PXI Express Technology Overview
Based on the latest PCI Express technology, PXI Express increases the PXI backplane bandwidth from 132 MB/s to 6 GB/s, an increase of more than 45 times. In addition to the existing timing and synchronization functions of PXI, PXI Express also provides additional timing and triggering buses, including 100 MHz differential system clock, differential signal, and differential star trigger (see Figure 1). By using differential clocks and triggers, PXI Express systems increase the noise resistance of instrument clocks and can transmit higher frequency clock signals.
Figure 1: PXI Express provides additional timing and synchronization capabilities based on the existing capabilities of the PXI platform, enabling higher-precision measurements.
While significantly improving performance, PXI Express is fully compatible with PXI hardware and software. The software compatibility of PCI Express makes the standard software framework provided by PXI also applicable to PXI Express. In order to ensure hardware compatibility, the PXI Express standard defines a hybrid slot that allows engineers to install PXI or PXI Express modules in the same slot. With these technologies, engineers and manufacturers can take advantage of hardware and software compatibility to retain existing investments in PXI systems and products to the greatest extent possible.
PXI Express Technical Advantages
For automated measurement and control applications, the PXI/PXI Express platform provides the following three technical advantages:
*Flexible, software-defined instrumentation system
*Highly integrated modular architecture
* High data throughput and precise timing synchronization
Through software-defined solutions, users can obtain raw measurement data and obtain flexible and fully customized measurement results by applying different analysis methods. For example, for testing in the RF/communication field, in the face of an endless stream of wireless standards, it is necessary to adopt a software radio architecture based on a unified hardware platform. Only by changing the modulation and demodulation methods on the software can different wireless protocols be tested.
Secondly, relying on the modular architecture, you can choose the right measuring instrument from more than 1,500 existing high-performance PXI instruments , while helping to save investment costs and conveniently upgrade the performance of controllers and modules at any time. For example, the modular architecture enables you to implement ASIC characterization of multiple mixed signals in one system , and configure and upgrade the test system according to the signal requirements.
Furthermore, the high throughput of PXI Express makes more high-speed measurement applications possible, such as high-bandwidth IF (intermediate frequency) instruments, high-speed digital video testing, etc. In conjunction with PXI Express RAID hard drives, real-time data streaming up to 600 MB/s can also be achieved. For sound vibration testing and structural testing that require high phase error between channels, the precise timing and synchronization functions of PXI/PXI Express are indispensable.
Software-defined measurements: RF/communications testing
As wireless devices now integrate more and more communication protocols, such as 802.11g, GSM, GPS, and Bluetooth, the challenges and testing costs of wireless device testing are increasing. In the past, you may need multiple instruments to test the performance of devices under different communication standards, which requires considerable cost and physical space. Now, with a software-defined modular architecture, you can use the same 2.7GHz PXI RF software radio platform to test a variety of wireless communication protocols. In addition, you can also add more integrated functions such as digital protocol testing and audio analysis to the testing of communication equipment. A typical case of wireless communication equipment testing is the production line test of mobile phones , as shown in Figure 2.
Figure 2: Production line testing of mobile phones integrating multiple wireless standards and functions
The PXI vector signal analyzer in Figure 2 can capture RF signals of various frequencies under different communication standards. Since the encoding and decoding of the communication protocol is implemented by software, different protocols such as GSM, IEEE 802.11g, and Bluetooth can be tested on the same platform. This software-defined measurement method not only reduces the size of the test equipment, but also reduces the cost of testing.
Integrated Modular Architecture: Mixed-Signal ASIC Characterization
Modern ASICs usually have multiple mixed-signal inputs and outputs. The single-platform solution provided by the PXI instrument system can integrate the test functions of multiple instruments in one platform to complete the characterization of complex ASIC chips.
For example, we need to test a four-channel, 12-bit, 100 MHz digital-to-analog converter chip. Such an ASIC requires 48 synchronous digital I/O channels, 4 precise analog input channels, and a programmable DC power module. Based on the PXI/PXI Express platform, you can integrate the above measurement modules into a system, in which multiple digital I/O modules can be synchronized to ensure that the synchronization error between the 48 channels is less than 1ns; in addition, the PXI high-speed digitizer can provide up to 14-bit resolution at a sampling rate of 100 MS/s, and with a low-loss RF switch module, it can switch the four-channel high-speed analog signal. Finally, the PXI programmable power module can provide a voltage signal of 0V~6V, which changes at intervals of 120mV, to power the Vcc of the ASIC (as shown in Figure 3).
Figure 3. Reference architecture for four-channel high-speed DAC testing
Relying on the modular instrument system architecture, the system can be reconfigured or expanded to meet future test needs. With the use of NI LabVIEW software programming environment, you can also measure various ASIC standard parameters such as THD, SFDR, SINAD, and perform complex and comprehensive characterization of the chip under test by observing its performance under different power, current and other factors.
High data throughput: real-time data streaming applications
High-speed measurement applications, such as RF/IF signal acquisition, digital video testing, high-speed image acquisition, etc., are becoming more and more widespread. Although traditional desktop instruments have very high sampling rates and bandwidths, due to the limitations of onboard memory capacity, their continuous acquisition time and waveform storage capacity are limited after all. What is transmitted back to the control PC via GPIB (or Ethernet, USB) is often only the analysis result. If the original measurement data is to be transmitted, a lot of test time will be consumed (GPIB bandwidth is about 1MB/s). In this way, the measurement function is completely defined by the instrument manufacturer. Users cannot get the original data, cannot do customized analysis, and lose control over the data.
Nowadays, with the high bandwidth of PXI/PXI Express, users can easily collect a large amount of raw data, transmit it back to the controller through the bus, and store it on the hard disk in real time for subsequent customized analysis and data backup. It is the use of commercial off-the-shelf (COTS) PCI/PCI Express technology that makes high-speed data streaming applications that originally required expensive dedicated instruments simpler and more feasible.
Let's take a look at an IF signal acquisition and streaming case, and analyze the technical points and programming implementation of high-speed data streaming applications based on PXI Express through the case.
Modern satellite communications and spectrum monitoring applications require storing large amounts of RF/IF signals on a hard disk for a long time for later data playback and signal analysis and capture. In the past, such applications could only be achieved with custom hardware that was expensive to build and maintain. Now, you can use high-bandwidth PXI/PXI Express instrument systems to develop such applications quickly and efficiently.
In this application, we use a down -conversion module to down-convert the RF signal to an IF signal that can be converted to an analog-to-digital signal, and then use a high-speed digitizer with a sampling rate of 100 MS/s to acquire the IF signal. Since the two channels of the digitizer can be used for simultaneous acquisition, each with a bandwidth of 50 MHz, this system can acquire RF signals with a bandwidth of up to 100 MHz (see Figure 4).
Figure 4: Data flow disk architecture in communication system testing
For signal monitoring applications, it is usually necessary to stream spectrum data for several minutes or even hours, and the real-time data throughput can be as high as 400 MB/s. It should be noted that the digitizer has a 14-bit resolution, so each sample value requires two bytes of storage space. The specific calculation formula for data throughput is as follows.
Data throughput = sampling rate × bytes/sample point × number of channels = 100 MS/s × 2 bytes/sample point × 2 channels = 400 MB/s
Such a high data throughput poses a huge challenge to the bus and hard disk. Even the ordinary PXI bus is not up to the task. Here we use the PXI Express bus with a data throughput of up to 2 GB/s and the PXI Express x4 RAID-0 hard disk drive (read and write speed up to 650 MB/s). Subsequent power spectrum and joint time-frequency domain software analysis are performed on a high-performance dual-core embedded controller (see Figure 5).
Figure 5: PXI Express-based communication test system
For software programming of such a complex system, we used the inherent multithreaded parallel programming model of NI LabVIEW to better optimize the speed of data streaming and give full play to the performance of multi-core processors. Because LabVIEW automatically distributes programming tasks to multiple threads (multiple threads can also be specified to run on different cores), we can separate instrument I/O and file I/O into two independent loops, as shown in Figure 6. This producer-consumer programming architecture. The upper loop (producer) collects data from the high-speed digitizer and passes it to a queue structure (a LabVIEW FIFO). The lower loop (consumer) reads the data from the queue structure and writes it to disk. This producer-consumer architecture achieves the best performance for data streaming applications because the producer loop can continuously collect data while the consumer loop writes data to disk.
Figure 6 Producer-Consumer Parallel Architecture in LabVIEW
Conclusion
Combined with the analysis of the above practical cases, with these technical advantages, the PXI/PXI Express platform can provide cost-effective solutions for emerging applications such as RF/IF signal acquisition, digital video testing, and mixed-signal ASIC characterization. With the high bandwidth of GHz on PXI Express, it can bring new concepts and implementation methods to the field of high-speed measurement, helping users build efficient and low-cost automated test systems.
Previous article:Analysis and Measurement of PIM in WCDMA Systems
Next article:Measuring Noise on DSL
Recommended ReadingLatest update time:2024-11-16 22:51
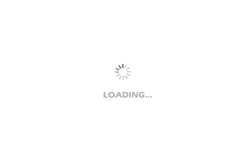
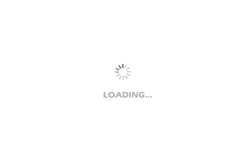
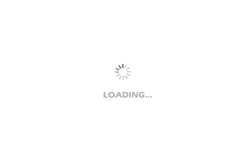
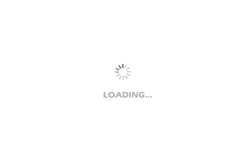
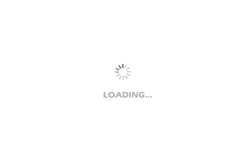
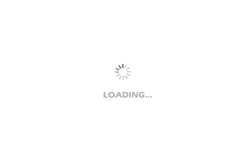
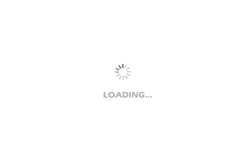
- Popular Resources
- Popular amplifiers
- Keysight Technologies Helps Samsung Electronics Successfully Validate FiRa® 2.0 Safe Distance Measurement Test Case
- From probes to power supplies, Tektronix is leading the way in comprehensive innovation in power electronics testing
- Seizing the Opportunities in the Chinese Application Market: NI's Challenges and Answers
- Tektronix Launches Breakthrough Power Measurement Tools to Accelerate Innovation as Global Electrification Accelerates
- Not all oscilloscopes are created equal: Why ADCs and low noise floor matter
- Enable TekHSI high-speed interface function to accelerate the remote transmission of waveform data
- How to measure the quality of soft start thyristor
- How to use a multimeter to judge whether a soft starter is good or bad
- What are the advantages and disadvantages of non-contact temperature sensors?
- Innolux's intelligent steer-by-wire solution makes cars smarter and safer
- 8051 MCU - Parity Check
- How to efficiently balance the sensitivity of tactile sensing interfaces
- What should I do if the servo motor shakes? What causes the servo motor to shake quickly?
- 【Brushless Motor】Analysis of three-phase BLDC motor and sharing of two popular development boards
- Midea Industrial Technology's subsidiaries Clou Electronics and Hekang New Energy jointly appeared at the Munich Battery Energy Storage Exhibition and Solar Energy Exhibition
- Guoxin Sichen | Application of ferroelectric memory PB85RS2MC in power battery management, with a capacity of 2M
- Analysis of common faults of frequency converter
- In a head-on competition with Qualcomm, what kind of cockpit products has Intel come up with?
- Dalian Rongke's all-vanadium liquid flow battery energy storage equipment industrialization project has entered the sprint stage before production
- Allegro MicroSystems Introduces Advanced Magnetic and Inductive Position Sensing Solutions at Electronica 2024
- Car key in the left hand, liveness detection radar in the right hand, UWB is imperative for cars!
- After a decade of rapid development, domestic CIS has entered the market
- Aegis Dagger Battery + Thor EM-i Super Hybrid, Geely New Energy has thrown out two "king bombs"
- A brief discussion on functional safety - fault, error, and failure
- In the smart car 2.0 cycle, these core industry chains are facing major opportunities!
- The United States and Japan are developing new batteries. CATL faces challenges? How should China's new energy battery industry respond?
- Murata launches high-precision 6-axis inertial sensor for automobiles
- Ford patents pre-charge alarm to help save costs and respond to emergencies
- New real-time microcontroller system from Texas Instruments enables smarter processing in automotive and industrial applications
- Comment to win a gift | TI SK-AM64 evaluation kit review
- I want to borrow a mm32f103 board
- Please help explain the principle of PWM2 generated in the following picture
- Clock module of MSP430G2553 microcontroller
- Is there anyone who can run the SPI of CH32V103?
- Free gift of old punch card machine (for disassembly and research)
- I need help from an expert to look at the program and tell me how to modify it so that the buzzer can sound three times and then pause for 0.5 seconds before sounding again.
- MSP430G2755 Main Memory Bootloader UART Porting Guide
- McAsp multi-channel understanding
- Please help me look at this oscillator circuit