As we all know, a motor is a device that can convert electrical energy into mechanical energy. It is widely used in the fields of industry, agriculture, military industry, rail transportation, household appliances, medical treatment, etc. It can be said that it is everywhere. Especially with the development of variable frequency speed regulation technology in the industry, more and more motors support real-time control, because they have some irreplaceable characteristics: they can adjust the output speed and torque in real time according to the load requirements to achieve motion control or energy saving. These motors have one thing in common - they need driver control, and the most typical ones are servo motors and variable frequency motors.
For example, the traditional fan and water pump industry originally used three-phase asynchronous motors, but now they should use a combination of frequency converter + variable frequency motor to achieve speed control of the motor and achieve energy saving and emission reduction. For example, when the drainage load is high, the output power of the water pump motor is increased to achieve full load output; at night when the drainage load is small, the speed of the water pump motor is reduced through the frequency converter to reduce the output power of the water pump, thereby achieving energy saving.
Although variable frequency motors and brushless motors achieve better energy saving through motor control, they also introduce a new device - motor driver (inverter). Since motor drivers also have efficiency losses, we cannot only focus on the motor when evaluating motor performance, but must evaluate the driver and motor as a comprehensive system.
Importance of synchronous testing of motors and drives
In traditional motor testing, the efficiency of the motor is not constant, but varies with the speed (load). The same is true for motor drivers in terms of efficiency testing.
Therefore, in order to ensure the accuracy of the motor efficiency and motor driver efficiency test, it is necessary to ensure that the efficiency of both is measured under the same load, that is, to ensure that the data is collected at the same time point. A multi-channel power analyzer is generally used for measurement. As shown in the figure below, it is a very common method for synchronous testing of variable frequency motors and inverters.
In this system, the three-phase input and three-phase output of the inverter (motor driver) and the speed and torque output of the motor are all connected to the same device (power analyzer) for collection, and the efficiency calculation tool inside the device is used to achieve synchronous measurement of the efficiency of the motor, motor driver and the entire system. If the synchronization of the power analyzer is ensured to be good enough, such as the PA power analyzer used in the example, the synchronization error is as low as 10ns, and the efficiency test results are basically accurate.
Practical Application
For example, in the motor testing product of ZLG Zhiyuan Electronics, the MPT motor testing system, the above-mentioned synchronous measurement solution is used. Through this method, the synchronous output performance parameters and efficiency values of the motor and drive can be obtained in real time, which is very helpful for users to effectively analyze and utilize the data.
Previous article:Temperature and humidity control based on ANFIS
Next article:Design and implementation of multi-FC daughter card test equipment based on PCIE
Recommended ReadingLatest update time:2024-11-15 17:21
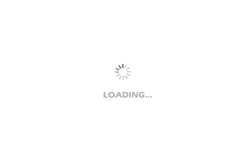
- Popular Resources
- Popular amplifiers
-
Evaluation and analysis of shift quality of passenger car dual-clutch transmission based on AVL-DRIVE system
-
Motor Control and Learning (Markus Latash, Francis Lestienne)
-
Motor control fundamentals (Steve Senty)
-
Human-Aware Robotics Modeling Human Motor Skills for the Design, Planning and Control of a New Gener
- From probes to power supplies, Tektronix is leading the way in comprehensive innovation in power electronics testing
- Seizing the Opportunities in the Chinese Application Market: NI's Challenges and Answers
- Tektronix Launches Breakthrough Power Measurement Tools to Accelerate Innovation as Global Electrification Accelerates
- Not all oscilloscopes are created equal: Why ADCs and low noise floor matter
- Enable TekHSI high-speed interface function to accelerate the remote transmission of waveform data
- How to measure the quality of soft start thyristor
- How to use a multimeter to judge whether a soft starter is good or bad
- What are the advantages and disadvantages of non-contact temperature sensors?
- In what situations are non-contact temperature sensors widely used?
- LED chemical incompatibility test to see which chemicals LEDs can be used with
- Application of ARM9 hardware coprocessor on WinCE embedded motherboard
- What are the key points for selecting rotor flowmeter?
- LM317 high power charger circuit
- A brief analysis of Embest's application and development of embedded medical devices
- Single-phase RC protection circuit
- stm32 PVD programmable voltage monitor
- Introduction and measurement of edge trigger and level trigger of 51 single chip microcomputer
- Improved design of Linux system software shell protection technology
- What to do if the ABB robot protection device stops
- Huawei's Strategic Department Director Gai Gang: The cumulative installed base of open source Euler operating system exceeds 10 million sets
- Download from the Internet--ARM Getting Started Notes
- Learn ARM development(22)
- Learn ARM development(21)
- Learn ARM development(20)
- Learn ARM development(19)
- Learn ARM development(14)
- Learn ARM development(15)
- Analysis of the application of several common contact parts in high-voltage connectors of new energy vehicles
- Wiring harness durability test and contact voltage drop test method
- The close connection between crystal oscillator and Bluetooth technology
- ADI's most popular technical articles
- 【DIY Creative LED】Main Component Description
- Design of automatic loading scheme for TMS320C6701
- GD32F chip problems and solutions
- 40 "Millions" of Raspberry Pi Cars - ROS Learning (C Language Programming to Control the Turtle)
- Free application: Sipeed Gaoyun GW2A FPGA development board
- EEWORLD University ---- Basic Electronic Components
- Can stm32f103 collect a sine wave signal with an amplitude of 200mv and a frequency of 1KH?
- EEWORLD University - How to use switching chargers to design safe and reliable products with long standby time and powered by micro batteries