1 Introduction
Ultrasonic waves propagate at different speeds in gases, liquids and solids. They have good directivity, concentrated energy, small attenuation during transmission, and strong reflection capabilities. Ultrasonic waves can propagate directionally at a certain speed and form reflections when encountering obstacles. Using this characteristic, the actual distance can be calculated by measuring the time it takes for the ultrasonic waves to return, thus achieving non-contact measurement of object distance. Ultrasonic ranging is fast, convenient, and not affected by factors such as light. It is widely used in hydrological level measurement, construction site measurement, on-site location monitoring, vehicle reversing obstacle detection, mobile machine entry detection and positioning, and other fields. The digital ultrasonic distance meter designed in this article counts the clock pulses of a specific frequency input to the counter during the ultrasonic round-trip time, and then displays the corresponding measurement distance.
2 Ultrasonic distance meter circuit composition and working principle
The ultrasonic distance meter is composed of an ultrasonic generating circuit, an ultrasonic receiving amplifier circuit, and a counting and display circuit.
2.1 Ultrasonic generating circuit
Figure 1 shows the ultrasonic generating circuit. The dual timer EN556 (U2b) forms a monostable trigger. R6 and C6 form a differential circuit, and its function is: when button S2 is pressed, the low level becomes a positive and negative peak pulse, and a negative peak pulse is obtained through VD1, triggering the flip of the monostable trigger. The high level of the monostable flip output lasts for about 1 ms, that is, tw≈1.1R5C5≈1 ms. EN556 (U2n) forms a multivibrator with an oscillation frequency f1=1/T1≈1/{0.7[(R1+R2)+2(R3+R4)]C3≈40 kHz. The oscillator oscillation is controlled by the monostable flip-flop output level. When the monostable trigger outputs a high level, the multivibrator oscillates, and pin 5 of the EN556 outputs about 40 rectangular pulses with a frequency of 40 kHz and a duty cycle of about 50%. Considering that the multivibrator is unstable at the start-up stage, the number of m pulses is designed to be transmitted. If the number of output pulses is too few, the emission intensity will be small and the measurement distance will be short. However, there are too many pulses and the transmission duration is long. When the distance to the measured object is close, the pulse train has not yet been completely transmitted. This will cause the echo generated by the first pulse to reach the receiving end, affecting the ranging results and causing the ranging The blind area increases. U1a~U1e of 74HC04 (U1) form an ultrasonic pulse drive circuit, which can increase the amplitude of the pulse voltage that drives the ultrasonic sending sensor, effectively perform electrical/acoustic conversion, enhance the ability to transmit ultrasonic waves, and increase the measurement distance. One path of the 40 kHz pulse train is inverted through U1a, and then inverted through the inverter connected in parallel between U1b and U1e; the other path is inverted through the inverter connected in parallel between U1c and U1d.
In this way, the two pulse voltages applied to both ends of the ultrasonic transmitting sensor have opposite phases, so that the peak-to-peak value of the pulse voltage at both ends of the ultrasonic transmitting sensor is increased by nearly 2 times the power supply voltage, and the output power is increased by 4 times. Two CMOS gates connected in parallel can increase the output drive current. Capacitor C1 is used to block DC to prevent DC voltage from being applied to the ultrasonic sensor for a long time, causing the insulation resistance of the ultrasonic sensor to decrease and thus reducing the performance of the ultrasonic sensor.
2.2 Ultrasonic receiving amplification and shaping circuit
The ultrasonic receiving amplification and shaping circuit is shown in Figure 2.
The ultrasonic receiving sensor converts the received returned ultrasonic wave into a weak electrical signal. After being amplified and shaped by CX20106A, it outputs a negative pulse voltage. CX20106A is an infrared remote control receiver, which is composed of preamplifier, band-pass filtering, detection and waveform shaping circuits. By connecting an external resistor and setting the center frequency f0 of the internal bandpass filter circuit to 40 kHz, the ultrasonic electrical signal can be received and amplified, and the negative pulse voltage can be shaped and output. Pin 1 of the device is the ultrasonic electrical signal input end. Pin 2 and ground are connected to an RC series network. This is a component of the negative feedback network of the internal preamplifier circuit. Changing the value of resistor R8 will change the preamplifier circuit. gain. The detection capacitor C9 is connected between pin 3 and ground. Appropriate changes in C9 can change the sensitivity and anti-interference ability of the ultrasonic electrical signal amplification and shaping circuit. A resistor is connected between pin 5 and the power supply to set the center frequency f0 of the internal band-pass filter circuit. When R9=200 kΩ, f0=40 kHz. An integrating capacitor C10 is connected between pin 6 and ground. The standard value is 330 pF. If the capacitance value is too large, the low-level duration of the output pulse will increase and the measurement distance will become shorter. Pin 7 is the open collector output of the circuit, and R10 is the pull-up resistor for this pin. When CX20106A has no signal input, pin 7 outputs high level. After the input ultrasonic electrical signal is amplified and shaped, pin 7 outputs a negative pulse voltage. Using CX20106A to achieve ultrasonic reception amplification and shaping can avoid problems such as self-excitation of high-gain amplification circuits composed of multi-stage integrated operational amplifiers.
During the transmission of ultrasonic waves, point C in Figure 2 is high level (tW≈1 ms), the transistor V Q1 is turned on, and the ultrasonic electrical signal input terminal is short-circuited, thereby avoiding receiving ultrasonic waves and sending direct waves emitted by the sensor. Therefore, the theoretical minimum measurement distance (backward area) of the rangefinder is approximately Smin=Ctw/2≈0.17 m. Among them, C is the propagation speed of ultrasonic waves in the air. Because the energy of ultrasonic waves propagating in the air will continue to attenuate, there is a maximum effective measurement distance for ultrasonic ranging. The maximum effective measurement distance is related to many factors: ultrasonic sensor performance, driving ultrasonic sensor pulse voltage amplitude (power), shape of the measured object, wave absorption characteristics of the measured object, angle between reflected wave and incident wave, ultrasonic wave receiving amplification Circuit sensitivity, etc.
Previous article:Design of HIOKI3286 power analyzer based on microprocessor
Next article:How to use the transformer ratio tester_What can the transformer ratio tester test?
Recommended ReadingLatest update time:2024-11-22 14:45
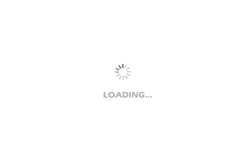
- New IsoVu™ Isolated Current Probes: Bringing a New Dimension to Current Measurements
- Modern manufacturing strategies drive continuous improvement in ICT online testing
- Methods for Correlation of Contact and Non-Contact Measurements
- Keysight Technologies Helps Samsung Electronics Successfully Validate FiRa® 2.0 Safe Distance Measurement Test Case
- From probes to power supplies, Tektronix is leading the way in comprehensive innovation in power electronics testing
- Seizing the Opportunities in the Chinese Application Market: NI's Challenges and Answers
- Tektronix Launches Breakthrough Power Measurement Tools to Accelerate Innovation as Global Electrification Accelerates
- Not all oscilloscopes are created equal: Why ADCs and low noise floor matter
- Enable TekHSI high-speed interface function to accelerate the remote transmission of waveform data
- Intel promotes AI with multi-dimensional efforts in technology, application, and ecology
- ChinaJoy Qualcomm Snapdragon Theme Pavilion takes you to experience the new changes in digital entertainment in the 5G era
- Infineon's latest generation IGBT technology platform enables precise control of speed and position
- Two test methods for LED lighting life
- Don't Let Lightning Induced Surges Scare You
- Application of brushless motor controller ML4425/4426
- Easy identification of LED power supply quality
- World's first integrated photovoltaic solar system completed in Israel
- Sliding window mean filter for avr microcontroller AD conversion
- What does call mean in the detailed explanation of ABB robot programming instructions?
- USB Type-C® and USB Power Delivery: Designed for extended power range and battery-powered systems
- RAQ #223: How to measure and determine soft-start timing without a soft-start equation?
- RAQ #223: How to measure and determine soft-start timing without a soft-start equation?
- GigaDevice's full range of automotive-grade SPI NOR Flash GD25/55 wins ISO 26262 ASIL D functional safety certification
- GigaDevice's full range of automotive-grade SPI NOR Flash GD25/55 wins ISO 26262 ASIL D functional safety certification
- New IsoVu™ Isolated Current Probes: Bringing a New Dimension to Current Measurements
- New IsoVu™ Isolated Current Probes: Bringing a New Dimension to Current Measurements
- Infineon Technologies Launches ModusToolbox™ Motor Kit to Simplify Motor Control Development
- Infineon Technologies Launches ModusToolbox™ Motor Kit to Simplify Motor Control Development
- STMicroelectronics IO-Link Actuator Board Brings Turnkey Reference Design to Industrial Monitoring and Equipment Manufacturers
- National Semiconductor launches new PWM buck controller with low noise emulated current mode structure
- [Evaluation of domestic FPGA Gaoyun GW1N-4 series development board] Development environment construction and new project
- [RVB2601 Creative Application Development] 1. Unboxing, Hardware Appreciation and Data Download
- Some questions about the secondary radar code~~Seek answers from the experts
- Python transplant
- Selection and Differences of Isolated Oscilloscopes and Differential Probes
- Power Input Inrush Current Limiting Module
- Recommend domestic low power LDO
- Common interface standards
- ST MEMS Creative Competition Post 7 - Machine Learning Core Learning (2) (MLC)