Due to
the advancement of
LED
technology, LED applications are becoming more and more diversified, from early
power
indicators to
LED lighting
products with advantages such as power saving, long life and high visibility. However, since only 15 to 20% of the input power of high-
power
LEDs is converted into light, and the remaining 80 to 85% is converted into heat, if this heat is not discharged to the outside world in time, the temperature of the LED grain interface will be too high, affecting the luminous
efficiency
and luminous life.
Heat dissipation is the key to LED development
.
With the continuous evolution of LED materials and packaging technology,
the brightness
of LED products
has been continuously improved, and the application of LEDs has become more and more extensive, providing a stable and growing market for the LED industry. Using LED as
the backlight source of
displays
has become a hot topic recently. It has gradually developed from the backlight source of small-sized displays to the backlight source of medium and large-sized
LCD
TVs, and it is likely to gradually replace the CCFL backlight source. The main reason is that LED has more advantages than traditional cold cathode tubes (CCFL) in color, brightness, life, power consumption and environmental protection, thus attracting industry players to actively invest.
In the early days, the power of single-chip LEDs was not high, the heat generation was limited, and the heat problem was not big, so its packaging method was relatively simple. However, in recent years, with the continuous breakthroughs in LED material technology, LED packaging technology has also changed, from the early single-chip cannonball-shaped packaging to a flat, large-area multi-chip packaging module; its operating current has evolved from the early low-power LED of about 20mA to the current high-power LED of about 1/3 to 1A, and the input power of a single LED is as high as 1W or even 3W or 5W.
The packaging method has evolved
Since the heat problem derived from the high-brightness and high-power LED system will be the key to affecting the product function, in order to quickly discharge the heat generated by the LED component to the surrounding environment, it is necessary to start with the thermal management of the packaging level (L1&L2); the current practice is to connect the LED die to a heat spreader with solder or thermal paste, and reduce the thermal impedance of the packaging module through the heat spreader. This is also the most common
LED packaging
module on the market. The main sources are internationally renowned LED manufacturers such as Lumileds, OSRAM,
Cree
and Ni
ic
ha.
In actual applications,
these
LED modules
can be assembled in a row to form a linear light source, or in an array or circular arrangement, and then joined to a heat dissipation substrate as a surface light source. However, for many terminal application products, such as mini
projectors
, automotive and lighting sources, the required
lumen
volume in a specific area needs to exceed thousands or tens of thousands of lumens.
Single-
crystal packaging modules alone are obviously not enough to cope with it. Moving towards multi-chip LED packaging and direct chip bonding to the substrate is the future development trend.
In the actual application of LED products, whether it is used for display backlight, indicator light or general lighting, multiple LEDs are usually assembled on a circuit substrate as needed. On the one hand, the circuit substrate plays the role of carrying the LED module structure. On the other hand, as the output power of LEDs becomes higher and higher, the substrate must also play the role of heat dissipation to
transfer the heat generated by
the LED chip
. Therefore, in the selection of materials, both structural strength and heat dissipation requirements must be taken into account.
Material costs need to be considered
Traditional LEDs have low power and are not a serious heat dissipation problem. It is sufficient to use a copper foil printed circuit board used in general electronics. However, as high-power LEDs become more and more popular, this board is no longer sufficient to meet the heat dissipation needs. Therefore, the printed circuit board needs to be attached to a metal plate, the so-called MetalCore
PCB
, to improve its heat transfer path.
Another method is to directly make an insulating layer or dielectric layer on the surface of the aluminum substrate, and then make a circuit layer on the surface of the dielectric layer. In this way, the LED module can directly connect the wires to the circuit layer. At the same time, in order to avoid increasing thermal impedance due to the poor thermal conductivity of the dielectric layer, perforation is sometimes used to allow the heat spreader at the bottom of the LED module to directly contact the metal substrate, which is the so-called direct chip bonding.
In addition to metal substrates, in order to respond to the development of high-power LED packaging and chip direct bonding substrates, the selection of substrate materials must not only consider heat dissipation, but also consider the matching of the thermal expansion coefficient with the chip to avoid thermal deformation and reliability problems caused by thermal stress. Therefore, ceramic substrates and metal composite substrates are also being developed at home and abroad. These newly developed substrate materials not only have good heat dissipation, but also have a thermal expansion coefficient (between 4~8ppm/K) that matches the LED chip. The only drawback is that they are more expensive than general metal substrates.
Focus on fanless heat dissipation
In fact, the heat dissipation components of LEDs are similar to CPU heat dissipation. They are mainly air-cooled modules composed of heat sinks, heat pipes, fans and thermal interface materials. Of course, water cooling is also one of the heat countermeasures.
For the most popular large-size LEDTV backlight
modules
, the input power of 40-inch and 46-inch
LED backlight sources
is 470W and 550W respectively. Assuming that 80% of them are converted into heat, the required heat dissipation is about 360W and 440W. How to take away this heat? There are water cooling methods, but there are concerns about high unit price and reliability; there are also heat pipes with heat sinks and fans for cooling (such as SONY46”LEDTV), but there are problems such as fan power consumption and noise. Therefore, how to design fanless heat dissipation is an important key to determine who will win in the future.
Previous article:A brief discussion on the new LED cooling technology IVC breaks through the limitations of traditional LED cooling technology
Next article:The battle of survival between RGB and white LED
Recommended ReadingLatest update time:2024-11-16 16:22
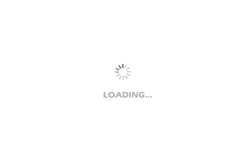
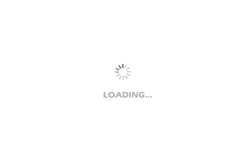
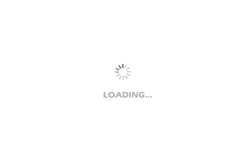
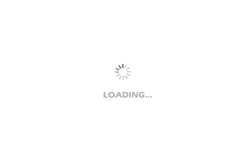
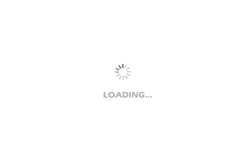
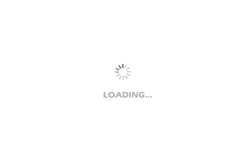
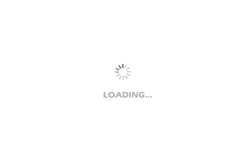
- Popular Resources
- Popular amplifiers
- MathWorks and NXP Collaborate to Launch Model-Based Design Toolbox for Battery Management Systems
- STMicroelectronics' advanced galvanically isolated gate driver STGAP3S provides flexible protection for IGBTs and SiC MOSFETs
- New diaphragm-free solid-state lithium battery technology is launched: the distance between the positive and negative electrodes is less than 0.000001 meters
- [“Source” Observe the Autumn Series] Application and testing of the next generation of semiconductor gallium oxide device photodetectors
- 采用自主设计封装,绝缘电阻显著提高!ROHM开发出更高电压xEV系统的SiC肖特基势垒二极管
- Will GaN replace SiC? PI's disruptive 1700V InnoMux2 is here to demonstrate
- From Isolation to the Third and a Half Generation: Understanding Naxinwei's Gate Driver IC in One Article
- The appeal of 48 V technology: importance, benefits and key factors in system-level applications
- Important breakthrough in recycling of used lithium-ion batteries
- Innolux's intelligent steer-by-wire solution makes cars smarter and safer
- 8051 MCU - Parity Check
- How to efficiently balance the sensitivity of tactile sensing interfaces
- What should I do if the servo motor shakes? What causes the servo motor to shake quickly?
- 【Brushless Motor】Analysis of three-phase BLDC motor and sharing of two popular development boards
- Midea Industrial Technology's subsidiaries Clou Electronics and Hekang New Energy jointly appeared at the Munich Battery Energy Storage Exhibition and Solar Energy Exhibition
- Guoxin Sichen | Application of ferroelectric memory PB85RS2MC in power battery management, with a capacity of 2M
- Analysis of common faults of frequency converter
- In a head-on competition with Qualcomm, what kind of cockpit products has Intel come up with?
- Dalian Rongke's all-vanadium liquid flow battery energy storage equipment industrialization project has entered the sprint stage before production
- Allegro MicroSystems Introduces Advanced Magnetic and Inductive Position Sensing Solutions at Electronica 2024
- Car key in the left hand, liveness detection radar in the right hand, UWB is imperative for cars!
- After a decade of rapid development, domestic CIS has entered the market
- Aegis Dagger Battery + Thor EM-i Super Hybrid, Geely New Energy has thrown out two "king bombs"
- A brief discussion on functional safety - fault, error, and failure
- In the smart car 2.0 cycle, these core industry chains are facing major opportunities!
- The United States and Japan are developing new batteries. CATL faces challenges? How should China's new energy battery industry respond?
- Murata launches high-precision 6-axis inertial sensor for automobiles
- Ford patents pre-charge alarm to help save costs and respond to emergencies
- New real-time microcontroller system from Texas Instruments enables smarter processing in automotive and industrial applications
- My question is, does IoT need a server? Is Alibaba Cloud better or Tencent Cloud? Can anyone recommend one?
- [RVB2601 Creative Application Development] Network Weather Clock
- [HPM-DIY] Pseudo 3D game doom ported to HPM6750
- Invalid declaration when using IP4_ADDR(ipaddr, a,b,c,d)
- Pingtouge RVB2601 Open Source Application Innovation Collection Activity Award Ceremony, thank you for your companionship with the growth of the NationalChip ecosystem
- Computer USB 3.0 interface hardware circuit design
- DIY-Handmade Constant Temperature Heating Table
- How to write driver for HT16K33_16*8 dot matrix
- I'm learning SOC FPGA recently. I don't know if any great god has a bare metal tutorial. I'm a newbie, the more detailed the better.
- Understanding of Bluetooth protocol based on TI cc2540 module