LED has become the most promising lighting source due to its advantages of no pollution, high efficiency, long life and small size. With the continuous development of power LED applications in the field of lighting, the requirements for miniaturization and high power of LED are becoming more and more urgent. The packaging structure with low thermal resistance, good heat dissipation and low stress is the technical key of power LED devices. Existing research results show that the bonding material has the greatest impact on the thermal resistance of LED packaging. The key to improving the heat dissipation capacity of power LED is to reduce the thermal resistance of the bonding layer. The thermal conductivity of the bonding material is low, and the contact thermal resistance between the materials after curing is very high, resulting in a large temperature gradient, which will generate a lot of thermal stress; in addition, the thermal expansion coefficient (CTE) between the bonding material and the chip and the heat sink is quite different, and when the expansion is subject to external constraints, it will also generate a large thermal stress. The thermal stress generated during the packaging process not only affects the physical stability of the LED device, but also changes the refractive index of the packaging silicone lens, thereby affecting the light output efficiency and light field distribution of the LED. The magnitude of thermal stress has become one of the main indicators of the reliability of low-cost power LEDs.
At present, relevant research on the thermal stress distribution of LEDs has been conducted at home and abroad. In 2006, Jianzhen Hu et al. conducted a finite element simulation of the thermal stress distribution of Ga-N-based LEDs. The results showed that the maximum thermal stress of the LED package was concentrated at the edge where the chip and the bonding layer contacted. In 2007, Yu Xingang et al. analyzed the influence of the thermal conductivity of the substrate material on the junction temperature and maximum thermal stress of the LED. In 2008, Dai Weifeng et al. used finite elements to simulate the changes in the transient temperature field and stress field of high-power LEDs. However, in the above studies, the temperature field and stress field of the LED were simulated and analyzed separately, without analyzing the corresponding change relationship between the temperature field and the stress field, nor analyzing the change trend of stress and strain. Moreover, from the perspective of public literature, no research has been found on the influence of the key factor of the bonding layer material on the stress field distribution of the LED.
Based on the thermal stress theory, the paper simulates the changes in the distribution of transient temperature and stress fields of LEDs, and compares them with the measured changes in the center temperature of the bottom of the LED substrate; analyzes the corresponding changes in the transient temperature field and stress field; simulates the influence of the thermal conductivity of the bonding layer material on the LED junction temperature and maximum equivalent stress; calculates the changing trends of thermal stress, strain and shear stress on the top surface of the substrate parallel to the X-axis path. The research in the paper is meaningful to the thermal design of LED packaging.
1 Theoretical model and physical model of thermal stress
According to heat transfer theory, the transient temperature field distribution of a high-power LED with an internal heat source should satisfy the following equation:
Where: T is temperature; t is time; x, y, z are three-dimensional coordinate systems; α is the thermal expansion coefficient, and α satisfies the equation:
Where: λ is the thermal conductivity, ρ is the density, and c is the specific heat capacity. According to the theory of thermoelasticity, the transient thermal stress generated when the thermal expansion caused by the temperature gradient of the LED is subject to external constraints satisfies the following equation:
Where: σ is thermal stress, α is thermal expansion coefficient, E is elastic modulus, T is temperature, and Tref is reference temperature. It can be seen from formula (3) that the temperature field inside the LED is the premise for determining the magnitude of thermal stress, and the temperature distribution is determined by the heat conduction differential equation (1). As long as the corresponding boundary conditions are given, the temperature field and stress field distribution can be obtained.
The Lumileds 1 W power LED device (as shown in Figure 1) is used as the research object. The LED consists of a lens, a chip, a bonding layer, a heat sink, a substrate, and a plastic package. The heat is conducted from the chip to the heat sink through the bonding layer, and finally dissipated by convection between the substrate and the air. The thermal performance parameters of various LED packaging materials are shown in Table 1.
Figure 1 Lumidleds 1 W LED model
Table 1 Thermodynamic parameters of LED packaging materials
2 Experimental, simulation results and analysis
The LED finite element model is established using free mesh, the heat source and bonding layer use the first-level mesh, and the rest use the sixth-level mesh. The chip input thermal power is calculated as 0.9 W at 90%, the ambient temperature is 25℃, the heat generation rate is 4.0×109 W/m3, the convection coefficient is loaded on the contact surface between the LED model and the air is 10 W/m2.℃, and the contact thermal resistance in each layer of material is ignored. The solution time is set to 600 s, and the time substep is 20 s. The finite element software ANSYS is used to solve equations (1) to (3) to obtain the transient temperature field distribution of Lumidleds 1 W LED.
2.1 LED transient temperature test experiment and simulation
In order to verify the reliability of finite element simulation, a set of experiments was designed to test the temperature of Lumidleds 1 W LED. The measuring point was the center of the bottom surface of the aluminum substrate. The given current was 350 mA, the voltage was 3 V, the temperature test time was 10 min, and the data was recorded every 10 s. The experimental results showed that after lighting for 8 minutes, the LED was basically in a thermal equilibrium state, and the center temperature of the substrate was 56°C. The simulation results showed that the LED junction temperature was 76.1°C at this time (as shown in Figure 2).
The temperature change curve of the substrate measurement point and the simulation results from the start of LED operation to steady state are shown in Figure 3. During the heating process, the measured results are slightly lower than the simulation results. After reaching steady state, the difference between the two is 2.9°C, which verifies the reliability of finite element analysis. The main reasons for the error are the error in material parameters, the neglect of thermal radiation in the simulation process, and the application of convection as a simple boundary condition.
Previous article:New Trend of LED Heat Dissipation─LED Silicon Substrate Package Thermal Conductivity
Next article:Detailed explanation of new dimming solution based on LED driver
Recommended ReadingLatest update time:2024-11-16 19:34
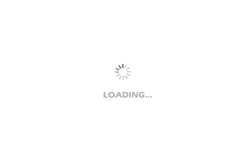
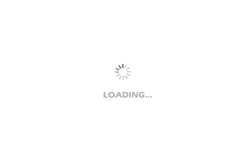
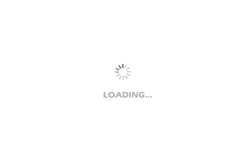
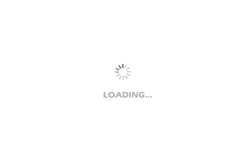
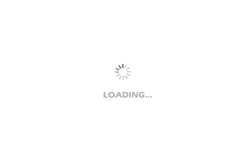
- Popular Resources
- Popular amplifiers
- MathWorks and NXP Collaborate to Launch Model-Based Design Toolbox for Battery Management Systems
- STMicroelectronics' advanced galvanically isolated gate driver STGAP3S provides flexible protection for IGBTs and SiC MOSFETs
- New diaphragm-free solid-state lithium battery technology is launched: the distance between the positive and negative electrodes is less than 0.000001 meters
- [“Source” Observe the Autumn Series] Application and testing of the next generation of semiconductor gallium oxide device photodetectors
- 采用自主设计封装,绝缘电阻显著提高!ROHM开发出更高电压xEV系统的SiC肖特基势垒二极管
- Will GaN replace SiC? PI's disruptive 1700V InnoMux2 is here to demonstrate
- From Isolation to the Third and a Half Generation: Understanding Naxinwei's Gate Driver IC in One Article
- The appeal of 48 V technology: importance, benefits and key factors in system-level applications
- Important breakthrough in recycling of used lithium-ion batteries
- Innolux's intelligent steer-by-wire solution makes cars smarter and safer
- 8051 MCU - Parity Check
- How to efficiently balance the sensitivity of tactile sensing interfaces
- What should I do if the servo motor shakes? What causes the servo motor to shake quickly?
- 【Brushless Motor】Analysis of three-phase BLDC motor and sharing of two popular development boards
- Midea Industrial Technology's subsidiaries Clou Electronics and Hekang New Energy jointly appeared at the Munich Battery Energy Storage Exhibition and Solar Energy Exhibition
- Guoxin Sichen | Application of ferroelectric memory PB85RS2MC in power battery management, with a capacity of 2M
- Analysis of common faults of frequency converter
- In a head-on competition with Qualcomm, what kind of cockpit products has Intel come up with?
- Dalian Rongke's all-vanadium liquid flow battery energy storage equipment industrialization project has entered the sprint stage before production
- Allegro MicroSystems Introduces Advanced Magnetic and Inductive Position Sensing Solutions at Electronica 2024
- Car key in the left hand, liveness detection radar in the right hand, UWB is imperative for cars!
- After a decade of rapid development, domestic CIS has entered the market
- Aegis Dagger Battery + Thor EM-i Super Hybrid, Geely New Energy has thrown out two "king bombs"
- A brief discussion on functional safety - fault, error, and failure
- In the smart car 2.0 cycle, these core industry chains are facing major opportunities!
- The United States and Japan are developing new batteries. CATL faces challenges? How should China's new energy battery industry respond?
- Murata launches high-precision 6-axis inertial sensor for automobiles
- Ford patents pre-charge alarm to help save costs and respond to emergencies
- New real-time microcontroller system from Texas Instruments enables smarter processing in automotive and industrial applications
- How is the current transformer used?
- Sensor Basics and Common Terms
- "Power supply obstacle" + voltage stress
- About LM2611
- STM32F767 fails to drive 7-inch screen
- EEWORLD University Hall----Analog Integrated Circuit Design Yang Qingyuan (National Chung Hsing University, Taiwan)
- Strange problem in high frequency control of PMOS field effect tube
- PCB tool ruler
- [National Technology N32G430] 01 Before the troops move, the food and grass must be prepared + Unboxing
- 【NUCLEO-WL55JC2 Review 6】 LoRa Point-to-Point Communication