Most lighting designers believe that all LED products are of the same quality. However, there are many manufacturers and suppliers of LEDs, and Asian manufacturers supply low-cost LEDs to the world. Surprisingly, only a small number of these manufacturers can produce high-quality LEDs. For applications that are only used for simple indication, low-quality LEDs are sufficient. However, high-quality LEDs must be used in many areas that require consistency, reliability, solid-state indication or lighting, especially in harsh environments, such as on highways, military/aviation, and industrial applications.
In environments such as New York subway stations, safety requirements are very stringent and LEDs must meet high quality requirements.
What are the factors that distinguish the quality of LEDs? How to tell the difference between two LEDs? In fact, there are many factors to consider when choosing high-quality LEDs, starting from the chip to the assembly. Tier-One LED manufacturing companies are able to produce high-quality wafers with consistent specifications starting from high-quality LED manufacturing materials, which can then produce high-quality chips. Among the conditions that determine all the performance indicators of LEDs, the chemical materials used in the wafer production process are quite important factors.
A 2-inch wafer can be cut into more than 6,000 LED chips , and only a few of them have different performance indicators than the whole. The chips made by a good chip manufacturer have very small differences in color, brightness , and voltage drop. When LED chips are packaged, many of their performance indicators may vary greatly, such as viewing angle. In addition, the impact of the packaging material is also considerable. For example, silicone resin performs better than epoxy resin.
Classification ability
Excellent LED manufacturers can not only manufacture high-quality chips, but also have the ability to classify and package LEDs according to their color, brightness, voltage drop and viewing angle. High-quality LED suppliers will provide customers with products with consistent working characteristics, while low-quality LED suppliers can only provide LEDs similar to "mixed packaging".
For high-end, quality-critical applications, such as airport runway boundary lights, which must meet FAA-level color and brightness specifications, LED packaging consistency is also strictly limited to ensure performance and safety. LEDs with poor packaging grades used in demanding applications will lead to a series of non-consistency problems such as premature failure, which may lead to major accidents. In order to avoid equipment downtime and ensure that the LEDs specified in the design have reliable operating characteristics, it is very important to avoid using "mixed" products in high-end and quality-critical applications.
Product Support Capabilities
In addition to discrete LEDs, the assembly and power supply of LEDs have a very important impact on its performance, brightness, color and other indicators. Since ambient temperature, operating current, circuit structure, voltage spikes and environmental factors can affect the performance indicators of LEDs, proper circuit design and assembly are the key to protecting LEDs and ensuring performance. LED manufacturers also use a variety of technologies and different materials to design circuit structures and assemblies. In most cases, the difference in experience of LED assemblers will cause differences in the overall performance and reliability of LEDs in the same application.
As the demand for LEDs grows rapidly, the number of manufacturers and assembly plants serving the global market has also increased rapidly. Unfortunately, the surge in supporting manufacturers not only uses a large number of low-quality LEDs, but their packaging and LED design engineers are also relatively inexperienced. Therefore, in addition to accurately screening LED suppliers through existing experience, OEMs must also examine their circuit design and assembly technology to ensure that design specifications are met, and whether the design provides sufficient heat dissipation capabilities, because the main factor leading to LED failure and inconsistent performance is overheating.
To ensure that design requirements are met, OEMs must test the LED assembly and circuit structure.
Third-party testing
In order to eliminate the unfairness in testing, many companies have entrusted a third party to test the assembly and circuit structure of LEDs. An LED device may be tested or used for weeks in a harsh environment. During the test, pressure, temperature cycle, voltage fixation/variation, current fixation/variation and other tests are carried out simultaneously to determine whether the LED meets the application requirements. A large number of parameter changes before and after the test must be recorded, and the changes in the brightness, color and voltage drop of the tested LED must be monitored.
Accelerated lifecycle testing is a key test to avoid failures in specific applications. Testing helps to screen out LEDs that are expected to operate for at least 100,000 hours but fail prematurely after only 1,000 hours. This is possible because low-quality LEDs (or high-quality LEDs that are not properly assembled) will lose brightness after 1,000 hours of operation. In fact, a low-quality LED with a higher drive current will be brighter than a high-quality LED at the beginning of operation, however, the excessive current will cause the LED to heat up too quickly, and the end result is dimming or burning.
In addition, there are also examples where assembly technology has a greater impact on LED performance than the chip itself. Design engineers should ask LED suppliers for LED reliability specifications, and should also perform LED assembly tests to ensure that higher brightness is indeed better. Some excellent LED suppliers can guarantee that the reliability of their LED assembly technology can last for three years or more, and can further provide final LED products including high-quality LEDs and appropriate designs for special applications.
Product Support Capabilities
In addition to discrete LEDs, the assembly and power supply of LEDs have a very important impact on its performance, brightness, color and other indicators. Since ambient temperature, operating current, circuit structure, voltage spikes and environmental factors can affect the performance indicators of LEDs, proper circuit design and assembly are the key to protecting LEDs and ensuring performance. LED manufacturers also use a variety of technologies and different materials to design circuit structures and assemblies. In most cases, the difference in experience of LED assemblers will cause differences in the overall performance and reliability of LEDs in the same application.
As the demand for LEDs grows rapidly, the number of manufacturers and assembly plants serving the global market has also increased rapidly. Unfortunately, the surge in supporting manufacturers not only uses a large number of low-quality LEDs, but their packaging and LED design engineers are also relatively inexperienced. Therefore, in addition to accurately screening LED suppliers through existing experience, OEMs must also examine their circuit design and assembly technology to ensure that design specifications are met, and whether the design provides sufficient heat dissipation capabilities, because the main factor leading to LED failure and inconsistent performance is overheating.
To ensure that design requirements are met, OEMs must test the LED assembly and circuit structure.
Third-party testing
In order to eliminate the unfairness in testing, many companies have entrusted a third party to test the assembly and circuit structure of LEDs. An LED device may be tested or used for weeks in a harsh environment. During the test, pressure, temperature cycle, voltage fixation/variation, current fixation/variation and other tests are carried out simultaneously to determine whether the LED meets the application requirements. A large number of parameter changes before and after the test must be recorded, and the changes in the brightness, color and voltage drop of the tested LED must be monitored.
Accelerated lifecycle testing is a key test to avoid failures in specific applications. Testing helps to screen out LEDs that are expected to operate for at least 100,000 hours but fail prematurely after only 1,000 hours. This is possible because low-quality LEDs (or high-quality LEDs that are not properly assembled) will lose brightness after 1,000 hours of operation. In fact, a low-quality LED with a higher drive current will be brighter than a high-quality LED at the beginning of operation, however, the excessive current will cause the LED to heat up too quickly, and the end result is dimming or burning.
In addition, there are also examples where assembly technology has a greater impact on LED performance than the chip itself. Design engineers should ask LED suppliers for LED reliability specifications, and should also perform LED assembly tests to ensure that higher brightness is indeed better. Some excellent LED suppliers can guarantee that the reliability of their LED assembly technology can last for three years or more, and can further provide final LED products including high-quality LEDs and appropriate designs for special applications.
Previous article:Analysis of LED optical and thermal characteristics
Next article:STSTEVAL-ILL015V1RGBLED dimming solution
Recommended ReadingLatest update time:2024-11-16 21:33
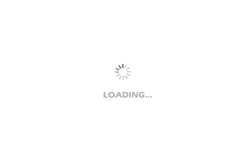
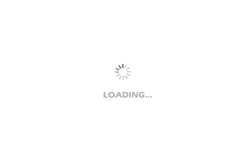
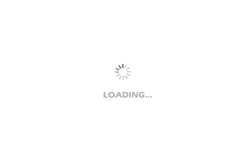
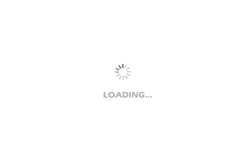
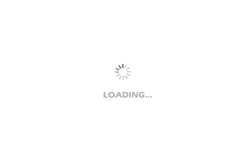
- Popular Resources
- Popular amplifiers
- MathWorks and NXP Collaborate to Launch Model-Based Design Toolbox for Battery Management Systems
- STMicroelectronics' advanced galvanically isolated gate driver STGAP3S provides flexible protection for IGBTs and SiC MOSFETs
- New diaphragm-free solid-state lithium battery technology is launched: the distance between the positive and negative electrodes is less than 0.000001 meters
- [“Source” Observe the Autumn Series] Application and testing of the next generation of semiconductor gallium oxide device photodetectors
- 采用自主设计封装,绝缘电阻显著提高!ROHM开发出更高电压xEV系统的SiC肖特基势垒二极管
- Will GaN replace SiC? PI's disruptive 1700V InnoMux2 is here to demonstrate
- From Isolation to the Third and a Half Generation: Understanding Naxinwei's Gate Driver IC in One Article
- The appeal of 48 V technology: importance, benefits and key factors in system-level applications
- Important breakthrough in recycling of used lithium-ion batteries
- Innolux's intelligent steer-by-wire solution makes cars smarter and safer
- 8051 MCU - Parity Check
- How to efficiently balance the sensitivity of tactile sensing interfaces
- What should I do if the servo motor shakes? What causes the servo motor to shake quickly?
- 【Brushless Motor】Analysis of three-phase BLDC motor and sharing of two popular development boards
- Midea Industrial Technology's subsidiaries Clou Electronics and Hekang New Energy jointly appeared at the Munich Battery Energy Storage Exhibition and Solar Energy Exhibition
- Guoxin Sichen | Application of ferroelectric memory PB85RS2MC in power battery management, with a capacity of 2M
- Analysis of common faults of frequency converter
- In a head-on competition with Qualcomm, what kind of cockpit products has Intel come up with?
- Dalian Rongke's all-vanadium liquid flow battery energy storage equipment industrialization project has entered the sprint stage before production
- Allegro MicroSystems Introduces Advanced Magnetic and Inductive Position Sensing Solutions at Electronica 2024
- Car key in the left hand, liveness detection radar in the right hand, UWB is imperative for cars!
- After a decade of rapid development, domestic CIS has entered the market
- Aegis Dagger Battery + Thor EM-i Super Hybrid, Geely New Energy has thrown out two "king bombs"
- A brief discussion on functional safety - fault, error, and failure
- In the smart car 2.0 cycle, these core industry chains are facing major opportunities!
- The United States and Japan are developing new batteries. CATL faces challenges? How should China's new energy battery industry respond?
- Murata launches high-precision 6-axis inertial sensor for automobiles
- Ford patents pre-charge alarm to help save costs and respond to emergencies
- New real-time microcontroller system from Texas Instruments enables smarter processing in automotive and industrial applications
- Structure of optical devices and chips
- GitHub stores open source code repositories in Arctic caves
- Has anyone done OTA online upgrade for RL78?
- Millimeter wave radar IWR1443
- mpy starts supporting USB for STM32L432
- Voltage follower composed of op amp
- [Hua Diao Experience] 08 Series of tests on the hardware control pinpong library of Xingkong board (Part 1)
- What sampling rate is required for an oscilloscope to measure various types of signals?
- Application of wireless Bluetooth transparent transmission modules in five common industries
- Do I need to set the pull-up or pull-down resistor of the port for output?