1 Introduction
As an energy storage component of electric vehicles, the power density, storage capacity, and safety of batteries not only determine the mileage and speed of electric vehicles, but also affect the service life and market prospects of electric vehicles. At present, the common problem of batteries in actual use is insufficient charge, and the mileage on a single charge is difficult to meet practical requirements.
In addition, using measurable battery parameters to make accurate and reliable estimates of the battery state of charge (SOC) has always been a research topic that electric vehicle and battery researchers have paid attention to and invested a lot of energy in. Therefore, it is necessary to establish a power battery test platform, use the platform to conduct comprehensive and accurate measurements of battery-related parameters, realize battery performance tests, work condition simulation and algorithm research, determine the most reasonable charging and discharging method and a more accurate SOC estimation method, so as to reasonably allocate and use the limited energy of the battery, extend the battery life as much as possible, and further reduce the vehicle cost of electric vehicles. Compared with previous battery test systems, this test platform can comprehensively monitor battery-related parameters and add the measurement of charging and discharging energy. It can describe the performance of the battery from the perspective of energy and analyze the battery efficiency from the perspective of energy state (SOE). The system hardware circuit has battery overvoltage, undervoltage protection and balancing functions, which can monitor and protect single cells and reduce the inconsistency between batteries. Establish communication between the charging and discharging equipment and the host computer, control the charger to change the control strategy and output current according to the programmed instructions, and examine the impact of the charging and discharging current size, method and environmental conditions on the battery charge and service life.
2 Test platform structure
The structure of the test platform is shown in Figure 1. The battery data acquisition system with the single chip as the core directly measures the single cell voltage, total voltage, temperature, current, charge and discharge capacity, charge and discharge energy and other information of the battery pack, and sends the data to the host computer through the RS232 bus. The host computer monitoring system composed of a microcomputer displays and records the received test data in real time, analyzes the data, and monitors the working status of the test system. In addition, according to the specific experimental requirements, the charging and discharging equipment can be controlled to output current according to the programming instructions to simulate the use of the battery under certain specific conditions. The charging and discharging equipment realizes the charging and discharging of the battery pack, completes the two-way flow of energy between the battery and the power grid, communicates with the monitoring PC through CAN, and can receive the programming control instructions of the monitoring PC. This paper mainly completes the design of the data acquisition system and the host computer monitoring system and realizes real-time communication between the various parts.
Figure 1 Platform structure diagram
3 System Hardware Design
The hardware structure of the data acquisition system is shown in Figure 2, which mainly includes the following modules: microcontroller, power module, current and ampere-hour detection module, watt-hour detection module, voltage detection module and communication interface circuit.
Figure 2 Hardware structure diagram
The microcontroller uses the MC9S12DT128B chip, which has rich peripheral resources such as serial interface and CAN controller. It only needs to add a level conversion circuit to realize 232 communication with the host computer. This design uses the digital temperature sensor DS18B20 to realize temperature detection. It supports 1-wire bus protocol and can use one port of the microcontroller to read the digital temperature information of multiple detection points, which is easy to expand.
The voltage detection uses the bq76PL536 chip, which detects 3 to 6 batteries at the same time, and the voltage range of a single battery is 1~5V.
The chip is directly powered by the measured battery, and the supply voltage range is 5.5~30V. In order to ensure that the chip can still work normally when the measured battery is less than 3 cells, a 9V DC power supply is connected to the circuit. When the total battery voltage is less than 9V, an external power supply is used. The chip has battery overvoltage and undervoltage protection functions, and the protection parameters such as voltage threshold and detection delay time can be written through the program. When the actual situation of a battery exceeds the set safety threshold range, the corresponding byte of the battery fault register in the chip is set, thereby notifying the charger to act to prevent the battery from being overcharged or over-discharged. On the periphery of the chip, there is a balancing circuit composed of MOS tubes and resistors. The CBx pin of the chip can control the conduction and shutdown of the MOS tube, as shown in Figure 3. Through software settings, when the program determines that a battery needs to be balanced, the CBx pin corresponding to the battery is set, and the MOS tube connected to CBx is turned on, and the balancing circuit is started.
Figure 3 Equalization circuit
The CS5460A chip can accurately detect and calculate active power, instantaneous power, IRM S and VRM S. This system uses two CS5460s to detect current, ampere-hours and watt-hours respectively. One CS5460 uses a voltage divider resistor to detect voltage and a shunt to detect current. Through software settings, it samples the voltage and current signals 4000 times per second and calculates the instantaneous power. Through the accumulation of 4000 times of power, the chip can calculate the energy value within this second, that is, watt-hours. The other CS5460 will measure the constant voltage source signal through the voltage measurement channel and the shunt signal through the current measurement channel. The measured value is the integral of current and time, that is, the unit of measurement of battery power, ampere-hours, which can be used for SOC calculation.
4 System Software Design
The data acquisition system software is divided into the main program, current detection and ampere-hour detection, watt-hour detection, voltage detection, temperature detection and RS232 program. After the system is powered on, the main program starts running. First, the system is initialized, then enters the main loop, and then cyclically calls other subroutine modules to complete the acquisition of various parameters, communication and other functions.
The host computer monitoring software is completed in the VC++6.0 programming environment. The entire application adopts a modular and structured mode: each program module is designed separately and then combined with a minimum interface. Control is clearly transferred from one program module to the next. The monitoring system includes:
Data display: Real-time display of the total battery voltage, single cell voltage, current, total charge and discharge capacity, total charge and discharge energy, temperature and other information detected by the battery data acquisition system, and store the received data in the access database in chronological order. Read the stored access library and display the data in the form of a list on the interface.
Parameter setting and calibration: After the data acquisition system is powered on, the battery information is modified or the chip is calibrated by software through the communication between the RS232 interface and the PC according to the pre-set communication protocol.
Data processing: Analyze the received voltage and temperature data, calculate the highest and lowest voltage/temperature, and their location information, and display them in real time.
In addition, the data acquisition system has realized the real-time calculation of battery capacity changes, but in actual applications, there is a cumulative error in SOC estimation through current integration, so it needs to be corrected regularly. In the host computer program, there is a reserved module to add code for SOC correction. When conducting SOC estimation experiments, SOC online estimation can be achieved based on the battery-related parameters received in real time and the correction method set in advance by the program.
Control of charging and discharging equipment: There is a reserved module in the host computer program for adding the control program of charging and discharging equipment, so that the battery voltage, temperature, charging and discharging capacity, charging and discharging energy and other related parameters can participate in the battery charging and discharging control and management. During the battery charging and discharging process, the host computer analyzes the received battery status and information, and determines whether all batteries in the battery pack are overcharged, over-discharged or over-temperatured. Since there is CAN communication between the charging and discharging equipment and the host computer, it will act in accordance with the program instructions of the host computer in a timely manner. This control mode can be conveniently used for the study of battery pack charging and discharging strategies. The host computer calculates the voltage and current control values of the charging and discharging equipment according to the pre-set control strategy, and sends them to the charging and discharging equipment to make it act. At the same time, this control mode can also simulate the actual operation of electric vehicles, improve the intelligence level of charging and discharging equipment, simplify the tedious work of charging staff to set charging parameters, and make the charger more adaptable. The charger only needs to receive the instructions provided by the host computer to achieve safe charging.
5 System Testing
In order to test the system, a 3.7V/80Ah lithium manganese oxide battery was used for constant current and constant voltage charging test. The following parameters were set in the host computer program: constant current stage charging current 80A, charging cut-off voltage 4.2V, constant voltage stage cut-off current 0.1A, and the obtained charging curve is shown in Figure 4.
Figure 4 Constant current and constant voltage charging curve
As can be seen from the figure, during constant current charging, the current value remains constant, the voltage rises steadily, and after reaching the cut-off voltage, the battery starts constant voltage charging, the voltage value is basically stable, and the current value gradually decreases to the cut-off current, achieving the control purpose. During the entire test process, the charger can act in a timely and accurate manner according to the programming instructions of the host computer. The system works stably, has good real-time performance, and high sampling accuracy. The maximum relative error of voltage measurement is 0.5%, the average error of current measurement is 0.41%, the temperature measurement error is 0.5%, and the measurement errors of ampere-hour and watt-hour are both within 0.5%, which meets the design requirements.
6 Conclusion
The test platform can accurately reflect the changes in battery status, provide data support for maximizing battery performance, improving battery efficiency, and realizing efficient use of battery capacity and energy, meeting the design requirements. The modular and structured advantages of the host computer monitoring program ensure the good functional scalability of the system, providing a reliable platform for performance testing, algorithm verification, and charging method research of power batteries, laying the foundation for the promotion and use of electric vehicles.
Previous article:Research on visual simulation of complex battlefield electromagnetic environment
Next article:Isolated low-side current monitor for negative high voltage rail
Recommended ReadingLatest update time:2024-11-16 15:41
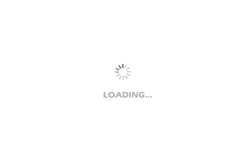
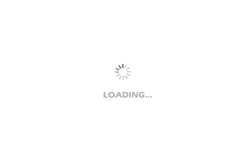
- Popular Resources
- Popular amplifiers
- MathWorks and NXP Collaborate to Launch Model-Based Design Toolbox for Battery Management Systems
- STMicroelectronics' advanced galvanically isolated gate driver STGAP3S provides flexible protection for IGBTs and SiC MOSFETs
- New diaphragm-free solid-state lithium battery technology is launched: the distance between the positive and negative electrodes is less than 0.000001 meters
- [“Source” Observe the Autumn Series] Application and testing of the next generation of semiconductor gallium oxide device photodetectors
- 采用自主设计封装,绝缘电阻显著提高!ROHM开发出更高电压xEV系统的SiC肖特基势垒二极管
- Will GaN replace SiC? PI's disruptive 1700V InnoMux2 is here to demonstrate
- From Isolation to the Third and a Half Generation: Understanding Naxinwei's Gate Driver IC in One Article
- The appeal of 48 V technology: importance, benefits and key factors in system-level applications
- Important breakthrough in recycling of used lithium-ion batteries
- Innolux's intelligent steer-by-wire solution makes cars smarter and safer
- 8051 MCU - Parity Check
- How to efficiently balance the sensitivity of tactile sensing interfaces
- What should I do if the servo motor shakes? What causes the servo motor to shake quickly?
- 【Brushless Motor】Analysis of three-phase BLDC motor and sharing of two popular development boards
- Midea Industrial Technology's subsidiaries Clou Electronics and Hekang New Energy jointly appeared at the Munich Battery Energy Storage Exhibition and Solar Energy Exhibition
- Guoxin Sichen | Application of ferroelectric memory PB85RS2MC in power battery management, with a capacity of 2M
- Analysis of common faults of frequency converter
- In a head-on competition with Qualcomm, what kind of cockpit products has Intel come up with?
- Dalian Rongke's all-vanadium liquid flow battery energy storage equipment industrialization project has entered the sprint stage before production
- Allegro MicroSystems Introduces Advanced Magnetic and Inductive Position Sensing Solutions at Electronica 2024
- Car key in the left hand, liveness detection radar in the right hand, UWB is imperative for cars!
- After a decade of rapid development, domestic CIS has entered the market
- Aegis Dagger Battery + Thor EM-i Super Hybrid, Geely New Energy has thrown out two "king bombs"
- A brief discussion on functional safety - fault, error, and failure
- In the smart car 2.0 cycle, these core industry chains are facing major opportunities!
- The United States and Japan are developing new batteries. CATL faces challenges? How should China's new energy battery industry respond?
- Murata launches high-precision 6-axis inertial sensor for automobiles
- Ford patents pre-charge alarm to help save costs and respond to emergencies
- New real-time microcontroller system from Texas Instruments enables smarter processing in automotive and industrial applications
- 【NXP Rapid IoT Review】+⑦NXP Rapid IoT Review Summary
- Fluke and universities jointly build laboratories
- Can CAN bus load resistors be 0603 package chip resistors?
- MicroPython driver porting of LIS2MDL magnetic field sensor
- IGBT DC voltage and current stabilizing power supply equipment solution requirements, seeking cooperation
- Watch the video, participate in the NXP quiz, and win wonderful gifts!
- [Analog Electronics Course Selection Test] + TI High Precision Laboratory
- Registration has ended | GigaDevice GD32E231 DIY Contest! 100 development boards free to try + great gifts!
- Things to note when measuring compressed air with vortex flowmeter
- Signal anti-reflection and impedance matching