With the development of power switching devices, power electronic devices are becoming increasingly miniaturized and high-frequency, and their electrical performance has been greatly improved. However, the resulting high-order harmonics cause serious pollution to the power grid. In power electronic equipment, rectifiers (AC/DC converters) account for a large proportion and are the main source of pollution. Since the solid-state induction heating power supply presents nonlinear characteristics to the power grid, the current output from the power grid is not a standard sine curve. High-frequency harmonic currents cause overheating or other hazards to power facilities.
The application of boost circuit in power factor correction is relatively mature. Conventional circuits can be used to correct power factor of a few hundred watts. However, there are still many practical problems for high-power power such as induction heating power supply. In order to solve the problem that the switching device is easily damaged by the impact current generated during the reverse recovery of the diode and reduce the switching loss of the switching device at high frequency, this paper uses a passive lossless buffer circuit to replace the traditional LC filter circuit. After analyzing the working principle of the soft switching circuit and the time-sharing-phase shifting power control strategy of the inverter module, Matlab software was used for simulation, and the correctness of the theoretical analysis was verified by experimental results.
1 Overall topology of power supply system
As shown in Figure 1, the main circuit topology is mainly composed of rectification, soft switching Boost power factor correction, inversion, and load matching.
The DC voltage output by the single-phase rectifier bridge is connected to the passive buffer soft switch Boost circuit. This paper adopts the Boost circuit to replace the traditional LC filter circuit. The Boost circuit here has two main functions: one is to improve the power factor on the rectifier input side; the other is to provide a stable DC voltage for the inverter side. The Boost correction circuit outputs a DC voltage and adds it to the inverter bridge. The inverter bridge is a single-phase full-bridge inverter composed of 8 IGBT modules. Each IGBT has an anti-parallel diode connected in parallel with it as a freewheeling current when the inverter voltage is reversed. The inverter power device is driven by the control circuit to control the pulse signal and periodically switch; the role of the isolation transformer T is electrical isolation and load impedance matching. Generally, T is a step-down transformer. Appropriately changing the transformer ratio can reduce the voltage value on the inductor and capacitor in the resonant tank circuit, and different load impedance matching can be performed. The output square wave voltage is isolated and stepped down by the transformer and added to the resonant circuit composed of the compensation capacitor, the induction coil and the load.
1.1 Working principle of soft switching APFC circuit
Figure 2 shows a passive soft-switching Boost circuit, a series inductor, and a lossless SNUBBER circuit. Compared with the ordinary Boost circuit, the addition of inductor L1 limits the VT0 turn-on impact current generated by the reverse recovery of VD0, C2→VD7 serves as the SNUBBER circuit of VD0, and the series structure of VD5→VD6→VD7 and the resonance and energy conversion between L1→C1→C2 are also conducive to suppressing the turn-on impact current of VT0.
The working conditions of the main circuit in one cycle can be divided into 6 stages:
(1) Mode 1 [t0, t1]: At t0, C0 discharges through resistor R, VT0 turns on in the ZCS state, C1 discharges, and the current flows through the C1→C2→L1 loop. Due to the action of L1, the turn-on current of VT0 gradually and steadily increases.
(2) Mode 2 [t1, t2]: The current on the inductor L1 gradually increases. After C1 is discharged, the current flows through the loop L0→L1→VD5→VD6→C2.
(3) Mode 3 [t2, t3]: C2 is slowly charged until all the energy from L1 is transferred. Finally, the current flowing through VT0 is equal to that of L0, and the charging of C2 is completed.
(4) Mode 4 [t3, t4]: At t4, VT0 is turned off under ZVS. When the voltage across C2-VD6-C1 is equal to the rectifier output voltage Vin, C2 is discharged through VD7, and the current of L1 charges C1 via L0→L1→VD5→C1.
(5) Mode 5 [t4, t5]: When the voltage of C1 is equal to Vin, charging stops. The current of L1 flows to the load via VD5 → VD6 → VD7.
(6) Mode 6 [t5, t6]: L1 current decays to 0. Bus inductor current L1 charges C2 through VD7. When C2 voltage is 0, current flowing through L0 flows to loads C0 and R0 through VD0 and then returns to Mode 1.
1.2 Post-stage frequency doubling inverter circuit
The double frequency high frequency inverter power supply circuit is shown in the right part of Figure 1. In the figure, VT11 ~ VT41 constitute the first group of inverter bridges, and VT12 ~ VT42 constitute the second group of inverter bridges. The two groups of inverter bridges are turned on for one resonant cycle in turn, and each IGBT device works at the rated load current. In this way, if the allowable switching frequency of the IGBT is f0, the output frequency of the power supply is 2f0.
The time-sharing-phase shifting control method adjusts the power by adjusting the phase difference of the diagonal bridge arm conduction. There is a phase shift angle between VT11 and VT41. When the power is full, the angle is 0. The time-sharing-phase shifting power regulation is to achieve the change of power by adjusting the size of the phase shift angle φ.
2 System Control Strategy
The control system mainly uses Altera's MAXⅡ series CPLD chip EPMl270T144C5 and TI's TMS320LF2407A DSP. The control link consists of a digital phase-locked loop, a PWM control module, a time-sharing pulse control module, a DSP phase-shift power adjustment link, and a DSP-PFC link. The CPLD phase-locked loop module tracks the load resonant frequency and receives the digital phase-shift angle output by the DSP, thereby calculating and outputting 8 phase-shift trigger pulses through the PWM and time-sharing modules. The DSP calculates the load output power, compares it with the power setting value, and outputs the phase-shift angle through the integral separation PI algorithm; the DSP also performs average current control on the soft-switching Boost circuit in CCM mode. In addition, the settings, protection, and display functions must be implemented.
Figure 3 System control block diagram
Figure 4 Input side current and voltage waveforms
Figure 5 Current and voltage through the BOOST circuit switch tube
Figure 6 Output current and voltage when the phase shift angle is 90 degrees
3 Simulation and experimental waveforms
Based on the above theoretical analysis and the hardware and software design of the system, the circuit was simulated using Matlab simulation software. The simulation parameters are as follows: input single-phase 220 V, input equivalent impedance 1 mΩ, bus inductance 6 mH, output capacitor 3 300μF, buffer inductance 4μH, resonant resistance R is 22 Ω, inductance is 1×10-6, and capacitance is 1.15×10-6. Based on the simulation analysis, an experiment was conducted on a 1 kW induction power prototype, which showed that the experimental and simulation results were basically consistent, verifying the correctness of the theoretical design and system simulation.
Figure 7 Voltage and current test waveforms of the boost circuit switch tube
Figure 8 Current and voltage test waveforms on the input side
4 Conclusion
Through simulation and test results, it can be seen that the frequency-doubled induction power supply using the soft-switching PFC circuit not only achieves unity power factor on the input side, but also, with the help of some buffer auxiliary devices, the switch tube works in a soft-switching state, the loss is greatly reduced, and a stable DC voltage is output for the inverter module. This design has high practical value.
Previous article:The development trend of high-performance automotive power supply design
Next article:Use the simplest and cheapest means to achieve frequency jitter in SMPS and achieve lower EMC
Recommended ReadingLatest update time:2024-11-16 16:51
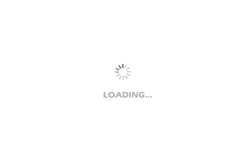
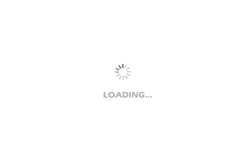
- Popular Resources
- Popular amplifiers
-
100 Examples of Microcontroller C Language Applications (with CD-ROM, 3rd Edition) (Wang Huiliang, Wang Dongfeng, Dong Guanqiang)
-
Theory and practice of small-size MOS device models for VLSI simulation
-
Power Electronics Technology 3rd Edition (Edited by He Yikang and Pan Zaiping)
-
Power electronics and motor control RTDS simulation (edited by Liu Guangchen and Tian Guizhen)
- MathWorks and NXP Collaborate to Launch Model-Based Design Toolbox for Battery Management Systems
- STMicroelectronics' advanced galvanically isolated gate driver STGAP3S provides flexible protection for IGBTs and SiC MOSFETs
- New diaphragm-free solid-state lithium battery technology is launched: the distance between the positive and negative electrodes is less than 0.000001 meters
- [“Source” Observe the Autumn Series] Application and testing of the next generation of semiconductor gallium oxide device photodetectors
- 采用自主设计封装,绝缘电阻显著提高!ROHM开发出更高电压xEV系统的SiC肖特基势垒二极管
- Will GaN replace SiC? PI's disruptive 1700V InnoMux2 is here to demonstrate
- From Isolation to the Third and a Half Generation: Understanding Naxinwei's Gate Driver IC in One Article
- The appeal of 48 V technology: importance, benefits and key factors in system-level applications
- Important breakthrough in recycling of used lithium-ion batteries
- Innolux's intelligent steer-by-wire solution makes cars smarter and safer
- 8051 MCU - Parity Check
- How to efficiently balance the sensitivity of tactile sensing interfaces
- What should I do if the servo motor shakes? What causes the servo motor to shake quickly?
- 【Brushless Motor】Analysis of three-phase BLDC motor and sharing of two popular development boards
- Midea Industrial Technology's subsidiaries Clou Electronics and Hekang New Energy jointly appeared at the Munich Battery Energy Storage Exhibition and Solar Energy Exhibition
- Guoxin Sichen | Application of ferroelectric memory PB85RS2MC in power battery management, with a capacity of 2M
- Analysis of common faults of frequency converter
- In a head-on competition with Qualcomm, what kind of cockpit products has Intel come up with?
- Dalian Rongke's all-vanadium liquid flow battery energy storage equipment industrialization project has entered the sprint stage before production
- Allegro MicroSystems Introduces Advanced Magnetic and Inductive Position Sensing Solutions at Electronica 2024
- Car key in the left hand, liveness detection radar in the right hand, UWB is imperative for cars!
- After a decade of rapid development, domestic CIS has entered the market
- Aegis Dagger Battery + Thor EM-i Super Hybrid, Geely New Energy has thrown out two "king bombs"
- A brief discussion on functional safety - fault, error, and failure
- In the smart car 2.0 cycle, these core industry chains are facing major opportunities!
- The United States and Japan are developing new batteries. CATL faces challenges? How should China's new energy battery industry respond?
- Murata launches high-precision 6-axis inertial sensor for automobiles
- Ford patents pre-charge alarm to help save costs and respond to emergencies
- New real-time microcontroller system from Texas Instruments enables smarter processing in automotive and industrial applications
- I have a question about the voltage regulator.
- GigaDevice GD32E231 DIY Competition Finalists
- [AB32VG1 Development Board Review] Button Control LED and Fan
- Writing cmd files in CCS
- Switching Power Supply Interest Group 17th Task
- The live broadcast has ended [Microchip Embedded Security Solutions | RISC-V Safe Place]
- EEWORLD University Hall----Live Replay: Application of MSP430 in Stepper Motor
- Recruiting mbse part-time training teachers
- [NXP Rapid IoT Review] Data Cloud Synchronization
- I am offering a reward to find a DSP expert with sufficient skills to be my mentor. It will be paid.