1 Introduction
Based on our many years of experience in DC system development and design and field application, this article attempts to explore the charging method of backup battery packs, hoping to play a role in inspiring others to study a more reasonable battery pack charging method.
2 Defects of current battery pack charging methods
In most current backup power sources (DC systems, UPS, etc.), energy storage is achieved by battery packs. Then the performance of the battery pack, which is the last guarantee for uninterrupted power supply, is crucial. Due to the semiconductor conversion technology and cost reasons, the charging method we have always adopted is to charge the entire series battery group with a single charger as shown in the figure below.
The charger is always connected in parallel with the battery pack in a constant voltage and current limiting mode. In theory, when the battery pack capacity is lost, the charger will automatically replenish it. However, in actual application, we found that this system has the following problems.
First, there are large differences in the characteristics of single batteries. Even batteries from the same batch have large deviations in their characteristics (especially in domestic batteries). Therefore, they are charged and discharged as a whole during operation. They cannot be charged and discharged according to the operating parameters and operating status of the single battery. This will inevitably cause some batteries to be overcharged or undercharged, and may also cause over-discharge. This is one of the important reasons why batteries generally fail to reach the nominal life when they are operated in groups.
Second, it is difficult to detect the voltage and internal resistance of single batteries in this operating mode. Now it is generally adopted to install a battery detection device separately, but the battery detection device cannot cooperate well with the charger. From the above two points, we can see that in this system, managing the battery according to the battery status (voltage, internal resistance, remaining capacity, temperature and other parameters) and charging curve is just empty talk. In addition, installing a battery detection device separately will inevitably increase the cost.
Third, with the advancement of semiconductor technology, high-frequency switching power supplies are replacing traditional thyristor rectifier power supplies with their advantages of small size, light weight, high efficiency and low noise. However, the charging method in Scheme 1 is adopted because the charger needs to provide a higher charging voltage and a larger output capacity, which has high requirements for devices, technology and process. As we all know, it is difficult for IGBT to exceed 20KHz, and if MOS-FET is used in a large current loop, the junction voltage drop is very large, and the heat generation is also very large. Therefore, due to the limitations of devices and processes, it is very difficult for a single high-frequency switching power supply (>20KHz) to have an output capacity exceeding 6KW. Therefore, most of them adopt the operation mode of parallel current sharing of small modules, but the increase in the number and complexity of modules also brings about a decrease in reliability. For this reason, the concept of N+1 redundant backup is proposed, which falls into a technical vicious circle, treating the symptoms instead of the root cause.
Fourth, please note that due to the memory effect of cadmium nickel batteries, it is not suitable for this operation mode. However, due to the high rate discharge capacity of cadmium nickel batteries, in order to pursue low cost, we use cadmium nickel batteries in a large number of such systems, which is wrong. Therefore, nickel-cadmium batteries are not suitable for floating charge operation, so we will not discuss it too much.
3 An ideal solution for battery pack charging
So is there a more perfect solution? After many deliberations, the author proposes the following solution for everyone to discuss. It is not rigorous, but just an idea. The principle is as follows:
As you can see, in this system, the charging and detection of batteries are carried out on a per-cell basis. All charging and battery detection modules contain processing units to handle the charging and detection process by themselves. All modules are coordinated by the monitoring unit through the communication bus according to the battery operating parameters and status. During normal operation, each group of charging modules is connected in series to form an overall power supply to supply power to the load, and each battery is float-charged. When the AC power supply is cut off, the battery will provide power for the load. All charging modules and batteries adopt a hot-swappable and removable structure, and the replacement and maintenance of modules and batteries will not affect the operation of the system. The above three problems will be well solved in this system.
First, in this system, the charging of a single battery is carried out independently. In each charging module, each battery can be scientifically charged and discharged in combination with the operating parameters and operating status of each battery, avoiding the occurrence of problems such as overcharging, undercharging, and over-discharging caused by inconsistent battery parameters, and ensuring the service life of the battery.
Second, in this system, the detection and charging of each battery are in the same module and are organically combined. On the one hand, the battery detection part can easily detect the battery voltage and internal resistance by controlling the charging part. On the other hand, the charging part can charge the battery reasonably according to the parameters measured by the detection unit (including the internal resistance, voltage, temperature and pH value of the single battery). It truly realizes the idea of managing the battery according to the charging curve and its operating status.
Third, we know that it is very easy to realize a small-capacity high-frequency switching power supply now, and it does not require high requirements for devices and processes. It also has high reliability. You can compare it with the commonly used 220V/10A module in scheme 1, whose output power is the highest voltage 280V*10A=2800W. In the system with a battery capacity of more than 800AH, we also need to use a module with an output current of 20A, and its output power is as high as 5600W. The large output capacity naturally puts higher requirements on high-frequency devices and manufacturing processes, and reduces reliability.
In the second scheme, the maximum battery capacity that can be used is 2V/1000AH battery, so the single module capacity is
0.1C (10-hour charging rate) A*2.5V (highest battery voltage) = 250W, where C is the battery capacity.
If a 300AH/12V battery system is used, the single module capacity is
0.1C (10-hour charging rate) A*15V (highest battery voltage) = 450W.
*Note that batteries over 300AH are mostly 2V per cell.
It can be seen that the single module capacity in the second scheme is much smaller than that in the first scheme, so it is very easy to implement, and there are no high requirements for devices and manufacturing processes, and the reliability is improved.
You should note that there is no backup concept in this solution 2. One of the reasons is that the high reliability of the small-capacity charging equipment itself makes it unnecessary to backup. The second reason is that the adoption of the hot-swappable pull-out structure and the existence of the diode D* will only reduce the system voltage (within the allowable range) when replacing the maintenance module and the battery, which will not affect the normal operation of the system. Therefore, this system does not need additional redundant backup.
4 Will the cost increase?
Below we will discuss the issue of system cost that everyone is more concerned about.
In the solution, the number of modules will increase a lot, but due to its small capacity, its requirements for devices and manufacturing processes are very low, and because of mass production, its cost will not increase but may decrease compared with solution 1. In addition, since the module in solution 2 includes a battery detection part, there is no need to install a separate battery detection device, and its cost will be further reduced.
5 Conclusion
In order to solve the problem, I put forward some insights on the battery charging method. There must be many inconsiderate places in the new solution, but technology always needs to continue to improve and improve. I hope that colleagues will give more valuable opinions to make the battery management technology more perfect.
Reference address:Thoughts on battery charging
Based on our many years of experience in DC system development and design and field application, this article attempts to explore the charging method of backup battery packs, hoping to play a role in inspiring others to study a more reasonable battery pack charging method.
2 Defects of current battery pack charging methods
In most current backup power sources (DC systems, UPS, etc.), energy storage is achieved by battery packs. Then the performance of the battery pack, which is the last guarantee for uninterrupted power supply, is crucial. Due to the semiconductor conversion technology and cost reasons, the charging method we have always adopted is to charge the entire series battery group with a single charger as shown in the figure below.
The charger is always connected in parallel with the battery pack in a constant voltage and current limiting mode. In theory, when the battery pack capacity is lost, the charger will automatically replenish it. However, in actual application, we found that this system has the following problems.
First, there are large differences in the characteristics of single batteries. Even batteries from the same batch have large deviations in their characteristics (especially in domestic batteries). Therefore, they are charged and discharged as a whole during operation. They cannot be charged and discharged according to the operating parameters and operating status of the single battery. This will inevitably cause some batteries to be overcharged or undercharged, and may also cause over-discharge. This is one of the important reasons why batteries generally fail to reach the nominal life when they are operated in groups.
Second, it is difficult to detect the voltage and internal resistance of single batteries in this operating mode. Now it is generally adopted to install a battery detection device separately, but the battery detection device cannot cooperate well with the charger. From the above two points, we can see that in this system, managing the battery according to the battery status (voltage, internal resistance, remaining capacity, temperature and other parameters) and charging curve is just empty talk. In addition, installing a battery detection device separately will inevitably increase the cost.
Third, with the advancement of semiconductor technology, high-frequency switching power supplies are replacing traditional thyristor rectifier power supplies with their advantages of small size, light weight, high efficiency and low noise. However, the charging method in Scheme 1 is adopted because the charger needs to provide a higher charging voltage and a larger output capacity, which has high requirements for devices, technology and process. As we all know, it is difficult for IGBT to exceed 20KHz, and if MOS-FET is used in a large current loop, the junction voltage drop is very large, and the heat generation is also very large. Therefore, due to the limitations of devices and processes, it is very difficult for a single high-frequency switching power supply (>20KHz) to have an output capacity exceeding 6KW. Therefore, most of them adopt the operation mode of parallel current sharing of small modules, but the increase in the number and complexity of modules also brings about a decrease in reliability. For this reason, the concept of N+1 redundant backup is proposed, which falls into a technical vicious circle, treating the symptoms instead of the root cause.
Fourth, please note that due to the memory effect of cadmium nickel batteries, it is not suitable for this operation mode. However, due to the high rate discharge capacity of cadmium nickel batteries, in order to pursue low cost, we use cadmium nickel batteries in a large number of such systems, which is wrong. Therefore, nickel-cadmium batteries are not suitable for floating charge operation, so we will not discuss it too much.
3 An ideal solution for battery pack charging
So is there a more perfect solution? After many deliberations, the author proposes the following solution for everyone to discuss. It is not rigorous, but just an idea. The principle is as follows:
As you can see, in this system, the charging and detection of batteries are carried out on a per-cell basis. All charging and battery detection modules contain processing units to handle the charging and detection process by themselves. All modules are coordinated by the monitoring unit through the communication bus according to the battery operating parameters and status. During normal operation, each group of charging modules is connected in series to form an overall power supply to supply power to the load, and each battery is float-charged. When the AC power supply is cut off, the battery will provide power for the load. All charging modules and batteries adopt a hot-swappable and removable structure, and the replacement and maintenance of modules and batteries will not affect the operation of the system. The above three problems will be well solved in this system.
First, in this system, the charging of a single battery is carried out independently. In each charging module, each battery can be scientifically charged and discharged in combination with the operating parameters and operating status of each battery, avoiding the occurrence of problems such as overcharging, undercharging, and over-discharging caused by inconsistent battery parameters, and ensuring the service life of the battery.
Second, in this system, the detection and charging of each battery are in the same module and are organically combined. On the one hand, the battery detection part can easily detect the battery voltage and internal resistance by controlling the charging part. On the other hand, the charging part can charge the battery reasonably according to the parameters measured by the detection unit (including the internal resistance, voltage, temperature and pH value of the single battery). It truly realizes the idea of managing the battery according to the charging curve and its operating status.
Third, we know that it is very easy to realize a small-capacity high-frequency switching power supply now, and it does not require high requirements for devices and processes. It also has high reliability. You can compare it with the commonly used 220V/10A module in scheme 1, whose output power is the highest voltage 280V*10A=2800W. In the system with a battery capacity of more than 800AH, we also need to use a module with an output current of 20A, and its output power is as high as 5600W. The large output capacity naturally puts higher requirements on high-frequency devices and manufacturing processes, and reduces reliability.
In the second scheme, the maximum battery capacity that can be used is 2V/1000AH battery, so the single module capacity is
0.1C (10-hour charging rate) A*2.5V (highest battery voltage) = 250W, where C is the battery capacity.
If a 300AH/12V battery system is used, the single module capacity is
0.1C (10-hour charging rate) A*15V (highest battery voltage) = 450W.
*Note that batteries over 300AH are mostly 2V per cell.
It can be seen that the single module capacity in the second scheme is much smaller than that in the first scheme, so it is very easy to implement, and there are no high requirements for devices and manufacturing processes, and the reliability is improved.
You should note that there is no backup concept in this solution 2. One of the reasons is that the high reliability of the small-capacity charging equipment itself makes it unnecessary to backup. The second reason is that the adoption of the hot-swappable pull-out structure and the existence of the diode D* will only reduce the system voltage (within the allowable range) when replacing the maintenance module and the battery, which will not affect the normal operation of the system. Therefore, this system does not need additional redundant backup.
4 Will the cost increase?
Below we will discuss the issue of system cost that everyone is more concerned about.
In the solution, the number of modules will increase a lot, but due to its small capacity, its requirements for devices and manufacturing processes are very low, and because of mass production, its cost will not increase but may decrease compared with solution 1. In addition, since the module in solution 2 includes a battery detection part, there is no need to install a separate battery detection device, and its cost will be further reduced.
5 Conclusion
In order to solve the problem, I put forward some insights on the battery charging method. There must be many inconsiderate places in the new solution, but technology always needs to continue to improve and improve. I hope that colleagues will give more valuable opinions to make the battery management technology more perfect.
Previous article:Battery Test System Based on Data Acquisition Card
Next article:Application of DC high voltage in detection of small lead-acid battery cell shell
Recommended ReadingLatest update time:2024-11-16 15:30
35%! The localization rate of IGBT continues to increase
Recently, Wang Yanli, a senior industry analyst, revealed in a speech entitled "2023 China IGBT Market Research Report" that by 2022, the global IGBT market will grow to US$7.6 billion. It is expected that the increased growth rate of wind, solar and storage this year is expected to continue to drive double-digit gr
[New Energy]
The 5.25 billion Sunking Asia Pacific Jiashan project started construction with an annual output of 2 million IGBT power devices
On June 9th and 10th, Jiaxing City held the second quarter opening and completion ceremonies. At this event, Saijing Asia Pacific Semiconductor Technology (Zhejiang) Co., Ltd. in Jiashan started construction of a new project with an annual output of 2 million IGBT power devices. Saijing Asia Pacific Semiconductor Te
[Mobile phone portable]
Design of IGBT-based voltage-source inverter auxiliary switching power supply
The auxiliary switching power supply of the voltage-type inverter power supply has a double-tube flyback switching power supply that can efficiently provide multiple DC outputs. The circuit components are all composed of discrete components, have strong anti-interference ability, and work stably and reliably, thus m
[Power Management]
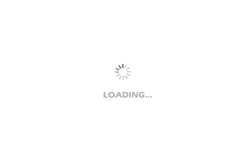
Research on the parallel connection technology of high-power DC/DC power supply with IGBT devices
Based on IGBT devices, this paper designs a high-power DC power supply using DC/DC power supply parallel technology. This power supply can be used as a high-power vertical displacement fast control DC power supply in the EAST Tokamak device . The power supply device was simulated and experimented, and relatively sati
[Power Management]
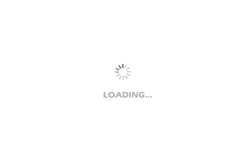
IGBT drive circuit design considerations and circuit diagram
In the gate circuit of IGBT, the main factors to be considered include the positive and negative values of gate voltage U and the size of gate resistance R. They have different degrees of influence on the on-voltage, switching time, switching loss, short-circuit withstand capability and other parameters of IGBT.
[Power Management]
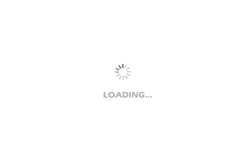
IX4352NE low-side gate driver for SiC MOSFETs and high-power IGBTs
New driver provides tailored turn-on and turn-off timing to minimize switching losses and enhance dV/dt immunity
Chicago, Illinois, May 27, 2024 -
Littelfuse, an industrial technology manufacturing company committed to powering a sustainable, connected and safer world,
is pleased to announce t
[Power Management]
STMicroelectronics' new 1350V IGBT transistor series improves resistance to variations and energy efficiency
STPOWER IH2 for industrial and electromagnetic heating applications
September 11, 2023, China –
STMicroelectronics’ new series of IGBT transistors increases the breakdown voltage to 1350V and extends the maximum operating temperature to 175°C. The higher ratings ensure that the transis
[Power Management]
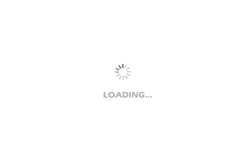
Fairchild Semiconductor Launches IGBT with High Reliability and Excellent Switching Performance
High-power and high-frequency induction heating (IH) home appliances require lower conduction losses and superior switching performance to achieve higher efficiency and system reliability in applications such as IH rice cookers, tabletop induction cookers, and inverter-based microwave ovens. Fairchild Semiconductor's h
[Analog Electronics]
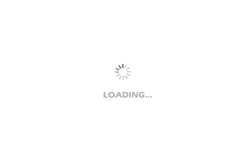
- Popular Resources
- Popular amplifiers
Latest Power Management Articles
- MathWorks and NXP Collaborate to Launch Model-Based Design Toolbox for Battery Management Systems
- STMicroelectronics' advanced galvanically isolated gate driver STGAP3S provides flexible protection for IGBTs and SiC MOSFETs
- New diaphragm-free solid-state lithium battery technology is launched: the distance between the positive and negative electrodes is less than 0.000001 meters
- [“Source” Observe the Autumn Series] Application and testing of the next generation of semiconductor gallium oxide device photodetectors
- 采用自主设计封装,绝缘电阻显著提高!ROHM开发出更高电压xEV系统的SiC肖特基势垒二极管
- Will GaN replace SiC? PI's disruptive 1700V InnoMux2 is here to demonstrate
- From Isolation to the Third and a Half Generation: Understanding Naxinwei's Gate Driver IC in One Article
- The appeal of 48 V technology: importance, benefits and key factors in system-level applications
- Important breakthrough in recycling of used lithium-ion batteries
MoreSelected Circuit Diagrams
MorePopular Articles
- Innolux's intelligent steer-by-wire solution makes cars smarter and safer
- 8051 MCU - Parity Check
- How to efficiently balance the sensitivity of tactile sensing interfaces
- What should I do if the servo motor shakes? What causes the servo motor to shake quickly?
- 【Brushless Motor】Analysis of three-phase BLDC motor and sharing of two popular development boards
- Midea Industrial Technology's subsidiaries Clou Electronics and Hekang New Energy jointly appeared at the Munich Battery Energy Storage Exhibition and Solar Energy Exhibition
- Guoxin Sichen | Application of ferroelectric memory PB85RS2MC in power battery management, with a capacity of 2M
- Analysis of common faults of frequency converter
- In a head-on competition with Qualcomm, what kind of cockpit products has Intel come up with?
- Dalian Rongke's all-vanadium liquid flow battery energy storage equipment industrialization project has entered the sprint stage before production
MoreDaily News
- Allegro MicroSystems Introduces Advanced Magnetic and Inductive Position Sensing Solutions at Electronica 2024
- Car key in the left hand, liveness detection radar in the right hand, UWB is imperative for cars!
- After a decade of rapid development, domestic CIS has entered the market
- Aegis Dagger Battery + Thor EM-i Super Hybrid, Geely New Energy has thrown out two "king bombs"
- A brief discussion on functional safety - fault, error, and failure
- In the smart car 2.0 cycle, these core industry chains are facing major opportunities!
- The United States and Japan are developing new batteries. CATL faces challenges? How should China's new energy battery industry respond?
- Murata launches high-precision 6-axis inertial sensor for automobiles
- Ford patents pre-charge alarm to help save costs and respond to emergencies
- New real-time microcontroller system from Texas Instruments enables smarter processing in automotive and industrial applications
Guess you like