1 Introduction
Failure of air-to-air missile test equipment will make it unusable or the detected parameters inaccurate, which will directly affect the combat readiness or combat support of air-to-air missiles. Therefore, it is necessary to repair the test equipment failure in a timely manner to ensure that the equipment is available at any time.
Air-to-air missile test equipment is a kind of optomechanical equipment, but its function is mainly reflected in the electronic circuit system, and its failure mainly occurs in the electronic circuit system, so its fault diagnosis problem is mainly the problem of electronic circuit fault diagnosis. Therefore, this article mainly discusses from the perspective of electronic circuit system fault diagnosis.
Judging from the current status of fault diagnosis of our military's air-to-air missile test equipment, there are still the following deficiencies:
(1) The test equipment still lacks effective status monitoring means, and faults cannot be discovered early;
(2) The fault diagnosis method is mainly manual diagnosis, and the test technicians rely on the data of the test instrument to diagnose the fault.
To this end, this paper first proposes that a two-level diagnostic instrument system should be established, and discusses the key technologies to be adopted; then discusses the theory and method of intelligent diagnosis to further improve the diagnostic ability of diagnostic instruments; finally points out the future research direction.
2 Diagnostic instrument system
Fault diagnosis requires certain instrument support. The diagnostic instrument system refers to the types of diagnostic instruments determined according to maintenance characteristics, maintenance system and diagnostic requirements.
The air-to-air missile test equipment has a modular, plug-in structure and can be quickly repaired by replacing modules or plug-ins, which is its maintenance feature.
From the maintenance system point of view, the air-to-air missile test equipment implements a two-level maintenance system: grassroots and base-level maintenance. Grassroots-level maintenance is mainly based on parts replacement repair, and the diagnosis target is the replaceable unit (plug-in). Base-level maintenance is mainly based on plug-in repair, and the diagnosis target is the replaceable component. In wartime, forward repair is implemented to ensure the use of the equipment.
Based on the above characteristics, it is believed that the fault diagnosis system of air-to-air missile test equipment should establish two levels of diagnostic instruments:
(1) System-level fault diagnosis instrument. Its diagnostic goal is to timely discover the faulty operating status of the equipment and locate the fault to the replaceable plug-in. The system-level fault diagnosis instrument can be implemented by BIT.
(2) Plug-in-level fault diagnosis instrument. Its goal is to further locate the replaced faulty plug-in to the replaceable component. It can generally be called a plug-in fault diagnosis instrument.
Therefore, the fault diagnosis instrument of air-to-air missile test equipment is composed of system-level and plug-in-level fault diagnosis instruments, forming a two-level instrument system.
3 System-level fault diagnosis instrument
The system-level fault diagnosis instrument runs simultaneously with the test equipment, and it should reflect the working condition of the test equipment in a timely manner. Its important design technology is the built-in test (BIT) technology.
BIT technology is a key common technology in the overall design, subsystem design, condition monitoring, fault diagnosis, maintenance decision-making, etc. of complex weapon equipment. It has the advantages of improving the accuracy of fault diagnosis, significantly shortening maintenance time, reducing maintenance costs and the skill requirements for maintenance personnel.
The key to BIT is the selection of test points. The basic principle of selection is that the test points should be able to ensure the best BIT fault detection rate and isolation rate. Generally, there are three types of test points: passive, active, and passive and active test points [1].
Different strategies are used to develop system-level diagnostic instruments for equipment at different life stages:
(1) For newly designed equipment, the BIT system is designed together with the test system during the design phase to improve the inherent condition monitoring and fault diagnosis capabilities of the equipment.
(2) For equipment already in service, system modification can be combined with equipment overhaul to improve condition monitoring and fault diagnosis capabilities. Modification should be carried out on the basis of sufficient demonstration and practice.
In response to the situation that a certain type of air-to-air missile test equipment has insufficient self-test function and lacks condition monitoring, references [2][3] designed a condition monitoring and fault diagnosis system. Its structure is shown in Figure 2. It is a system-level fault diagnosis instrument.
4 Plug-in level fault diagnosis instrument
The plug-in is a printed circuit board (PCB), which is generally composed of analog and digital circuits. Its fault diagnosis is a mixed diagnosis problem. The test instruments used for plug-in fault diagnosis can be divided into two types: diagnostic instruments based on component testing and diagnostic instruments based on board-level I/O testing.
A diagnostic instrument based on component testing is also called an online tester. It mainly uses related technologies such as post-drive, and can directly test the components on the circuit board when the circuit board is not working, determine their quality, function and model, so as to conveniently and quickly perform first-level device maintenance on various complex circuits [4]. Post-drive technology is also called "strong drive", "reverse drive" or "overdrive" technology. Its main design concept is to use transient large signals to isolate the influence of other devices on the device under test, so as to achieve the purpose of applying test codes to the device under test. The function of the online tester is ideal, but it also has disadvantages such as high price, relatively complex operation, and possible damage to components caused by post-drive. It is more suitable for base maintenance. [page]
Diagnostic instruments based on board-level I/O testing, under the control of a computer, apply stimulus to the circuit plug-in port in accordance with the requirements of the test program set (TPS), measure the corresponding response, and compare it with the TPS result to complete the detection and location of the fault. The plug-in of air-to-air missile test equipment generally has a unified interface, and the plug-in can be connected to the diagnostic instrument through a unified adapter. Since most operations are automatically performed under the control of a computer, it is very simple to use and suitable for on-site troubleshooting.
Using TPS to automatically test circuit boards is currently a relatively advanced method in the world. However, the development of TPS is a task that requires a lot of manpower and material resources. In order to reduce the difficulty of TPS development and improve development efficiency, the use of software simulation tools to develop test programs has become the mainstream technology for TPS development. For example, the simulation software LASAR (Logic Automatic Stimulus and Response) is used for digital circuit test development and logic analysis [5]. In addition, commonly used EDA software such as Protel and OrCAD also have circuit simulation functions, which can be used to assist in the development of TPS.
During the specific design, attention should be paid to the comprehensive use of advanced technologies to develop the diagnostic instrument hardware platform in the direction of standardization and universalization, and to engineer the test software and unify the test software platform[6].
Reference [7] proposed a design of an air-to-air missile tester plug-in fault diagnosis instrument based on board-level I/O testing. The overall scheme is shown in Figure 1.
The diagnostic instrument adopts a structural system of upper and lower computers, which has the advantages of flexible control, simplicity and low cost.
5. Intelligent Diagnosis
At present, the methods used for system fault diagnosis can be divided into two categories: traditional diagnosis methods based entirely on detection data processing and intelligent diagnosis methods based on knowledge processing [8]. Intelligent diagnosis is the development of traditional diagnosis methods. It is based on knowledge processing technology and realizes the integration of dialectical logic and mathematical logic, the unification of symbolic processing and numerical processing, the unification of reasoning process and algorithmic process, and the interaction between knowledge base and database [9].
Diagnostic expert system is the earliest and most mature intelligent diagnosis method. Expert system is generally composed of knowledge base, inference engine, comprehensive database, interpretation program, knowledge acquisition program and human-computer interface. Reference [2][3] proposed the structure of an air-to-air missile tester fault diagnosis expert system, as shown in Figure 2.
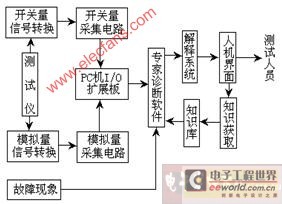
Reference [10] elaborated on the establishment and maintenance of a knowledge base for air-to-air missile test equipment fault diagnosis based on production rules, and reference [11] made a useful discussion on the establishment of a certain type of missile detection equipment fault diagnosis expert system.
To improve the fault diagnosis capability of diagnostic instruments, it is necessary to apply intelligent diagnosis theory and methods in diagnostic instruments. The theory and methods of intelligent diagnosis are still under continuous development and improvement, and there is still a long way to go before they can be applied to the fault diagnosis of air-to-air missile test equipment.
6 Summary and Outlook
This paper introduces the establishment and design practice of the system architecture of air-to-air missile test equipment fault diagnosis instrument based on specific models. In the fault diagnosis of air-to-air missile test equipment, the use of system-level and plug-in-level fault diagnosis instruments is a reasonable instrument system.
There is still a lot of work to be done to finally solve the problem of fault diagnosis of air-to-air missile test equipment. In the future, we should pay attention to the following points:
(1) From the perspective of the diagnostic system design process, we should carry out testability design of the equipment during the equipment design stage to improve the testability of the equipment; during the equipment use stage, we should redesign the diagnostic system to further improve the diagnostic capability.
(2) From the perspective of diagnostic theory and methods, we should comprehensively use data-based diagnosis and knowledge-based diagnosis.
(3) From the perspective of diagnostic technology, we should pay attention to the use of the achievements of modern information technology to realize remote and networked diagnosis.
Previous article:Field effect tube detection method and related testing experience
Next article:Classification of measurement methods and use of measuring instruments
- Popular Resources
- Popular amplifiers
- Keysight Technologies Helps Samsung Electronics Successfully Validate FiRa® 2.0 Safe Distance Measurement Test Case
- From probes to power supplies, Tektronix is leading the way in comprehensive innovation in power electronics testing
- Seizing the Opportunities in the Chinese Application Market: NI's Challenges and Answers
- Tektronix Launches Breakthrough Power Measurement Tools to Accelerate Innovation as Global Electrification Accelerates
- Not all oscilloscopes are created equal: Why ADCs and low noise floor matter
- Enable TekHSI high-speed interface function to accelerate the remote transmission of waveform data
- How to measure the quality of soft start thyristor
- How to use a multimeter to judge whether a soft starter is good or bad
- What are the advantages and disadvantages of non-contact temperature sensors?
- Innolux's intelligent steer-by-wire solution makes cars smarter and safer
- 8051 MCU - Parity Check
- How to efficiently balance the sensitivity of tactile sensing interfaces
- What should I do if the servo motor shakes? What causes the servo motor to shake quickly?
- 【Brushless Motor】Analysis of three-phase BLDC motor and sharing of two popular development boards
- Midea Industrial Technology's subsidiaries Clou Electronics and Hekang New Energy jointly appeared at the Munich Battery Energy Storage Exhibition and Solar Energy Exhibition
- Guoxin Sichen | Application of ferroelectric memory PB85RS2MC in power battery management, with a capacity of 2M
- Analysis of common faults of frequency converter
- In a head-on competition with Qualcomm, what kind of cockpit products has Intel come up with?
- Dalian Rongke's all-vanadium liquid flow battery energy storage equipment industrialization project has entered the sprint stage before production
- Allegro MicroSystems Introduces Advanced Magnetic and Inductive Position Sensing Solutions at Electronica 2024
- Car key in the left hand, liveness detection radar in the right hand, UWB is imperative for cars!
- After a decade of rapid development, domestic CIS has entered the market
- Aegis Dagger Battery + Thor EM-i Super Hybrid, Geely New Energy has thrown out two "king bombs"
- A brief discussion on functional safety - fault, error, and failure
- In the smart car 2.0 cycle, these core industry chains are facing major opportunities!
- The United States and Japan are developing new batteries. CATL faces challenges? How should China's new energy battery industry respond?
- Murata launches high-precision 6-axis inertial sensor for automobiles
- Ford patents pre-charge alarm to help save costs and respond to emergencies
- New real-time microcontroller system from Texas Instruments enables smarter processing in automotive and industrial applications
- 【EasyARM-RT1052 Review】+ MQTTClient transplantation
- EEWorld adds double bonus to ELEXCON Shenzhen International Electronics Exhibition and sincerely invites you to participate
- The 32.768K crystal does not vibrate, so the selection is very important!
- Without calibration before testing, how much do you know about the real results?
- A set of common codes suitable for small projects
- C2000 Key Technology Guide
- MicroPython upgraded to v1.14
- Baby education is a bit difficult...
- What TI DSP Power Knows
- Xilinx FPGA Development Tools