The automobile industry is a pillar industry of the country, and the electronics industry is also a pillar industry of the country. As the intersection of the automobile industry and the electronics industry, the rise and fall of the automotive electronic parts industry is closely related to the national economy. At present, the output of automobiles in China is rising year by year. While the national automobile brands are growing, they also force international automobile companies or joint ventures to reduce production costs and implement the strategy of localization of automotive electronic parts. This provides a good opportunity for the development of China's automotive electronics industrialization.
In addition to its complex functional requirements, the requirements for real-time, safety, reliability and environmental protection of pre-installed automotive electronic products are very strict, and automobile manufacturers have their own relevant execution inspection standards and production process specifications. Therefore, it is very necessary to develop corresponding fault detection systems for pre-installed automotive electronic products.
1 System design scheme
1.1 Design basis
CAN bus, as a serial automotive bus, has the advantages of simple structure, high reliability and mature technology. It has been widely used in the automotive field. Pre-installed automotive electronic products must follow the CAN communication protocol of a specific model. Almost all control and status information of the whole vehicle depends on CAN bus transmission. By collecting and analyzing the signals on the CAN bus, the working status and real-time parameters of each component can be accurately obtained. This is the basic basis of the automotive electronic test system.
The general requirements of automobile manufacturers for test instruments include real-time, reliability, portability, and friendly human-computer interaction. Embedded systems can fully meet the requirements of manufacturers for test instruments due to their flexible hardware and software design, good reliability and real-time performance, and low power consumption. Therefore, CAN frame testing and embedded design are effective solutions for automotive electronic test systems.
1.2 Implementation plan
Embedded automotive electronic test systems generally choose 32-bit microprocessors with relatively good performance, such as ARM processors. The hardware design includes power modules, storage modules, and human-computer interaction modules commonly used in embedded systems. Based on CAN bus communication, the corresponding CAN bus communication module must be designed. The module usually consists of two parts: one is the CAN controller, which is used to implement the data link layer protocol of the CAN bus; the other is the CAN driver, which is used to implement the physical layer of the CAN bus. The basic structure diagram of the system is shown in Figure 1.
Automotive electronic test instruments generally require friendly human-computer interaction and have relatively high requirements for interface design. Therefore, a layered software design method should be adopted in software design. Generally, it is necessary to transplant related embedded operating systems. Currently, the commonly used embedded operating systems are mainly Linux and Wince. The software design process mainly includes three stages: operating system transplantation, driver writing, and application design. Transplant a suitable embedded operating system to build a development platform for software development; develop relevant drivers to support hardware devices and provide interfaces for application software to access hardware. In the CAN module, it is generally necessary to develop drivers that support controllers and drivers to facilitate communication with automotive electronic products; the application is the top-level software that directly faces the user and provides friendly interaction for user use.
2 System Design Example
Based on the above system analysis, a specific design example explanation is given. The USB car audio playback system is a pre-installed automotive electronic product developed for a certain automobile manufacturer. The product strictly abides by the CAN bus protocol provided by the manufacturer in communication. This test system is mainly used for fault detection before components leave the factory.
2.1 Hardware Design
Considering the requirements of performance, power consumption, stability, etc., Intel's 32-bit industrial-grade microprocessor PXA270 is selected. The processor is based on the ARM10 core, runs at a main frequency of up to 520M-Hz, has rich interface resources, and adds IntelSpeedStep dynamic power management technology. It can minimize the power consumption of the device while ensuring CPU performance. The use of this processor simplifies the hardware design and ensures the fast operation of the software; the storage module uses 64 MB NorFlash and 64 MB SDRAM; the human-computer interaction adopts the solution of LCD display and touch control.
In the design of the CAN bus communication module, the chips used are SJA1000, PCA82C250 and TJA1055. SJA1000 is an independent CAN controller released by PHLIPS for automotive and general industrial environments. SJA1000 is a replacement product for PCA82C200 controller. In addition to supporting BasicCAN operation mode, it also adds a new operation mode PeliCAN, which supports CAN2.0B protocol with many new features. SJA1000 is used in CAN hardware module to implement the data link layer protocol of CAN bus. Two SJA1000 chips are used in this design, which are used for high-speed CAN and low-speed CAN communication respectively. The specific circuit schematic diagram of SJA1000 is shown in Figure 2. The data bus AD0~AD7 is connected to the data bus MD0~MD7 of PXA270 through the data buffer device, and the signal lines such as timing control are connected to CPLD and managed by PXA270 processor through CPLD.
PCA82C250 and TA1055 are both driver transceivers used to implement the physical layer of CAN bus. The difference is that the two chips each implement two standards of CAN physical layer: high-speed CAN and low-speed CAN. High-speed CAN can provide a baud rate of up to 1 Mbit/s according to the cable length, and low-speed CAN can provide a baud rate of 5~125 kbit/s, and allows the CAN bus to continue communication when the connection fails, so it is also called fault-tolerant CAN. The instrument supports two physical standards. The circuit diagram of the driver is shown in Figure 3. HTXD0, HRXD0, LTXD0, LRXD0 all come from SJA1000, and after passing through PCA82C250 and TJA1055, they get high-speed CAN channels HCHNH, HCHNL and low-speed CAN channels LGANH, LCANL respectively.
2.2 Software Design
Considering the high requirements of the manufacturer for human-computer interaction and in order to shorten the R&D cycle, Microsoft's Windows CE was selected as the embedded operating system. Wince is a compact, complete and scalable embedded operating system. It is a multi-threaded, priority-based preemptive operating system with memory management functions. It can suppress the danger of directly destroying the system due to abnormal application programs. It is particularly suitable for hardware platforms with limited resources. In addition, the Wince operating system inherits the style of the desktop Windows system in terms of interface operation, which is convenient for operators to familiarize themselves with and use.
The main work of software design includes the transplantation of Wince5.0 system on PXA270, the implementation of drivers such as CAN bus, LCD display, touch screen, Flash storage, Bluetooth, CAN protocol implementation and application design.
Wince drivers are mainly divided into local drivers and stream interface drivers. Local drivers are drivers that are required by hardware and do not support general device driver interfaces, such as touch screen drivers; stream interface drivers refer to drivers that expose stream interface functions without considering the type of device controlled by the driver. The driver of CAN bus is mainly software support for controller SJA1000. It is a typical stream interface driver in wince. The functions of SJA-1000 are realized through functions such as CAN_Init, CAN_Open, CAN_Close, CAN_Read, CAN_Write, CAN_IOControl, and CAN_Deiit. Among them, CAN_Init mainly completes the initialization of SJA1000, CAN_Open is used to respond to the request of the application, CAN_Read and CAN_Write are used to read and write characters from the CAN bus, CAN_IOControl is used to expand other functions, CAN_Close is used to close the response, and CAN_Deiit is used to release resources and unload the driver.
The application is developed using Embedded Visual C++4.0. The test instrument has many tasks. Most of the tests are based on the analysis of CAN frames sent by components. The main test functions of the instrument include: audio left and right channel test, microphone test, Bluetooth test, USB test, etc. The software flow of the system is shown in Figure 4, and the main interface of the system is shown in Figure 5.
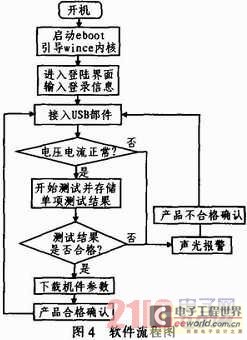
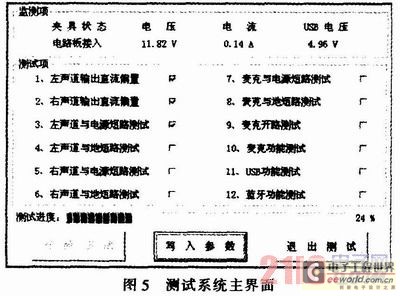
2.3 Field Application
This test instrument has been applied in field production to conduct quality test on USB car audio playback components before delivery. Practice shows that this test instrument is fast, reliable and user-friendly. Each instrument can detect 300 to 500 components per working day, and the detection accuracy rate reaches more than 99%, which fully meets the needs of manufacturers.
3 Conclusion
This paper proposes an automotive electronics test method based on CAN communication and CAN frame analysis in response to the specific needs of automotive electronics development. Field application shows that this method is a fast and effective method for testing pre-installed automotive electronic products. The embedded automotive electronic test instrument based on this method meets the manufacturers' needs for volume, price, speed, reliability, etc., and will continue to be widely used in pre-installed automotive electronic products developed in the future.
Previous article:Test instruments for wireless network installation and maintenance
Next article:VideoMASTER and PXI Create Wireless HDMI MIMO Test System
- Popular Resources
- Popular amplifiers
- Keysight Technologies Helps Samsung Electronics Successfully Validate FiRa® 2.0 Safe Distance Measurement Test Case
- From probes to power supplies, Tektronix is leading the way in comprehensive innovation in power electronics testing
- Seizing the Opportunities in the Chinese Application Market: NI's Challenges and Answers
- Tektronix Launches Breakthrough Power Measurement Tools to Accelerate Innovation as Global Electrification Accelerates
- Not all oscilloscopes are created equal: Why ADCs and low noise floor matter
- Enable TekHSI high-speed interface function to accelerate the remote transmission of waveform data
- How to measure the quality of soft start thyristor
- How to use a multimeter to judge whether a soft starter is good or bad
- What are the advantages and disadvantages of non-contact temperature sensors?
- Innolux's intelligent steer-by-wire solution makes cars smarter and safer
- 8051 MCU - Parity Check
- How to efficiently balance the sensitivity of tactile sensing interfaces
- What should I do if the servo motor shakes? What causes the servo motor to shake quickly?
- 【Brushless Motor】Analysis of three-phase BLDC motor and sharing of two popular development boards
- Midea Industrial Technology's subsidiaries Clou Electronics and Hekang New Energy jointly appeared at the Munich Battery Energy Storage Exhibition and Solar Energy Exhibition
- Guoxin Sichen | Application of ferroelectric memory PB85RS2MC in power battery management, with a capacity of 2M
- Analysis of common faults of frequency converter
- In a head-on competition with Qualcomm, what kind of cockpit products has Intel come up with?
- Dalian Rongke's all-vanadium liquid flow battery energy storage equipment industrialization project has entered the sprint stage before production
- Allegro MicroSystems Introduces Advanced Magnetic and Inductive Position Sensing Solutions at Electronica 2024
- Car key in the left hand, liveness detection radar in the right hand, UWB is imperative for cars!
- After a decade of rapid development, domestic CIS has entered the market
- Aegis Dagger Battery + Thor EM-i Super Hybrid, Geely New Energy has thrown out two "king bombs"
- A brief discussion on functional safety - fault, error, and failure
- In the smart car 2.0 cycle, these core industry chains are facing major opportunities!
- The United States and Japan are developing new batteries. CATL faces challenges? How should China's new energy battery industry respond?
- Murata launches high-precision 6-axis inertial sensor for automobiles
- Ford patents pre-charge alarm to help save costs and respond to emergencies
- New real-time microcontroller system from Texas Instruments enables smarter processing in automotive and industrial applications
- Regarding the question of whether the GND level is stable
- AD19 installation package always reports errors
- Tektronix offers free trials for more than 100 advanced application functions!
- Research on A-type digital flaw detection system based on FPGA.pdf
- Phase loss detection of three-phase three-wire circuit
- EEWORLD University Hall----Principle and Operation of DC Bridge Fudan University
- Small base stations can also take the center stage in the 5G era
- Vivado prompts [Synth 8-91] ambiguous clock in event control Problem Cause
- Simulation and Testbench Design.zip
- GaN tube selection