At present, most of the testing equipment for automobile safety parts is imported from countries with developed automobile manufacturing industries, especially the functional testing equipment for ABS (Anti-lock Braking System) sensors . Therefore, it is necessary to independently develop a fast, stable and universal testing equipment suitable for the production environment to meet the needs of a process that must be inspected for each piece in the production process.
This design uses the NI PCI-6220 multi-function data acquisition card and LabVIEW 7.1 development software to develop a test system that meets the requirements according to the German Volkswagen ABS sensor functional test standards. The system is fast and reliable, can realize data acquisition, analysis and storage, and has been put into use on the production line.
How ABS works
The most important function of ABS is not to shorten the braking distance, but to maintain the directional stability of the car as much as possible during braking. When ABS is in effect, the friction between the wheels and the road is rolling friction. It will make full use of the maximum adhesion between the wheels and the road to brake, thereby increasing the braking acceleration and shortening the braking distance, but the most important thing is to ensure the directional stability of the car. When ABS is working, it is equivalent to braking at a very high frequency. Therefore, in an emergency, if you press the brake pedal to the bottom,
Test Principle
As shown in Figure 1, during the test, the ABS rotating system is driven by the drive system to rotate at a constant speed in any direction. For the MK60 ABS sensor, it means rotating at a constant speed of 139.5r/m without braking force. As shown in Figure 2, 12Vdc and 3.3Vdc voltages are applied to the sensor between contacts ① and ② (UB), and two tests are performed continuously during rotation. Each test must ensure a complete test cycle. When the ABS sensor senses the number plate, a square wave peak is generated, otherwise a trough is generated. A 115Ω high-precision resistor R is used to obtain the voltage US. When UB is 12V, the frequency of the square wave, the maximum and minimum values of the current peak IH, the maximum and minimum values of the current valley IL, and the duty cycle of the signal are calculated based on the measured voltage value. As shown in Figure 3, when UB is 3.3V, the number of pole pairs and the pole spacing are calculated based on the measured voltage value. If these values are within the permitted range, the ABS sensor can be determined to be qualified.
Figure 1 Schematic diagram of ABS sensor test system
Figure 2 ABS circuit diagram
Figure 3 ABS square wave
In order to ensure a complete test cycle and determine whether the number of pole pairs of the ABS sensor is correct, a reference pulse generator is required. For this purpose, a toothed disc with 45 teeth is made. Because the number of pole pairs of the workpiece is 43 under normal circumstances, the number of teeth on the toothed disc is close to it. The tooth gap ratio of the toothed disc is 1:1, and it rotates with the workpiece being tested. The number of teeth on the reference toothed disc is detected by a photoelectric switch. Only when the signals of 45 photoelectric switches are detected can it be ensured that the ABS has been tested for a complete cycle. The photoelectric switch generates a sequence pulse of 0 to 24V, but after the photoelectric isolation of the interface board, it is converted into a sequence pulse of 0 to 5V, hereinafter referred to as the REF signal. When selecting this photoelectric switch, it should be noted that the response frequency must be greater than 45×139.5÷60=105Hz. [page]
Control Principle
Using NI PCI-6220 multi-function acquisition card, the ABS signal and REF signal are used as voltage analog quantities and connected to channel 0 and channel 1 of the multi-function acquisition card using differential input. In order to ensure the test accuracy, the analog quantity sampling rate is set to 25kS/s, and the buffer area of each channel is set to 500kS. The test data is stored reliably, and the number of reading points per channel is set to 250S. The test condition judgment signal and the test conclusion value are output to DIO as digital signals. In order to realize the switching of test voltage, analog quantity input and digital quantity input or output, an interface board is designed and developed by ourselves, and its structural block diagram is shown in Figure 4. There are two DC/DC\'); companyAdEvent.show(this,\'companyAdDiv\',[5,18])"> DC/DC modules in the interface board, which are used to convert 24Vdc into 5Vdc and 12Vdc respectively. 5Vdc is used for the DIO of the multi-function acquisition card. In order to protect the NI PCI-6220 multi-function acquisition card, bidirectional input photoelectric isolation and NPN/PNP input selection switch are used for digital input, and 24 digital quantities are divided into 16 inputs and 8 outputs; the output part uses a Darlington driver module to drive the relay output. The test voltage requires an accuracy of 12±0.1V and 3.3±0.1V. Two voltage regulators and potentiometers are used to ensure that the test voltage is adjusted to 12V and 3.3 V. Yaskawa SGMGH series servo motors and SGDM series servo controllers are selected to maintain constant speed. The servo motor uses a 17-bit encoder and applies an internal speed control method. No other control modules are required to achieve testing under constant speed conditions.
Figure 4 Interface board structure diagram
Figure 5 is a flow chart of the test procedure, Figure 6 is a full diagram of the equipment, and the specific steps of the test are as follows.
Figure 5 Test procedure flow chart
Figure 6 Full view of the equipment
1 Start the program and initialize it, including reading parameter setting values, initializing arrays and clusters.
2 The test program scans the "test instruction" pulse signal every 50ms, and the pulse signal is maintained for at least 200ms. Once the "test instruction" pulse signal is scanned, the test begins.
3 The last test result must be cleared first.
4 Relays K1 and K13 on the interface board are powered on, the ABS
sensor
is connected
, and 12V voltage is applied to perform the first test and calculate the test value.
5 Relay K13 on the interface board remains connected to the ABS sensor, K1 is disconnected, the voltage is switched to 3.3V, the second test is performed, and the test value is calculated.
6 Summarize the calculation results and draw conclusions.
7 Output the calculation results and test conclusions, and send them to
the PLC
test completion and qualified I/O signals; display the calculation results and test conclusions on the main interface of the test software; save the calculation results with the time, date and barcode.
8 Wait for the feedback signal from PLC. If the "result received" signal is received from PLC within 3 seconds, return to step 2 and wait for the "test command" pulse signal to prepare for the next test; otherwise, an alarm will be issued. [page]
Programming points
The standard state machine of LabVIEW is used as a template, with a total of 19 boxes. Four clusters are established as data highways, namely: ABS and REF sequential comparison, parameter setting, calculation results and measured data. A total of 15 subroutines are called to complete functions such as testing, parameter setting and hardware testing.
The display screen can be switched between the four interfaces of "View Data", "First Waveform", "Second Waveform" and "Parameter Setting and Hardware Test". The default screen is "View Data", which is also the main interface, as shown in Figure 7. The calculated value of the required test items, the test results, and the number of tests, the number of qualified tests and the qualified rate after the program is run are displayed on the default screen. During the test, there is a test progress display. The ABS signal and REF signal waveforms of two consecutive tests are displayed in the "First Waveform" and "Second Waveform" screens. Figure 8 is the first test waveform. In the "Parameter Setting and Hardware Test" screen, authorized users can set parameters. Hardware testing can be performed when the system needs to be debugged. Data recording files are generated every day with the date as the prefix of the file, such as "2006-6-3_ABS".
Figure 7 Main interface
Figure 8 The first test waveform
The test data is saved together with the date, time and barcode of the tested piece in front of it. A row is added for each test. The data is stored in both the C and D disks, both of which are 80G, to ensure data security and facilitate data traceability. The data storage format is shown in Table 1. The record file can be viewed using Excel software.
Due to the fast acquisition speed, although in theory the rising and falling edges of the square wave signal are jumps, such as jumping from 0V to 5V, if this jump process is magnified many times, the intermediate value from 0V to 5V can be captured, which may be 2.7V, 3.5V, etc. It is a value similar to such a jump process, that is, the value of the peak or trough exceeding the limit. Through the analysis of the collected data, it is found that according to the required sampling rate and the frequency of the square wave, at most one intermediate value can be generated during the jump process. In this way, such intermediate values are identified and filtered in the program, which avoids false unqualified data from participating in the calculation. In addition, although from a macroscopic point of view: if the ABS sensor is qualified, the reference signal has 45 teeth, and the ABS should have 43 teeth. However, through the analysis of the paper model, it is found that at the moment of sampling, the relative state of the ABS or the reference signal (abbreviated as REF) is different, and the calculated value is different. That is, if the pulse sequence judgment result is that REF precedes ABS, then taking REF as the benchmark, when REF=46, ABS=43 is correct; if the pulse sequence judgment result is that ABS precedes REF, then taking ABS as the benchmark, when ABS=44, REF=45 is correct; if the pulse sequence judgment result is that ABS and REF arrive at the same time, then taking ABS as the benchmark, when ABS=43, REF=45 is correct.
Conclusion
Practice has proved that the graphical programming of LabVIEW 7.1 is easy to read and understand. The rich routines in the software are extremely useful for beginners. Practical decorative parts can make a beautiful and practical interface. Figure 9 is a LabVIEW block diagram program. At present, this ABS functional test system has been delivered for use. The system is technically reliable, stable in operation, and can ensure measurement accuracy. Compared with similar imported equipment, although the sampling rate of the acquisition card is 250kS/s, the A/D conversion resolution of the imported equipment is 12 bits, while the conversion resolution of NI PCI-6220 is 16 bits. In addition, the price of imported equipment is 3 or 4 times that of this system. The success of this system also saves users equipment investment.
Figure 9 LabVIEW block diagram program
Previous article:Solution for automobile reversing obstacle detection system
Next article:Design of sensing system based on light intensity sensor TSL256x
Recommended ReadingLatest update time:2024-11-17 03:30
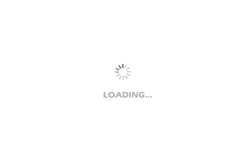
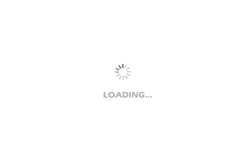
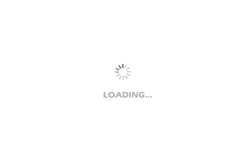
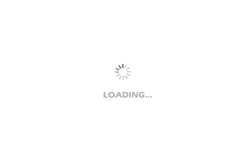
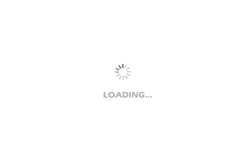
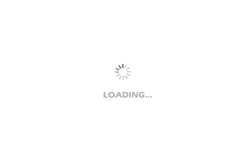
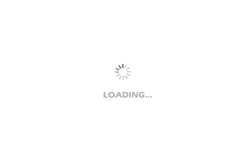
- Popular Resources
- Popular amplifiers
-
Analysis and Implementation of MAC Protocol for Wireless Sensor Networks (by Yang Zhijun, Xie Xianjie, and Ding Hongwei)
-
Introduction to Internet of Things Engineering 2nd Edition (Gongyi Wu)
-
西门子S7-12001500 PLC SCL语言编程从入门到精通 (北岛李工)
-
Modern Motor Control Technology (Wang Chengyuan, Xia Jiakuan, Sun Yibiao)
- Keysight Technologies Helps Samsung Electronics Successfully Validate FiRa® 2.0 Safe Distance Measurement Test Case
- From probes to power supplies, Tektronix is leading the way in comprehensive innovation in power electronics testing
- Seizing the Opportunities in the Chinese Application Market: NI's Challenges and Answers
- Tektronix Launches Breakthrough Power Measurement Tools to Accelerate Innovation as Global Electrification Accelerates
- Not all oscilloscopes are created equal: Why ADCs and low noise floor matter
- Enable TekHSI high-speed interface function to accelerate the remote transmission of waveform data
- How to measure the quality of soft start thyristor
- How to use a multimeter to judge whether a soft starter is good or bad
- What are the advantages and disadvantages of non-contact temperature sensors?
- Innolux's intelligent steer-by-wire solution makes cars smarter and safer
- 8051 MCU - Parity Check
- How to efficiently balance the sensitivity of tactile sensing interfaces
- What should I do if the servo motor shakes? What causes the servo motor to shake quickly?
- 【Brushless Motor】Analysis of three-phase BLDC motor and sharing of two popular development boards
- Midea Industrial Technology's subsidiaries Clou Electronics and Hekang New Energy jointly appeared at the Munich Battery Energy Storage Exhibition and Solar Energy Exhibition
- Guoxin Sichen | Application of ferroelectric memory PB85RS2MC in power battery management, with a capacity of 2M
- Analysis of common faults of frequency converter
- In a head-on competition with Qualcomm, what kind of cockpit products has Intel come up with?
- Dalian Rongke's all-vanadium liquid flow battery energy storage equipment industrialization project has entered the sprint stage before production
- Allegro MicroSystems Introduces Advanced Magnetic and Inductive Position Sensing Solutions at Electronica 2024
- Car key in the left hand, liveness detection radar in the right hand, UWB is imperative for cars!
- After a decade of rapid development, domestic CIS has entered the market
- Aegis Dagger Battery + Thor EM-i Super Hybrid, Geely New Energy has thrown out two "king bombs"
- A brief discussion on functional safety - fault, error, and failure
- In the smart car 2.0 cycle, these core industry chains are facing major opportunities!
- Rambus Launches Industry's First HBM 4 Controller IP: What Are the Technical Details Behind It?
- The United States and Japan are developing new batteries. CATL faces challenges? How should China's new energy battery industry respond?
- Murata launches high-precision 6-axis inertial sensor for automobiles
- Ford patents pre-charge alarm to help save costs and respond to emergencies
- Ntrip Communication Protocol 1.0
- [Perf-V Review] + Perf-V IDE driver and its problems
- Nios 2 software build tools for eclipse freezes when creating a project
- DC power supply design
- [Qinheng RISC-V core CH582] BUG serial port can only receive up to 8 bytes at a time
- Op amp offset voltage and single or dual power supply issues?
- Keysight Technologies' Thanksgiving Month Oscilloscope Award Photos
- Serial communication, 1-wire, TWI communication, what are the differences between these three communication methods? Who knows about it? Popular...
- Technical staff salary
- Precision Wide Bandwidth, RMS to DC Converter