With the advancement of science and technology, high-voltage power supplies are being used in more and more fields. The term "high-voltage power supply" is defined based on its output voltage . I don't know how high a voltage is called a high-voltage power supply. I personally think that anything with an output voltage of more than 1000V can be considered a high-voltage power supply. The fields covered by DC high-voltage power supplies are actually very broad, ranging from DC high-voltage transmission and transformation systems in power systems to household electric mosquito swatters. Here I mainly want to talk about high-voltage power supplies in the field of electronic power supplies. The main applications of high-voltage power supplies in this field include: X-ray systems used in the field of medical security non-destructive testing, some particle accelerator systems, industrial flue gas dust removal, withstand voltage test instruments, electrostatic devices, gas lasers, etc.
The main technical feature of high-voltage power supply is that the output voltage is very high. High output voltage puts forward special requirements in many aspects - requirements for component withstand voltage, structural design requirements, insulation material requirements, etc. At the same time,
the circuit
structure is also different from the usual structure. Usually, for power supplies with an output below 10KV, various traditional topological structures can be directly adopted. However, for power supplies with higher voltages, some modifications must be made to the circuit structure to meet the higher voltage output. Due to the withstand voltage limit of the power devices in the primary part of the transformer, the general drive part is still the traditional
switching power supply
topology, and the modification of the circuit structure is mainly concentrated on the transformer and the subsequent rectifier circuit. The following mainly discusses these two parts.
1. Transformer part
1. Multiple transformers connected in series
In short, once you have mastered the basic principles, you can choose the combination of transformer and rectifier circuit according to actual conditions in specific engineering cases.
The circuit diagram of this method is shown in Figure 1. The characteristic is that the step-up ratio of each transformer is not very high, and the voltage difference between the magnetic core and the secondary winding is not large. The advantages of this method are: it is suitable for high-power output. The insulation of the transformer winding to the magnetic core is easy to handle. The disadvantages are: the power to be transmitted by each transformer is different, the transformer at the lowest voltage end transmits the largest power, and the transformer at the highest voltage end transmits the highest power. Each transformer has different insulation requirements to the ground. The transformer at the highest voltage end has the highest insulation requirements to the ground. Since the transformer has leakage inductance, the farther the transformer is from the drive input, the greater the equivalent leakage inductance in its loop. Then the actual output voltage of the transformer is different, even if the turns ratio is the same.
2. Single transformer, multiple secondary cascades
The circuit
diagram
of this method
is shown in Figure 2. The characteristic is that
the voltage step-up
ratio
of each secondary winding to the primary
is not very high. The advantages are: it is suitable for larger power output. The number of transformers is small, and only one pair of magnetic cores is required. The disadvantages are:
the voltage
difference between the winding at the high voltage end and the magnetic core is large, and the insulation is not easy to handle. If the secondary winding is inconsistent with the magnetic core or the primary structure, the leakage inductance will be inconsistent, resulting in differences between the windings. If the structure is kept consistent, all secondary windings must be designed according to the highest insulation requirements, and the window utilization rate of the transformer will be greatly reduced.
3. Single transformer, insulated core, multiple secondary cascades
The circuit diagram of this method is shown in Figure 3. The characteristic is that the magnetic core is composed of multiple sections, and each section of the magnetic core is insulated by a film with good insulation performance. Each section of the magnetic core has a secondary winding. The advantages are: it is suitable for higher power output. The number of transformers is small, and only one pair of magnetic cores is required. The voltage difference between each section of the secondary winding and the magnetic core is small, and the insulation of the secondary winding to the magnetic core is easy to handle. The disadvantages are: the magnetic core is segmented and the structure is complex. The magnetic core has an air gap. The more segments there are, the larger the equivalent air gap is, and the magnetic core is difficult to fix.
4. Multiple transformers, common primary and secondary cascade
The schematic diagram of the circuit
of this method
is shown in Figure 4. In order to make it more intuitive, a 3D drawing is drawn here. It took a long time to draw this schematic diagram, especially the primary coil. It looks simple, but it took a lot of effort! The characteristic of this structure is that multiple transformers are combined, the primary is
a series
structure, and the secondary is independently rectified and then connected in series. The advantages are: it is suitable for high-power output, and the transformer's
step-up
ratio is not large. The disadvantages are: there is always a high insulation requirement between the primary and secondary cores, and multiple transformers are required.
2. Rectification Circuit
1. Half-wave multiplier circuit
There are two structures of half-wave multiplier circuits. One is the structure of Figure 5A, which is the basic and most common voltage doubler rectifier circuit. The advantages of this circuit are: simple structure, low voltage stress of diodes and capacitors , and low output voltage of transformer. The disadvantages are: poor load capacity, the higher the voltage doubler order, the more voltage drops, and there is a limit voltage doubler order. Beyond this order, the voltage will no longer increase, but will decrease. The other is the structure of Figure 5B. This circuit has a stronger load capacity, but the voltage stress of the capacitor is very high.
2. Full-wave multiplier
circuit
The circuit structure is shown in Figure 6. This is actually an extended structure of the half-wave multiple voltage circuit. Positive and negative high voltages can be obtained at the same time. Of course, if the middle high voltage is grounded and the secondary of the transformer is suspended, it is also possible. The advantage of this is that to get the same high voltage, only half the order of the half-wave multiple voltage is needed. Then
the voltage
drop and ripple are much smaller. The disadvantage is: if the high voltage at one end is grounded and the secondary of the high-voltage transformer is suspended, the insulation requirements of the high-voltage transformer are very high. If the secondary of the high-voltage transformer is grounded, then positive and negative high voltages are obtained, which is not very convenient to use.
3. Tapped double half-wave multiplier circuit
The circuit structure is shown in Figure 7. The characteristic of this structure is that the secondary of the high-voltage transformer has an intermediate tap. The advantages of this structure are: the voltage drop of the doubled voltage is much smaller than that of the half-wave multiple voltage method. The ripple is also much smaller. The disadvantages are: the secondary of the transformer needs a tap, and the number of turns of the secondary of the transformer is doubled for the same high voltage output. There are many components and the cost is high.
4. There are other extended or mixed uses
For example, the tapped double half-wave can be expanded into a tapped full-wave positive and negative multiple voltage circuit to obtain positive and negative high voltage. The structure of Figure 5B and the structure of Figure 5A can also be mixed and used. The conventional rectification method and the voltage doubler rectification method can also be mixed and used. In the positive and negative voltage doubler method, the positive and negative orders can also be inconsistent. In many occasions, we use the two solutions of transformer and rectifier circuit at the same time, such as the transformer secondary segment, each segment is full-wave voltage doubled and then
connected in series
for output, etc.
The voltage doubler circuit that uses
a diode
and
a capacitor
to form a charge pump cannot generally withstand large output power, and the output voltage rise rate is relatively slow. Because this is a charge pump that sacrifices power to obtain a high voltage, the pump capacity is relatively limited.
Previous article:Research on Intelligent Wind Turbine Nacelle Control Based on Fuzzy Control
Next article:Discussion on Several Issues of Intelligent Low Voltage Reactive Power Compensation Device
Recommended ReadingLatest update time:2024-11-16 19:57
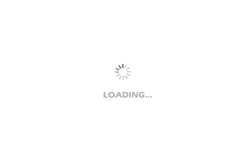
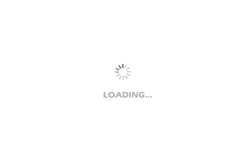
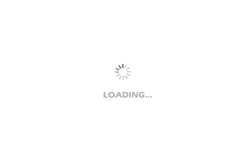
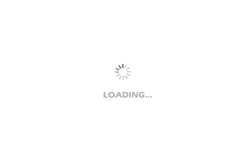
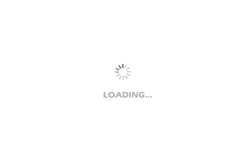
- Popular Resources
- Popular amplifiers
-
西门子S7-12001500 PLC SCL语言编程从入门到精通 (北岛李工)
-
New Energy Vehicle Detection and Diagnosis Experiment (Edited by Mao Caiyun, Zhou Xien, and Long Jiwen)
-
Virtualization Technology Practice Guide - High-efficiency and low-cost solutions for small and medium-sized enterprises (Wang Chunhai)
-
ESP32-S3 source code
- MathWorks and NXP Collaborate to Launch Model-Based Design Toolbox for Battery Management Systems
- STMicroelectronics' advanced galvanically isolated gate driver STGAP3S provides flexible protection for IGBTs and SiC MOSFETs
- New diaphragm-free solid-state lithium battery technology is launched: the distance between the positive and negative electrodes is less than 0.000001 meters
- [“Source” Observe the Autumn Series] Application and testing of the next generation of semiconductor gallium oxide device photodetectors
- 采用自主设计封装,绝缘电阻显著提高!ROHM开发出更高电压xEV系统的SiC肖特基势垒二极管
- Will GaN replace SiC? PI's disruptive 1700V InnoMux2 is here to demonstrate
- From Isolation to the Third and a Half Generation: Understanding Naxinwei's Gate Driver IC in One Article
- The appeal of 48 V technology: importance, benefits and key factors in system-level applications
- Important breakthrough in recycling of used lithium-ion batteries
- Innolux's intelligent steer-by-wire solution makes cars smarter and safer
- 8051 MCU - Parity Check
- How to efficiently balance the sensitivity of tactile sensing interfaces
- What should I do if the servo motor shakes? What causes the servo motor to shake quickly?
- 【Brushless Motor】Analysis of three-phase BLDC motor and sharing of two popular development boards
- Midea Industrial Technology's subsidiaries Clou Electronics and Hekang New Energy jointly appeared at the Munich Battery Energy Storage Exhibition and Solar Energy Exhibition
- Guoxin Sichen | Application of ferroelectric memory PB85RS2MC in power battery management, with a capacity of 2M
- Analysis of common faults of frequency converter
- In a head-on competition with Qualcomm, what kind of cockpit products has Intel come up with?
- Dalian Rongke's all-vanadium liquid flow battery energy storage equipment industrialization project has entered the sprint stage before production
- Allegro MicroSystems Introduces Advanced Magnetic and Inductive Position Sensing Solutions at Electronica 2024
- Car key in the left hand, liveness detection radar in the right hand, UWB is imperative for cars!
- After a decade of rapid development, domestic CIS has entered the market
- Aegis Dagger Battery + Thor EM-i Super Hybrid, Geely New Energy has thrown out two "king bombs"
- A brief discussion on functional safety - fault, error, and failure
- In the smart car 2.0 cycle, these core industry chains are facing major opportunities!
- The United States and Japan are developing new batteries. CATL faces challenges? How should China's new energy battery industry respond?
- Murata launches high-precision 6-axis inertial sensor for automobiles
- Ford patents pre-charge alarm to help save costs and respond to emergencies
- New real-time microcontroller system from Texas Instruments enables smarter processing in automotive and industrial applications
- Thank you + thank you EEWORLD community
- Medical electronics popular data download collection
- GaN Power Devices
- PIN diodes for RF circuits explained in detail
- During the fight against the epidemic, we will teach you how to have instruments in your mind without having any in your hands.
- Migrating between TMS320F28004x and TMS320F28002x
- 5G high-frequency board material selection and multi-layer board design requirements
- EETALK: What changes has the epidemic brought about in technology?
- "Playing with the board" + Yu Zhennan's STM32 development board experiment 4
- MSP430F169 MCU DAC12