The micro-power supply chips available on the market have the following control modes: PFM, PWM, cha rge pump, FPWM, PFM/PWM, pulse-skipPWM, digitalPWM. Among them, the most common ones are PFM, PWM, cha rge pump and PFM/PWM.
1. PFM is a technology that achieves voltage regulation output by adjusting the pulse frequency (i.e. the operating frequency of the switch tube). Its pulse width is fixed and the internal oscillation frequency is variable, so filtering is more difficult than PWM. However, PFM is limited by the output power and can only provide a small current. Therefore, PFM control can be used in situations where the output power requirement is low and the static power consumption is low.
2. The principle of PWM is that when the input voltage, internal parameters and external load change, the control circuit performs closed-loop feedback through the difference between the controlled signal and the reference signal, adjusts the conduction pulse width of the internal switch device of the integrated circuit, and stabilizes the output voltage or current and other controlled signals. The switching frequency of PWM is generally a constant value, so it is easier to filter. However, due to the influence of the error amplifier, the loop gain and response speed of PWM are limited, especially the low loop gain, which makes it difficult to use it for constant current driving of LEDs. Although many products currently use this solution, there is a common constant current problem. PWM control can be used in situations where a large output power and low output noise are required.
3. The charge pump solution uses discrete capacitors to send power from the input to the output, and no inductor is required in the entire process. The main disadvantage of the charge pump is that it can only provide a limited voltage output range (the output generally does not exceed 2 times the input voltage) because when multiple stages of the charge pump are cascaded, its efficiency drops significantly. When using a charge pump to drive more than one white light LED, a parallel drive method must be used, so it is only suitable for applications where the input and output voltages are not much different.
4. DigitalPWM (digital pulse width modulation) is used to monitor, control and manage the DC/DC load point power conversion through digital management of independent digital control loops and phases to provide a stable power supply and reduce the instability of the system caused by the voltage fluctuation of the traditional power supply module. In addition, DigitalPWM does not need to use traditional high-volume liquid capacitors for wave storage and filtering. DigitalPWM digital control technology can make the MOSFET tube run at a higher frequency, effectively alleviating the pressure on the capacitor. DigitalPWM is suitable for large current density and has a fast response speed, but the loop gain is still limited and the current cost is relatively high. Therefore, its application in LED constant current drive still needs further research.
5. FPWM (forced pulse width modulation) is a control method based on constant current output. Its working principle is that no matter how the output load changes, it always works at a fixed frequency. The high-side FET is turned on in a clock cycle, allowing current to flow through the inductor. The inductor current rises and generates a voltage drop through the inductor. This voltage drop is amplified by the current sensing amplifier. The voltage from the current sensing amplifier is added to the input of the PWM comparator and compared with the control end of the error amplifier. Once the current sensing signal reaches this control voltage, the PWM comparator will restart the logic drive circuit that turns off the high-side FET switch, and the low-side FET will turn on after a delay. When working under light load, in order to maintain a fixed frequency, the inductor current must flow through the low-side FET in the opposite direction. FPWM technology driver chips are currently only used by MAXIM and National Semiconductor chips.
As mentioned above, PFM and PWM use constant voltage drive mode to control LEDs, while FPWM and PFM/PWM are constant current drive mode control technologies, which have been proven to be more suitable for LED driving.
The IV0101/IV0102 boost converter chip recently launched by our company. Its control mode is an improved PFM/PWM control technology based on PFM. It is a control mode that organically combines PFM and PWM (not the switching between PFM and PWM). The input voltage determines the N switch tube opening time, and the output voltage and input voltage difference determines the synchronous tube opening time, instead of using the error amplifier feedback output to adjust the pulse width like PWM. Under certain load conditions, the switching frequency depends on the N tube opening time tN and the P tube opening time tP.
Among them, tP≧KP/(Vout-Vin); tN≦KN/Vin
. Under light load, the charging cycle continues at the maximum value tN. When the inductor current is zero and the synchronous rectifier is turned on, the chip works in discrete mode (DCM). When the load increases, the output quickly drops to the set point due to the large load. If the load current increases, the chip works in continuous mode (CCM), that is, there is always current flowing through the inductor. As long as the inductor current peak does not reach the maximum, the N tube opening time tN always remains at the set point. When charging ends and the discharge cycle begins, the switch tube current will reach the maximum. However, the full load is not reached yet, because after the minimum discharge time is over, the output is still adjustable. When the discharge time reaches the minimum value tP, the full load will be reached. Therefore, this control mode is to adjust the switching frequency by continuously adjusting the N-tube opening time tN and the P-tube opening time tP to ensure constant current output. Under the PWM control mode, in order to avoid system oscillation failure caused by parasitic inductance, the input capacitor Cin is generally connected. This chip does not connect the input capacitor at the power supply access end, thus eliminating the PCB board capacitor position, reducing the board area, and avoiding the surge pulse phenomenon generated by the capacitor during the PWM cycle, preventing the system performance from declining. Because it is a control method that organically combines PFM and PWM, it has a faster response speed of PFM and a very high loop gain and PWM large current output characteristics, which can be matched with PWM dimming to become an ideal small and medium power LED constant current driver chip.
Keywords:LED
Reference address:Analysis and comparison of different control modes of LED constant current drive
1. PFM is a technology that achieves voltage regulation output by adjusting the pulse frequency (i.e. the operating frequency of the switch tube). Its pulse width is fixed and the internal oscillation frequency is variable, so filtering is more difficult than PWM. However, PFM is limited by the output power and can only provide a small current. Therefore, PFM control can be used in situations where the output power requirement is low and the static power consumption is low.
2. The principle of PWM is that when the input voltage, internal parameters and external load change, the control circuit performs closed-loop feedback through the difference between the controlled signal and the reference signal, adjusts the conduction pulse width of the internal switch device of the integrated circuit, and stabilizes the output voltage or current and other controlled signals. The switching frequency of PWM is generally a constant value, so it is easier to filter. However, due to the influence of the error amplifier, the loop gain and response speed of PWM are limited, especially the low loop gain, which makes it difficult to use it for constant current driving of LEDs. Although many products currently use this solution, there is a common constant current problem. PWM control can be used in situations where a large output power and low output noise are required.
3. The charge pump solution uses discrete capacitors to send power from the input to the output, and no inductor is required in the entire process. The main disadvantage of the charge pump is that it can only provide a limited voltage output range (the output generally does not exceed 2 times the input voltage) because when multiple stages of the charge pump are cascaded, its efficiency drops significantly. When using a charge pump to drive more than one white light LED, a parallel drive method must be used, so it is only suitable for applications where the input and output voltages are not much different.
4. DigitalPWM (digital pulse width modulation) is used to monitor, control and manage the DC/DC load point power conversion through digital management of independent digital control loops and phases to provide a stable power supply and reduce the instability of the system caused by the voltage fluctuation of the traditional power supply module. In addition, DigitalPWM does not need to use traditional high-volume liquid capacitors for wave storage and filtering. DigitalPWM digital control technology can make the MOSFET tube run at a higher frequency, effectively alleviating the pressure on the capacitor. DigitalPWM is suitable for large current density and has a fast response speed, but the loop gain is still limited and the current cost is relatively high. Therefore, its application in LED constant current drive still needs further research.
5. FPWM (forced pulse width modulation) is a control method based on constant current output. Its working principle is that no matter how the output load changes, it always works at a fixed frequency. The high-side FET is turned on in a clock cycle, allowing current to flow through the inductor. The inductor current rises and generates a voltage drop through the inductor. This voltage drop is amplified by the current sensing amplifier. The voltage from the current sensing amplifier is added to the input of the PWM comparator and compared with the control end of the error amplifier. Once the current sensing signal reaches this control voltage, the PWM comparator will restart the logic drive circuit that turns off the high-side FET switch, and the low-side FET will turn on after a delay. When working under light load, in order to maintain a fixed frequency, the inductor current must flow through the low-side FET in the opposite direction. FPWM technology driver chips are currently only used by MAXIM and National Semiconductor chips.
As mentioned above, PFM and PWM use constant voltage drive mode to control LEDs, while FPWM and PFM/PWM are constant current drive mode control technologies, which have been proven to be more suitable for LED driving.
The IV0101/IV0102 boost converter chip recently launched by our company. Its control mode is an improved PFM/PWM control technology based on PFM. It is a control mode that organically combines PFM and PWM (not the switching between PFM and PWM). The input voltage determines the N switch tube opening time, and the output voltage and input voltage difference determines the synchronous tube opening time, instead of using the error amplifier feedback output to adjust the pulse width like PWM. Under certain load conditions, the switching frequency depends on the N tube opening time tN and the P tube opening time tP.
Among them, tP≧KP/(Vout-Vin); tN≦KN/Vin
. Under light load, the charging cycle continues at the maximum value tN. When the inductor current is zero and the synchronous rectifier is turned on, the chip works in discrete mode (DCM). When the load increases, the output quickly drops to the set point due to the large load. If the load current increases, the chip works in continuous mode (CCM), that is, there is always current flowing through the inductor. As long as the inductor current peak does not reach the maximum, the N tube opening time tN always remains at the set point. When charging ends and the discharge cycle begins, the switch tube current will reach the maximum. However, the full load is not reached yet, because after the minimum discharge time is over, the output is still adjustable. When the discharge time reaches the minimum value tP, the full load will be reached. Therefore, this control mode is to adjust the switching frequency by continuously adjusting the N-tube opening time tN and the P-tube opening time tP to ensure constant current output. Under the PWM control mode, in order to avoid system oscillation failure caused by parasitic inductance, the input capacitor Cin is generally connected. This chip does not connect the input capacitor at the power supply access end, thus eliminating the PCB board capacitor position, reducing the board area, and avoiding the surge pulse phenomenon generated by the capacitor during the PWM cycle, preventing the system performance from declining. Because it is a control method that organically combines PFM and PWM, it has a faster response speed of PFM and a very high loop gain and PWM large current output characteristics, which can be matched with PWM dimming to become an ideal small and medium power LED constant current driver chip.
Previous article:Analysis of the bottleneck of development in China's LED lighting technology field
Next article:Analysis of AC LED applications and development trends
Recommended ReadingLatest update time:2024-11-16 21:22
Analysis of radiation loss during LED use
Commonly used single chip system RAM test method
LED
is called the fourth generation lighting source or green light source. It has the characteristics of energy saving, environmental protection, long life and small size. It can be widely used in various indications, displays, decorations, backlight sourc
[Analog Electronics]
Use dual-color LED to indicate 10 states
Most devices that use a microcontroller have several operating states. These states are usually controlled by a pushbutton switch. To minimize cost, many designs use a single switch; the number of times the switch is pressed determines the state of the microcontroller. The circuit in this article uses a lighted LE
[Power Management]
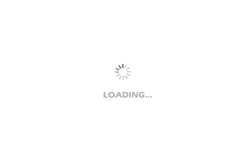
Osram launches new LED smart headlights with 1024 independently controllable pixels
Two years ago, OSRAM launched the world's first intelligent and controllable LED headlight Eviyos, which has a total of 1,024 independently controllable pixels that can automatically light up or turn off with extremely fine resolution according to traffic conditions. Once oncoming traffic is detected, the correspondin
[Embedded]
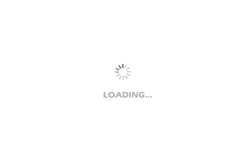
Application of high brightness LED in lighting
Since the birth of the first light-emitting diode in the 1960s, for a long time, LEDs were only used for signal indication purposes due to the limitation of output lumens. In the 1990s, blue light LEDs were commercialized due to a more economical implementation method. In the 21st century, high-power white light LED
[Power Management]
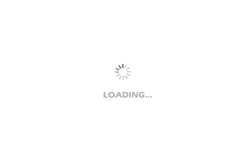
Analysis of high-power LED lighting solutions
The biggest design challenges currently faced by developers of high-power LED lighting solutions are heat dissipation design and overheat protection. They must overcome the problem that LED light sources are highly sensitive to heat, because excessive heat or improper application will greatly reduce the performance
[Power Management]
Interpretation of two major misunderstandings in LED lighting and its application fields
In recent years,
investment in
LED lighting
has been "hot" and even frenzied. Due to the "ruthlessness" of many problems in applications, people's minds have been forced to become clear, and the understanding of LED lighting has returned to a rational track, forcing some people with dizzy heads to start th
[Power Management]
Kongming LED lights create a new benchmark for environmental protection and energy saving
With the increasing exhaustion of global energy, the continuous rise in surface temperature, the frequent visits of severe weather, and the gradual strengthening of human awareness of energy conservation and environmental protection, the LED industry with the concept of energy conservation and environmental protecti
[Power Management]
Understand the differences between different LED driver power supplies in different applications in minutes
LED has been applied more and more widely due to its small size, low voltage, long service life, high brightness, low heat and environmental protection. If you don't understand different LED driver power supplies, it will seriously affect the service life and lighting of LED. In this article, I will introduce the diff
[Power Management]
- Popular Resources
- Popular amplifiers
Recommended Content
Latest Power Management Articles
- MathWorks and NXP Collaborate to Launch Model-Based Design Toolbox for Battery Management Systems
- STMicroelectronics' advanced galvanically isolated gate driver STGAP3S provides flexible protection for IGBTs and SiC MOSFETs
- New diaphragm-free solid-state lithium battery technology is launched: the distance between the positive and negative electrodes is less than 0.000001 meters
- [“Source” Observe the Autumn Series] Application and testing of the next generation of semiconductor gallium oxide device photodetectors
- 采用自主设计封装,绝缘电阻显著提高!ROHM开发出更高电压xEV系统的SiC肖特基势垒二极管
- Will GaN replace SiC? PI's disruptive 1700V InnoMux2 is here to demonstrate
- From Isolation to the Third and a Half Generation: Understanding Naxinwei's Gate Driver IC in One Article
- The appeal of 48 V technology: importance, benefits and key factors in system-level applications
- Important breakthrough in recycling of used lithium-ion batteries
MoreSelected Circuit Diagrams
MorePopular Articles
- Innolux's intelligent steer-by-wire solution makes cars smarter and safer
- 8051 MCU - Parity Check
- How to efficiently balance the sensitivity of tactile sensing interfaces
- What should I do if the servo motor shakes? What causes the servo motor to shake quickly?
- 【Brushless Motor】Analysis of three-phase BLDC motor and sharing of two popular development boards
- Midea Industrial Technology's subsidiaries Clou Electronics and Hekang New Energy jointly appeared at the Munich Battery Energy Storage Exhibition and Solar Energy Exhibition
- Guoxin Sichen | Application of ferroelectric memory PB85RS2MC in power battery management, with a capacity of 2M
- Analysis of common faults of frequency converter
- In a head-on competition with Qualcomm, what kind of cockpit products has Intel come up with?
- Dalian Rongke's all-vanadium liquid flow battery energy storage equipment industrialization project has entered the sprint stage before production
MoreDaily News
- Allegro MicroSystems Introduces Advanced Magnetic and Inductive Position Sensing Solutions at Electronica 2024
- Car key in the left hand, liveness detection radar in the right hand, UWB is imperative for cars!
- After a decade of rapid development, domestic CIS has entered the market
- Aegis Dagger Battery + Thor EM-i Super Hybrid, Geely New Energy has thrown out two "king bombs"
- A brief discussion on functional safety - fault, error, and failure
- In the smart car 2.0 cycle, these core industry chains are facing major opportunities!
- The United States and Japan are developing new batteries. CATL faces challenges? How should China's new energy battery industry respond?
- Murata launches high-precision 6-axis inertial sensor for automobiles
- Ford patents pre-charge alarm to help save costs and respond to emergencies
- New real-time microcontroller system from Texas Instruments enables smarter processing in automotive and industrial applications
Guess you like
- Application design using the FRAM-based MCU MSP430FR57xx series
- EEWORLD University Hall----Live Replay: AVNET uses MPLAB? Ecosystem and Curiosity Nano Development Board to create an innovative development workflow
- BleuNRG-1 one master and multiple slaves master module search interval setting
- How to use iic to make LCD screen display
- Design of MSP430 and MMC/SD card interface
- An Engineer's Guide to Temperature Sensing
- N ways to program the development board
- Analysis of Rectification Circuit and Filter Circuit
- Learn more about logic analyzers
- What is the status of lithium battery?