchange between nodes. In the distributed solution, the multi-energy controller is the main control ECU, which communicates with multiple subordinate ECUs through the fieldbus. During the working process, the communication submodule of each controller runs in the background in the form of timer or interrupt to complete the data transmission and reception, saving the main process resource expenditure. As shown in Figure 1.
The battery SOC value is sent to the multi-energy controller via the CAN bus by the battery controller, and the vehicle's operating mode is determined by the multi-energy controller through a certain logic algorithm by collecting information from each ECU. Once these parameters are determined, we can decide whether to start or shut down the engine, and we can also decide which state the motor should work in. For example, when the battery's SOC value is between 50% and 70%, the multi-energy controller calculates that the vehicle's operating mode is in the starting mode, which means that the current system has sufficient electrical energy and does not need to start the engine, and the motor can work in a driving mode.
2 System Hardware Composition
As shown in Figure 2, the battery controller can communicate with other control systems in the external car through the CAN bus network. One battery management ECU (electronic control unit) and four battery pack information detection ECUs; the single cells we use are combined into 24 battery packs. We configure a measurement unit for every 6 battery packs, that is, there are battery pack ECU1 to ECU4. The four battery pack ECUs and the battery pack ECU form a CAN bus network, one CAN controller and the battery pack ECU form a CAN network inside the battery management system, and another CAN controller and other control systems in the car form a fiber optic CAN bus network for the entire vehicle.
Figure 2 Block diagram of the battery management ECU
As shown in Figure 3, the embedded microcontroller used in the battery pack ECU is the P87C591 single-chip microcomputer, which has an internal hardware integrated with a CAN controller and an A/D analog-to-digital conversion module. Each battery pack ECU manages 6 battery packs, and its function is to measure the voltage and temperature information of the 6 battery packs and send the collected information to the battery management ECU through the CAN bus. The voltages of the 6 battery packs are connected to the 6 A/D input ports of the P87C591 after passing through the voltage conditioning circuit. The signal lines of the 6 temperature sensors are connected to the same IO port of the P87C591.
Figure 3 Circuit diagram of battery pack ECU
3 CAN interface circuit design
In this design, P87C591 is used as the microcontroller. The interface circuit design between P87C591 and CAN driver chip is shown in Figure 4. It mainly consists of three parts: P87C591, photoelectric isolation circuit, and CAN driver. Photoelectric isolation circuit: In order to further suppress interference, photoelectric isolation circuit is often used in CAN bus interface. Photoelectric isolator is generally located between CAN controller and transceiver.
Figure 4 CAN communication module hardware design circuit diagram
The system overall program includes the initialization program and the main loop program, and its flow chart is shown in Figure 5:
Figure 5 Main program diagram
The system is first powered on, then CAN and timer are initialized, and the system waits for an interrupt. If there is an interrupt, the interrupt type is determined. If it is an interrupt from the SJA1000 controller, the data from the SJA1000 controller is read and the buffer is released. The interrupt is returned after the operation is completed. If it is a 50ms period interrupt from the timer, AD conversion is performed on the voltage and current data, the SOC value is calculated, and the relevant data is sent by CAN. The interrupt is returned after the operation is completed.
4 Conclusion
The data communication technology based on CAN bus has high reliability, real-time and flexibility. CAN bus has broad application prospects and development space in the application of nickel-hydrogen battery management system of hybrid electric vehicles.
Previous article:However, experts on overcharging and overdischarging suggest a simple way to extend the life of lithium batteries
Next article:Discussion on UPS power supply design ideas
Recommended ReadingLatest update time:2024-11-17 06:44
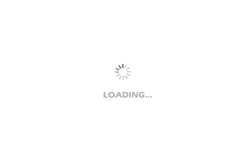
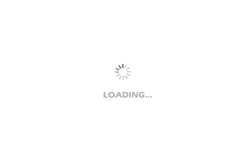
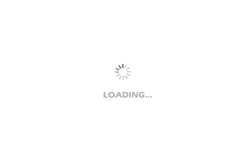
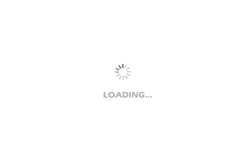
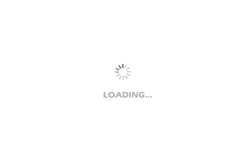
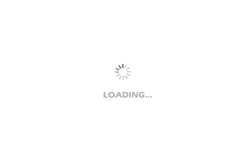
- Popular Resources
- Popular amplifiers
-
New Energy Vehicle Control System Inspection and Maintenance (Edited by Bao Pili)
-
Detailed explanation of big data technology system: principles, architecture and practice (Dong Xicheng)
-
Automotive CAN embedded intrusion detection system based on deep learning
-
Lightweight FPGA-based IDS-ECU architecture for automotive CAN networks
- MathWorks and NXP Collaborate to Launch Model-Based Design Toolbox for Battery Management Systems
- STMicroelectronics' advanced galvanically isolated gate driver STGAP3S provides flexible protection for IGBTs and SiC MOSFETs
- New diaphragm-free solid-state lithium battery technology is launched: the distance between the positive and negative electrodes is less than 0.000001 meters
- [“Source” Observe the Autumn Series] Application and testing of the next generation of semiconductor gallium oxide device photodetectors
- 采用自主设计封装,绝缘电阻显著提高!ROHM开发出更高电压xEV系统的SiC肖特基势垒二极管
- Will GaN replace SiC? PI's disruptive 1700V InnoMux2 is here to demonstrate
- From Isolation to the Third and a Half Generation: Understanding Naxinwei's Gate Driver IC in One Article
- The appeal of 48 V technology: importance, benefits and key factors in system-level applications
- Important breakthrough in recycling of used lithium-ion batteries
- Innolux's intelligent steer-by-wire solution makes cars smarter and safer
- 8051 MCU - Parity Check
- How to efficiently balance the sensitivity of tactile sensing interfaces
- What should I do if the servo motor shakes? What causes the servo motor to shake quickly?
- 【Brushless Motor】Analysis of three-phase BLDC motor and sharing of two popular development boards
- Midea Industrial Technology's subsidiaries Clou Electronics and Hekang New Energy jointly appeared at the Munich Battery Energy Storage Exhibition and Solar Energy Exhibition
- Guoxin Sichen | Application of ferroelectric memory PB85RS2MC in power battery management, with a capacity of 2M
- Analysis of common faults of frequency converter
- In a head-on competition with Qualcomm, what kind of cockpit products has Intel come up with?
- Dalian Rongke's all-vanadium liquid flow battery energy storage equipment industrialization project has entered the sprint stage before production
- Allegro MicroSystems Introduces Advanced Magnetic and Inductive Position Sensing Solutions at Electronica 2024
- Car key in the left hand, liveness detection radar in the right hand, UWB is imperative for cars!
- After a decade of rapid development, domestic CIS has entered the market
- Aegis Dagger Battery + Thor EM-i Super Hybrid, Geely New Energy has thrown out two "king bombs"
- A brief discussion on functional safety - fault, error, and failure
- In the smart car 2.0 cycle, these core industry chains are facing major opportunities!
- Rambus Launches Industry's First HBM 4 Controller IP: What Are the Technical Details Behind It?
- The United States and Japan are developing new batteries. CATL faces challenges? How should China's new energy battery industry respond?
- Murata launches high-precision 6-axis inertial sensor for automobiles
- Ford patents pre-charge alarm to help save costs and respond to emergencies
- Solution Download Littelfuse 2022 Latest Battery Solution Online Exhibition Hall
- What causes radio frequency interference in wireless communication networks?
- User Guide:TI LAUNCHXL-F28027 C2000 Piccolo LaunchPad
- [Raspberry Pico Review] -- Just received the sample today
- The six lies of open source. Are they true?
- 【ST NUCLEO-H743ZI Review】Testing SPI+TFT (3)
- MSP430 uses timer to measure frequency
- STEVAL-MKI109V3 FSM Experience Analysis
- High internal resistance amplifier design issues
- Inductor and capacitor knowledge points record