Fluorescent lamps are popular all over the world as a soft and effective light source. They can be found wherever lighting is needed, whether in homes, shops, offices, schools, supermarkets, hospitals, theaters, commercial freezers, advertising light boxes, subways, pedestrian tunnels, civil air defense projects, night market lighting, etc.
The utilization rate of the power supply of traditional fluorescent lamps is not ideal: the additional ballast consumes a lot of power and needs auxiliary high voltage when turned on; the mercury inside the fluorescent tube cannot be handled when it is discarded, which becomes a public hazard to the environment. The fluorescent powder of the fluorescent tube contains a large amount of mercury during the filling process of the fluorescent tube. Therefore, after the fluorescent tube breaks, the mercury vapor that escapes is more harmful to the human body. Authoritative data shows that when the mercury vapor reaches 0.04 to 3 mg, it will cause chronic poisoning in people within 2 to 3 months, and when it reaches 1.2 to 8.5 mg, it will induce acute mercury poisoning. If the amount reaches 20 mg, it will directly cause the death of animals.
As the fourth generation of new energy-saving light sources, LED light sources were used as light sources for various lamps when they were born. 0.06W white light LED straw hat lamps and piranhas were the first to be used in LED fluorescent lamps. The number of LED fluorescent lamps used in each tube varies, about 280-360. Now the new generation of LED fluorescent lamps use SMD LED flat light sources ranging from 0.06W to 1W, with pure white, bluish white, warm white, and cold white colors .
Energy saving is the biggest feature of LED fluorescent lamps. Taking T8 fluorescent lamps as an example, the nominal 36W fluorescent lamp (CFL) consumes 8W of power with the additional ballast, and actually consumes 44W of power when working, with a luminous lumen of 420lm and a service life of 3,000 hours. The same specification LED fluorescent lamp actually consumes only 16W of power when working, with a luminous lumen of 550lm and a service life of up to 30,000 hours.
PWM LED driver Controller PT4107
LED light strips for LED fluorescent lamps Power supply Driver There are many solutions. Currently, non-isolated solutions are the mainstream due to their high efficiency, and the majority of them use PWM LED driver controllers as LED fluorescent lamp driver power supplies.
PT4107 is a typical PWM LED driver controller, and its internal topology is shown in Figure 1.
PT4107 is a high-voltage step-down PWM LED driver controller. Through external resistors and internal Zener diodes, the rectified 110V or 220V AC voltage can be clamped to 20V. When the voltage on Vin exceeds the undervoltage lockout threshold of 18V, the chip starts to work and drives the external MOSFET in the peak current control mode. A current sampling resistor is connected between the source terminal and ground of the external MOSFET, and the voltage on the resistor is directly transmitted to the CS terminal of the PT4107 chip. When the CS terminal voltage exceeds the internal current sampling threshold voltage, the drive signal at the GATE terminal is terminated and the external MOSFET is turned off. The threshold voltage can be set internally or controlled by applying a voltage to the LD terminal. If soft start is required, a capacitor can be connected in parallel to the LD terminal to obtain the required voltage rise speed and be consistent with the LED current rise speed.
The main technical features of PT4107: wide voltage input range from 18V to 450V, constant current output; frequency jitter is used to reduce electromagnetic interference, and random sources are used to modulate the oscillation frequency, which can expand the audio energy spectrum. The expanded energy spectrum can effectively reduce in-band electromagnetic interference and reduce the difficulty of system-level design; linear and PWM dimming are available, supporting hundreds of 0.06W LED drive applications, and the operating frequency is 25kHz-300kHz, which can be set by external resistors.
The PT4107 package is shown in Figure 2, and the functions of each pin are as follows:
1. GND chip ground terminal;
2. CS LED peak current sampling input terminal;
3. LD linear modulation optical access end;
4. RI oscillation resistor access terminal;
5. ROTP over temperature protection setting terminal;
6. PWMD PWM dimming and enable input terminal, there is a 100K pull-up resistor inside the chip;
7. VIN chip power supply terminal;
8. GATE drives the external MOSFET gate;
Design full voltage 20W fluorescent lamp switch constant current source
Taking AC 85V~245V full voltage input as an example, PT4107 PWM LED driver controller is used as the main chip of LED fluorescent lamp driver power supply to design a relatively ideal application circuit solution (Figure 3). The solution consists of anti-surge protection, EMC filtering, full-bridge rectification, passive power factor correction (PFC), buck regulator, PWM LED driver controller, and current expansion constant current circuit.
According to this concept, the schematic diagram of the full voltage 20W fluorescent lamp switch constant current source is shown in Figure 4. From the AC 220V, the AC mains inlet is connected to a 1A fuse FS1 and an anti-surge negative temperature coefficient thermistor NTC, followed by an EMI filter composed of L1, L2 and CX1. BD1 is a rectifier full bridge with 4 high-voltage silicon diodes inside. C1, C2, R1, D1~D3 form a passive power factor correction circuit. The PT4107 chip is powered by an electronic filter composed of T1, D4, C4, R2~R4, which is stepped down and stabilized. The input impedance of this filter is very high and the output impedance is very small. After rectification, the nearly 300V DC high voltage is stepped down by this transistor to provide a stable voltage of about 18~20V to the PT4107 Vin, ensuring that the chip works stably in the full voltage range.
This circuit does not consume energy and generate heat like the resistor step-down circuit in the previous scheme. The PWM control chip U1 (PT4107) and the power MOS tube Q1, the ballast power inductor L3, and the freewheeling diode D5 form a step-down voltage regulator circuit. U1 collects the peak current on the current sampling resistors R6~R9, and the internal logic controls the pulse duty cycle of the GATE pin signal in a single cycle for constant current control. The output constant current is combined with the freewheeling circuit of D5 and L3 to supply constant current to the LED light source. Changing the resistance value of resistors R6~R9 can change the output current of the entire circuit, but D5 and L3 must also be changed accordingly. R5 is part of the chip oscillation circuit, and changing it can adjust the oscillation frequency. The potentiometer RT is not used for dimming in this circuit, but is used to fine-tune the current of the constant current source so that the circuit reaches the designed power. Due to the dispersion of the device, the output current of each power board will be slightly different during mass production. This potentiometer can be used to adjust the output current of each power board on the production line. In order to ensure the stability of the adjusted power board, be sure to use a turbine and worm rod fine-tuning potentiometer and seal it with glue after adjustment.
The parameters of this circuit are designed based on 22 0.06W LEDs per string, 15 strings in parallel, driving 330 60mW white LED loads, the current of each string is 17.8mA, and the designed output is 36-80V/25OmA. If the number of LEDs is changed, the parameters of R6~R9 need to be modified.
The arrangement of PCB
boards is the key to making a good product, so the routing of PCB boards should be designed according to
the power electronics
specifications. This circuit can be used for T10 and T8 fluorescent tubes. Due to the different sizes of the spaces between the two tubes, the widths of the two PCB boards will be different. It is necessary to reduce the height of all parts to accommodate the T10 and T8 tubes. Figure 5 is a real photo of the T10 constant current source board. 33
components
are installed on a 235×25×0.8 mm epoxy single-sided printed board.
Key design and considerations
1. Surge-resistant NTC.
The surge-resistant NTC uses a 300Ω/0.3A thermistor. If the output of this solution is changed, such as increasing the current, the current of the NTC should also be larger to avoid overcurrent and self-heating.
2. EMC filtering
At the input end of the AC power supply, it is generally necessary to add a filter composed of a conjugate inductor, an X capacitor and a Y capacitor to increase the anti-EMI effect of the entire circuit and filter out the conducted interference signal and the radiated noise. This circuit adopts the simple method of conjugate inductor plus X capacitor, mainly for the consideration of overall cost, in line with the design principle of good enough. The X capacitor should be marked with the safety certification mark and the words AC275V withstand voltage. Its real DC withstand voltage is above 2,000V, and its appearance is mostly orange or blue. The conjugate inductor is two inductors with the same inductance wound on the same magnetic core. It is mainly used to suppress common mode interference. The inductance is selected in the range of 10 to 30mH. In order to reduce the volume and improve the filtering effect, it is preferred to use products made of high permeability microcrystalline material cores, and the inductance should be as large as possible. Using two identical inductors to replace one conjugate inductor is also a way to reduce costs.
3. Full-bridge rectifier
The full-bridge rectifier BD1 is mainly used for AC/DC conversion, so a safety margin of 1.5 is required. It is recommended to use 600V/1A.
4. Passive PFC
The output current of the ordinary bridge rectifier after rectification is pulsating DC, discontinuous current, large harmonic distortion, and low power factor. Therefore, it is necessary to add a low-cost passive power factor compensation circuit, as shown in Figure 6. This circuit is called a balanced half-bridge compensation circuit. C1 and D1 form one arm of the half bridge, C2 and D2 form the other arm of the half bridge, and D3 and R form a charging connection path. Compensation is performed using the valley filling principle. The filter capacitors C1 and C2 are connected in series, and the voltage on the capacitor is charged to half of the input voltage. Once the line voltage drops below half of the input voltage, the diodes D1 and D2 will be forward biased, causing C1 and C2 to start discharging in parallel. In this way, the conduction angle of the positive half-cycle input current increases from the original 75°~105° to 30°~150°; the conduction angle of the negative half-cycle input current increases from the original 255°~285° to 210°~330° (Figure 7). The resistor R in series with D3 helps to smooth the input current spikes and also improves the power factor by limiting the current flowing into capacitors C1 and C2. With this circuit, the system power factor is improved from 0.6 to 0.89. R has surge buffering and current limiting functions, so it should not be omitted.
5. Buck regulator circuit
The circuit that powers PT4107 is a capacitor-multiplied ripple filter (Figure 8), which has the dual functions of a capacitor-multiplied low-pass filter and a series voltage regulator. A capacitor C4 is connected from the base of the emitter output to the ground. Since the base current is only 1/(1+β) of the emitter current, it is equivalent to connecting a large capacitor with a capacitance of (1+β)C4 to the emitter. This is the principle of the capacitor-multiplied filter. If a Zener diode is connected between the base and the ground, it is a simple series voltage regulator. This circuit can effectively eliminate high-frequency switching ripples. Please note that T1 should be a bipolar transistor with a Vbceo of 500V and Ic = 100mA. The voltage regulator diode D4 should be a 20V, 1/4W low-power voltage regulator of any type.
6. Ballast power inductor
The ballast power inductor L3 and Q1 MOS tube, as well as the current sampling resistors in parallel with R6, R7, R8, and R9, are the three key components of the constant current output of this circuit. The ballast power inductor L3 requires high Q value, large saturation current, and small resistance. The nominal 3.9mH inductor should have a Q value greater than 90 in the frequency range of 40kHz to 100kHz. When designing, a power inductor with a saturation current twice the normal working current should be selected. This circuit is designed to output a current of 250mA, so 500mA is selected. The winding resistance of the power inductor should be less than 2Ω and the Curie temperature should be greater than 400 oC. High-quality power inductors. Once the inductor is saturated, the MOS tube, LED light source, and PWM control chip will burn out instantly. It is recommended to use a power inductor made of high-permeability microcrystalline material, which can ensure that the constant current source works safely and reliably for a long time.
The L3 inductor should be a closed magnetic circuit inductor with EE13 core, or a lower EPC13 core (Figure 9). Most LED fluorescent lamps now use half-aluminum and half- PV plastic tubes to help the LED light source dissipate heat. The magnetic circuit of the I-shaped core inductor is open. When the power driver board using the I-shaped core inductor enters the half-aluminum and half-PV plastic tube, the metal aluminum can change its magnetic circuit, which often reduces the output current of the debugged power driver board.
7. Freewheeling diode
The freewheeling diode D5 must be a fast recovery diode, which must keep up with the switching cycle of the MOS tube. If 1N4007 is used here, it will burn out during operation. In addition, the current passing through the freewheeling diode should be 1.5 to 2 times the load current of the LED light source. This circuit should use a 1A fast recovery diode.
8. PT4107 switching frequency setting
The switching frequency of PT4107 determines the size of power inductor L3 and input filter capacitors C1, C2, C3. If the switching frequency is high, smaller inductors and capacitors can be selected, but the switching loss of Q1 MOSFET will also increase, resulting in reduced efficiency. Therefore, for AC 220V power input, 50kHz~100kHz is more suitable. The calculation formula for PT4107 switching frequency setting resistor R5 is as follows. When F=50kHz, R5=500KΩ.
9. Selection of MOSFET
MOSFET tube Q1 is the key device of this circuit output. First of all, its RDS(ON) should be small, so that its power consumption is small when it is working. In addition, its withstand voltage should be high, so that it is not easy to be broken down when encountering high voltage surge during work.
During each switching process of the MOSFET, current spikes will inevitably appear on the sampling resistors R6~R9. To avoid this, a 400ns sampling delay time is set inside the chip. Therefore, the traditional RC filter can be omitted. During this delay time, the comparator will lose its function and cannot control the output of the GATE pin.
10. Current sampling resistor
Resistors R6, R7, R8, and R9 are connected in parallel as sampling resistors, which can reduce the influence of resistor accuracy and temperature on the output current, and can easily change the resistance value of one or several resistors to achieve the purpose of modifying the current. It is recommended to use SMD (1206) 1/4W resistors with a thousandth accuracy and a temperature coefficient of 50ppm. The total resistance setting and power selection of current sampling resistors R6 to R9 should be calculated based on the LED light source load current of the entire circuit.
R(6-9)=0.275/ILED
PR(6-9)=ILED2 x R(6-9)
11. Electrolytic capacitors
LED light source is a long-life light source with a theoretical life of up to 50,000 hours. However, unreasonable application circuit design, improper selection of circuit components, and poor heat dissipation of LED light sources will affect its service life. Especially in the drive power circuit , the electrolytic capacitor used as the output filter of the AC/DC rectifier bridge has a service life of less than 5,000 hours, which has become a stumbling block in the technology of manufacturing long-life LED lamps . This circuit design uses multiple aluminum electrolytic capacitors C1, C2, C4, C5, and C7. The life of aluminum electrolytic capacitors is also closely related to the ambient temperature. The loss of electrolyte accelerates with the increase of ambient temperature. The life of electrolytic capacitors will be reduced by half for every 6 oC increase in ambient temperature. The temperature inside the LED fluorescent tube is not easy to flow because of the difficulty of air flow. If the power drive board is not designed properly, the temperature inside the tube will be relatively high, and the life of the electrolytic capacitor will be greatly reduced. The use of solid electrolytic capacitors may be one of the good ways to extend the life, but it will lead to increased costs.
PT4107 can be used to design LED fluorescent lamp solutions with AC 110V or AC 220V input voltage of T10, T8, T5, and similar applications such as ceiling lamps , starry sky lamps, outdoor lighting work lamps, and bulb lamps, etc., with multiple 0.06W WLED light sources connected in series and parallel as loads. It can also be used to design LED garden lights, LED street lights , and LED tunnel lights with high- brightness 1W WLED light sources connected in series as loads .
In early 2009, the Japanese government forced enterprises to implement energy-saving and carbon-reduction policies to reduce carbon emissions from public lighting. The demand for energy-saving lighting in Japanese offices gradually increased, and LED fluorescent lamps were vigorously promoted, which promoted the production of LED fluorescent lamps in China. Therefore, the LED fluorescent lamp circuit suitable for AC110V has been widely used in production according to the optimized design of this circuit.
Previous article:LED Street Light Test Analysis Evaluation and Application Countermeasures
Next article:Analysis of the Dilemma Faced by the EMC Model of LED Street Lights Contract Energy Management
Recommended ReadingLatest update time:2024-11-16 15:35
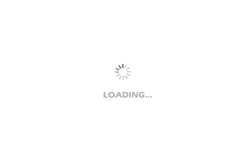
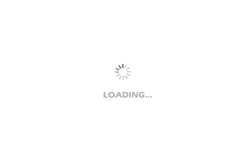
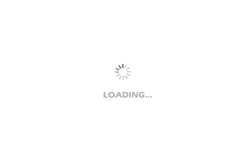
- Popular Resources
- Popular amplifiers
-
西门子S7-12001500 PLC SCL语言编程从入门到精通 (北岛李工)
-
Small AC Servo Motor Control Circuit Design (by Masaru Ishijima; translated by Xue Liang and Zhu Jianjun, by Masaru Ishijima, Xue Liang, and Zhu Jianjun)
-
Intelligent Control Technology of Permanent Magnet Synchronous Motor (Written by Wang Jun)
-
100 Examples of Microcontroller C Language Applications (with CD-ROM, 3rd Edition) (Wang Huiliang, Wang Dongfeng, Dong Guanqiang)
- MathWorks and NXP Collaborate to Launch Model-Based Design Toolbox for Battery Management Systems
- STMicroelectronics' advanced galvanically isolated gate driver STGAP3S provides flexible protection for IGBTs and SiC MOSFETs
- New diaphragm-free solid-state lithium battery technology is launched: the distance between the positive and negative electrodes is less than 0.000001 meters
- [“Source” Observe the Autumn Series] Application and testing of the next generation of semiconductor gallium oxide device photodetectors
- 采用自主设计封装,绝缘电阻显著提高!ROHM开发出更高电压xEV系统的SiC肖特基势垒二极管
- Will GaN replace SiC? PI's disruptive 1700V InnoMux2 is here to demonstrate
- From Isolation to the Third and a Half Generation: Understanding Naxinwei's Gate Driver IC in One Article
- The appeal of 48 V technology: importance, benefits and key factors in system-level applications
- Important breakthrough in recycling of used lithium-ion batteries
- Innolux's intelligent steer-by-wire solution makes cars smarter and safer
- 8051 MCU - Parity Check
- How to efficiently balance the sensitivity of tactile sensing interfaces
- What should I do if the servo motor shakes? What causes the servo motor to shake quickly?
- 【Brushless Motor】Analysis of three-phase BLDC motor and sharing of two popular development boards
- Midea Industrial Technology's subsidiaries Clou Electronics and Hekang New Energy jointly appeared at the Munich Battery Energy Storage Exhibition and Solar Energy Exhibition
- Guoxin Sichen | Application of ferroelectric memory PB85RS2MC in power battery management, with a capacity of 2M
- Analysis of common faults of frequency converter
- In a head-on competition with Qualcomm, what kind of cockpit products has Intel come up with?
- Dalian Rongke's all-vanadium liquid flow battery energy storage equipment industrialization project has entered the sprint stage before production
- Allegro MicroSystems Introduces Advanced Magnetic and Inductive Position Sensing Solutions at Electronica 2024
- Car key in the left hand, liveness detection radar in the right hand, UWB is imperative for cars!
- After a decade of rapid development, domestic CIS has entered the market
- Aegis Dagger Battery + Thor EM-i Super Hybrid, Geely New Energy has thrown out two "king bombs"
- A brief discussion on functional safety - fault, error, and failure
- In the smart car 2.0 cycle, these core industry chains are facing major opportunities!
- The United States and Japan are developing new batteries. CATL faces challenges? How should China's new energy battery industry respond?
- Murata launches high-precision 6-axis inertial sensor for automobiles
- Ford patents pre-charge alarm to help save costs and respond to emergencies
- New real-time microcontroller system from Texas Instruments enables smarter processing in automotive and industrial applications
- Try it, can you access this website of ST?
- I found the fish's partner - [Electronic Components Artwork]
- ESD protection and elimination methods in switching power supply design and production
- 【TI mmWave Radar Review】+3D Profile Test
- I thought it was washing the phone, but it turned out to be washing the phone
- Medium and low pressure MODS pipes
- EEWORLD University Hall----Live Replay: Microchip Security Series 14 - GoodLock with SAM L11 and TrustFLEX ATECC608 Security Devices
- 【ST NUCLEO-G071RB Review】_02_LED Light Experiment
- Help, MPU6050 freezes and no data output after running for a while
- TC58CVG0S3HxAIx Engineering Data Sheet