In view of the need for CAN bus communication quality, testing and verification, as well as the complexity of traditional CAN analyzers and the insufficiency of having to use a PC as a display terminal, a design of a CAN bus analyzer based on an ARM microcontroller and a smart phone is demonstrated. The analyzer uses a hardware circuit with an ARM microcontroller as the core to complete real-time data collection and monitoring of the CAN network; it uses Bluetooth communication to achieve communication between the analyzer and the smart phone and uses the smart phone as the terminal to complete data analysis. The article specifically designs the analyzer hardware, software and smart phone page, proposes a new baud rate automatic detection method, and finally gives the actual test results of the designed CAN bus analyzer, which can realize the functions of CAN bus baud rate automatic detection, normal monitoring and CAN bus status analysis.
CAN (controller area network) is a serial data bus with strong real-time performance, good flexibility and high standardization. It is widely used in automotive electronics, industrial automation, ships, medical equipment, industrial equipment and other fields. Its test equipment, CAN network analyzer, has become a must-have for developers. With the help of the easy-to-use CAN bus analyzer, it is possible to quickly find the design problems or abnormal interference problems in the use of the CAN bus system, and eliminate the faults and problems.
Traditional CAN analyzers require the computer to be connected to the CAN analyzer via USB, and then the bus to be tested is connected to the CAN analyzer via the DB9 interface. Since the CAN bus is a popular field bus in the vehicle industry, such a debugging method is not very convenient for vehicles that need to be road tested, and it is difficult to ensure normal operation. Similarly, in the field of industrial control, the traditional CAN analyzer may cause some confusion in industrial sites with many wiring harnesses because both ends have wires. In addition, in order to ensure safety, today's equipment using the CAN bus sometimes has more than one bus. Traditional analyzers have at most two interfaces, which means that if you want to test more than two CAN buses at the same time, you need two USB interfaces. If the two CAN buses are far apart, you need a longer USB cable. For this reason, here is a Bluetooth CAN bus analyzer with low cost, small size, simple structure, wireless debugging and low environmental requirements.
1 Hardware Design
1.1 Overall design
In view of the various shortcomings of traditional CAN analyzers, this paper proposes a new CAN analyzer that uses a smartphone instead of a PC as a display terminal, uses Bluetooth wireless transmission instead of USB cable transmission, and has its own lithium battery. The overall design structure is shown in Figure 1.
Figure 1 Overall design block diagram of Bluetooth CAN analyzer
Since the CAN analyzer is a communication protocol with a high baud rate, and complex calculations are required for communication quality analysis and fault location, the Bluetooth CAN analyzer proposed in this paper includes three parts in its overall design: one part is a processing motherboard with ARM as the processing core, which is responsible for CAN bus baud rate detection, data acquisition and Bluetooth communication signal transmission; the second part is a lithium battery, which is responsible for providing power to the motherboard. The lithium battery has a voltage of 5V, a capacity of 3000mAh, and a size of 11.6mm X42mm×69ram, which can ensure that the system works for more than 10h; the third part is a smart phone, which is responsible for receiving CAN bus data and processing the data.
1.2 Motherboard Design
There are 4 modules on the mainboard, namely, isolated CAN interface module, ARM processor module, Bluetooth serial port module, and power circuit module. The design block diagram is shown in Figure 2, and the actual picture is shown in Figure 3.
The isolated CAN interface module is responsible for sending the ARM data to the CAN bus and sending the data on the CAN bus to the ARM processor.
Figure 2 Mainboard system design block diagram
Figure 3 Motherboard shopping map
The ARM processor module is the core of this analyzer, using the NXP LPC2119 processor. LPC2119 is based on a 16/32-bit ARM7TDMI-STM CPU that supports real-time simulation and tracing, with 128KB embedded high-speed Flash memory, and internally integrated with 2 CAN controllers. Its main features are: data transmission rate on a single bus up to 1MB/s; 32-bit register and RAM access; compatible with CAN2.0B, IS011898.1 specifications; global acceptance filter can identify all 11-bit and 29-bit identifiers; acceptance filter provides Full CAN-style automatic reception for selected standard identifiers. It is mainly responsible for processing the data on the CAN bus and then sending it to the mobile phone through the Bluetooth serial port. In addition, the ARM module is also responsible for detecting the baud rate on the unknown CAN bus and sending it to the mobile phone.
The Bluetooth serial port module is responsible for exchanging data between ARM and the mobile phone, and the communication rate of its serial port reaches 1 382 400bps. The power module is responsible for supplying power to each module.
Previous article:Learn about logic analyzer testing in seven steps
Next article:Waveguide Calibration Setup Guide Using a Network Analyzer
Recommended ReadingLatest update time:2024-11-16 15:00
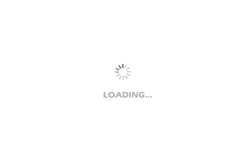
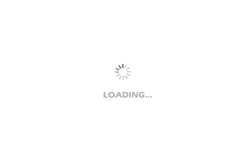
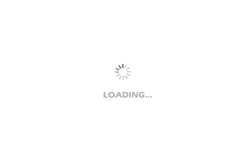
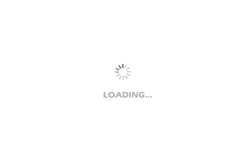
- Keysight Technologies Helps Samsung Electronics Successfully Validate FiRa® 2.0 Safe Distance Measurement Test Case
- From probes to power supplies, Tektronix is leading the way in comprehensive innovation in power electronics testing
- Seizing the Opportunities in the Chinese Application Market: NI's Challenges and Answers
- Tektronix Launches Breakthrough Power Measurement Tools to Accelerate Innovation as Global Electrification Accelerates
- Not all oscilloscopes are created equal: Why ADCs and low noise floor matter
- Enable TekHSI high-speed interface function to accelerate the remote transmission of waveform data
- How to measure the quality of soft start thyristor
- How to use a multimeter to judge whether a soft starter is good or bad
- What are the advantages and disadvantages of non-contact temperature sensors?
- Innolux's intelligent steer-by-wire solution makes cars smarter and safer
- 8051 MCU - Parity Check
- How to efficiently balance the sensitivity of tactile sensing interfaces
- What should I do if the servo motor shakes? What causes the servo motor to shake quickly?
- 【Brushless Motor】Analysis of three-phase BLDC motor and sharing of two popular development boards
- Midea Industrial Technology's subsidiaries Clou Electronics and Hekang New Energy jointly appeared at the Munich Battery Energy Storage Exhibition and Solar Energy Exhibition
- Guoxin Sichen | Application of ferroelectric memory PB85RS2MC in power battery management, with a capacity of 2M
- Analysis of common faults of frequency converter
- In a head-on competition with Qualcomm, what kind of cockpit products has Intel come up with?
- Dalian Rongke's all-vanadium liquid flow battery energy storage equipment industrialization project has entered the sprint stage before production
- Allegro MicroSystems Introduces Advanced Magnetic and Inductive Position Sensing Solutions at Electronica 2024
- Car key in the left hand, liveness detection radar in the right hand, UWB is imperative for cars!
- After a decade of rapid development, domestic CIS has entered the market
- Aegis Dagger Battery + Thor EM-i Super Hybrid, Geely New Energy has thrown out two "king bombs"
- A brief discussion on functional safety - fault, error, and failure
- In the smart car 2.0 cycle, these core industry chains are facing major opportunities!
- The United States and Japan are developing new batteries. CATL faces challenges? How should China's new energy battery industry respond?
- Murata launches high-precision 6-axis inertial sensor for automobiles
- Ford patents pre-charge alarm to help save costs and respond to emergencies
- New real-time microcontroller system from Texas Instruments enables smarter processing in automotive and industrial applications
- Loss Analysis of MOSFET in Flyback Critical Operation Mode
- [SAMR21 new gameplay] 30. Pin definition
- In fact, the original "analog electronics" and "digital electronics" are incompatible!
- Learning ARM-LINUX embedded system based on LS_BBB development board Part 1: Platform Overview
- What is loop response?
- GD32E231 DIY Competition (3) GD32E231C driving OLED (128X32)
- Looking for domestic brushless motor control chip?
- A serial screen product with analog video signal usage sharing
- Useful information | Four major development skills for microcontrollers!
- 【TI mmWave Radar Review】+Configuration File Test (I)