1) LED single chip packaging
LED has achieved rapid development in the past 30 years. The first batch of products appeared in 1968. The luminous flux of LED with a working current of 20mA was only a few thousandths of a lumen, and the corresponding luminous efficiency was 0.1 lm/W, and there was only one light color, red light at 650 nm. In the early 1970s, the technology progressed rapidly, the luminous efficiency reached 1 lm/W, and the colors were expanded to red, green and yellow. With the invention of new materials and the improvement of light efficiency, the power and luminous flux of a single LED light source are also increasing rapidly. Originally, the driving current of a general LED was only 20 mA. In the 1990s, the driving current of an LED light source code-named "Piranha" increased to 50-70mA, and the driving current of a new high-power LED reached 300-500 mA. In particular, the successful development of white light LEDs in 1998 has made a substantial step forward in the application of LEDs from simple identification display functions to lighting functions. Figures 2-1 to 2-4 describe the development of LEDs.
Figure 2-1 Ordinary LEDs are mainly used for indicator lights
Figure 2-2 High-brightness LEDs are mainly used for lighting
Figure 2-3 Piranha LED
Figure 2-4 High-power LED
A Status of Power LED Packaging Technology
Power LEDs are divided into two types: power LEDs and watt (W) class power LEDs. The input power of power LEDs is less than 1W (except for LEDs with tens of milliwatts); the input power of W class power LEDs is equal to or greater than 1W.
HP first launched the "piranha" package structure LED in the early 1990s, and launched the improved "Snap LED" in 1994, with two working currents of 70mA and 150mA, and the input power can reach 0.3W. Then OSRAM launched the "PowerTOP LED", and then some companies launched a variety of power LED packaging structures. The power LEDs of these structures have several times higher input power than the original bracket packaged LEDs, and the thermal resistance is reduced to a fraction of the past.
W class power LEDs are the core of future lighting, and major companies around the world have invested a lot of effort in researching and developing their packaging technology. The first single-chip W-class power LED was LUXEON LED launched by Lumileds in 1998. The packaging structure is characterized by the use of thermal and electrical separation, the flip chip is directly soldered to the heat sink with a silicon carrier, and new structures and new materials such as reflective cups, optical lenses and flexible transparent adhesives are used. Now single-chip 1W, 3W and 5W high-power LEDs are available. Lumileds has a number of patented technologies in power-type white light diode packaging. OSRAM launched the single-chip "Golden Dragon" series LED in 2003. Its characteristics are that the heat sink is in direct contact with the metal circuit board, with good heat dissipation performance, and the input power can reach 1W. Nichia's 1W LED has an operating current of 350 mA, and the luminous flux of white light, blue light, blue-green light and green light are 23, 7, 28 and 20 lumens respectively, and its life is expected to be 50,000 hours.
B Overview of power LED packaging technology
If semiconductor LEDs are to be used as lighting sources, the luminous flux of conventional products is far from that of general-purpose light sources such as incandescent lamps and fluorescent lamps. Therefore, the key to the development of LEDs in the field of lighting is to increase their luminous efficiency and luminous flux to the level of existing lighting sources. Due to the continuous increase in the input power of LED chips, the power LED packaging technology should mainly meet the following two requirements: ① The packaging structure must have a high light extraction efficiency; ② The thermal resistance must be as low as possible, so as to ensure the photoelectric performance and reliability of the power LED.
The epitaxial material used in power LEDs adopts MOCVD epitaxial growth technology and multi-quantum well structure. Although its internal quantum efficiency needs to be further improved, the biggest obstacle to obtaining high luminous flux is still the low light extraction efficiency of the chip. The existing design of power LEDs uses a new flip-chip structure to improve the light extraction efficiency of the chip, improve the thermal characteristics of the chip, and increase the photoelectric conversion efficiency of the device by increasing the chip area and increasing the working current, thereby obtaining a higher luminous flux. In addition to the chip, the device packaging technology is also very important.
Key technologies for power LED packaging:
a. Heat dissipation technology
The traditional indicator LED packaging structure is generally to install the chip in a small-sized reflective cup or on a wafer stage with conductive or non-conductive glue, and then use gold wire to complete the internal and external connections of the device and then encapsulate it with epoxy resin. Its thermal resistance is as high as 150-250℃/W. If the new power chip adopts the traditional LED packaging form, the chip junction temperature will rise rapidly and the epoxy will carbonize and turn yellow due to poor heat dissipation, thus causing the device to accelerate light decay until failure, and even fail due to the stress caused by rapid thermal expansion.
For power LED chips with large operating current, low thermal resistance, good heat dissipation and low stress The new packaging structure is the key technology of power LED devices. Low-resistance and high-thermal-conductivity materials can be used to bond the chip; copper or aluminum heat sinks are added to the bottom of the chip, and a semi-encapsulated structure is used to accelerate heat dissipation; even a secondary heat dissipation device is designed to reduce the thermal resistance of the device; the inside of the device is filled with highly transparent flexible silicone, which will not cause the device to open due to sudden temperature changes, nor will it turn yellow; the material of the parts should also fully consider its thermal conductivity and heat dissipation characteristics to obtain good overall thermal characteristics.
The packaging structures of ordinary LEDs and high-power LEDs are shown in Figures 2-5 and 2-6 respectively. The reference value of thermal resistance is shown in Table 2-1.
2-5 Ordinary LED packaging structure diagram
Figure 2-6 High-power LED package structure diagram Table
2-1 Comparison of thermal resistance reference values of ordinary LEDs and high-power LEDs
LED power Thermal resistance reference (℃/W)
Ordinary LED 150~250
1W LED < 50
3W LED < 30
5W LED < 18
10W LED < 9
b Secondary optical design technology
In order to improve the light collection efficiency of the device, design an additional reflector cup and multiple optical lenses.
c. Power LED white light technology
There are three common process methods for achieving white light:
① YAG phosphor is coated on the blue chip, and the yellow-green light emitted by the blue light excites the phosphor to synthesize white light with the blue light. This method is relatively simple, efficient and practical. The disadvantages are that the consistency of the amount of glue is poor, the phosphor is easy to precipitate, resulting in poor uniformity of the light output surface and poor color consistency; the color temperature is high and the color rendering is not ideal.
② Multiple chips or multiple devices of the three primary colors of RGB emit light and mix colors to produce white light, or use blue + yellow dual chips to complement the colors to produce white light. As long as the heat dissipation is done properly, the white light produced by this method is more stable than the previous method, but the driving is more difficult.③
Apply RGB phosphor on the ultraviolet chip, and use ultraviolet light to excite the phosphor to produce three primary colors to mix and form white light. Due to the low efficiency of the current ultraviolet chip and RGB phosphor, it has not yet reached the practical stage.
Table 2-2 Comparison of three main white light LED preparation routes
Ultraviolet LED + RGB phosphor Blue LED + Yellow phosphor Binary complementary color LED RGB multi-chip combination White light LED chip
Color rendering Best General General Good
Color stability Best Good General General Good
Lumen retention rate No data General Good Good
Fluorescent materials are under research and are relatively mature - - -
-Efficiency Best Good General General Good
Application White light lighting Backlight Special lighting display
Backlight
To achieve industrialization of W-level power LED products for lighting, the following technical problems must be solved:
①Control of phosphor coating amount and uniformity: The glue coating method used in the LED chip + phosphor process is usually to mix the phosphor with glue and then apply it to the chip with a dispenser. During the operation, due to the influence of factors such as the viscosity of the carrier glue being a dynamic parameter, the precipitation caused by the phosphor being heavier than the carrier glue, and the precision of the dispenser, it is difficult to control the uniformity of the phosphor coating amount in this process, resulting in uneven white light color.
② Chip optoelectronic parameter matching: The characteristics of semiconductor technology determine that there may be differences in optical parameters (such as wavelength, light intensity) and electrical (such as forward voltage) parameters between chips of the same material and the same wafer. This is even more true for RGB three-primary color chips, which have a great impact on the chromaticity parameters
of white light. This is one of the key technologies that must be solved for industrialization. ③ Control of light chromaticity parameters generated according to application requirements: Products with different uses have different requirements for the color coordinates, color temperature, color rendering, light power (or light intensity) and spatial distribution of white light LEDs. The control of the above parameters involves the coordination of many factors such as product structure, process methods, and materials. In industrial production, it is very important to control the above factors and obtain products that meet application requirements and have good consistency.
d. Testing technology and standards
With the development of W-class power chip manufacturing technology and white light LED process technology, LED products are gradually entering the lighting market. The parameter testing standards and test methods of traditional LED products for display or indication can no longer meet the needs of lighting applications. Domestic and foreign semiconductor equipment and instrument manufacturers have also launched their own test instruments. There are certain differences in the test principles, conditions, and standards used by different instruments, which increases the difficulty and complexity of test applications and product performance comparisons. LEDs are to expand into the lighting industry, and establishing LED lighting product standards is an important means of industrial standardization.
e. Screening technology and reliability assurance
Due to the limitations of the appearance of lamps, the assembly space of LEDs for lighting is sealed and limited, which is not conducive to the heat dissipation of LEDs, which means that the use environment of lighting LEDs is inferior to that of traditional display and indication LED products. In addition, lighting LEDs work under high current drive, which puts higher reliability requirements on them. In industrial production, it is necessary to conduct appropriate thermal aging, temperature cycle shock, and load aging process screening tests for different product uses to eliminate early failure products and ensure product reliability.
f. Electrostatic protection technology
Since GaN is a wide bandgap material with high resistivity, the induced charge generated by static electricity in the production process of this type of chip is not easy to disappear. When accumulated to a considerable degree, it can generate a very high electrostatic voltage. When the material's tolerance is exceeded, breakdown and discharge will occur. The positive and negative electrodes of the blue chip on the sapphire substrate are both located on the chip with a very small spacing; for the InGaN/AlGaN/GaN double heterojunction, the InGaN active layer is only tens of nanometers, and the tolerance to static electricity is very small. It is very easy to be broken down by static electricity, causing the device to fail. Compared with traditional LEDs, GaN-based LEDs have poor anti-static ability, which is their distinct disadvantage. The failure problem caused by static electricity has become a very thorny problem affecting the product qualification rate and use promotion. Therefore, in industrial production, whether static electricity prevention is appropriate directly affects the product yield, reliability and economic benefits.
There are several types of static electricity prevention technologies: ① Implement prevention in the production and use places from the aspects of human body, platform, ground, space, product transmission, stacking, etc. ② Design static electricity protection circuits on the chip. ③ Install static electricity protection devices on LEDs.
2) Multi-chip integrated packaging
In order to avoid the problem of reduced luminous efficiency caused by large-size chips, the method of integrating small-size chips can be used to increase the single chip
Keywords:LED
Reference address:Comparison of the main LED packaging technologies
LED has achieved rapid development in the past 30 years. The first batch of products appeared in 1968. The luminous flux of LED with a working current of 20mA was only a few thousandths of a lumen, and the corresponding luminous efficiency was 0.1 lm/W, and there was only one light color, red light at 650 nm. In the early 1970s, the technology progressed rapidly, the luminous efficiency reached 1 lm/W, and the colors were expanded to red, green and yellow. With the invention of new materials and the improvement of light efficiency, the power and luminous flux of a single LED light source are also increasing rapidly. Originally, the driving current of a general LED was only 20 mA. In the 1990s, the driving current of an LED light source code-named "Piranha" increased to 50-70mA, and the driving current of a new high-power LED reached 300-500 mA. In particular, the successful development of white light LEDs in 1998 has made a substantial step forward in the application of LEDs from simple identification display functions to lighting functions. Figures 2-1 to 2-4 describe the development of LEDs.
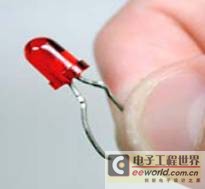
Figure 2-1 Ordinary LEDs are mainly used for indicator lights
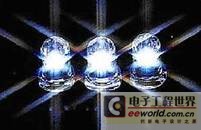
Figure 2-2 High-brightness LEDs are mainly used for lighting
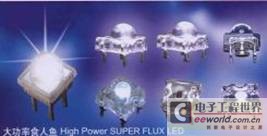
Figure 2-3 Piranha LED
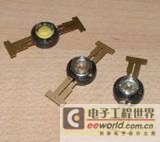
Figure 2-4 High-power LED
A Status of Power LED Packaging Technology
Power LEDs are divided into two types: power LEDs and watt (W) class power LEDs. The input power of power LEDs is less than 1W (except for LEDs with tens of milliwatts); the input power of W class power LEDs is equal to or greater than 1W.
HP first launched the "piranha" package structure LED in the early 1990s, and launched the improved "Snap LED" in 1994, with two working currents of 70mA and 150mA, and the input power can reach 0.3W. Then OSRAM launched the "PowerTOP LED", and then some companies launched a variety of power LED packaging structures. The power LEDs of these structures have several times higher input power than the original bracket packaged LEDs, and the thermal resistance is reduced to a fraction of the past.
W class power LEDs are the core of future lighting, and major companies around the world have invested a lot of effort in researching and developing their packaging technology. The first single-chip W-class power LED was LUXEON LED launched by Lumileds in 1998. The packaging structure is characterized by the use of thermal and electrical separation, the flip chip is directly soldered to the heat sink with a silicon carrier, and new structures and new materials such as reflective cups, optical lenses and flexible transparent adhesives are used. Now single-chip 1W, 3W and 5W high-power LEDs are available. Lumileds has a number of patented technologies in power-type white light diode packaging. OSRAM launched the single-chip "Golden Dragon" series LED in 2003. Its characteristics are that the heat sink is in direct contact with the metal circuit board, with good heat dissipation performance, and the input power can reach 1W. Nichia's 1W LED has an operating current of 350 mA, and the luminous flux of white light, blue light, blue-green light and green light are 23, 7, 28 and 20 lumens respectively, and its life is expected to be 50,000 hours.
B Overview of power LED packaging technology
If semiconductor LEDs are to be used as lighting sources, the luminous flux of conventional products is far from that of general-purpose light sources such as incandescent lamps and fluorescent lamps. Therefore, the key to the development of LEDs in the field of lighting is to increase their luminous efficiency and luminous flux to the level of existing lighting sources. Due to the continuous increase in the input power of LED chips, the power LED packaging technology should mainly meet the following two requirements: ① The packaging structure must have a high light extraction efficiency; ② The thermal resistance must be as low as possible, so as to ensure the photoelectric performance and reliability of the power LED.
The epitaxial material used in power LEDs adopts MOCVD epitaxial growth technology and multi-quantum well structure. Although its internal quantum efficiency needs to be further improved, the biggest obstacle to obtaining high luminous flux is still the low light extraction efficiency of the chip. The existing design of power LEDs uses a new flip-chip structure to improve the light extraction efficiency of the chip, improve the thermal characteristics of the chip, and increase the photoelectric conversion efficiency of the device by increasing the chip area and increasing the working current, thereby obtaining a higher luminous flux. In addition to the chip, the device packaging technology is also very important.
Key technologies for power LED packaging:
a. Heat dissipation technology
The traditional indicator LED packaging structure is generally to install the chip in a small-sized reflective cup or on a wafer stage with conductive or non-conductive glue, and then use gold wire to complete the internal and external connections of the device and then encapsulate it with epoxy resin. Its thermal resistance is as high as 150-250℃/W. If the new power chip adopts the traditional LED packaging form, the chip junction temperature will rise rapidly and the epoxy will carbonize and turn yellow due to poor heat dissipation, thus causing the device to accelerate light decay until failure, and even fail due to the stress caused by rapid thermal expansion.
For power LED chips with large operating current, low thermal resistance, good heat dissipation and low stress The new packaging structure is the key technology of power LED devices. Low-resistance and high-thermal-conductivity materials can be used to bond the chip; copper or aluminum heat sinks are added to the bottom of the chip, and a semi-encapsulated structure is used to accelerate heat dissipation; even a secondary heat dissipation device is designed to reduce the thermal resistance of the device; the inside of the device is filled with highly transparent flexible silicone, which will not cause the device to open due to sudden temperature changes, nor will it turn yellow; the material of the parts should also fully consider its thermal conductivity and heat dissipation characteristics to obtain good overall thermal characteristics.
The packaging structures of ordinary LEDs and high-power LEDs are shown in Figures 2-5 and 2-6 respectively. The reference value of thermal resistance is shown in Table 2-1.
2-5 Ordinary LED packaging structure diagram
Figure 2-6 High-power LED package structure diagram Table
2-1 Comparison of thermal resistance reference values of ordinary LEDs and high-power LEDs
LED power Thermal resistance reference (℃/W)
Ordinary LED 150~250
1W LED < 50
3W LED < 30
5W LED < 18
10W LED < 9
b Secondary optical design technology
In order to improve the light collection efficiency of the device, design an additional reflector cup and multiple optical lenses.
c. Power LED white light technology
There are three common process methods for achieving white light:
① YAG phosphor is coated on the blue chip, and the yellow-green light emitted by the blue light excites the phosphor to synthesize white light with the blue light. This method is relatively simple, efficient and practical. The disadvantages are that the consistency of the amount of glue is poor, the phosphor is easy to precipitate, resulting in poor uniformity of the light output surface and poor color consistency; the color temperature is high and the color rendering is not ideal.
② Multiple chips or multiple devices of the three primary colors of RGB emit light and mix colors to produce white light, or use blue + yellow dual chips to complement the colors to produce white light. As long as the heat dissipation is done properly, the white light produced by this method is more stable than the previous method, but the driving is more difficult.③
Apply RGB phosphor on the ultraviolet chip, and use ultraviolet light to excite the phosphor to produce three primary colors to mix and form white light. Due to the low efficiency of the current ultraviolet chip and RGB phosphor, it has not yet reached the practical stage.
Table 2-2 Comparison of three main white light LED preparation routes
Ultraviolet LED + RGB phosphor Blue LED + Yellow phosphor Binary complementary color LED RGB multi-chip combination White light LED chip
Color rendering Best General General Good
Color stability Best Good General General Good
Lumen retention rate No data General Good Good
Fluorescent materials are under research and are relatively mature - - -
-Efficiency Best Good General General Good
Application White light lighting Backlight Special lighting display
Backlight
To achieve industrialization of W-level power LED products for lighting, the following technical problems must be solved:
①Control of phosphor coating amount and uniformity: The glue coating method used in the LED chip + phosphor process is usually to mix the phosphor with glue and then apply it to the chip with a dispenser. During the operation, due to the influence of factors such as the viscosity of the carrier glue being a dynamic parameter, the precipitation caused by the phosphor being heavier than the carrier glue, and the precision of the dispenser, it is difficult to control the uniformity of the phosphor coating amount in this process, resulting in uneven white light color.
② Chip optoelectronic parameter matching: The characteristics of semiconductor technology determine that there may be differences in optical parameters (such as wavelength, light intensity) and electrical (such as forward voltage) parameters between chips of the same material and the same wafer. This is even more true for RGB three-primary color chips, which have a great impact on the chromaticity parameters
of white light. This is one of the key technologies that must be solved for industrialization. ③ Control of light chromaticity parameters generated according to application requirements: Products with different uses have different requirements for the color coordinates, color temperature, color rendering, light power (or light intensity) and spatial distribution of white light LEDs. The control of the above parameters involves the coordination of many factors such as product structure, process methods, and materials. In industrial production, it is very important to control the above factors and obtain products that meet application requirements and have good consistency.
d. Testing technology and standards
With the development of W-class power chip manufacturing technology and white light LED process technology, LED products are gradually entering the lighting market. The parameter testing standards and test methods of traditional LED products for display or indication can no longer meet the needs of lighting applications. Domestic and foreign semiconductor equipment and instrument manufacturers have also launched their own test instruments. There are certain differences in the test principles, conditions, and standards used by different instruments, which increases the difficulty and complexity of test applications and product performance comparisons. LEDs are to expand into the lighting industry, and establishing LED lighting product standards is an important means of industrial standardization.
e. Screening technology and reliability assurance
Due to the limitations of the appearance of lamps, the assembly space of LEDs for lighting is sealed and limited, which is not conducive to the heat dissipation of LEDs, which means that the use environment of lighting LEDs is inferior to that of traditional display and indication LED products. In addition, lighting LEDs work under high current drive, which puts higher reliability requirements on them. In industrial production, it is necessary to conduct appropriate thermal aging, temperature cycle shock, and load aging process screening tests for different product uses to eliminate early failure products and ensure product reliability.
f. Electrostatic protection technology
Since GaN is a wide bandgap material with high resistivity, the induced charge generated by static electricity in the production process of this type of chip is not easy to disappear. When accumulated to a considerable degree, it can generate a very high electrostatic voltage. When the material's tolerance is exceeded, breakdown and discharge will occur. The positive and negative electrodes of the blue chip on the sapphire substrate are both located on the chip with a very small spacing; for the InGaN/AlGaN/GaN double heterojunction, the InGaN active layer is only tens of nanometers, and the tolerance to static electricity is very small. It is very easy to be broken down by static electricity, causing the device to fail. Compared with traditional LEDs, GaN-based LEDs have poor anti-static ability, which is their distinct disadvantage. The failure problem caused by static electricity has become a very thorny problem affecting the product qualification rate and use promotion. Therefore, in industrial production, whether static electricity prevention is appropriate directly affects the product yield, reliability and economic benefits.
There are several types of static electricity prevention technologies: ① Implement prevention in the production and use places from the aspects of human body, platform, ground, space, product transmission, stacking, etc. ② Design static electricity protection circuits on the chip. ③ Install static electricity protection devices on LEDs.
2) Multi-chip integrated packaging
In order to avoid the problem of reduced luminous efficiency caused by large-size chips, the method of integrating small-size chips can be used to increase the single chip
Previous article:LED packaging technology, structural types and product application prospects
Next article:High-brightness LED packaging light flux principle
Recommended ReadingLatest update time:2024-11-16 16:56
Analysis of LED application in backlight module
1. LEDs used in backlight modules have the advantage of saving power
LED is used as a light source in the backlight module to replace the traditional cold cathode fluorescent lamp (CCFL). It is not only light and thin, power-saving, small in size, long in life, low in voltage, and fast in startup, but also envi
[Power Management]
Three things to note when using LED display
1.
Notes
on switching
LED
electronic display screen:
1. Switching sequence:
When opening the screen: turn on the machine first, then open the screen.
When turning off the screen: turn off the screen first, then turn off the phone
(If you turn off the computer first but not the dis
[Power Management]
A simple ballpoint pen can handwrite customized LEDs
Researchers at Washington University in St. Louis have developed an ink pen that allows individuals to handwrite flexible, stretchable optoelectronic devices on everyday materials such as paper, textiles, rubber, plastics and even 3D objects. A newly published paper in Nature Photonics reports this simple and versatil
[Internet of Things]
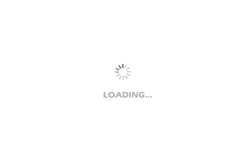
Select LED driver topology based on application needs
发光二极管 (HB- led) 在每封装流明输出和光效 (efficacy ,单位为流明 / 瓦或 lm/W) 方面的性能快速提升。商用的 1 W LED 已提供有冷色温 LED( 色温 5000K) 的每封装流明输出超过 100 流明,光效达 100 lm/W ,而相同功率等级的暖色温白光 LED( 色温 3000 至 3500K) 也超过了 70 到 80 流明。与两年前相比,这些性能等级提高了 30-40% 。有了这样的性能, LED 如今正逐步发展成为众多高性能应用中传统白炽灯、卤素灯和荧光灯的切实可行的替代光源。因此,固态 照明 (SSL) 相当多地渗入到了汽车、商业和景观照明,以及城市街道照明之中。 LED 还能用于新
[Power Management]
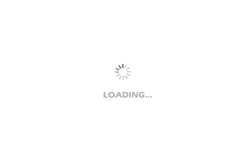
Five factors of LED quality determine the full-color LED display
The choice of LED has determined more than 50% of the quality of the entire display. If the LED is not selected well, no matter how good the other components of the display are, they cannot make up for the defects in the quality of the display. The most critical component of the full-color LED display is the LED device
[Power Management]
Keil uses the tutorial to write the first LED light program
1. Create a new empty folder 2. Open keil -- new uVision project 3. Select the directory and name the file 4. Select chip 5. Add files 6. Write C51 MCU program According to the circuit diagram you drew, confirm the pins Here we write a program to light up an LED lamp, pin p0.0 7. Generate a hex file tha
[Microcontroller]
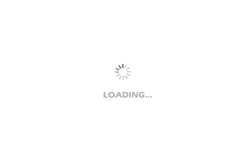
The influence of temperature on LED guardrail tube and its countermeasures
In daily conditions, the temperature changes that LED guardrail tubes experience every day include not only normal temperature changes, but also the greenhouse effect caused by sunlight radiation heating. What is the impact of temperature on guardrail tubes? The following uses the state equation of gas to make analy
[Power Management]
Driving LED offline lighting to its full potential
While it may be years before a viable screw-in LED replaces incandescent bulbs, the use of LEDs in architectural lighting is growing, offering greater reliability and energy savings potential. Like most electronics, a power supply is needed to convert the input power into a form usable by the LEDs. In a streetlight
[Power Management]
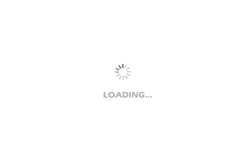
- Popular Resources
- Popular amplifiers
Recommended Content
Latest Power Management Articles
- MathWorks and NXP Collaborate to Launch Model-Based Design Toolbox for Battery Management Systems
- STMicroelectronics' advanced galvanically isolated gate driver STGAP3S provides flexible protection for IGBTs and SiC MOSFETs
- New diaphragm-free solid-state lithium battery technology is launched: the distance between the positive and negative electrodes is less than 0.000001 meters
- [“Source” Observe the Autumn Series] Application and testing of the next generation of semiconductor gallium oxide device photodetectors
- 采用自主设计封装,绝缘电阻显著提高!ROHM开发出更高电压xEV系统的SiC肖特基势垒二极管
- Will GaN replace SiC? PI's disruptive 1700V InnoMux2 is here to demonstrate
- From Isolation to the Third and a Half Generation: Understanding Naxinwei's Gate Driver IC in One Article
- The appeal of 48 V technology: importance, benefits and key factors in system-level applications
- Important breakthrough in recycling of used lithium-ion batteries
MoreSelected Circuit Diagrams
MorePopular Articles
- Innolux's intelligent steer-by-wire solution makes cars smarter and safer
- 8051 MCU - Parity Check
- How to efficiently balance the sensitivity of tactile sensing interfaces
- What should I do if the servo motor shakes? What causes the servo motor to shake quickly?
- 【Brushless Motor】Analysis of three-phase BLDC motor and sharing of two popular development boards
- Midea Industrial Technology's subsidiaries Clou Electronics and Hekang New Energy jointly appeared at the Munich Battery Energy Storage Exhibition and Solar Energy Exhibition
- Guoxin Sichen | Application of ferroelectric memory PB85RS2MC in power battery management, with a capacity of 2M
- Analysis of common faults of frequency converter
- In a head-on competition with Qualcomm, what kind of cockpit products has Intel come up with?
- Dalian Rongke's all-vanadium liquid flow battery energy storage equipment industrialization project has entered the sprint stage before production
MoreDaily News
- Allegro MicroSystems Introduces Advanced Magnetic and Inductive Position Sensing Solutions at Electronica 2024
- Car key in the left hand, liveness detection radar in the right hand, UWB is imperative for cars!
- After a decade of rapid development, domestic CIS has entered the market
- Aegis Dagger Battery + Thor EM-i Super Hybrid, Geely New Energy has thrown out two "king bombs"
- A brief discussion on functional safety - fault, error, and failure
- In the smart car 2.0 cycle, these core industry chains are facing major opportunities!
- The United States and Japan are developing new batteries. CATL faces challenges? How should China's new energy battery industry respond?
- Murata launches high-precision 6-axis inertial sensor for automobiles
- Ford patents pre-charge alarm to help save costs and respond to emergencies
- New real-time microcontroller system from Texas Instruments enables smarter processing in automotive and industrial applications
Guess you like
- Powering a Boost Topology Battery Charger with a Solar Panel
- [RISC-V MCU CH32V103 Review] USB flash drive read and write test
- NI Special Month, enjoy up to 40% off on software and more!
- Help: About the ESP32 Anxinke integrated environment project import compilation error
- Various PCB onboard antennas and PCB design points
- 【Silicon Labs Development Kit Review 06】_Transplanting freertos+Vcom+LED
- There is no more comprehensive article about RF chips than this one! Worth saving!
- Supplement: Design of the lower computer for the computer room monitoring project
- Emulating an IBM PC on ESP32
- Understanding C language pointers