The shooting range undertakes the test tasks such as weapon equipment development, design finalization, etc. For a long time, due to the restrictions and influence of many factors such as the system, technology, design and use purpose of the weapon system development department, the test equipment is generally designed for the specific model of the weapon system being tested, resulting in poor versatility and difficulty in upgrading
and transformation. The system hardware is based on virtual instrument technology and modular design for the form of the tested signal, and the software is designed based on database technology. When applied, according to the specific conditions such as the type and scale of the tested signal, by combining and configuring the collector hardware and software modules, a special test system with different functions and different scales can be formed. When its function cannot meet the test requirements, it only needs to add hardware and software modules according to the requirements, and the main body of the equipment can remain unchanged or only be modified to meet the test needs of other types of weapon systems.
1 Hardware composition and function
The shipborne weapon test system is designed based on the PXI bus module. The system consists of four parts: the main controller, the collector, the signal pickup/conditioning equipment and the signal simulator. Its composition is shown in Figure 1.
(1) Main controller
The main controller consists of an industrial computer system configured with a PXI-PCI8335 external controller module (MXI-3) and a GPS timing card. The industrial computer is responsible for system management and the collection, storage and processing of data collected by the collector. The MXI-3 module is used by the industrial computer to control each collector. The GPS timing card adopts a PCI bus plug-in card structure and can receive GPS satellite time information or target range IRIG-B code time information to achieve synchronization between the system and the target range measurement and control network. By processing GPS or IRIG-B time information, 1 PPS, 20 PPS interrupt signals and parallel hour, minute, second, and millisecond time information can be obtained on the PCI bus, and 1 PPS and 20 PPS synchronization signals of TTL level can be output.
(2) Collector The
collector consists of three electrical signal collectors (1#, 2#, and 3# collectors) and a non-electrical quantity measurement subsystem (4# collector). The electrical signals to be tested mainly include DC voltage signals, control command signals, pulse frequency signals and various digital signals (serial, parallel and network information). Non-electrical parameters mainly include temperature, angular velocity, vibration, pressure and strain signals.
The three electrical signal collectors are composed of PXI-1006 chassis and PXI bus modules, and the connection between collectors is realized by the PXI-PXI bridge of the PXI-1006 chassis. The PXI bus modules include NI's PXI-6608 counter/timer module, PXI-6031E data acquisition module, PXI-1411 image signal acquisition module, PXI-6533 digital I/O module, PXI-8422 RS 232 interface module, PXI-8423 RS 422/485 interface module, PXI-8210 Ethernet interface module and PXI-8460 CAN bus module.
The specific configuration of each PXI collector can be determined according to the type and quantity of the tested signals and the physical location of the system under test. In specific applications, the functions of each collector can be flexibly configured according to the different test objects. [page]
(3) Signal pickup/conditioning equipment
Signal pickup/conditioning equipment is used to complete the pickup and conditioning of the measured signal. In order to facilitate the connection with the measured device; a cable transfer box is required.
(4) Signal simulator
The signal simulator consists of an industrial control computer system and a variety of measured signal simulation cards, which are used to simulate/emulate the measured signal.
2 Software design
2.1 Design ideas
For modern computer test systems, software is the soul of the system. For simple test systems, due to the single test task and dedicated hardware system, the relevant configuration can be completed uniformly during software design. Since the amount of test result data is relatively small and data processing and output are simple, it is the best choice to complete the entire test task as a whole at one time.
For the integrated test system, due to its large scale and the requirement for good flexibility, the above software design method is obviously inappropriate. If the system is regarded as a task, it is difficult to achieve scientific management of many system hardware modules and a large amount of test data.
The use of database technology can realize the orderly management of test tasks, test instruments, system configuration, and test data in the integrated test system. The system database includes the system task library, the system instrument library, the channel configuration and channel calibration database, and the test database. The
test task library is designed for organizing and managing test tasks. It defines the task name and task code, and also includes a description of the task and the corresponding help file. The task code is designed to be a unique feature code to distinguish the task, and it is used as a token for the test system to execute the task. The system instrument library stores all the instruments or hardware modules included in the test system, which is the basis for defining a dedicated test system. The system channel library includes the system channel configuration library and the calibration database corresponding to each channel. The channel configuration library is responsible for managing the channel configuration of all test tasks. It describes and defines the channels used by each test task. The calibration database is used to save the calibration data of the corresponding channel, so that the data obtained during the test execution corresponds to the actual physical quantity. In order to manage the test data scientifically and orderly and reproduce the test site, the test information, test data and intermediate data generated during the data editing and data output process related to the test site should be saved. For this purpose, the system software should establish a test database.
2.2 Software Development Environment
The system uses the Windows XP operating system and uses LabVIEW 8 to write applications. The database management software is programmed in Visual C++6.0 to implement the storage, query, retrieval and playback of system configuration, test data and other information.
2.3 Software Structure and Application Software Functions
2.3.1 Software Structure
The test system software consists of four parts: instrument driver layer, I/O interface layer, test management layer and test program layer.
The instrument driver software is the software that performs communication and control on the instrument hardware. The software is a set of relatively abstract operation functions provided by the instrument standard parts manufacturer for the low-level operation of the instrument hardware, including initialization, configuration, action/status, data, utility and shutdown functions.
I/O interface software is a low-level communication protocol between a computer and the hardware or functional modules of a collector instrument.
Test management software is a software package used to manage and execute a certain test task. It includes functions such as realizing human-computer dialogue, data collection of collectors, data processing, data exchange, performance evaluation of the system under test, simulation/emulation of the signal under test and target indication information, and database management.
The test program is used to implement specific test functions of each collector. The test program is directly oriented to specific test tasks. It is a data acquisition program for specific applications generated by reconstructing the collector device layer components according to the requirements of the test task.
2.3.2 Application software functions
The system application software includes channel configuration and calibration, GPS/IRIG-B code time information collection, test execution (data collection), data processing (including performance evaluation of the system under test), data exchange, simulation/emulation of the signal under test, and other functional modules. The database includes system task DB, system instrument and hardware module DB, channel configuration DB, channel calibration DB, communication interface parameter DB, and test data DB. The software structure is shown in Figure 2.
(1) Channel configuration and calibration module. Initialize the required hardware modules for each specific test task to form a dedicated test system. After the dedicated test system is constructed, calibrate the system hardware modules and set the parameters of the collector communication interface.
When the collector chassis does not have the hardware modules required for the task, first complete the configuration of the required hardware modules manually.
(2) GPS/IRIG-B code time information acquisition module. This module is used to collect satellite time or range time information, thereby achieving synchronization between the system and the range measurement and control network. (3
) Data acquisition module. Complete the data acquisition of the current specific test task. Its execution subject is the dedicated test system defined during system configuration and calibration. In addition to the original test data, the collected data also includes relevant information such as system configuration and calibration, test date and flight number, so as to be used when analyzing the test results.
(4) Data processing module. Complete the playback, editing, and dimension conversion of test data. When the system is connected to the range measurement and control network, it can also process the test data in real time. Combined with the tactical and technical indicators of the test system, the test results can be analyzed and evaluated.
(5) Data exchange module. Completes the sending of test data or the receiving of range control network data. This includes sending the original test data of the shipborne weapon system to the range control network (in real time or after the fact), receiving the target true value data provided by the range control network, the carrier attitude, speed and position and other test data of the participating equipment.
(6) Signal simulation/emulation module. Simulates the test signal for system debugging or mission preparation. Simulates the air or sea target information and plays it back to the weapon system for weapon system debugging and ship sailor training.
(7) Database management module. Independent of the system application software, it is mainly used for the management of the system database.
3 Conclusion
The system is based on NI's multi-chassis solution to form a distributed test system. The hardware is based on virtual instrument technology and adopts modular design for the form of the test signal. The software is based on LabVIEW language and database technology. This design provides a guarantee for the further expansion of system functions, achieving the purpose of adapting to different test requirements and improving system performance and its versatility.
Previous article:Research on GPS nonlinear dynamic filtering based on WLS-KF
Next article:Comparison of architecture-based and process-based DFT testing approaches
Recommended ReadingLatest update time:2024-11-16 17:56
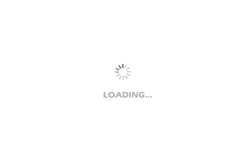
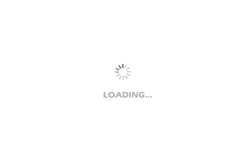
- Keysight Technologies Helps Samsung Electronics Successfully Validate FiRa® 2.0 Safe Distance Measurement Test Case
- From probes to power supplies, Tektronix is leading the way in comprehensive innovation in power electronics testing
- Seizing the Opportunities in the Chinese Application Market: NI's Challenges and Answers
- Tektronix Launches Breakthrough Power Measurement Tools to Accelerate Innovation as Global Electrification Accelerates
- Not all oscilloscopes are created equal: Why ADCs and low noise floor matter
- Enable TekHSI high-speed interface function to accelerate the remote transmission of waveform data
- How to measure the quality of soft start thyristor
- How to use a multimeter to judge whether a soft starter is good or bad
- What are the advantages and disadvantages of non-contact temperature sensors?
- Innolux's intelligent steer-by-wire solution makes cars smarter and safer
- 8051 MCU - Parity Check
- How to efficiently balance the sensitivity of tactile sensing interfaces
- What should I do if the servo motor shakes? What causes the servo motor to shake quickly?
- 【Brushless Motor】Analysis of three-phase BLDC motor and sharing of two popular development boards
- Midea Industrial Technology's subsidiaries Clou Electronics and Hekang New Energy jointly appeared at the Munich Battery Energy Storage Exhibition and Solar Energy Exhibition
- Guoxin Sichen | Application of ferroelectric memory PB85RS2MC in power battery management, with a capacity of 2M
- Analysis of common faults of frequency converter
- In a head-on competition with Qualcomm, what kind of cockpit products has Intel come up with?
- Dalian Rongke's all-vanadium liquid flow battery energy storage equipment industrialization project has entered the sprint stage before production
- Allegro MicroSystems Introduces Advanced Magnetic and Inductive Position Sensing Solutions at Electronica 2024
- Car key in the left hand, liveness detection radar in the right hand, UWB is imperative for cars!
- After a decade of rapid development, domestic CIS has entered the market
- Aegis Dagger Battery + Thor EM-i Super Hybrid, Geely New Energy has thrown out two "king bombs"
- A brief discussion on functional safety - fault, error, and failure
- In the smart car 2.0 cycle, these core industry chains are facing major opportunities!
- The United States and Japan are developing new batteries. CATL faces challenges? How should China's new energy battery industry respond?
- Murata launches high-precision 6-axis inertial sensor for automobiles
- Ford patents pre-charge alarm to help save costs and respond to emergencies
- New real-time microcontroller system from Texas Instruments enables smarter processing in automotive and industrial applications
- Operational amplifier stability analysis problem
- 【NXP Rapid IoT Review】+ My Review Summary
- VHDL Introduction. Questions and Answers. Classic Examples. Experience Summary
- ROM and RAM How does the microcontroller execute step by step after power is turned on?
- How does the program execute from the reset sequence to the main function?
- [AutoChips AC7801x motor demo board review] + Motor drive - BLDC sensorless method
- EEWORLD University ---- Practical Projects for IoT Embedded Engineers
- AC 220v to DC 24v (LM7824CT)
- Today's live broadcast! How to design high-performance servo drives using Infineon IGBT7
- STM32MP157A-DK1 Evaluation + HelloWorld and GPIO (2)