With the development of the global economy and the improvement of people's living standards, cars are increasingly used in daily life, so the requirements for energy conservation, emission reduction and driving safety are increasing. The automotive lighting system is a key component to ensure the safe driving of the car, and the light source is the key to the automotive lighting system. As the fourth generation of automotive light sources, light-emitting diodes (LEDs) have many advantages such as long life, low energy consumption, small size, fast response, and good monochromaticity, which conforms to the development trend of future automobiles in terms of safety, energy saving, compactness and fashion. It is believed that with the maturity of the automotive industry and the rapid development of LED chips, packaging, heat dissipation and other technologies, the application of LEDs in automotive lighting systems will become more and more extensive and the scale will become larger and larger.
1. Feasibility and advancement of automotive LED lighting
The use of lighting sources in cars began around the beginning of the 20th century. Kerosene lamps and acetylene lamps were first used, and electric light sources began to be used in 1910, followed by incandescent lamps, halogen tungsten lamps, and high-intensity discharge gas lamps HID (Intensity Discharge Lamp). Since 1985, the era of LED automotive lights has begun. At the same time, the technology of LED lamps used in the adaptive front lighting system AFS (Adaptive Front Lighting System) has emerged.
At present, LEDs have been used by many automobile manufacturers to manufacture various styles of headlights. In order to improve their overall competitiveness, famous brands such as BMW, Ford, Honda, Toyota, Mercedes-Benz, and Audi have launched new cars equipped with various LED headlights to attract customers. LEDs have many advantages that other light sources do not have: (1) Long life and good shock resistance. The theoretical service life of LEDs can reach 50,000 hours, and the actual service life can reach 20,000 hours (ordinary halogen bulbs are only about 150 to 500 hours), which generally exceeds the life of the car itself. In addition, there are no fragile moving parts in the basic structure of LEDs, so the shock resistance is very good. (2) Energy saving and environmental protection. LEDs can obtain sufficient brightness under low voltage and low current conditions, and their power consumption is only 10% to 20% of that of incandescent lamps of the same brightness; LED light sources do not contain mercury that is harmful to human health, and the production process and waste will not cause environmental pollution. (3) Fast response speed. Compared with incandescent lamps, the response time of LED lamps has reached tens of nanoseconds. Therefore, when LED is used as a car taillight, it can enable the driver of the following car to react earlier, thus reducing the occurrence of traffic accidents. (4) Small size. The compact LED can make the design of the car style more free and diversified, thus making the car model more fashionable; compared with traditional light sources, the installation depth of the LED signal light system can be reduced by 80 mm, which is of great significance to the car styling and internal parts layout.
At present, the automobile industry is still a pillar industry in the global economy and is in a critical period of rapid development. It will definitely drive the development of automotive lighting and provide a broad market space for the application of LEDs in automobiles.
2 Driving circuit for automotive LED lighting
LED is a current-controlled semiconductor device. Figure 1 is the volt-ampere characteristic curve of LED. As shown in Figure 1, this curve is relatively steep. Before forward conduction, almost no current flows through the LED. When the forward voltage exceeds the turn-on voltage, the current rises sharply. The luminous brightness L is approximately proportional to the forward current IF: L=KIF, where K is the proportional coefficient. Therefore, the luminous brightness of the LED can be controlled by controlling the IF of the LED. Therefore, in order to ensure the consistency of its brightness, a constant current source drive circuit is usually used.
The operating voltage range of the car battery is 9 V to 16 V, usually 12 V, but when the car is cold-started, the battery voltage can drop to 4 V, and when the battery is defective and the generator is directly powered, the voltage can reach a high voltage of 36 V. Therefore, for automotive LED lamps, in order to reliably drive the LED string with constant current, the drive controller must have precise voltage and current regulation, protection circuit and dimming function. Therefore, it is necessary to design a drive circuit with good voltage regulation performance and constant current output.
At present, automotive LED drivers generally use two methods to control forward current. (1) Use the VI curve of the LED to determine the voltage required to be applied to the LED to generate the expected forward current. The disadvantage is that any change in the LED forward voltage will cause a change in the LED current, and the voltage drop and power consumption of the ballast resistor will waste power and reduce the battery life. (2) Use a constant current source to drive the LED. Because this method requires the LEDs to be connected in parallel in the circuit, and driving parallel LEDs requires placing a ballast resistor in each LED string, which will lead to reduced efficiency and current mismatch. Therefore, neither of these two methods can fully reflect the advantages that LEDs should have. In order to overcome the shortcomings of existing automotive LED drivers, an efficient and intelligent driving method for automotive LED arrays has emerged. This method uses half-bridge DC-DC conversion technology, full-wave rectification technology, optocoupler technology, etc. to ensure the working efficiency of the entire drive circuit; an intelligent control scheme based on an embedded system is proposed. This scheme uses intelligent PWM current control and dimming control, and has load open circuit/short circuit protection and overcurrent and overvoltage protection functions. Figure 2 is the LED array intelligent driving experimental circuit.
As shown in Figure 2, the CPU outputs two completely inverted symmetrical PWM signals A and B, which act on the switch devices respectively to make them conduct in turn; the energy is coupled to the secondary through the high-frequency transformer T, and then full-wave rectified through the fast recovery diodes D1 and D2 to achieve the drive of the LED array. The photocoupler of the LED array drive circuit completes the monitoring of the LED array drive current and feeds back to the CPU, forming an intelligent current negative feedback closed-loop control system to ensure the stability and reliability of the drive current.
The integration and intelligence of automotive LED drive circuits are becoming increasingly higher. The miniaturization of chips and packages such as PMU (power management unit) will gradually replace the method of combining multiple single-function circuits to adapt to automotive applications with very limited board space. At the same time, due to the continuous development of control chips such as single-chip microcomputers, DSPs, and embedded technologies, the automation of automotive lighting systems can be achieved through software technology, so that the constant current drive accuracy of LEDs and the automatic adjustment of brightness will be more accurate. Intelligent control has become the design concept of the new generation of automotive LED drivers.
3 Automotive LED headlights
Since car headlights play an important role in driving safety, LED headlights are the most difficult and the last to be put into use. In the past, LED headlights were only used on concept cars. With the continuous development of LED lighting technology and the automotive industry, the application scope of LED headlights has transitioned from concept cars and luxury cars to mid-range cars and even general models, and the lighting intensity has reached the level of incandescent lamps.
Automobile headlights include high beam and low beam. When driving at night, the high beam should ensure that objects within 100 m in front of the car and 2 m in height are illuminated, and the brightness is uniform; the low beam should not only ensure that the driver can see obstacles clearly 40 m in front of the car, but also should not cause glare to oncoming drivers or pedestrians, so as to ensure the safety of the car when crossing at night.
Traditional automobile headlights output two types of beams: low beam and high beam. Each beam distribution mode is statically distributed, and the specific light distribution also complies with national standards. However, in actual applications, the beams emitted by this system are distributed in a limited angle range, which can easily cause visual blind spots in some complex road conditions (such as turning). In addition, traditional automobile front lighting systems do not have the function of automatically adjusting beam distribution. The conversion between low beam and high beam requires manual operation by the driver, which can easily cause glare between vehicles in a driving environment with frequent traffic. In order to overcome the above shortcomings of traditional automobile headlights, the adaptive front lighting system AFS came into being.
AFS is a headlamp system that enables drivers to better adapt to changes in speed, road type and weather conditions, thereby improving driving safety. Its working principle is as follows: When a car enters a special road condition (such as a curve), the signals transmitted from the angle sensor and speed sensor to the electronic control unit (ECU) change accordingly due to changes in the steering wheel and speed. The ECU captures these signal changes, determines which curve the vehicle has entered, and sends corresponding instructions to the headlamp control unit. The control unit controls the micromotor installed in the AFS lamp body according to the received instructions to drive the three light-emitting elements to rotate around the corresponding rotation axis, thereby changing the lighting mode when driving on unconventional roads and weather conditions, providing better safety protection.
With the development of white light LED technology and the requirements of aerodynamics and car styling, the front of the car is getting lower and more streamlined, and the space reserved for headlights is getting smaller and smaller. In order to meet the needs of intelligent and humanized car lighting, the combination of AFS and LED lights has become the development trend of modern car headlights.
4 Problems and countermeasures faced by automotive LED lighting
As a breakthrough new technology, automotive LED lighting technology has been accepted by most automakers and consumers, and more and more high-end cars are equipped with LED lights. However, due to the special requirements of the automotive application environment, there are still many technical problems to be solved in order to truly realize the replacement of traditional light sources with automotive LEDs.
(1) Cost Issue
Globally, the rate of decline in automotive LED production costs will be one of the main factors affecting the large-scale application of automotive LEDs in the future. In terms of the components themselves, the price of LED lights is generally higher than other traditional light sources. For example:
The market price of a 1 W high-power white light LED is about 10 to 100 times that of an incandescent lamp. Therefore, there is still a lot of room for price reduction of LED chips. The main ways to reduce the price are: ① Develop large chips and large currents. The current chips are generally between 0.5 mm and 1.5 mm. The small chips make it difficult to increase the current. This is an obstacle to the development of single-chip high-power LEDs. If the chip is made larger without reducing the light efficiency so that a larger current can pass through, the power of a single LED can be greatly increased. In this way, the number of LEDs used in lamps will be significantly reduced, which will help reduce the cost of lamps. ② Develop new substrate materials. China has started research on relatively cheap Si substrate materials, hoping to replace expensive sapphire or SiC. In addition to being cheap, Si can also be made into substrates with larger sizes than sapphire or SiC substrates to improve the utilization rate of MOCVD and thus increase the tube core yield [18]. In addition, since the hardness of Si is lower than that of sapphire and SiC, it can also save costs in processing. According to estimates by a well-known foreign company, the manufacturing cost of blue GaN LEDs made with silicon substrates will be 90% lower than that of sapphire and SiC substrates. ③ Continue to extend the life of LEDs. In theory, the life of LEDs has exceeded the life of cars, but in actual automotive applications, the life of LEDs needs to be further improved. If the actual life of LEDs can reach the life of the entire vehicle, there is no need to replace the light source during the life of the vehicle, eliminating the maintenance costs in this regard, which will be more economical.
As far as the entire automotive LED lighting system is concerned, the system-level cost of the LED driving solution must be reduced to improve the market competitiveness of this technology.
One way to reduce solution cost is to reduce the number of driver components as much as possible, which also helps to improve system reliability because each component on the PCB may be a failure point in the system.
(2) Heat dissipation problem
Generally, about 20% of the input power of high-power LEDs is converted into light energy, and the remaining 80% is converted into heat energy, which is much higher than that of traditional light sources. If this part of the heat energy cannot be discharged, the temperature of the LED interface will be too high, which will affect the product life cycle, luminous efficiency and stability, and thus the entire automotive lighting system will be seriously affected [19]. At present, the main ways to improve the heat dissipation of automotive LED lamps are: ① Improvement of the LED itself. First, improve the packaging structure. The thermal resistance of the traditional direct-plug LED packaging structure is as high as 250℃/W~300℃/W, while the new packaging structure uses low-resistivity and high-thermal conductivity materials to bond the chip, adds copper or aluminum heat sinks at the bottom of the chip, and adopts a semi-encapsulated structure, which greatly improves the heat dissipation capacity of the LED [20-21]. Secondly, improve the manufacturing materials of the LED, use ultra-thin, high-thermal conductivity, high-insulation ceramic sheets as the substrate, and improve the heat dissipation effect; develop phosphors with high quantum conversion efficiency and high temperature resistance, increase the maximum allowable junction temperature, and increase the allowable heat dissipation design temperature difference to reduce the difficulty of heat dissipation design. ② Improvement of heat dissipation device. The main improvements include: Consider adopting appropriate heat dissipation form, such as heat pipe, fan, water cooling, etc., to ensure that the heat is quickly dissipated and the heat dissipation device can work stably [22-23]; Consider the structure, shape and size of the heat sink to ensure sufficient heat dissipation area and good heat dissipation effect; Consider the design format of the circuit board. The printed circuit board can be designed into two layers, the lower layer is dedicated to the signal generation circuit and the drive circuit, and the upper layer is the LED dot matrix circuit. This can effectively prevent the heat of the LED from being transferred to the driver chip and causing damage to it.
(3) Lighting effect problem
Improving LED luminous efficiency is the key to the development of automotive LED technology and the starting point and driving force for the industrialization of automotive LED. From the perspective of packaging technology, LED packaging should minimize the total reflection of light inside it and increase the reflectivity of the substrate, so that as much light as possible can be transmitted, increasing the luminous efficiency of the LED. In February this year, Cree announced that its laboratory results have reached 2081 m/W of LED luminous efficiency. I believe this is not the limit, and there will be room for higher improvement, but new technological breakthroughs are needed.
(4) Electromagnetic interference problem
The automotive environment also faces the problem of electromagnetic interference (EMI). In-vehicle electronics are very sensitive to noise, especially navigation systems, wireless circuits, and AM radio band receivers. In order to minimize the possibility of noise interference, some LED driver ICs use a constant frequency switching topology. In addition, users can set the switching frequency in the range of 200 kHz to 2 MHz to keep the switching noise away from critical frequency bands (such as the AM radio band).
5 Outlook of the automotive LED lighting market
Although the application of LED in automotive lighting systems has just started, with the rapid development of semiconductor lighting technology and the automotive industry, the overall efficiency and cost-effectiveness of automotive LED lamps will be greatly improved, the scale of application will gradually expand, and eventually occupy the entire automotive lighting market.
According to the survey, the annual sales of LED for in-car applications in the world is about 500 million to 600 million euros. In the interior of the car, such as the car dashboard, in-car radio, switches, etc., 100% of them have adopted LED, and this trend is accelerating from in-car applications to exterior applications. In addition, the European Commission recently announced that from 2011, all new cars produced in the EU must be equipped with "daytime driving automatic lighting system". At the same time, the European Commission has approved Audi and Toyota to use LED as lighting lamps in cars. It can be seen that automotive LED lamps have great market potential worldwide.
Automotive LED lighting technology has also received strong support from our government.
In January 2010, the National Semiconductor Lighting Electronic Industry Standards Release and Promotion Conference was held in Jiangmen City, Guangdong Province, and the first batch of national standards for the LED industry was released, marking the beginning of the standardization era for the development of my country's LED industry [24].
Fang Zhilie, a professor at Fudan University and an expert in semiconductor physics, said that in 2009, the output value of LED application products in my country exceeded 60 billion yuan, and the entire industry has entered a major historical opportunity to achieve independent innovation and leapfrog development. In 2015, the industry scale is expected to reach 500 billion yuan [25]. Therefore, LED in my country will face huge development opportunities. Similarly, automotive LED lighting technology will also develop rapidly, and scientific research, production and business will pay close attention to this.
With its excellent reliability, environmental protection, energy saving and fashion, automotive LED lamps have injected new vitality into the upgrade and transformation of automobile lamps.
With the reduction of product costs, the improvement of production technology and the expansion of capital scale, the development of automotive LED lighting technology will surely provide stronger protection for automobile driving and safety. The LEDization of automotive lamps will surely become a turning point in the development history of automotive lighting systems.
Previous article:Comparison between LED road lighting and traditional road lighting
Next article:Design of color asynchronous LED large screen display
Recommended ReadingLatest update time:2024-11-16 15:49
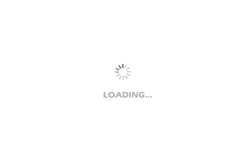
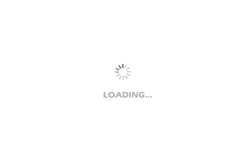
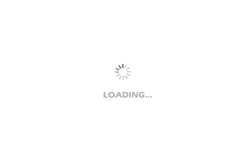
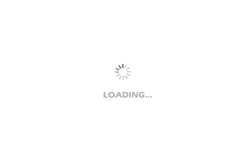
- Popular Resources
- Popular amplifiers
- MathWorks and NXP Collaborate to Launch Model-Based Design Toolbox for Battery Management Systems
- STMicroelectronics' advanced galvanically isolated gate driver STGAP3S provides flexible protection for IGBTs and SiC MOSFETs
- New diaphragm-free solid-state lithium battery technology is launched: the distance between the positive and negative electrodes is less than 0.000001 meters
- [“Source” Observe the Autumn Series] Application and testing of the next generation of semiconductor gallium oxide device photodetectors
- 采用自主设计封装,绝缘电阻显著提高!ROHM开发出更高电压xEV系统的SiC肖特基势垒二极管
- Will GaN replace SiC? PI's disruptive 1700V InnoMux2 is here to demonstrate
- From Isolation to the Third and a Half Generation: Understanding Naxinwei's Gate Driver IC in One Article
- The appeal of 48 V technology: importance, benefits and key factors in system-level applications
- Important breakthrough in recycling of used lithium-ion batteries
- Innolux's intelligent steer-by-wire solution makes cars smarter and safer
- 8051 MCU - Parity Check
- How to efficiently balance the sensitivity of tactile sensing interfaces
- What should I do if the servo motor shakes? What causes the servo motor to shake quickly?
- 【Brushless Motor】Analysis of three-phase BLDC motor and sharing of two popular development boards
- Midea Industrial Technology's subsidiaries Clou Electronics and Hekang New Energy jointly appeared at the Munich Battery Energy Storage Exhibition and Solar Energy Exhibition
- Guoxin Sichen | Application of ferroelectric memory PB85RS2MC in power battery management, with a capacity of 2M
- Analysis of common faults of frequency converter
- In a head-on competition with Qualcomm, what kind of cockpit products has Intel come up with?
- Dalian Rongke's all-vanadium liquid flow battery energy storage equipment industrialization project has entered the sprint stage before production
- Allegro MicroSystems Introduces Advanced Magnetic and Inductive Position Sensing Solutions at Electronica 2024
- Car key in the left hand, liveness detection radar in the right hand, UWB is imperative for cars!
- After a decade of rapid development, domestic CIS has entered the market
- Aegis Dagger Battery + Thor EM-i Super Hybrid, Geely New Energy has thrown out two "king bombs"
- A brief discussion on functional safety - fault, error, and failure
- In the smart car 2.0 cycle, these core industry chains are facing major opportunities!
- The United States and Japan are developing new batteries. CATL faces challenges? How should China's new energy battery industry respond?
- Murata launches high-precision 6-axis inertial sensor for automobiles
- Ford patents pre-charge alarm to help save costs and respond to emergencies
- New real-time microcontroller system from Texas Instruments enables smarter processing in automotive and industrial applications
- Some experience summary on AD conversion design
- How to conduct standard ZigBee testing and certification of products
- [Zero-knowledge ESP8266 tutorial] Quick Start 12- Making a flame alarm
- Ask: MOS tube switch circuit
- Introduction to the classification and manufacturing methods of PCB copper-clad laminates
- Problems that should be paid attention to in the development and design of TMS320C2XX
- Goodbye 2018, hello 2019
- STM32 related altium library files (F0, F1, F2, F3, F4, etc.)
- "Me and Intel SoC FPGA" + ARM hardcore development that is difficult to understand
- STM32L151C8T6 wake-up problem from standby mode