As we all know, the most important component of a frequency converter is the inverter. Early inverters, such as three-phase bridge inverters, often use a six-pulse operation mode, and their output voltage is a square wave or a step wave with a large harmonic content.
In recent years, with the advent of fully controlled power electronic devices that allow very high switching frequencies, such as IGBT, GTR, IGCT, etc., the control of inverters has mostly been replaced by pulse width modulation PWM, among which sinusoidal pulse width modulation SPWM is the most commonly used. The advantage of PWM is that it can simultaneously complete the tasks of frequency modulation and voltage regulation, greatly reducing the harmonic content in the output voltage. In addition, due to the high switching frequency, it is conducive to fast current control. When designing and studying frequency converters, the most convenient method is undoubtedly to use simulation tools. It should be said that the Matlab software of MATHWORKS, which has been developed for nearly 30 years, especially the Simulink simulation tool it provides, should be one of the best choices. It is a very powerful and complete simulation software with many toolboxes. Users can take out the required components from the toolbox, and through operations such as connection, establish a mathematical model corresponding to the physical object, so as to test it. The obtained simulation results can be used as a reference for design research.
In the Simulink (7.04) toolbox, there is a power system SimPowerSystem toolbox, which provides almost all the components required for inverter simulation, so it is easy to simulate using them. Reference [1] is an example of this type of simulation. It simulates a dual PWM AC-DC-AC inverter system, that is, converting a 1000 Hz, 500 V three-phase AC voltage into a 50 Hz, 400 V three-phase AC voltage. During the simulation, all components in the toolbox, including the PWM generator, are used.
It should be pointed out that in the actual application of frequency converters, the frequency converter is not required to output a fixed frequency, but an output voltage with variable frequency and amplitude. For example, in the frequency conversion system on the rotor side of a doubly fed induction generator (DFIG), as the wind speed and rotor speed change, the magnitude of the current supplied to the rotor side and the slip frequency must also change accordingly. In this way, the SPWM generator with fixed output frequency and constant voltage taken out of the toolbox is not competent, and must be realized by an externally controlled SPWM generator. This paper adopts the designed external control unit of the PWM generator to realize the real-time simulation of the variable output voltage frequency and amplitude of the frequency converter.
1 Structural types of AC-DC-AC inverters
Figure 1 is a typical AC-DC-AC inverter schematic, which is mainly composed of a rectifier (controllable or uncontrollable), a DC side capacitor C, a voltage source inverter VSI, and a PWM generator for control. In practice, there may also be input and output side filters (not shown in Figure 1). In addition, Figure 1 also shows a three-phase power supply and a load motor, which is a relatively typical usage.
Figure 2 shows the schematic diagram of the frequency conversion system for wind power generation DFIG to supply power to the rotor. In addition to the power grid (Ac Power Grid) and DFIG, it is mainly composed of the grid side inverter (Inverter on Grid Side) and the rotor side inverter (Inverter on Rotor Side) and the PWM generators connected to each other, and the DC side capacitor C. When the rotor speed is less than the synchronous speed of the stator magnetic field, the grid side inverter works in the rectification state and the rotor side inverter works in the inverter state. On the contrary, when the rotor speed is greater than the synchronous speed, the rotor side inverter works in the rectification state and the grid side inverter works in the inverter state. When this type of inverter works, the energy flows in both directions. Therefore, the inverter of Figure 1 is no longer applicable. In order to maintain the stability of the DC voltage, capacitors C are usually connected to the DC side of the two inverters to form a voltage source inverter. A filter is also provided in Figure 2 to ensure that the current waveform entering the rotor is a sine wave.
The requirement for the frequency converter that supplies power to the DFIG rotor is that both the frequency and amplitude of the supplied current are variable and controllable.
2 Inverter simulation structure diagram
Figure 3 is a structural diagram for simulation of a variable-frequency inverter with variable output voltage frequency and amplitude, which represents a three-phase AC-DC-AC frequency conversion system controlled by PWM. The system input is a three-phase 50Hz industrial frequency power supply, which is rectified by the SPWM rectifier Universal Bridge1, and the output DC voltage is filtered by a capacitor, and then enters the three-phase SPWM inverter Universal Bridge that can externally control the voltage frequency and amplitude, and is inverted into AC, and then filtered by the filter composed of L and C1, and then connected to the three-phase resistive load Load.
In addition, there are also instruments for measuring the incoming current and the total distortion rate THD of the load voltage, as well as instruments for measuring the waveforms of electrical quantities at each point, oscilloscopes, etc. It should be pointed out that the above simulation components are all taken from the SimPower Systems toolbox of Simulink.
The PWM generator PWMGeneration taken out from the Sim Power Systems toolbox has two working modes, namely internal setting mode and external control mode.
The internal setting needs to be set before running:
1) Working modes, such as single arm, double arm and 3-arm bridge, etc.;
2) Carrier frequency fc;
3) Modulation coefficient m;
4) Output voltage frequency;
5) Output voltage initial phase angle.
It can be seen that the output voltage frequency and voltage magnitude (modulation coefficient m) are fixed and cannot be changed during the model simulation. Under external control, the first two items of the internal setting formula need to be set, while the output voltage frequency f and modulation coefficient m are both allowed to be externally controlled.
Figure 4 shows the proposed method for 3 arms 6
The external control submodule of the pulse inverter (A) and its expansion diagram (B). It can be seen that the output voltage frequency f and the modulation coefficient m are controllable. The output voltage initial phase angle cannot and does not need to be adjusted during operation. Here, the three initial phase angles can be set in advance by three sine wave generators. Connecting the output Out1 of the external control submodule to the input terminal of the PWM generator set to External can realize the simulation of the inverter's real-time control of the output voltage frequency and amplitude changes during operation.
3 Simulation Examples
In this simulation example, it is assumed that the incoming power supply is three-phase 50Hz, the phase voltage amplitude is 500V, the carrier frequency of the left PWM generator is 1000Hz, the modulation factor m=0.8, the DC side filter capacitor C=1.5F, the inverter (Universal Bridge) output side filter inductor L=3×2 mH, when the input line voltage is 400V (effective value), 50 Hz, the filter capacitor reactive power Qc=3 kvar. At the line voltage of 400 V (effective value) 50Hz, the load active power is 50 kW.
The simulation is carried out under the condition that the inverter is loaded, and is divided into the following two situations:
1) The inverter output frequency is 35 Hz and is suddenly changed to 15 Hz by external control, and the modulation coefficient m remains unchanged;
2) The inverter output frequency remains at 45 Hz, and the modulation coefficient m=0.4 suddenly changes from external control to m=0.8.
Figure 5 shows the three-phase PWM on the input side of the inverter
Rectifier electrical quantity waveform, Figure 5 (a) is the three-phase grid voltage, Figure 5 (b) is the three-phase input current, Figure 5 (c) is the DC voltage on the DC side capacitor C, and Figure 5 (d) is the total distortion rate of the A-phase input current. Due to the use of SPWM, its THD is only slightly > 1%. It should be noted that these waveforms are unchanged in the two cases mentioned above.
Figure 6 shows the simulation results when the inverter output frequency is at 35 Hz and suddenly changes from external control to 15 Hz, and the modulation coefficient m remains unchanged. Figure 6(a) is the external control input signal, Figure 6(b) is the inverter output three-level AC A and B phase line voltages, Figure 6(c) is the filtered a, b, c three-phase phase voltages, Figure 6(d) is the filtered a, b phase line voltages and three-phase load currents, and Figure 6(e) is the total distortion rate THD of the load current. When the frequency is 35 Hz, THD is <2%, and it quickly rises to 9% when the frequency drops to 15 Hz.
Note that in the simulation, at t=0.05 s, the frequency changes suddenly.
Figure 7 shows the simulation results when the inverter output voltage is at 45 Hz and the modulation coefficient of the PWM generator changes suddenly from m=0.4 to 0.8.
Figure 7(a) is the external control signal of the PWM generator, and Figure 7(b) is the three-level square wave between the line voltages A and B output by the inverter.
As a result of the change, in fact, the density of the square wave changes before and after the change of m, but it is not clear here. Figure 7 (c) is the a, b, c phase voltage output to the load after filtering, and Figure 7 (d) is the three-phase load current ia, ib, ic and the load line voltage Uab after filtering. Figure 7 (e) is the total distortion rate THD of the load current, <1.5%.
During the entire simulation process, only components in Simulink's Sim Power Systems tool library were used. There is no need for programming, analysis, or calculation, which is very convenient.
Previous article:Flyback converter based on synchronous rectification technology
Next article:Single-chip synchronous step-down DC/DC converter reduces area by 60%
Recommended ReadingLatest update time:2024-11-16 22:02
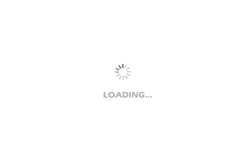
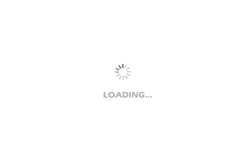
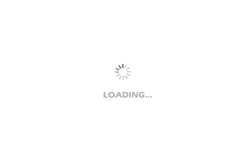
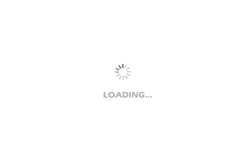
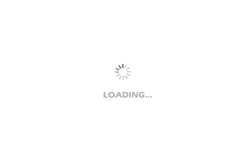
- Popular Resources
- Popular amplifiers
-
西门子S7-12001500 PLC SCL语言编程从入门到精通 (北岛李工)
-
Small AC Servo Motor Control Circuit Design (by Masaru Ishijima; translated by Xue Liang and Zhu Jianjun, by Masaru Ishijima, Xue Liang, and Zhu Jianjun)
-
Intelligent Control Technology of Permanent Magnet Synchronous Motor (Written by Wang Jun)
-
100 Examples of Microcontroller C Language Applications (with CD-ROM, 3rd Edition) (Wang Huiliang, Wang Dongfeng, Dong Guanqiang)
- MathWorks and NXP Collaborate to Launch Model-Based Design Toolbox for Battery Management Systems
- STMicroelectronics' advanced galvanically isolated gate driver STGAP3S provides flexible protection for IGBTs and SiC MOSFETs
- New diaphragm-free solid-state lithium battery technology is launched: the distance between the positive and negative electrodes is less than 0.000001 meters
- [“Source” Observe the Autumn Series] Application and testing of the next generation of semiconductor gallium oxide device photodetectors
- 采用自主设计封装,绝缘电阻显著提高!ROHM开发出更高电压xEV系统的SiC肖特基势垒二极管
- Will GaN replace SiC? PI's disruptive 1700V InnoMux2 is here to demonstrate
- From Isolation to the Third and a Half Generation: Understanding Naxinwei's Gate Driver IC in One Article
- The appeal of 48 V technology: importance, benefits and key factors in system-level applications
- Important breakthrough in recycling of used lithium-ion batteries
- Innolux's intelligent steer-by-wire solution makes cars smarter and safer
- 8051 MCU - Parity Check
- How to efficiently balance the sensitivity of tactile sensing interfaces
- What should I do if the servo motor shakes? What causes the servo motor to shake quickly?
- 【Brushless Motor】Analysis of three-phase BLDC motor and sharing of two popular development boards
- Midea Industrial Technology's subsidiaries Clou Electronics and Hekang New Energy jointly appeared at the Munich Battery Energy Storage Exhibition and Solar Energy Exhibition
- Guoxin Sichen | Application of ferroelectric memory PB85RS2MC in power battery management, with a capacity of 2M
- Analysis of common faults of frequency converter
- In a head-on competition with Qualcomm, what kind of cockpit products has Intel come up with?
- Dalian Rongke's all-vanadium liquid flow battery energy storage equipment industrialization project has entered the sprint stage before production
- Allegro MicroSystems Introduces Advanced Magnetic and Inductive Position Sensing Solutions at Electronica 2024
- Car key in the left hand, liveness detection radar in the right hand, UWB is imperative for cars!
- After a decade of rapid development, domestic CIS has entered the market
- Aegis Dagger Battery + Thor EM-i Super Hybrid, Geely New Energy has thrown out two "king bombs"
- A brief discussion on functional safety - fault, error, and failure
- In the smart car 2.0 cycle, these core industry chains are facing major opportunities!
- The United States and Japan are developing new batteries. CATL faces challenges? How should China's new energy battery industry respond?
- Murata launches high-precision 6-axis inertial sensor for automobiles
- Ford patents pre-charge alarm to help save costs and respond to emergencies
- New real-time microcontroller system from Texas Instruments enables smarter processing in automotive and industrial applications
- ABI Research: UWB device shipments will surge to 1.3 billion by 2026
- PWM port isolation driver from control chip to stepper motor
- Does anyone know the conversion formula for cc6903so-30a?
- STMicroelectronics' STM32MP1 is coming. What do you think of this chip?
- Component pad design, everything you don’t understand is here!
- 【EVK-NINA-B400 Evaluation Kit】+Development Environment
- Raspberry Pi mini TFT expansion PiTFT
- Serial line transmission distance
- C6678 SPI Flash boot failure
- Design of a USB reader based on embedded system