LED display is a high-tech engineering product that integrates electronics, electricity, computers, communications, information, image processing, optics, materials, structures and other multidisciplinary technologies. The relevant engineering and technical problems in any of these disciplines will affect the final operation effect of the entire display. A perfect LED display must be an organic combination of multidisciplinary technologies.
LED is the most important basic element of LED display. This article mainly briefly explains the causes of the brightness, consistency and failure of LED display, the relationship with LED and the effective measures for related improvements.
1. LED display brightness problem
LED brightness is an important determinant of display brightness. The higher the LED brightness, the greater the margin of current used, which is good for saving power and maintaining LED stability. LED has different angle values. When the chip brightness is fixed, the smaller the angle, the brighter the LED, but the smaller the viewing angle of the display. Generally, a 100-degree LED should be selected to ensure sufficient viewing angle of the display. For display screens with different dot spacing and different viewing distances, a balance should be found between brightness, angle and price.
The brightness of a single LED tube physically limits the maximum brightness of the screen, and the actual brightness is affected by the scanning method, signal lighting efficiency, color correction factors, etc. The maximum brightness of the LED display can be expressed as: Lm= (η*L* gmax)/S, where Lm is the actual required display brightness value, L is the brightness of the selected LED, η is the screen signal lighting efficiency, gmax is the color correction factor, and S is the system scanning method (1, 2... can be taken). When designing and applying full-color LED display screens, when selecting the brightness of a single primary color, we need to consider the white balance brightness of the three primary colors, and try to make the nominal values of the three primary colors close to 3:6:1 (red: green: blue).
Limited by semiconductor technology and packaging technology, the early LED lamps had low light efficiency and low luminous intensity of the red, green, and blue primary colors, so the low brightness value of the entire display was the main problem. Due to the low light efficiency of the lamp, in order to meet the brightness requirements of the display screen, the LED driving current setting value is generally high. The high current setting will inevitably lead to an increase in the working temperature of the LED, which will be detrimental to the long-term use of the display screen; by properly designing the pixel combination to improve the pixel brightness, such as using multiple LED lamps in series to increase the brightness value of a single primary color, thereby increasing the brightness of the LED display screen, it is a design method commonly used in previous engineering applications, but this will inevitably increase the cost of the entire display screen. With the development of LED chips and packaging technology, the light efficiency of LED lamps has been greatly improved, and it has been fully able to meet the brightness requirements of indoor and outdoor LED displays, and the working current of the LED can be set below the rated safe working current to ensure system reliability.
The LED display screen used outdoors should also be viewable in the sun, so the brightness must have a brightness difference (ratio) with the background. If the text is displayed, it can be 2:1, if it is an image, there is still a difference. Experience has shown that 10:1 is the minimum allowable limit, 20:1 is the standard, and it is hoped to be above 40:1. In a dark room, measure the brightness Lm of the maximum image signal input and the brightness Lb of a certain external light without signal, and then calculate the contrast V=(Lm+Lb)/Lb. In actual engineering, increasing the color depth of the mask, increasing the brim of the mask and the design of the reflective steps can effectively improve the contrast effect of the outdoor display.
The LED display dot matrix module drive is generally completed by a constant current driver chip. The chip includes a serial shift register, a serial-to-parallel conversion and a constant current driver. The functional circuit composition is shown in Figure 1. The constant current chip is a conversion device that converts the brightness signal of the controller into an appropriate drive current to drive the LED to emit light. The quality factor of the switch constant current of the constant current device will affect the effective brightness of the LED display. Especially when the refresh frequency and the number of gray levels of the display are higher, the constant current chip will more obviously affect the brightness of the entire display. As shown in Figure 1, the power supply voltage V-LED of the display will also be one of the important factors affecting the brightness. Especially when its voltage is lower than the normal conduction voltage of the LED, the LED luminous effect is affected, thereby affecting the brightness of the entire display.
Figure 1 LED static constant current drive circuit
In summary, in order to solve the brightness problem of display screen applications, we can take practical measures including: using high-brightness chips, selecting LED tubes with high light extraction rate, and designing to reserve enough margin in advance while ensuring the white balance brightness requirements; designing appropriate pixel combination to ensure the reasonable light output angle of the pixel points, and increase the visual contrast of the display screen through the reasonable arrangement and structural design of the lamps; selecting high-quality constant current driver chips, and designing reasonable drive current and voltage to ensure efficient LED driving.
Of course, ensuring efficient LED driving requires strong R&D and technical strength of enterprises. After the rapid development of the LED display industry in recent years, a group of excellent display screen applications and display light source packaging enterprises have also grown up. For example, the display light source packaging enterprise--Boshi, after several years of development and growth, now has its own display R&D laboratory, dedicated to the research of LED display technology, and has carried out a lot of technical research work on the application of LED display screens in conjunction with well-known domestic key scientific research institutes.
2. The problem of white balance consistency of LED display screens
LED display screens are composed of a large number of LED tubes, especially outdoor LED display screens using direct plug-in lamps. The problem of white balance consistency is quite common, which is a thorny problem often encountered in the industry.
The full-color display screen is composed of countless red, green and blue LED pixels. The brightness and wavelength consistency of each color LED determine the brightness consistency, white balance consistency and color consistency of the entire display screen. Generally speaking, display screen manufacturers require device suppliers to provide LEDs with a wavelength range of 5nm and a brightness range of 1:1.3. These indicators can be achieved by device suppliers through grading by spectrophotometers. Voltage consistency is generally not required. Generally speaking, the LED brightness difference is within the brightness range of 1:1.3, the red light wavelength difference is less than 5nm, and the blue-green wavelength difference is less than 3nm. The display screen composed of such lamps (the other conditions of the LED display screen are perfect) will have a very good white balance consistency. The display screen under the opposite conditions may have a flowery screen and poor consistency.
Since LEDs are angled, full-color LED displays also have angle directionality, that is, when viewed at different angles, their brightness will increase or decrease. In this way, the angle consistency of the red, green and blue LEDs will seriously affect the consistency of white balance at different angles, and directly affect the fidelity of the video color of the display screen. To achieve the matching consistency of the brightness changes of the red, green and blue LEDs at different angles, it is necessary to strictly carry out scientific design in the packaging lens design and raw material selection, which depends on the technical level of the packaging supplier. No matter how good the white balance of the normal direction of the display screen is, if the angle consistency of the LED is not good, the white balance effect of the whole screen at different angles will be poor. The angle consistency characteristics of LED devices can be measured by LED angle comprehensive tester, which is especially important for mid- and high-end display screens. The better the consistency of the light shape curve of the red, green and blue LEDs, the better the consistency of the entire display screen will be. Due to the uneven color caused by the inconsistent brightness of R/G/B at different angles, it is difficult to achieve white balance consistency at different angles; and the discrete distribution of the monochromatic light shape curve is serious, which will cause poor consistency of the display screen.
In actual production, the LED lights have different brightness. If the bright LEDs are concentrated in one module and the dark LEDs are concentrated in another module, the difference is obvious. Therefore, the mixed lamp process must be used in production to make the LED lights normally distributed on the display screen, so that the display consistency of the entire screen is better; if the direct plug-in lamp is not flat during installation, the light consistency of the LED lamp is poor, which will directly affect the consistency of the white balance of the display screen, so the "whole lamp process" must be added to ensure the flatness of the LED display screen.
As shown in Figure 1, the difference in the output current accuracy of the constant current chip and the difference in the accuracy of the adjustment resistor may affect the LED light-emitting effect, thereby affecting the consistency of the white balance of the display screen; the difference in the encoding of the signal system and the bandwidth of the signal transmission may also affect the consistency of the white balance of the LED display screen. In the design of the LED dot matrix module, the rationality of the combination and arrangement of the pixels may affect the light-emitting effect of the LED lamp and the optical superposition effect of the pixels, thereby affecting the consistency of the display screen; the rationality of the PCB layout and routing leads to differences in power supply and temperature distribution, which affects the consistency of the white balance of the display screen.
The optical parameters of the LED are closely related to the junction temperature of the pn junction. If the ambient temperature is high, the LED main wavelength or λp will drift to a longer wavelength, especially the temperature rise of dot matrix and large screen has a great impact on the reliability and stability of LED. The bandgap width value of the material in the light-emitting area of the LED device directly determines the wavelength or color of the device's light. The chip materials of LEDs such as InGaAlP and InGaN belong to III-V compound semiconductors. Their properties are similar to GaAs. When the temperature rises, the material bandgap will decrease, causing the device's light wavelength to become longer and the color to red shift. The wavelength changes with the junction temperature as: λ(T2)=λ(T1)+?T*K (nm/℃). Generally, K=0.1. Every time the junction temperature rises by 10 degrees, the wavelength drifts to a longer wavelength by 1nm, and the uniformity and consistency of the light emission deteriorate. The human eye can feel the wavelength change of 2~5nm. There are great differences in the sensitivity of the human eye to different colors. In the blue and green areas, very small wavelengths will cause changes in the human eye's perception, thus putting forward higher requirements for the temperature rise effect of blue-green LED devices.
In summary, in order to solve the problem of white balance consistency, we recommend the following measures:
1. For LED display products, it is important to use certain detection methods and means for the products. However, given the high value of the products and the fact that many defects cannot be solved through subsequent repairs, detection and inspection can provide a basis and direction for subsequent product improvements, but cannot change the defective products that have already been established. Therefore, prior control is particularly valuable. It can stably and effectively ensure the reasonable control of the entire process of LED packaging, including material grading control to ensure the consistency of brightness and wavelength; strict management of spectroscopic and color separation equipment, and dedicated personnel to operate the machines and workstations to ensure the consistency of various parameters of the products.
2. Strictly carry out scientific design in the design of packaging lenses and the selection of raw materials to achieve matching consistency of brightness changes of red, green and blue LEDs at different angles; in the design of LED display modules, reasonably select drive circuits and signal processing algorithms, and perform reasonable optimization design of PCB to ensure constant current accuracy and reduce the internal temperature difference of display module; adopt reasonable mixed lamp process control in the production of LED display modules.
3. Due to the differences in the pixel LEDs of the LED display, or after the electronic display has been working for a period of time, each LED will have different degrees of brightness and chromaticity decline, which seriously affects the display effect. The use of brightness and color correction control technology can achieve brightness <1%, chromaticity Cx/Cy <0.003 accuracy correction, quickly improve the display effect of the display, and make the updated module and the module that has been working for a period of time keep the same brightness and chromaticity. The dot correction calculation formula is:
Rout = Rin * A (1,1) + Grnin * A (1,2) + Bluin * A (1,3)
Gout = Rin * A (2,1) + Grnin * A (2,2) + Bluin * A (2,3)
Bout = Rin * A (3,1) + Grnin * A (3,2) + Bluin * A (3,3)
At present, a few domestic companies have established display R&D laboratories, and have conducted a lot of research on dot correction in conjunction with domestic universities and research institutes. The company where I work has already developed industry-leading dot correction technology to ensure the long-term and effective use of the display.
3. LED failure problem
LED is the most critical component of full-color LED display, which is equivalent to the CPU of a computer. The choice of LED has determined more than 50% of the quality of the entire display. If the LED is not selected well, no matter how good the other components of the display are, they cannot make up for the defects in the quality of the display. Since the full-color display is composed of tens of thousands or even hundreds of thousands of pixels composed of red, green and blue LEDs, the failure of any color LED will affect the overall visual effect of the display. Generally speaking, according to industry experience, the failure rate from the beginning of assembly of the LED display to aging for 72 hours before shipment should not be higher than 3/10,000 (referring to failure caused by the LED device itself).
LED failure generally includes the following three categories: short circuit (leakage), open circuit, and dim light. Short circuit (leakage) is generally caused by the excessive impact current in the module circuit, which causes the performance of the LED chip to change and the leakage current of the chip to increase; open circuit may cause static electricity or other reasons to cause the LED chip to be broken down; dim light is generally due to improper use of LED, which causes water vapor to enter the colloid, affecting the optical effect of the LED.
For LED failure issues. First of all, starting from the application design, it is necessary to select the appropriate circuit, reduce the threat of static electricity from the circuit interface, prevent the working state of the LED from being damaged by large current pulses, and design a reasonable structure to protect the sealed LED to prevent the possibility of external force pulling the LED tube legs.
Secondly, pay attention to the details of the reasonable use of LEDs in production: pay attention to the reasonable control of the use of materials, and make sure to do moisture-proof process treatment for expired materials; pay attention to the strict control of anti-static measures. The display assembly factory should have good anti-static measures, special anti-static ground, anti-static floor, anti-static soldering iron, anti-static mat, anti-static ring, anti-static clothing, humidity control, equipment grounding (especially foot cutting machine), etc. are all basic requirements, and they should be regularly tested with an electrostatic meter; the temperature and furnace time of wave front soldering must be strictly controlled. It is recommended that the preheating temperature is 100℃±5℃, the maximum does not exceed 120℃, and the preheating temperature rise is required to be stable, the welding temperature is 245℃±5℃, and the welding time is recommended to be no more than 3 seconds. After the furnace, avoid vibration or impact on the LED until it returns to normal temperature.
The temperature parameters of the wave soldering machine should be checked regularly, which is determined by the characteristics of the LED. Overheating or fluctuating temperatures will directly damage the LED or cause quality risks for the LED, especially for small-sized round and oval LEDs such as 3mm. When the LED display screen does not light up, there is often a probability of more than 50% that it is caused by various types of cold soldering, such as cold soldering of LED pins, cold soldering of IC pins, cold soldering of pin headers and mother headers. The improvement of these problems requires strict improvement of the process and strengthening of quality inspection to solve them. High temperature and room temperature aging tests and vibration tests before leaving the factory are also a good inspection method. The
effective control of LED product failure problems is an important link that needs to be paid attention to in packaging, display design, production and display engineering. The effective guarantee of these links requires our industry to breed more excellent companies such as Boshi, Guoxing, Leman, and Leyard, implement a more stringent quality management system, and monitor the quality of products from the entire process of design, procurement, production, quality inspection, packaging, transportation, pre-sales and after-sales tracking to ensure "zero defects in quality service" of products and promote the healthy and orderly growth of the entire industry.
Previous article:Discussion on the rationality of low gray signal ignition conditions for LED display screen
Next article:Design of LED rotating screen based on ATmega16L chip
Recommended ReadingLatest update time:2024-11-16 21:36
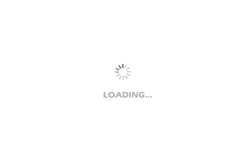
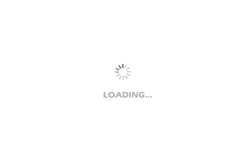
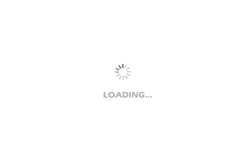
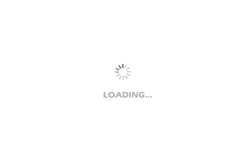
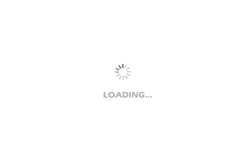
- Popular Resources
- Popular amplifiers
- MathWorks and NXP Collaborate to Launch Model-Based Design Toolbox for Battery Management Systems
- STMicroelectronics' advanced galvanically isolated gate driver STGAP3S provides flexible protection for IGBTs and SiC MOSFETs
- New diaphragm-free solid-state lithium battery technology is launched: the distance between the positive and negative electrodes is less than 0.000001 meters
- [“Source” Observe the Autumn Series] Application and testing of the next generation of semiconductor gallium oxide device photodetectors
- 采用自主设计封装,绝缘电阻显著提高!ROHM开发出更高电压xEV系统的SiC肖特基势垒二极管
- Will GaN replace SiC? PI's disruptive 1700V InnoMux2 is here to demonstrate
- From Isolation to the Third and a Half Generation: Understanding Naxinwei's Gate Driver IC in One Article
- The appeal of 48 V technology: importance, benefits and key factors in system-level applications
- Important breakthrough in recycling of used lithium-ion batteries
- Innolux's intelligent steer-by-wire solution makes cars smarter and safer
- 8051 MCU - Parity Check
- How to efficiently balance the sensitivity of tactile sensing interfaces
- What should I do if the servo motor shakes? What causes the servo motor to shake quickly?
- 【Brushless Motor】Analysis of three-phase BLDC motor and sharing of two popular development boards
- Midea Industrial Technology's subsidiaries Clou Electronics and Hekang New Energy jointly appeared at the Munich Battery Energy Storage Exhibition and Solar Energy Exhibition
- Guoxin Sichen | Application of ferroelectric memory PB85RS2MC in power battery management, with a capacity of 2M
- Analysis of common faults of frequency converter
- In a head-on competition with Qualcomm, what kind of cockpit products has Intel come up with?
- Dalian Rongke's all-vanadium liquid flow battery energy storage equipment industrialization project has entered the sprint stage before production
- Allegro MicroSystems Introduces Advanced Magnetic and Inductive Position Sensing Solutions at Electronica 2024
- Car key in the left hand, liveness detection radar in the right hand, UWB is imperative for cars!
- After a decade of rapid development, domestic CIS has entered the market
- Aegis Dagger Battery + Thor EM-i Super Hybrid, Geely New Energy has thrown out two "king bombs"
- A brief discussion on functional safety - fault, error, and failure
- In the smart car 2.0 cycle, these core industry chains are facing major opportunities!
- The United States and Japan are developing new batteries. CATL faces challenges? How should China's new energy battery industry respond?
- Murata launches high-precision 6-axis inertial sensor for automobiles
- Ford patents pre-charge alarm to help save costs and respond to emergencies
- New real-time microcontroller system from Texas Instruments enables smarter processing in automotive and industrial applications
- When using ALTium Designer to edit the PCB library, the pads placed are invisible. I don't know why.
- [Serial server rs485 communication experience tutorial] Storage gateway working mode
- 【GD32F310G-START】Solve Error: Device not found and turn on the LED light
- [National Technology N32G457 Review] Install RT-Thread Studio
- FPGA chip power backflow problem
- Visit the MPS Core Cloud Exhibition Hall online to learn about the latest technologies and win gifts by simply passing levels!
- Real-time Signal Analyzer Based on TMS320VC5509A
- Case Study - Self-Powered Environmental Sensors for IoT Systems Using Energy Harvesting Technology
- Unable to start automatically
- Get it for free|Explore the NXP i.MX RT1020 evaluation kit worth 500 yuan