The most common problems with general electronic products are: RE--radiation, CE--conduction, ESD--static electricity.
Communication electronic products not only include the above three items: RE, CE, ESD, but also Surge--surge (lightning strike, thunder)
The most common problems with medical devices are: ESD--static electricity, EFT--transient pulse interference prevention, CS--conduction interference prevention, and RS--radiation interference prevention.
For the dry northern regions, the product's ESD (static electricity) requirements must be very high.
For areas like Sichuan and some southwestern areas prone to lightning, EFT lightning protection requirements are very high.
How to improve the anti-interference ability and electromagnetic compatibility of electronic products:
1. The following systems should pay special attention to anti-electromagnetic interference:
(1) Systems with very high microcontroller clock frequencies and very fast bus cycles.
(2) The system contains high-power, high-current drive circuits, such as spark-generating relays, high-current switches, etc.
(3) Systems containing weak analog signal circuits and high-precision A/D conversion circuits.
2. To increase the system's ability to resist electromagnetic interference, take the following measures:
(1) Choose a low-frequency microcontroller:
Selecting a microcontroller with a low external clock frequency can effectively reduce noise and improve the system's anti-interference ability. For square waves and sine waves of the same frequency, the high-frequency components in the square wave are much more than those in the sine wave. Although the amplitude of the high-frequency component of the square wave is smaller than that of the fundamental wave, the higher the frequency, the easier it is to emit and become a noise source. The most influential high-frequency noise generated by the microcontroller is about 3 times the clock frequency.
(2) Reduce distortion in signal transmission
Microcontrollers are mainly manufactured using high-speed CMOS technology. The static input current of the signal input end is about 1mA, the input capacitance is about 10PF, and the input impedance is quite high. The output end of the high-speed CMOS circuit has a considerable load capacity, that is, a considerable output value. If the output end of a gate is connected to the input end with a relatively high input impedance through a very long line, the reflection problem will be very serious, which will cause signal distortion and increase system noise. When Tpd>Tr, it becomes a transmission line problem, and signal reflection, impedance matching and other issues must be considered.
The delay time of the signal on the printed circuit board is related to the characteristic impedance of the lead, that is, the dielectric constant of the printed circuit board material. It can be roughly assumed that the transmission speed of the signal on the printed circuit board lead is about 1/3 to 1/2 of the speed of light. The Tr (standard delay time) of the commonly used logic telephone elements in the system composed of microcontrollers is between 3 and 18ns.
On a printed circuit board, the signal passes through a 7W resistor and a 25cm long lead, and the line delay time is roughly between 4 and 20ns. In other words, the shorter the signal lead on the printed circuit, the better, and the longest should not exceed 25cm. In addition, the number of vias should be as small as possible, preferably no more than 2.
When the rise time of the signal is faster than the signal delay time, it must be processed according to fast electronics. At this time, the impedance matching of the transmission line must be considered. For signal transmission between integrated blocks on a printed circuit board, the situation of Td>Trd must be avoided. The larger the printed circuit board, the slower the system speed.
A rule for printed circuit board design can be summarized as follows:
When a signal is transmitted on a printed circuit board, its delay time should not be greater than the nominal delay time of the device used.
(3) Reduce cross-interference between signal lines:
At point A, a step signal with a rise time of Tr is transmitted to end B through lead AB. The delay time of the signal on line AB is Td. At point D, due to the forward transmission of the signal at point A, the reflection of the signal after reaching point B and the delay of line AB, a page pulse signal with a width of Tr will be induced after Td time. At point C, due to the transmission and reflection of the signal on AB, a positive pulse signal with a width twice the delay time of the signal on line AB, that is, 2Td, will be induced. This is the cross-interference between signals. The strength of the interference signal is related to the di/at of the signal at point C and the distance between the lines. When the two signal lines are not very long, what is actually seen on AB is the superposition of two pulses.
The microcontroller manufactured by CMOS technology has high input impedance, high noise, and high noise tolerance. The digital circuit can be superimposed with 100~200mv noise without affecting its operation. If the AB line in the figure is an analog signal, this interference becomes intolerable. If the printed circuit board is a four-layer board, one of which is a large-area ground, or a double-layer board, the back of the signal line is a large-area ground, this cross-interference between signals will become smaller. The reason is that the large-area ground reduces the characteristic impedance of the signal line, and the reflection of the signal at the D end is greatly reduced. The characteristic impedance is inversely proportional to the square of the dielectric constant of the medium between the signal line and the ground, and is proportional to the natural logarithm of the thickness of the medium. If the AB line is an analog signal, to avoid the interference of the digital circuit signal line CD on AB, there must be a large area of ground under the AB line, and the distance from the AB line to the CD line must be greater than 2~3 times the distance between the AB line and the ground. A local shielding ground can be used, and ground wires are laid on both sides of the lead with a lead.
(4) Reducing noise from the power supply
While the power supply provides energy to the system, it also adds its noise to the power supply it supplies. The reset line, interrupt line, and other control lines of the microcontroller in the circuit are most susceptible to interference from external noise. Strong interference on the power grid enters the circuit through the power supply. Even in battery-powered systems, the battery itself has high-frequency noise. The analog signals in the analog circuit are even more vulnerable to interference from the power supply.
(5) Pay attention to the high-frequency characteristics of printed circuit boards and components
In the case of high frequencies, the distributed inductance and capacitance of the leads, vias, resistors, capacitors, and connectors on the printed circuit board cannot be ignored. The distributed inductance of capacitors cannot be ignored, and the distributed capacitance of inductors cannot be ignored. The resistors reflect high-frequency signals, and the distributed capacitance of the leads will play a role. When the length is greater than 1/20 of the corresponding wavelength of the noise frequency, an antenna effect is generated, and the noise is emitted outward through the leads.
The vias in the printed circuit board introduce approximately 0.6 pf of capacitance.
The packaging material of an integrated circuit itself introduces 2~6pf capacitance.
A connector on a circuit board has a distributed inductance of 520nH. A dual in-line 24-pin integrated circuit socket introduces a distributed inductance of 4~18nH.
These small distributed parameters can be ignored in this line of microcontroller systems at lower frequencies; however, special attention must be paid to high-speed systems.
(6) Component layout should be divided into reasonable areas
The arrangement of components on the printed circuit board should fully consider the anti-electromagnetic interference problem. One of the principles is that the leads between components should be as short as possible. In terms of layout, the analog signal part, high-speed digital circuit part, and noise source part (such as relays, high-current switches, etc.) should be reasonably separated to minimize the signal coupling between them.
G. Handle the grounding wire properly
On a printed circuit board, the power line and the ground line are the most important. The most important means to overcome electromagnetic interference is grounding.
For double-sided boards, the grounding arrangement is particularly particular. By adopting the single-point grounding method, the power supply and the ground are connected to the printed circuit board from both ends of the power supply, one contact for the power supply and one contact for the ground. There should be multiple return ground wires on the printed circuit board, which will converge to the point where the power supply is returned, which is the so-called single-point grounding. The so-called separation of analog ground, digital ground, and high-power device ground means that the wiring is separated and finally converges to this grounding point. When connected to signals outside the printed circuit board, shielded cables are usually used. For high-frequency and digital signals, both ends of the shielded cable are grounded. For shielded cables used for low-frequency analog signals, it is better to ground one end.
Circuits that are very sensitive to noise and interference or circuits with particularly severe high-frequency noise should be shielded with metal covers.
(7) Make good use of decoupling capacitors.
Good high-frequency decoupling capacitors can remove high-frequency components up to 1GHZ. Ceramic chip capacitors or multilayer ceramic capacitors have better high-frequency characteristics. When designing a printed circuit board, a decoupling capacitor should be added between the power supply and ground of each integrated circuit. The decoupling capacitor has two functions: on the one hand, it is the energy storage capacitor of the integrated circuit, providing and absorbing the charging and discharging energy of the integrated circuit when it opens and closes; on the other hand, it bypasses the high-frequency noise of the device. The typical decoupling capacitor in the digital circuit is a 0.1uf decoupling capacitor with a distributed inductance of 5nH. Its parallel resonance frequency is about 7MHz, which means that it has a good decoupling effect on noise below 10MHz and has almost no effect on noise above 40MHz.
1uf, 10uf capacitors, parallel resonance frequency above 20MHz, the effect of removing high frequency noise is better. It is often beneficial to put a 1uf or 10uf high frequency capacitor where the power enters the printed circuit board, even battery-powered systems need this capacitor.
For every 10 or so integrated circuits, a charging and discharging capacitor, or storage capacitor, should be added. The capacitance can be 10uf. It is best not to use electrolytic capacitors, which are two layers of thin film rolled up. This rolled-up structure behaves as an inductor at high frequencies. It is best to use a bile capacitor or a polycarbonate capacitor.
The selection of decoupling capacitor value is not strict, and can be calculated as C=1/f; that is, 0.1uf is used for 10MHz, and for a system composed of a microcontroller, the value can be between 0.1~0.01uf.
3. Some experience in reducing noise and electromagnetic interference.
(1) If a low-speed chip can be used, don’t use a high-speed chip. High-speed chips are used in critical places.
(2) A resistor can be connected in series to reduce the rate at which the control circuit rises and falls.
(3) Try to provide some form of damping for relays etc.
(4) Use the lowest frequency clock that meets the system requirements.
(5) The clock generator should be as close as possible to the device that uses the clock. The shell of the quartz crystal oscillator should be grounded.
(6) Use the ground line to circle the clock area and keep the clock line as short as possible.
(7) The I/O drive circuit should be as close to the edge of the printed circuit board as possible, so that it can leave the printed circuit board as soon as possible. The signals entering the printed circuit board should be filtered, and the signals coming from the high noise area should also be filtered. At the same time, the terminal resistor should be used in series to reduce signal reflection.
(8) The unused end of MCD should be connected to a high level, or to the ground, or defined as an output end. The ends of the integrated circuit that should be connected to the power ground should be connected and not left floating.
(9) Do not leave the input of unused gate circuits floating. The positive input of unused op amps should be grounded, and the negative input should be connected to the output. (10) Try to use 45-degree zigzag lines instead of 90-degree zigzag lines for printed circuit boards to reduce the emission and coupling of high-frequency signals.
(11) The printed circuit board should be divided into zones according to frequency and current switching characteristics, and the distance between noise components and non-noise components should be as far as possible.
(12) Single-sided and double-sided boards should use a single point for power supply and single point for grounding. The power line and ground line should be as thick as possible. If the economy can afford it, use multi-layer boards to reduce the capacitance and inductance of the power supply and ground.
(13) Clock, bus, and chip select signals should be kept away from I/O lines and connectors.
(14) The analog voltage input line and reference voltage terminal should be kept as far away from the digital circuit signal line as possible, especially the clock.
(15) For A/D devices, it is better to unify the digital and analog parts rather than cross them.
(16) The clock line is perpendicular to the I/O line, which has less interference than the parallel I/O line. The clock component pins should be kept away from the I/O cable.
(17) The component pins and decoupling capacitor pins should be as short as possible.
(18) Key lines should be as thick as possible and have protective grounds on both sides. High-speed lines should be short and straight.
(19) Do not run noise-sensitive lines parallel to high-current, high-speed switching lines.
(20) Do not run traces under quartz crystals or noise-sensitive devices.
(21) Do not form current loops around weak signal circuits and low-frequency circuits.
(22) No signal should form a loop. If it is unavoidable, make the loop area as small as possible.
(23) Each integrated circuit has a decoupling capacitor. A small high-frequency bypass capacitor should be added next to each electrolytic capacitor.
(24) Use large-capacity tantalum capacitors or polycooled capacitors instead of electrolytic capacitors as circuit charging and discharging energy storage capacitors. When using tubular capacitors, the casing must be grounded.
Previous article:Research on the relationship between balance and protection of lithium-ion battery pack
Next article:Maintenance and monitoring of valve-regulated lead-acid batteries VRLA
Recommended ReadingLatest update time:2024-11-16 17:52
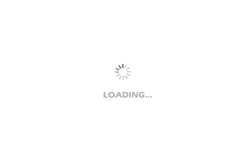
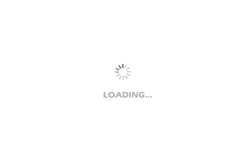
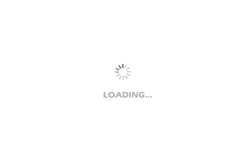
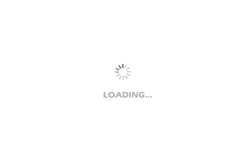
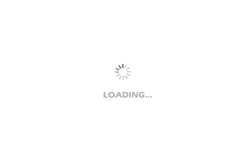
- Popular Resources
- Popular amplifiers
- MathWorks and NXP Collaborate to Launch Model-Based Design Toolbox for Battery Management Systems
- STMicroelectronics' advanced galvanically isolated gate driver STGAP3S provides flexible protection for IGBTs and SiC MOSFETs
- New diaphragm-free solid-state lithium battery technology is launched: the distance between the positive and negative electrodes is less than 0.000001 meters
- [“Source” Observe the Autumn Series] Application and testing of the next generation of semiconductor gallium oxide device photodetectors
- 采用自主设计封装,绝缘电阻显著提高!ROHM开发出更高电压xEV系统的SiC肖特基势垒二极管
- Will GaN replace SiC? PI's disruptive 1700V InnoMux2 is here to demonstrate
- From Isolation to the Third and a Half Generation: Understanding Naxinwei's Gate Driver IC in One Article
- The appeal of 48 V technology: importance, benefits and key factors in system-level applications
- Important breakthrough in recycling of used lithium-ion batteries
- Innolux's intelligent steer-by-wire solution makes cars smarter and safer
- 8051 MCU - Parity Check
- How to efficiently balance the sensitivity of tactile sensing interfaces
- What should I do if the servo motor shakes? What causes the servo motor to shake quickly?
- 【Brushless Motor】Analysis of three-phase BLDC motor and sharing of two popular development boards
- Midea Industrial Technology's subsidiaries Clou Electronics and Hekang New Energy jointly appeared at the Munich Battery Energy Storage Exhibition and Solar Energy Exhibition
- Guoxin Sichen | Application of ferroelectric memory PB85RS2MC in power battery management, with a capacity of 2M
- Analysis of common faults of frequency converter
- In a head-on competition with Qualcomm, what kind of cockpit products has Intel come up with?
- Dalian Rongke's all-vanadium liquid flow battery energy storage equipment industrialization project has entered the sprint stage before production
- Allegro MicroSystems Introduces Advanced Magnetic and Inductive Position Sensing Solutions at Electronica 2024
- Car key in the left hand, liveness detection radar in the right hand, UWB is imperative for cars!
- After a decade of rapid development, domestic CIS has entered the market
- Aegis Dagger Battery + Thor EM-i Super Hybrid, Geely New Energy has thrown out two "king bombs"
- A brief discussion on functional safety - fault, error, and failure
- In the smart car 2.0 cycle, these core industry chains are facing major opportunities!
- The United States and Japan are developing new batteries. CATL faces challenges? How should China's new energy battery industry respond?
- Murata launches high-precision 6-axis inertial sensor for automobiles
- Ford patents pre-charge alarm to help save costs and respond to emergencies
- New real-time microcontroller system from Texas Instruments enables smarter processing in automotive and industrial applications
- The impact of water depth on power supply and communications.
- MSP430G2755 Main Memory Bootloader UART Porting Guide
- A simple temperature control circuit to help you understand the circuit diagram
- 【CH579M-R1】3. ADC internal temperature measurement, external channel and touch button test
- How to migrate from GCC Linker to SEGGER Linker in Embedded Studio?
- Based on PSOC6 development board simulation I2C solution X-NUCLEO-IKS01A3 LPS22HH
- 【CH579M-R1】+OTA first experience
- Xunwei i.MX6ULL Terminator to view the real-time value of variables
- Simple 6LoWPAN Mesh Data Collector
- I created a project with stm32cubemx and then used the module generated by keil RTE, but the code generated by RTE is repeated. How can I disable the duplication?