At present, network technology is a new technology developed in the field of automotive electronics. It is not only a technology to solve the problems of complex circuits and increased wiring harnesses in automotive electronics, but also its communication and resource sharing capabilities have become a basis for the application of new electronic and computer technologies in vehicles and a support for vehicle information and control systems.
According to their functions, automotive electronic networks can be divided into control-oriented networks (CON) and information transmission-oriented networks (ION). According to the speed of network information transmission, the Society of Automotive Engineers (SAE) of the United States divides networks into three categories: A, B, and C. Category A is a low-speed network with a baud rate below 9600bps, and the baud rate below 125kbps is a medium-speed network category B, and the baud rate above 125kbps is a high-speed network category C. The wheel speed (i.e., the linear speed of the wheel rotating around the wheel axle) sensor (referred to as the wheel speed sensor) signal can be shared by the engine control module, the anti-lock braking system (ABS) control module, and the instrument control module, so that during the braking process of the vehicle, the anti-lock braking control module and the engine control module can be jointly controlled to achieve the best braking performance. Although the ABS system has been widely used in developed countries, the method of processing wheel speed signals is protected by special circuits and chips in the form of hardware and software as part of the electronic controller (ECU) of the ABS system. Most of the domestic processing of wheel speed signals has the problem that the threshold value of wheel speed recognition is too high (when the vehicle speed, i.e., the speed of the vehicle body, is lower than 10km/h, the wheel speed cannot be correctly measured).
The author uses the developed drum wheel speed sensor test bench to conduct experiments. According to the signal characteristics of the wheel speed sensor, the author designs a CAN bus-based automobile wheel speed sensor signal processing circuit, and uses a single-chip microcomputer to collect and quantify the signal. The results show that the designed wheel speed sensor system has the advantages of low wheel speed measurement threshold (vehicle speed up to 3km/h), reliable operation, strong anti-interference ability, etc. At the same time, it can be used as a measurement point of the CAN bus local area network to realize the digitalization and network transmission of sensor signals.
Wheel speed sensor
Since magnetoelectric sensors work stably and reliably and are hardly affected by environmental factors such as temperature and dust, variable reluctance electromagnetic sensors are widely used in wheel speed sensors currently used in automobiles. Variable reluctance wheel speed sensors consist of a stator and a rotor. The stator includes an induction coil and a magnetic head (a magnetic pole composed of a permanent magnet). The rotor can be in the form of a ring gear or a gear. The gear-shaped rotor is shown in Figure 1 (a). The magnetic head is fixed on the magnetic pole bracket, the bracket is fixed on the long shaft, the ring gear is connected to the wheel hub and the brake hub, and the long shaft passes through the wheel and cooperates with the internal bearing, as shown in Figure 1 (b).
The speed of the rotor is proportional to the angular velocity of the wheel. The drum drives the wheel to rotate, and the tooth tops and gaps between the teeth of the sensor rotor alternately approach and leave the magnetic poles, causing the magnetic field in the stator induction coil to change periodically, inducing an AC sine wave signal in the coil. The control test bench makes the wheel run under various working conditions and measures the sensor output signal. The experimental results show that the signal generated by the variable reluctance wheel speed sensor has the following characteristics:
(1) The signal generated by the sensor is a sinusoidal signal close to zero mean;
(2) The amplitude of the sine wave signal is affected by the air gap (the air gap between the magnetic head and the gear ring, generally about 1.0mm is the most ideal) and the wheel speed. The smaller the air gap, the higher the wheel speed, and the greater the amplitude of the sine wave signal;
(3) The frequency of the sine wave signal is affected by the number of teeth on the gear ring and the wheel speed. It is the number of teeth passing through the magnetic head coil per second, which is equal to the number of teeth on the gear ring multiplied by the wheel speed per second. The signal generated by the variable reluctance wheel speed sensor is shown in Figure 2.
The test simulates the front wheel of the BJ212 model, and the drum speed is used to simulate the vehicle speed. When the drum speed is controlled to 3km/h, the amplitude of the sine wave signal generated by the 88-tooth sensor is about 1V, and its frequency is 31Hz; when the drum speed is controlled to 100km/h, the amplitude of the sine wave signal generated by the sensor is about 7V, and its frequency is 1037Hz. Due to the burrs generated by gear processing and other environmental factors, the actual signal is a certain frequency component interference signal superimposed on the above signal, as shown in Figure 2 (b).
Link to this article:
Application of CAN bus in the design of automobile wheel speed sensor
http://ee.ofweek.com/2011-01/ART-8300-2809-28436740.html
Article Tags:
Automobile wheel speed sensor CAN bus anti-interference
(Editor: Kevin)
Recommend to a friend
Printable version
share
-->
Local Collection
At present, network technology is a new technology developed in the field of automotive electronics. It is not only a technology to solve the problems of complex circuits and increased wiring harnesses in automotive electronics, but also its communication and resource sharing capabilities have become a basis for the application of new electronic and computer technologies in vehicles and a support for vehicle information and control systems.
According to their functions, automotive electronic networks can be divided into control-oriented networks (CON) and information transmission-oriented networks (ION). According to the speed of network information transmission, the Society of Automotive Engineers (SAE) of the United States divides networks into three categories: A, B, and C. Category A is a low-speed network with a baud rate below 9600bps, and the baud rate below 125kbps is a medium-speed network category B, and the baud rate above 125kbps is a high-speed network category C. The wheel speed (i.e., the linear speed of the wheel rotating around the wheel axle) sensor (referred to as the wheel speed sensor) signal can be shared by the engine control module, the anti-lock braking system (ABS) control module, and the instrument control module, so that during the braking process of the vehicle, the anti-lock braking control module and the engine control module can be jointly controlled to achieve the best braking performance. Although the ABS system has been widely used in developed countries, the method of processing wheel speed signals is protected by special circuits and chips in the form of hardware and software as part of the electronic controller (ECU) of the ABS system. Most of the domestic processing of wheel speed signals has the problem that the threshold value of wheel speed recognition is too high (when the vehicle speed, i.e., the speed of the vehicle body, is lower than 10km/h, the wheel speed cannot be correctly measured).
The author uses the developed drum wheel speed sensor test bench to conduct experiments. According to the signal characteristics of the wheel speed sensor, the author designs a CAN bus-based automobile wheel speed sensor signal processing circuit, and uses a single-chip microcomputer to collect and quantify the signal. The results show that the designed wheel speed sensor system has the advantages of low wheel speed measurement threshold (vehicle speed up to 3km/h), reliable operation, strong anti-interference ability, etc. At the same time, it can be used as a measurement point of the CAN bus local area network to realize the digitalization and network transmission of sensor signals.
Wheel speed sensor
Since magnetoelectric sensors work stably and reliably and are hardly affected by environmental factors such as temperature and dust, variable reluctance electromagnetic sensors are widely used in wheel speed sensors currently used in automobiles. Variable reluctance wheel speed sensors consist of a stator and a rotor. The stator includes an induction coil and a magnetic head (a magnetic pole composed of a permanent magnet). The rotor can be in the form of a ring gear or a gear. The gear-shaped rotor is shown in Figure 1 (a). The magnetic head is fixed on the magnetic pole bracket, the bracket is fixed on the long shaft, the ring gear is connected to the wheel hub and the brake hub, and the long shaft passes through the wheel and cooperates with the internal bearing, as shown in Figure 1 (b).
The speed of the rotor is proportional to the angular velocity of the wheel. The drum drives the wheel to rotate, and the tooth tops and gaps between the teeth of the sensor rotor alternately approach and leave the magnetic poles, causing the magnetic field in the stator induction coil to change periodically, inducing an AC sine wave signal in the coil. The control test bench makes the wheel run under various working conditions and measures the sensor output signal. The experimental results show that the signal generated by the variable reluctance wheel speed sensor has the following characteristics:
(1) The signal generated by the sensor is a sinusoidal signal close to zero mean;
(2) The amplitude of the sine wave signal is affected by the air gap (the air gap between the magnetic head and the gear ring, generally about 1.0mm is the most ideal) and the wheel speed. The smaller the air gap, the higher the wheel speed, and the greater the amplitude of the sine wave signal;
(3) The frequency of the sine wave signal is affected by the number of teeth on the gear ring and the wheel speed. It is the number of teeth passing through the magnetic head coil per second, which is equal to the number of teeth on the gear ring multiplied by the wheel speed per second. The signal generated by the variable reluctance wheel speed sensor is shown in Figure 2.
The test simulates the front wheel of the BJ212 model, and the drum speed is used to simulate the vehicle speed. When the drum speed is controlled to 3km/h, the amplitude of the sine wave signal generated by the 88-tooth sensor is about 1V, and its frequency is 31Hz; when the drum speed is controlled to 100km/h, the amplitude of the sine wave signal generated by the sensor is about 7V, and its frequency is 1037Hz. Due to the burrs generated by gear processing and other environmental factors, the actual signal is a certain frequency component interference signal superimposed on the above signal, as shown in Figure 2 (b).
Previous article:Cost-effective control of high-brightness LEDs in automotive applications
Next article:Research on electrical engineering and automation technology in buildings
Recommended ReadingLatest update time:2024-11-16 17:52
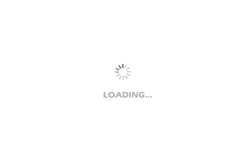
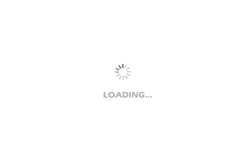
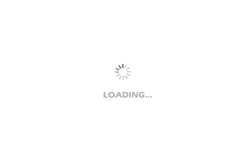
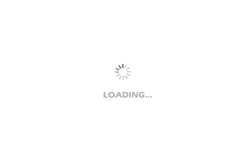
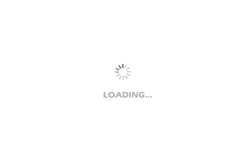
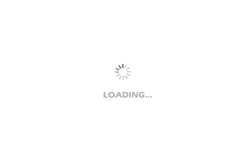
- Popular Resources
- Popular amplifiers
-
Analysis and Implementation of MAC Protocol for Wireless Sensor Networks (by Yang Zhijun, Xie Xianjie, and Ding Hongwei)
-
Introduction to Internet of Things Engineering 2nd Edition (Gongyi Wu)
-
西门子S7-12001500 PLC SCL语言编程从入门到精通 (北岛李工)
-
Modern Motor Control Technology (Wang Chengyuan, Xia Jiakuan, Sun Yibiao)
- MathWorks and NXP Collaborate to Launch Model-Based Design Toolbox for Battery Management Systems
- STMicroelectronics' advanced galvanically isolated gate driver STGAP3S provides flexible protection for IGBTs and SiC MOSFETs
- New diaphragm-free solid-state lithium battery technology is launched: the distance between the positive and negative electrodes is less than 0.000001 meters
- [“Source” Observe the Autumn Series] Application and testing of the next generation of semiconductor gallium oxide device photodetectors
- 采用自主设计封装,绝缘电阻显著提高!ROHM开发出更高电压xEV系统的SiC肖特基势垒二极管
- Will GaN replace SiC? PI's disruptive 1700V InnoMux2 is here to demonstrate
- From Isolation to the Third and a Half Generation: Understanding Naxinwei's Gate Driver IC in One Article
- The appeal of 48 V technology: importance, benefits and key factors in system-level applications
- Important breakthrough in recycling of used lithium-ion batteries
- Innolux's intelligent steer-by-wire solution makes cars smarter and safer
- 8051 MCU - Parity Check
- How to efficiently balance the sensitivity of tactile sensing interfaces
- What should I do if the servo motor shakes? What causes the servo motor to shake quickly?
- 【Brushless Motor】Analysis of three-phase BLDC motor and sharing of two popular development boards
- Midea Industrial Technology's subsidiaries Clou Electronics and Hekang New Energy jointly appeared at the Munich Battery Energy Storage Exhibition and Solar Energy Exhibition
- Guoxin Sichen | Application of ferroelectric memory PB85RS2MC in power battery management, with a capacity of 2M
- Analysis of common faults of frequency converter
- In a head-on competition with Qualcomm, what kind of cockpit products has Intel come up with?
- Dalian Rongke's all-vanadium liquid flow battery energy storage equipment industrialization project has entered the sprint stage before production
- Allegro MicroSystems Introduces Advanced Magnetic and Inductive Position Sensing Solutions at Electronica 2024
- Car key in the left hand, liveness detection radar in the right hand, UWB is imperative for cars!
- After a decade of rapid development, domestic CIS has entered the market
- Aegis Dagger Battery + Thor EM-i Super Hybrid, Geely New Energy has thrown out two "king bombs"
- A brief discussion on functional safety - fault, error, and failure
- In the smart car 2.0 cycle, these core industry chains are facing major opportunities!
- The United States and Japan are developing new batteries. CATL faces challenges? How should China's new energy battery industry respond?
- Murata launches high-precision 6-axis inertial sensor for automobiles
- Ford patents pre-charge alarm to help save costs and respond to emergencies
- New real-time microcontroller system from Texas Instruments enables smarter processing in automotive and industrial applications
- MicroPython Hands-on (24) - Expanding the Control Panel with the Control Panel
- [Flower carving hands-on] Interesting and fun music visualization series of small projects (14) --- water cup and bottle lamp
- Does TMS320C6748 support TFTP instance in stareware?
- Asynchronous Serial Transceiver Design Report.docx
- Design of robotic arm gesture tracking and voice control system
- A new trend in home appliances, PI opens up your new life in home appliances! Download product information and answer questions to win prizes!
- Voltage acquisition circuit
- Problems with IO pin configuration when STM32 is low power
- Lei Jun: Young people should not make suggestions on strategy and business within six months of joining the company, as many of their ideas are unreliable!
- The baby was born--received a special care from the forum