OLED display technology is a type of OEL display technology. It has developed rapidly in the past decade and has achieved great success. More and more display manufacturers around the world have invested in research and development, which has greatly promoted the industrialization process of OLED. At present, OLED is on the eve of large-scale mass production. It is believed that in the near future, OEL display devices will have a breakthrough development.
1. The Origin and Development of OLED
The research of OLED originated from an accidental discovery. One night in 1979, Dr. CW Tang, a Chinese scientist working in Kodak, suddenly remembered that he had forgotten something in the laboratory on his way home. After returning home, he found a bright object in the dark. He turned on the light and found that it was an organic battery used in the experiment that was glowing. What was going on? OLED research began, and Dr. Deng was also known as the father of OLED.
In 1987, Kodak first published its research results. Since then, many companies and research institutions around the world have begun to devote themselves to the research of small molecule OLED devices and related topics. The number of related monographs and patents has increased by hundreds every year. In the United States (except Kodak) and Europe, most of the research work on organic EL started in the early 1990s. Today, organic EL devices with high efficiency (>15lm/w) and high stability (working life>10,000 hours when the luminous intensity is 150nits) have been developed.
The research on polymer organic EL started much later than that on small molecule organic EL. It was not until 1990 that Burroughes and his collaborators successfully developed the first polymer organic EL device. Since then, a lot of research has been done in the United States and Europe to develop polymer EL technology. People generally believe that polymer materials are more stable than organic small molecule materials, which has become the driving force for the development of polymer EL.
At present, OLED products have gone from the laboratory to the market. From 1997 to 1999, the only market for OLED displays was in car displays. After 2000, the application scope of the products gradually expanded to mobile phone displays. The application of OLED in mobile phones has greatly promoted the further development of its technology and the rapid expansion of its application scope, posing a strong challenge to the existing LCD, LED and VFD.
2. Characteristics and classification of OLED display
Organic electroluminescent light is referred to as OEL. It has two technical branches, one is the small molecule organic light-emitting diode (Organic Light Emitting Diode) with a molecular weight between 500 and 2000, referred to as OLED or SM-OLED; the other is the high molecule (also known as polymer) organic light-emitting diode (Polymer Light-Emitting Diode) with a molecular weight between 10000 and 100000, referred to as PLED or P-OLED.
OEL display devices have the advantages of active light emission, high light efficiency, low power consumption, light weight, thinness, and no viewing angle restrictions. They are considered by industry insiders to be the new generation of display devices that are most likely to dominate the future display device market. As a new display technology, OLED inevitably has many shortcomings. Its materials, device life, and yield rate need to be further studied and improved, and its application areas need to be further expanded, which provides a lot of research space for future scientific research exploration.
OLED technology has developed rapidly in the past decade and has made great achievements. As more and more display manufacturers around the world have invested in research and development, the industrialization process of OLED has been greatly promoted, making the growth rate of the OLED industry amazing, and it has now reached the eve of large-scale mass production. Industry insiders predict that 2007 may be the first year of large-scale mass production of OLED. From 2000 to 2005, the average annual growth rate of OLED panel shipments exceeded 175%. In the future, as OLED products gradually develop towards active full-color and large-size, the OLED industry will continue to maintain a high growth momentum. OLED products have gradually been recognized by downstream manufacturers, and the demand has also increased significantly. At present, the main application areas of OLED include communication products (mobile phone sub-screen), consumer electronics (MP3), automotive and instrumentation.
Compared with OLED technology, PLED technology is a little behind in development, mainly because of limited involvement of manufacturers, relatively immature technology, difficulty in synthesizing raw materials, and few equipment manufacturers. Despite this, its development speed is also very rapid, and products equipped with lower-grade PLED can already be seen on the market. According to DisplaySearch's forecast, by 2008, the PLED market share will quickly rise to 40% of the OEL market.
3. Brief description of the structure and luminescence mechanism of OLED
OLED display devices are current-type semiconductor light-emitting devices based on organic materials. Its typical structure is to make a layer of organic light-emitting material several tens of nanometers thick on ITO glass as a light-emitting layer, and there is a metal electrode with a low work function above the light-emitting layer. When a voltage is applied to the electrode, the light-emitting layer generates light radiation.
The luminescence mechanism and process of OLED is to inject electrons and holes from the cathode and anode respectively. The injected electrons and holes are transmitted in the organic layer and recombined in the luminescent layer, thereby exciting the molecules in the luminescent layer to produce singlet excitons. The singlet excitons radiate and decay to emit light.
There are three ways to achieve full color for OLED:
1. Use a white light-emitting layer plus a color filter. This is the simplest way to obtain full-color display.
2. Three organic light-emitting materials, red, green and blue, are used, so the light-emitting layer has a three-layer structure.
3. Use blue organic light-emitting materials and then use color conversion materials to obtain full color.
4. OLED preparation process
1. OLED preparation process
Currently in mainland China, the preparation of OLED display devices is still in the laboratory stage, but has reached the edge of pilot production, so we will mainly discuss the laboratory OLED preparation process.
Whether in the laboratory, pilot plant, or mass production, the preparation process of OLED devices is basically the same, and the main difference lies in the vacuum evaporation equipment of the device. The laboratory generally uses manual vacuum evaporation equipment to evaporate single samples in order to make different types of experimental samples; the pilot line generally uses semi-automatic vacuum evaporation equipment to continuously evaporate multiple samples to facilitate the switching of small batches of products; the mass production line generally uses fully automatic vacuum evaporation equipment for continuous sample evaporation (or line evaporation technology and processes) to improve the yield and reduce product costs. It is reported that some institutions are also studying and trying to use spin coating technology and processes to produce OLED products on mass production lines.
The preparation process of OLED display devices includes more than a dozen steps: ITO glass cleaning → photolithography → re-cleaning → pre-treatment → vacuum evaporation of organic layer → vacuum evaporation of back electrode → vacuum evaporation of protective layer → packaging → cutting → testing → module assembly → product inspection and aging test. The processes of several key processes are as follows.
(1) Cleaning and surface treatment of ITO glass
The surface state of ITO as an anode directly affects the injection of holes, the interface electronic state between the organic thin film layer and the film-forming properties of organic materials. If the ITO surface is not clean, its surface free energy becomes smaller, which causes the hole transport material evaporated on it to condense and form an uneven film.
The treatment process of ITO surface is: detergent cleaning → ethanol cleaning → acetone cleaning → pure water cleaning, all of which are cleaned with an ultrasonic cleaning machine. Each washing adopts the method of cleaning for 5 minutes, stopping for 5 minutes, and repeating 3 times. Then use an infrared oven to dry for standby use. The cleaned ITO glass also needs to be surface activated to increase the oxygen content of the ITO surface layer and improve the work function of the ITO surface. The ITO surface can also be treated with a hydrogen peroxide solution mixed with a ratio of water: hydrogen peroxide: ammonia = 5:1:1 to reduce the excess tin content on the ITO surface and increase the proportion of oxygen, so as to increase the work function of the ITO surface to increase the probability of hole injection, which can increase the brightness of the OLED device by an order of magnitude.
ITO glass should also be treated with "ultraviolet-ozone" or "plasma" surface treatment before use. The main purpose is to remove organic matter remaining on the ITO surface, promote oxidation of the ITO surface, increase the work function of the ITO surface, and improve the flatness of the ITO surface. The work function of the untreated ITO surface is about 4.6 eV. The work function of the ITO surface after ultraviolet-ozone or plasma surface treatment is above 5.0 eV, and the luminous efficiency and working life will be improved. The treatment of the ITO glass surface must be carried out in a dry vacuum environment. The treated ITO glass cannot be placed in the air for too long, otherwise the ITO surface will lose its activity.
(2) ITO photolithography process
(3) Vacuum evaporation process of organic thin films
OLED devices require the evaporation of multiple layers of organic thin films in a high vacuum chamber. The quality of the thin films is related to the quality and life of the device. There are multiple evaporation boats in the high vacuum chamber to place organic materials. The evaporation boats are heated to evaporate the organic materials, and a quartz crystal oscillator is used to control the film thickness. The ITO glass substrate is placed on a heated rotating sample holder, and a metal mask plate placed underneath controls the evaporation pattern.
The evaporation experiment was carried out on our vacuum evaporation equipment. The experimental results showed that the evaporation effect is better when the evaporation temperature of organic materials is generally between 170℃ and 400℃, the substrate temperature of ITO samples is between 100℃ and 150℃, the evaporation rate is between 1 point and 10 points/second (that is, about 0.1nm to 1nm/S), and the vacuum degree of the evaporation chamber is between 5×10-4Pa and 3×10-4Pa.
However, the evaporation of organic materials currently still has shortcomings such as low effective material utilization rate (<10%), difficulty in accurately controlling the concentration of dopants, unstable evaporation rate, and easy contamination of the vacuum chamber, which results in the coating uniformity of the sample substrate failing to meet the device requirements.
(4) Vacuum evaporation process of metal electrodes
The metal electrode still needs to be evaporated in the vacuum chamber. Metal electrodes usually use active metals with low work function, so they are evaporated after the organic material film is evaporated. Commonly used metal electrodes are Mg/Ag, Mg:Ag/Ag, Li/Al, LiF/Al, etc. The boat used for metal electrode evaporation is usually made of materials such as molybdenum, tantalum and tungsten, so that it can be used for different metal electrode evaporation (mainly to prevent the boat metal from chemically reacting with the evaporated metal).
The evaporation of metal electrode materials is generally represented by heating current. The evaporation experiment was carried out on our vacuum evaporation equipment. The experimental results show that the evaporation heating current of metal electrode materials is generally between 70A and 100A (some metals must exceed 100A), the substrate temperature of ITO samples is around 80°C, the evaporation rate is between 5 points and 50 points/second (that is, about 0.5nm to 5nm/S), and the vacuum degree of the evaporation chamber is between 7×10-4Pa and 5×10-4Pa. The evaporation effect is better.
(5) Device packaging process
The organic film and metal film of OLED devices will oxidize immediately when they come into contact with water and air, causing the device performance to decline rapidly. Therefore, they must not come into contact with air and water before packaging. Therefore, the packaging process of OLED must be carried out in a glove box that is free of water and oxygen and filled with inert gas (such as argon). The packaging materials include adhesives and covering materials. The adhesive uses a UV-curing epoxy curing agent, and the covering material uses a glass cover, in which a desiccant is installed to absorb residual moisture. Figure 3.4 shows the damage to the organic layer caused by water intrusion.
The earliest research on organic electroluminescence can be traced back to 1936[1], but the early light-emitting devices had high driving voltage and low luminous efficiency[2, 3], which did not attract much attention. In 1987, CW Tang et al. successfully prepared a small molecule light-emitting device driven by low voltage (<10V)[4], which once again attracted widespread attention to the phenomenon of organic luminescence. In 1990, JH Borroughes et al. reported the luminescence phenomenon of polymer devices under low voltage[5], opening up a new field of polymer material research.
Organic electroluminescent devices, also known as organic light-emitting diodes (OLEDs), are composed of a transparent anode ITO, a metal cathode, and an organic thin film layer, as shown in Figure 1. Driven by a DC voltage, the electrons injected from the cathode and the holes injected from the anode move toward the organic light-emitting layer, where they eventually meet and recombine to emit light. Depending on the materials used to prepare the organic light-emitting layer, there are two types of organic light-emitting devices: small molecules and polymers. The organic thin films of small molecule devices are generally multi-layer structures, while polymer devices are mostly single-layer structures. At present, small molecule devices have advantages in performance and have basically been industrialized, but they are relatively expensive and difficult to produce.
Previous article:What is a Surface Mount LED
Next article:LED chip life test
Recommended ReadingLatest update time:2024-11-16 15:40
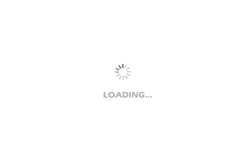
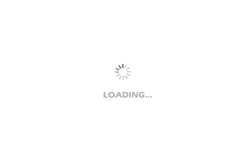
- Popular Resources
- Popular amplifiers
- MathWorks and NXP Collaborate to Launch Model-Based Design Toolbox for Battery Management Systems
- STMicroelectronics' advanced galvanically isolated gate driver STGAP3S provides flexible protection for IGBTs and SiC MOSFETs
- New diaphragm-free solid-state lithium battery technology is launched: the distance between the positive and negative electrodes is less than 0.000001 meters
- [“Source” Observe the Autumn Series] Application and testing of the next generation of semiconductor gallium oxide device photodetectors
- 采用自主设计封装,绝缘电阻显著提高!ROHM开发出更高电压xEV系统的SiC肖特基势垒二极管
- Will GaN replace SiC? PI's disruptive 1700V InnoMux2 is here to demonstrate
- From Isolation to the Third and a Half Generation: Understanding Naxinwei's Gate Driver IC in One Article
- The appeal of 48 V technology: importance, benefits and key factors in system-level applications
- Important breakthrough in recycling of used lithium-ion batteries
- Innolux's intelligent steer-by-wire solution makes cars smarter and safer
- 8051 MCU - Parity Check
- How to efficiently balance the sensitivity of tactile sensing interfaces
- What should I do if the servo motor shakes? What causes the servo motor to shake quickly?
- 【Brushless Motor】Analysis of three-phase BLDC motor and sharing of two popular development boards
- Midea Industrial Technology's subsidiaries Clou Electronics and Hekang New Energy jointly appeared at the Munich Battery Energy Storage Exhibition and Solar Energy Exhibition
- Guoxin Sichen | Application of ferroelectric memory PB85RS2MC in power battery management, with a capacity of 2M
- Analysis of common faults of frequency converter
- In a head-on competition with Qualcomm, what kind of cockpit products has Intel come up with?
- Dalian Rongke's all-vanadium liquid flow battery energy storage equipment industrialization project has entered the sprint stage before production
- Allegro MicroSystems Introduces Advanced Magnetic and Inductive Position Sensing Solutions at Electronica 2024
- Car key in the left hand, liveness detection radar in the right hand, UWB is imperative for cars!
- After a decade of rapid development, domestic CIS has entered the market
- Aegis Dagger Battery + Thor EM-i Super Hybrid, Geely New Energy has thrown out two "king bombs"
- A brief discussion on functional safety - fault, error, and failure
- In the smart car 2.0 cycle, these core industry chains are facing major opportunities!
- The United States and Japan are developing new batteries. CATL faces challenges? How should China's new energy battery industry respond?
- Murata launches high-precision 6-axis inertial sensor for automobiles
- Ford patents pre-charge alarm to help save costs and respond to emergencies
- New real-time microcontroller system from Texas Instruments enables smarter processing in automotive and industrial applications
- C2000 floating point calculation notes - differences between CPU and CLA and error handling techniques
- EEWORLD University ---- Theoretical basis of IoT terminal development
- Tips for implementing I2C with MSP
- ARM-based support for advanced video graphics capabilities on MCUs
- 12-bit ADC
- New Bluetooth TFT color screen capacitive touch electronic bracelet 10 yuan each
- Research and application of GaN materials
- What does it mean to have a window in the solder mask layer of a PCB? Reasons for having a window in the solder mask layer of a PCB
- Signal generator and DA conversion
- Use AM5728 EVM to make and download 6678 program