1 Introduction
In the substation, the DC power supply is very important for the secondary equipment of the substation and the real-time communication of the substation. If the DC power supply is unreliable, it will cause the relay protection to fail, resulting in the expansion of the power outage area, and communication errors, leading to greater accidents. For this reason, it is required to have higher reliability. Usually, energy storage capacitors or batteries are used as backup power supplies and directly used as DC outputs, but the output power quality is not high and the battery management is complicated. Therefore, this article uses a switching power supply with a battery to improve the reliability of the power supply, while the output power quality is high to meet the communication requirements. In general, battery management is a very complicated task. The system uses a PIC16C73 microcontroller to implement battery management, and the management solution is simple and reliable.
2 24V DC uninterruptible power supply system
The schematic diagram of the 24V distribution network dedicated uninterruptible power supply system is shown in Figure 1.
Figure 1 Schematic diagram of 24V DC power supply system dedicated to substation distribution network
2.1 Performance indicators of power supply system
Two-way AC input 90~130V;
Can be used to start small DC motors in substations;
Output DC 24±0.03V;
Real-time detection of battery operating parameters and remote monitoring;
When the load current is 3A, the standby time is ≥10h;
Battery management operations can be performed remotely and on-site;
Working temperature range: -40℃~+80℃.
2.2 Power supply system modules
1) The first stage is a half-bridge DC/DC circuit, which is used as a charger. To improve reliability, the input is two AC 110V, which can work at AC 90~130V, and the output is DC 28V (the battery is in the charging state), which is used to charge the battery and start a small DC motor through the battery. The switch tube uses the transistor 2SC2625, and the control chip uses TL494. Circuit self-excitation start process: The voltage divider resistor on the DC bus makes the V BE of 2SC2625 ≥0.6V, the transistor is turned on, the circuit starts to self-excite, and an instantaneous voltage is established on the auxiliary winding, which makes the TL494 work and the circuit enters the normal working state.
2) The DC/DC circuit at the latter stage adopts a push-pull circuit structure, and the transformer is bidirectionally magnetized, which effectively prevents magnetic saturation [1] . Since the battery terminal voltage can vary between 21V and 27V, the circuit can achieve buck-boost regulation, so that the output voltage is stabilized at 24V, meeting the load requirements.
3) The battery management module uses PIC16C73, and its block diagram is shown in Figure 2. PIC16C73 is a PIC8-bit mid-range microcontroller launched by Microchip. It has only 35 single-byte instructions, 5 built-in A/D conversion modules, good stability, and can work in harsh environments [2] .
Figure 2 Battery management block diagram
Through the sampling circuit, the battery terminal voltage, discharge current, charge current, battery temperature, AC power failure, charger fault signal, etc. are sent to PIC16C73 for processing in real time. The processed data can be sent to the on-site LCD display for on-site inspection; the data can be sent to the host computer for remote monitoring.
4) The integrated controller TL494 of the switching power supply can output two complementary pulse control signals, and can also realize single-ended output. The minimum dead zone is 3% and adjustable, and there is a voltage stabilization and overcurrent protection op amp inside.
3 Battery Management Solution and Function Implementation
The hardware diagram of the battery management part is shown in Figure 3.
Figure 3 Battery management hardware diagram
3.1 Selection of battery capacity
To meet the requirement of continuous discharge under AC power outage. Under the condition that the manufacturer provides the battery capacity conversion factor Kc , the capacity C is calculated using formula (1) [3]
C = IG /( K c δ T δ K ) (1)
Where: I is designed according to the maximum load current of the distribution network;
G is the independent power supply time of the battery, which is determined by the reliability level of the distribution network;
δ T is the temperature coefficient of battery discharge capacity. When the ambient temperature is between 15 and 25°C, the capacity increases or decreases by 0.006 to 0.007 of the rated capacity for every 1°C increase or decrease in temperature. δ T =1+0.006( T -25°C);
δ K is the battery aging coefficient, which is generally taken as 0.8.
According to the above principles and combined with the actual application scenarios, this system selected two 12A·h/12V lead-acid batteries in series.
3.2 Hardware Implementation of Battery Management
After AC power is turned on, the battery is charged through R 4 and D 3 , and input is provided for the next stage. At this time, relay K 1 is energized, but due to the reverse bias of D 4 , the battery does not discharge the load; when AC power is off or the battery is discharged, D 1 is reverse biased and cut off, and the battery supplies power to the load through the relay contacts and D 4. When the battery voltage is detected to be ≤21V, the power supply is stopped and the system is in a complete power outage state. This situation should be avoided. R 7 and R 8 are used to detect the charge and discharge current of the battery. In the charging state, the 28V DC output is constant, and when it is in the discharge state, the output will change.
1) DC starting In the case of AC power failure, you can directly press S1 , the battery will power the load, at the same time, R5 terminal is high level, relay K1 is energized, even if S1 is disconnected, the power supply will not be interrupted, and S1 will be self-locked.
2) Discharge control Since the battery is in a charging state in most cases, this has a great impact on the battery life. Therefore, the battery should be discharged within a certain period of time. In this system, discharge is divided into manual discharge and automatic timed discharge. The length of the timer is determined according to the user's requirements, generally set to 60 days. After the internal timer of the single-chip microcomputer reaches the time, a discharge signal is given. The discharge signal passes through the hardware circuit and a resistor R1 is connected to the R3 terminal , so that the potential of TL494 pin 1 rises, the control pulse becomes narrower, the output voltage becomes lower, and D1 is in reverse bias cutoff. At this time, the battery alone supplies power to the load, and the previous DC/DC is equivalent to a no-load state. According to the battery manufacturer's recommendation, the battery discharge end voltage is set to 10.5V×2=21V. When the battery voltage is detected to be ≤21V, the discharge signal is canceled, and the charger charges the battery and provides energy to the load at the same time.
3) Motor start-up Since the current required for motor start-up is relatively large, this purpose is achieved by discharging the battery in this system. Before starting, a signal is sent manually to reduce the voltage of the charger, and the battery starts working.
4) Charging voltage is controllable. Changing the charging voltage of the battery means changing the output of the charger. By connecting different resistors R1 and R2 in parallel to the R3 terminal , the output voltage can be changed. Users can set the voltage according to their needs.
3.3 Battery parameter detection
1 ) Charging current Ic and discharging current Id When the battery is in charging state, due to the clamping effect of D4 , the load current Io is completely provided by the charger . At this time, the terminal voltage of R7 U R7 = Io R7 , Id = 0 , I R8 = Io + Ic , and R7 = R8
I c = ( UR 8 - U R 7 ) / R 7 ;
When powered by a battery alone, the clamping effect of D4 disappears . At this time, UR8 = 0, Ic = 0, therefore, Id = Io = UR7 / R7. Therefore, as long as UR7 and UR8 are used to obtain a 0-5V current signal through a differential amplifier and sent to the two A / D conversion channels of PIC16C73 , Ic and Id at any moment can be detected through processing by the microprocessor .
2) Battery voltage Since two 12V batteries are connected in series, the battery terminal voltage should be detected separately, and the voltage output is obtained by resistor voltage division to obtain the voltage sampling value. When the battery voltage U B1 ( U B2 ) is detected to be | ( U B1 -12) |/12 ≥ δ 0 (δ 0 is the balance rate, 4% here), it means that the battery voltage is not charged evenly, and corresponding measures should be taken.
3) Battery temperature: The AD590 temperature sensor is used to send the temperature sampling value to the single-chip microcomputer. When it is detected that the battery temperature exceeds 80℃ for more than 10 minutes, the discharge control signal is immediately canceled, and the high level of R5 is changed to a low level to disconnect the relay.
4) Battery capacity Battery capacity detection has always been a difficult problem in battery management. Common methods include: capacity prediction based on electromotive force, capacity prediction based on battery internal resistance, capacity prediction based on both battery internal resistance and electromotive force, capacity prediction based on current discharge rate, capacity prediction based on current time integral, etc. In this system, since the load change follows Io = 0.2n ( n is the number of parallel loads), the capacity detection uses the capacity prediction of current time integral, which makes the detection simple and feasible. The battery discharge capacity CΔ = Iddt . Due to the switching of the load , the current changes according to a fixed rule, so CΔ = 0.2n1t1 + 0.2n2t2 (n1t1, n2t2 is the time of different loads ) . If the initial capacity C o of the battery before discharge is known , the battery capacity after the change is Cx = C o - CΔ . This method is relatively simple and easy to implement, and can use the current sampling circuit of the system itself without the need for additional special equipment.
3.4 Prediction of remaining time
The purpose of battery capacity prediction is to obtain information about the working time that the battery system can provide. Therefore, in fact, we only need to know the working time that the battery system can provide under the current conditions (voltage, current, temperature). At a certain moment, the voltage, current, and temperature values can be measured, so we can predict the duration of the battery's constant current discharge at this current, that is, there is such a table in the system, which divides the voltage into several levels and the current into several levels, as listed in Table 1.
Table 1 Battery capacity prediction table
I 0 | I x | I | |
---|---|---|---|
V o | t (0,0) | t (0, x ) | t (0, m ) |
V x | t ( x ,0) | t ( x , x ) | t ( x , x ) |
V n | t ( n ,0) | t ( n , x ) | t ( n , m ) |
What the system needs to do is to fill the table and calculate the time the battery can run at the current according to the terminal voltage and current at a certain moment. The size of the voltage and current grading interval determines the accuracy of the battery remaining capacity prediction. The following takes a 12A·h/12V lead-acid battery as an example to illustrate the working process of the system.
1) Initialization of the table Initialization can be done in two ways: first, by obtaining data from the battery discharge curve provided by the battery manufacturer; second, by obtaining data from operation. The initialization data does not need to fill the table completely, but the amount of initialization data determines the accuracy of the remaining capacity prediction at the initial stage of system operation. We divide the current into 4 levels: 0.05 C / 0.1 C / 0.15 C / 0.2 C , and the voltage is divided into 0.1V levels.
2) Correction voltage At different discharge currents, the battery internal resistance and polarization voltage are different. Therefore, the correction voltage at different discharge currents must be obtained first. Using 0.05 C as the benchmark, the battery is discharged and the correction voltage at different voltage points is obtained.
3) Predicting the remaining time Based on the initialization result, obtain part of the data in the prediction table. If t ( V1 , I2 ) is known from the prediction table, predict the remaining time when I1 discharges to V1 , and use the conversion formula (2) to predict.
t ( V 1 , I 1 )= t ( V 1 − V x 2 + V x 1 , I 2 )× I 2 / I 1 (2)
Where: t ( V 1 , I 1 ) is the remaining time when the battery voltage reaches V 1 after discharging at I 1 ;
Vxn is the correction voltage corresponding to each current.
The selection of I 2 takes into account the principle of proximity to ensure the accuracy of the prediction. The most recent discharge result is selected for prediction. For example, if the last discharge was 0.1 C and 0.2 C is to be predicted this time , I 2 is 0.1 C. This is because the physical and chemical state of the battery is changing at any time. The closer the time is, the more accurate the result should be. The error of this method in predicting the remaining time is less than 15 minutes. In practical applications, it can improve the measurement accuracy of time and voltage, thereby improving the accuracy of prediction.
4) Correction of the prediction table The correction of the prediction table is carried out when the battery is discharged to the cut-off voltage and is divided into several cases:
(1) Before the end of discharge, the battery is discharged at a constant current, and the discharge prediction table under the constant current value is corrected;
(2) Before the discharge is completed, the battery is discharged by several currents, and the corresponding voltage prediction table of these currents is corrected by the time conversion formula (2);
(3) At different temperatures, correction is made according to -4mV/℃.
FIG4 is a flow chart of the remaining time prediction program.
Figure 4 Flowchart of the remaining time prediction program
The advantages of this forecasting method are:
——No need for a large number of preset curves;
——No need to add extra measuring equipment, making full use of the voltage and current measuring system of the original system;
——As the running time increases, the prediction accuracy increases;
——This prediction method can adjust the memory capacity as needed to improve accuracy.
4 Conclusion
The DC uninterruptible power supply system introduced in this article has high reliability, good EMC performance, simple battery detection scheme, convenient control operation, simple and practical remaining time prediction method, simple and flexible software and hardware design. It can be seen from the use of the substation site that the effect is very good.
Previous article:Application of wide area relay protection in smart grid
Next article:Design of power supply for LED display screen
Recommended ReadingLatest update time:2024-11-17 00:03
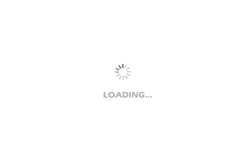
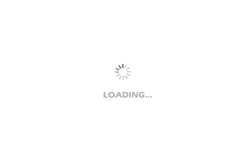
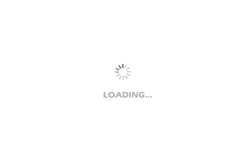
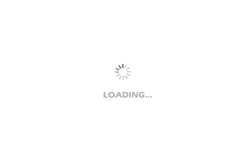
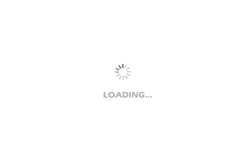
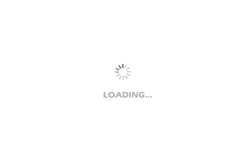
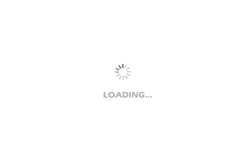
- Popular Resources
- Popular amplifiers
-
西门子S7-12001500 PLC SCL语言编程从入门到精通 (北岛李工)
-
New Energy Vehicle Detection and Diagnosis Experiment (Edited by Mao Caiyun, Zhou Xien, and Long Jiwen)
-
Virtualization Technology Practice Guide - High-efficiency and low-cost solutions for small and medium-sized enterprises (Wang Chunhai)
-
ESP32-S3 source code
- MathWorks and NXP Collaborate to Launch Model-Based Design Toolbox for Battery Management Systems
- STMicroelectronics' advanced galvanically isolated gate driver STGAP3S provides flexible protection for IGBTs and SiC MOSFETs
- New diaphragm-free solid-state lithium battery technology is launched: the distance between the positive and negative electrodes is less than 0.000001 meters
- [“Source” Observe the Autumn Series] Application and testing of the next generation of semiconductor gallium oxide device photodetectors
- 采用自主设计封装,绝缘电阻显著提高!ROHM开发出更高电压xEV系统的SiC肖特基势垒二极管
- Will GaN replace SiC? PI's disruptive 1700V InnoMux2 is here to demonstrate
- From Isolation to the Third and a Half Generation: Understanding Naxinwei's Gate Driver IC in One Article
- The appeal of 48 V technology: importance, benefits and key factors in system-level applications
- Important breakthrough in recycling of used lithium-ion batteries
- Innolux's intelligent steer-by-wire solution makes cars smarter and safer
- 8051 MCU - Parity Check
- How to efficiently balance the sensitivity of tactile sensing interfaces
- What should I do if the servo motor shakes? What causes the servo motor to shake quickly?
- 【Brushless Motor】Analysis of three-phase BLDC motor and sharing of two popular development boards
- Midea Industrial Technology's subsidiaries Clou Electronics and Hekang New Energy jointly appeared at the Munich Battery Energy Storage Exhibition and Solar Energy Exhibition
- Guoxin Sichen | Application of ferroelectric memory PB85RS2MC in power battery management, with a capacity of 2M
- Analysis of common faults of frequency converter
- In a head-on competition with Qualcomm, what kind of cockpit products has Intel come up with?
- Dalian Rongke's all-vanadium liquid flow battery energy storage equipment industrialization project has entered the sprint stage before production
- Allegro MicroSystems Introduces Advanced Magnetic and Inductive Position Sensing Solutions at Electronica 2024
- Car key in the left hand, liveness detection radar in the right hand, UWB is imperative for cars!
- After a decade of rapid development, domestic CIS has entered the market
- Aegis Dagger Battery + Thor EM-i Super Hybrid, Geely New Energy has thrown out two "king bombs"
- A brief discussion on functional safety - fault, error, and failure
- In the smart car 2.0 cycle, these core industry chains are facing major opportunities!
- The United States and Japan are developing new batteries. CATL faces challenges? How should China's new energy battery industry respond?
- Murata launches high-precision 6-axis inertial sensor for automobiles
- Ford patents pre-charge alarm to help save costs and respond to emergencies
- New real-time microcontroller system from Texas Instruments enables smarter processing in automotive and industrial applications
- 【TouchGFX Design】Make a Rubik's Cube
- Two circuits for modeling the behavior of a two-input AND gate
- Last two days! Application channel for GigaDevice GD32307E-START and GD32450I-EVAL evaluation will be closed soon, hurry up and get on board
- About MSP430 general I/O port settings
- Circuit protection devices protect mobile devices from ESD
- Let's discuss some gadgets commonly used by RF engineers
- Are there clear standards for defining differential amplification and instrument amplification? Is instrument amplification a type of differential amplification?
- [Serial] [Starlight Lightning STM32F407 Development Board] Chapter 8 External Interrupt Experiment
- [RVB2601 Creative Application Development] Infrared Device Control
- Analysis of Embedded C Language Pointers