Induction heating Power supply is widely used in metal heat treatment, quenching, annealing, heat penetration, melting, welding, heat sleeve, semiconductor material refining, plastic heat sealing, baking and purification, etc.; it uses the induced current generated by the high-frequency magnetic field to cause the conductor to heat itself for heating. Compared with furnace heating, combustion heating or electric heating wire heating, induction heating has the advantages of significant energy saving, non-contact, fast speed, simple process, easy to realize automation and so on.
The induction heating power supply is mainly composed of four parts: the rectifier unit, the inverter unit, the resonant output unit, and the inductor. The rectifier unit converts the industrial frequency three-phase AC voltage into DC voltage; the inverter unit converts the electric energy into high-frequency electric energy of several thousand to hundreds of kilohertz; the resonant output unit is connected to the inverter at one end and the inductor at the other end. After isolation and impedance matching, a strong high-frequency current is generated in the inductor through resonance. When heating, the inductor induces a high-frequency current in the workpiece, so the conductor is quickly heated. In the early induction heating equipment, the high-frequency inverter device required by the inverter unit determined the form of the device, which has gone through the development process from electron tubes and thyristors to the currently commonly used IGBT .
Among the current mainstream IGBT induction heating products, there are still many differences in circuits and structures. From the perspective of the rectifier unit, there are controlled rectifiers and uncontrolled rectifiers; from the perspective of the inverter unit, there are pulse width modulation inverters and chopper voltage regulation inverters; from the perspective of the resonant output unit, there are parallel resonance and series resonance. Various circuits and structures have different performances in terms of efficiency, power factor, reliability, etc.
1 Common problems and causes of current products
Although great progress has been made in replacing thyristors and electron tubes with IGBTs, there are still some common problems in the induction heating power supply equipment developed and produced by most manufacturers. These problems are mainly manifested as follows:
a. Low efficiency, high power and cooling water consumption b. Power component IGBT is easily damaged c. Reactor or output transformer is easily damaged d. More cooling water circuit faults e. Low power factor, high harmonic pollution f. Poor equipment reliability and continuous operation performance These problems are mainly caused by design defects. Now we will discuss the reasons for these problems:
a Since IGBT, reactor, output transformer and resonant capacitor are all water-cooled, they not only have large losses, low efficiency and high cooling water consumption, but are also prone to burning of components due to scaling and clogging of copper tubes, and water leakage leading to the expansion of the fault range. Moreover, since there are many parallel branches in the water circuit, the system cannot guarantee that each branch has a water cut-off protection function.
b Since the analog control circuit cannot adapt to various changing working conditions, the power element IGBT will be out of the zero-crossing soft switching state, which will increase the switching loss and often cause the IGBT to overheat and be damaged.
c Pulse width modulation (no chopping voltage regulation) products use soft turn-on and hard turn-off (or hard turn-off with buffer) circuits, so the IGBT loss is large, and this method is easy to leave the soft switching state and cause IGBT damage.
d. When the equipment is over-voltage, over-loaded, short-circuited or partially short-circuited, or the power element is overheated, the control circuit cannot effectively limit and protect it, resulting in damage to the equipment.
e Equipment using parallel resonance is prone to inverter unit overvoltage and damage to the device.
f. The control circuit has poor anti-interference ability, the system operation is unstable or the protection limit function is prone to malfunction, and the equipment reliability is poor; or the equipment cannot automatically restart after being shut down due to external factors or accidental factors.
g After rectification, large-capacity power capacitors are used for filtering directly, without filtering inductors or IGBT chopper circuits on the DC side. Therefore, the power factor is low and the input current harmonics are large. If power electrolytic capacitors are used, there are also defects such as heating, series voltage balancing problems, and short life.
2 Main features of the new digital air-cooled induction heating power supply
The main circuit of an induction heating power supply with a new type of introduced technology is shown in the figure below. This product has an innovative full air-cooling structure. Under the digital control of the central processing unit DSP , the power device IGBT always works accurately in the zero-current switching state, and the automatic restart function ensures the reliability of continuous operation of the equipment. Compared with non-digital products, digital products have improved performance in all aspects.
The rectifier unit of this product is uncontrolled rectifier, and the DC side adopts IGBT chopper voltage regulation, and the resonance mode is output isolation type secondary series resonance. This circuit effectively improves the efficiency and power factor of the equipment, reduces input harmonics, and reduces IGBT losses; it allows the equipment to adopt a full air-cooling structure and eliminates equipment failures from the water system; based on this structure, the operating frequency of the equipment is 1KHz-100KHz.
2.1 Accurate and reliable zero-crossing soft-switching IGBT inverter
High-frequency induction heating power supplies generally use resonant soft switching control, which can greatly reduce IGBT switching losses and achieve automatic tracking of the resonant frequency.
Some products do not have an IGBT chopper circuit on the DC side. This is a soft-on hard-off circuit, or a hard-off circuit with buffering. This circuit has a large turn-off loss and is easy to leave the soft switching state. After using the DC-side IGBT chopper circuit, complete soft turn-on and soft turn-off can be achieved, and both turn-on and turn-off losses can be minimized.
The traditional control circuit uses a phase-locked loop to track the system resonant frequency. However, when the resonant frequency is high, the discrete parameters that affect the frequency tracking are more prominent. When the frequency is high, the phase-locked loop is not accurate enough and it is easy to be out of the soft switching state, so the switching loss increases, and in severe cases, the IGBT is damaged. Therefore, improving the accuracy of control is a prerequisite for ensuring the safe operation of the IGBT.
The new induction heating power supply uses DSP for tracking control. With the fast processing capability of DSP, it can perform tracking compensation according to different working conditions, greatly improving the accuracy of the system and greatly reducing the tracking error of the resonant frequency and phase. In addition, the fast IGBT drive circuit used in the system also helps to realize a more accurate and fast high-frequency soft switching circuit.
2.2 Full air cooling structure
Traditional water cooling equipment has two major defects: one is high loss and the other is easy to damage. Since the water cooling coil is wound with a copper tube, its eddy current loss is very large when running at high frequency, and the lost energy is carried away by the water, which reduces the efficiency of the system. In addition, the water cooling pipeline is prone to scale blockage and burnout of the device.
Based on accurate and reliable digital IGBT soft switching technology, the induction heating power supply adopts a fully air-cooled structure, which not only improves efficiency but also completely eliminates equipment failures from the water system.
This product is an output-isolated secondary series resonant. Output isolation is conducive to safe operation; due to the use of digital control, extremely low inverter DC components can be achieved, making it possible to adopt a secondary series resonant mode; the isolation transformer of the secondary series resonant only carries active power, and also adopts an air-cooled structure. The efficiency of the entire system from the input of the rectifier unit to the resonant output unit is higher than 95%. If the primary resonant belt is isolated by a transformer, the efficiency of the entire system is lower than 90% because the transformer carries 5-10 times the reactive power.
Air-cooled equipment has a longer lifespan than water-cooled equipment.
2.3 Uninterrupted operation
Digital products can take many measures to improve product reliability and reduce downtime; the most effective is the automatic restart function. After a shutdown due to external factors or accidental factors, the processor will automatically restart immediately after analysis. This has almost no effect on the heating of the workpiece, thus greatly improving equipment reliability.
For example, if the sensor cooling water pressure fluctuates and causes the equipment to shut down, the analog equipment can only wait for manual recovery and restart, while the digital induction heating power supply can restart immediately when the water pressure returns to normal and return to the original operating state.
2.4 Comprehensive restrictive protection measures
In induction heating equipment, due to the complex load conditions, perfect limiting protection measures are essential, but the limiting protection measures must not reduce the reliability of equipment operation.
Perfect limiting protection measures should be based on considerable anti-disturbance. When a larger disturbance occurs, the equipment starts the limiting program but continues to maintain safe operation. After the disturbance is eliminated, the equipment resumes normal operation. In this way, the equipment can operate continuously and uninterruptedly, and its reliability is greatly improved. Only when the equipment's tolerance is exceeded will the equipment be forced to exit operation for protection.
Digital products can easily achieve the above functions, but analog products cannot provide complete restriction protection due to their inability to perform calculations and judgments.
2.5 Enhancements
Due to the use of digital, the induction heating power supply can achieve many enhanced functions, such as:
a Multiple operating modes, built-in PID, constant temperature control can be achieved without other equipment
b. Multiple control modes, easy to realize remote control and automatic control
c Process curve programming function and automatic operation
d Automatic frequency tracking
3 Performance comparison of various types of induction heating power supply products
At present, the induction heating power supply mainly includes electron tube type, thyristor type, MOSFET type and IGBT type; and the IGBT type has the following mainstream products:
a Controllable voltage-regulating IGBT parallel resonant type (transformer isolated or non-isolated);
b Uncontrollable voltage-regulating IGBT parallel resonant type (transformer isolated or non-isolated);
c Pulse width modulation IGBT series resonant type (transformer isolation type);
d Chopper voltage regulation IGBT series resonant type (transformer isolation type);
Here only the various IGBT-type devices are compared with the new digital air-cooled devices.
4 Energy saving analysis
4.1 Energy-saving measures for induction heating systems
For an induction heating system, when considering energy saving, we should not only consider the induction heating power supply itself, but also consider whether the inductor structure and its matching are appropriate. However, the structure and design of the inductor have no direct relationship with the type of induction heating power supply adopted, but are mainly determined by the user's process requirements. Sometimes the energy saving effect obtained by optimizing the inductor design is far better than the energy saving effect of improving the efficiency of the induction heating power supply itself; or if the matching is not appropriate, the power loss is also very large. However, since the structure and design of the inductor are mainly determined by the user's process requirements, there are many variables, and it is difficult to quantitatively analyze its energy saving effect.
For the equipment itself, in addition to efficiency, power factor is also very important, because users need to pay not only for active power but also for reactive power. Moreover, the power factor drop caused by harmonics cannot be compensated by compensation capacitors.
In most cases, the equipment is not running at full power. If the actual operating power factor of a device is only 0.6, then it is obvious that the cost that the user needs to pay for reactive power will far exceed the cost of active power loss caused by equipment efficiency (according to power supply rules, when the power factor is higher than 0.85, there is no increase in electricity charges; when the power factor is 0.60, the monthly electricity charge will increase by 15%, and when it is lower than 0.60, for every 0.01 lower, the charge will increase by 2%, that is, if the power factor is 0.40, the monthly electricity charge will increase by 55%).
The figure shows the power factor of series resonant equipment and parallel resonant equipment under different loads (the power factor drop caused by harmonics is not taken into account).
In addition, for induction heating systems, the savings in cooling water are also considerable and should also be part of energy saving.
If tap water is used for cooling and discharged directly, the loss of water bills will be greater than the loss of electricity bills caused by equipment efficiency (equipment efficiency is calculated at 92%, and water flow is calculated at 50 liters per minute); if the user uses circulating water cooling or a closed water chiller, the electrical power required for water cooling and the electrical power of the water pump should still be included as part of the loss.
4.2 Series Induction Heating Power Supply Compared with Other Types of Induction Heating Power Supply
Taking the induction heating power supply with a power of 160KW as an example, the power consumption of the isolated controllable voltage-regulating IGBT parallel resonant type, the non-isolated uncontrollable voltage-regulating IGBT parallel resonant type, the pulse width modulation IGBT series resonant type, and the digital air-cooled IGBT series secondary resonant type induction heating power supply is compared. The average output power of the equipment is 120KW, the average working days per year are 300, the daily working hours are 8 hours, and the electricity fee is calculated at 0.80 yuan per kilowatt-hour:
5 Conclusion
a Traditional induction heating power supply products have defects such as large loss, high consumption of electricity and water, low power factor, frequent water system failures, and low operating reliability.
b. The new digital air-cooled induction heating power supply reduces system losses by adopting measures such as digital full air-cooling structure and IGBT soft switching, which not only improves efficiency but also eliminates system failures from the water system; by adopting DSP to achieve full digital control, it not only improves system tracking and control accuracy, but also improves system reliability and advancement; through the DC side IGBT chopper circuit structure, it not only realizes the zero-crossing turn-on and zero-crossing turn-off of the inverter IGBT, but also improves the power factor of the power supply.
Previous article:Considerations for PCB layout in switching power supplies
Next article:Design of Switching Power Supply Using Single Chip Microcomputer
Recommended ReadingLatest update time:2024-11-16 18:09
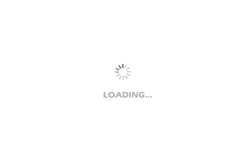
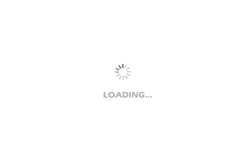
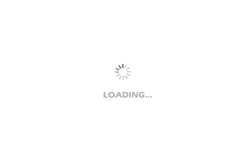
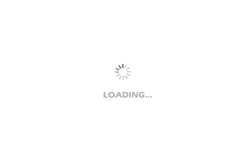
- Popular Resources
- Popular amplifiers
- MathWorks and NXP Collaborate to Launch Model-Based Design Toolbox for Battery Management Systems
- STMicroelectronics' advanced galvanically isolated gate driver STGAP3S provides flexible protection for IGBTs and SiC MOSFETs
- New diaphragm-free solid-state lithium battery technology is launched: the distance between the positive and negative electrodes is less than 0.000001 meters
- [“Source” Observe the Autumn Series] Application and testing of the next generation of semiconductor gallium oxide device photodetectors
- 采用自主设计封装,绝缘电阻显著提高!ROHM开发出更高电压xEV系统的SiC肖特基势垒二极管
- Will GaN replace SiC? PI's disruptive 1700V InnoMux2 is here to demonstrate
- From Isolation to the Third and a Half Generation: Understanding Naxinwei's Gate Driver IC in One Article
- The appeal of 48 V technology: importance, benefits and key factors in system-level applications
- Important breakthrough in recycling of used lithium-ion batteries
- Innolux's intelligent steer-by-wire solution makes cars smarter and safer
- 8051 MCU - Parity Check
- How to efficiently balance the sensitivity of tactile sensing interfaces
- What should I do if the servo motor shakes? What causes the servo motor to shake quickly?
- 【Brushless Motor】Analysis of three-phase BLDC motor and sharing of two popular development boards
- Midea Industrial Technology's subsidiaries Clou Electronics and Hekang New Energy jointly appeared at the Munich Battery Energy Storage Exhibition and Solar Energy Exhibition
- Guoxin Sichen | Application of ferroelectric memory PB85RS2MC in power battery management, with a capacity of 2M
- Analysis of common faults of frequency converter
- In a head-on competition with Qualcomm, what kind of cockpit products has Intel come up with?
- Dalian Rongke's all-vanadium liquid flow battery energy storage equipment industrialization project has entered the sprint stage before production
- Allegro MicroSystems Introduces Advanced Magnetic and Inductive Position Sensing Solutions at Electronica 2024
- Car key in the left hand, liveness detection radar in the right hand, UWB is imperative for cars!
- After a decade of rapid development, domestic CIS has entered the market
- Aegis Dagger Battery + Thor EM-i Super Hybrid, Geely New Energy has thrown out two "king bombs"
- A brief discussion on functional safety - fault, error, and failure
- In the smart car 2.0 cycle, these core industry chains are facing major opportunities!
- The United States and Japan are developing new batteries. CATL faces challenges? How should China's new energy battery industry respond?
- Murata launches high-precision 6-axis inertial sensor for automobiles
- Ford patents pre-charge alarm to help save costs and respond to emergencies
- New real-time microcontroller system from Texas Instruments enables smarter processing in automotive and industrial applications
- Sensor Basics and Common Terms
- Introduction to the basic knowledge of lithium batteries (PPT)
- EEWORLD University - Understanding PID Control (English subtitles)
- Live broadcast registration with prizes [Microchip Embedded Security Solutions | Automotive Network Security]
- sensor
- Canaan-K510 kit version network usage and current difficulties
- IAR Compilation Optimization Level Introduction
- Problem with peripheral clock enable statement
- Three-phase brushless DC motor control board
- Choosing the right ARM-based MCU