For mobile phone products, using low-cost components in design is only the first step to make the price competitive. The cost of the production process, especially the cost incurred during the final test process, has an equally important impact on the final product price. Moreover, design engineers often underestimate the cost added by the production process. For these reasons, production engineers and design engineers must work closely together to ensure that production cost targets are accurately achieved.
Design a good test process
For production engineers, it is necessary to optimize the production process and design the corresponding test process to ensure that the products produced meet the technical specifications. In other words, the hardware components work properly and are correctly connected and calibrated. However, production testing is not to repeat the comprehensive type approval test including many software tests. This is because the software does not change much between different products in the same series.
As we all know, time is money. This is especially true on the production line, so production engineers need to identify the components and circuits that are most critical to performance. Then, they design tests that are as non-repetitive as possible to fully test these most critical components and circuits to ensure that the mobile phone meets quality standards when it leaves the factory. In addition, separate troubleshooting tests are no longer required during the life of the mobile phone, thereby improving productivity.
Of course, the specific tests still depend on the quality of each design. The simplest case is to perform functional testing through a call mode including the call establishment process. This pass/no-go test usually covers all components of the mobile phone, including antennas, power amplifiers, receivers, oscillators, mixers and audio components. This functional test is usually performed at the last stage of the production process before the product is packaged, and generally includes measurements of power accuracy, frequency error and receiver sensitivity.
If there is a separate RF connector, then these functional tests can be completed through the RF connector. The advantage of this is high accuracy and good repeatability. However, it is not enough to just provide a test connector. It is also not okay to ignore the antenna test, because this may result in the antenna being poorly soldered and not being detected.
It is possible to further reduce production costs by using cheaper components with wide tolerances, but additional electronic adjustment and calibration processes are required at the end of the production process to achieve the required accuracy. Therefore, this approach requires a balance between the cost of the components and the additional cost of measurement and adjustment.
The most common adjustment process in the production of mobile phones is the adjustment of the power amplifier, because the gain of the power amplifier is often nonlinear. The transmit power of the mobile phone must comply with certain transmit power levels specified by the standard, with small deviations and high accuracy. Therefore, the communication test device must test the output power of the mobile phone at all possible transmit power levels. The control computer compares each measured value with the normalized output power, calculates the correction value and sends it to the mobile phone, which stores the correction value. For each frequency band supported by the mobile phone, this test must be repeated at several frequency points.
Since the output power level needs to be calibrated at 6 to 12 frequencies, the entire process can be very time consuming and can create a costly bottleneck on the production line. Therefore, the phone must be able to cycle through all power levels as quickly as possible, and the test equipment must also synchronize with the changes in power levels so that the test results can be easily correlated to the corresponding power level.
Receiving and transmitting circuit testing is important
Before production testing, components are installed, the PCB is connected to a power source, and software is downloaded. A comprehensive test is first performed to ensure that components and connections are working properly, including testing the current under different conditions to determine if there are any short circuits. During the receive circuit test, the received signal strength indicator (RSSI) circuit is very important to ensure accurate gain. The RSSI circuit generally requires calibration. Finally, the electronic correction circuit is adjusted. If the test fails, the board is removed from the production line and enters the repair cycle.
Adjusting and calibrating equipment must be fast and accurate enough, otherwise the calibration process may take too long. The calibration process usually takes 10 seconds to 2 minutes, but if the design process of the mobile phone is not designed for testing, the calibration process may be extended to 10 minutes or even 15 minutes.
In addition, if the initial software download only includes the test program, then the end-user application must be downloaded next. When the software and all the shells are installed, the final functional test can be carried out, mainly measuring the transmit and receive circuits and overall functions. The measurement parameters of the transmit circuit mainly include power level, frequency error and modulation quality.
It is not practical to add more test steps beyond these two steps, because connecting the PCB circuit board or mobile phone to the test equipment will extend the test time. Therefore, the value of assembly line measurement is not great. Of course, different types of test equipment can be installed in other production steps, but most production engineers currently choose to minimize the number of different types of instruments installed on the production line.
In contrast, a high-quality, fully functional test set that can be used to test different technologies helps maintain a stable test environment in a rapidly changing environment, shortens the time required to troubleshoot problems when they occur, and minimizes the number of spare devices required. It is best if the communication test set itself can provide a test language so that automation can be achieved during the test and repair process.
Depending on the target test needs, tests and measurements can be performed in call mode, non-call mode (test mode). Comprehensive functional tests should be performed in call mode. To save time, other tests can be completed in test mode. In addition, some test equipment also provides a simplified call mode, in which the test process is carried out through a service channel between the tester and the mobile phone that does not include the call establishment process. The test equipment required in production should include a high-speed and high-precision communication test device that can simulate a base station. The communication test device should be able to provide most of the functions of RF and voice testing. In addition, the current development trend is to use small general-purpose test systems. Such small general-purpose test systems only include a few instruments, sometimes including power supplies and ammeters.
Previous article:Basic knowledge of LTE testing technology
Next article:User-oriented testing research
Recommended ReadingLatest update time:2024-11-16 15:47
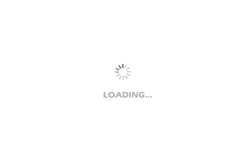
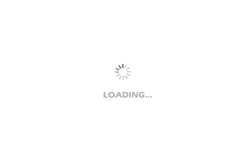
- Keysight Technologies Helps Samsung Electronics Successfully Validate FiRa® 2.0 Safe Distance Measurement Test Case
- From probes to power supplies, Tektronix is leading the way in comprehensive innovation in power electronics testing
- Seizing the Opportunities in the Chinese Application Market: NI's Challenges and Answers
- Tektronix Launches Breakthrough Power Measurement Tools to Accelerate Innovation as Global Electrification Accelerates
- Not all oscilloscopes are created equal: Why ADCs and low noise floor matter
- Enable TekHSI high-speed interface function to accelerate the remote transmission of waveform data
- How to measure the quality of soft start thyristor
- How to use a multimeter to judge whether a soft starter is good or bad
- What are the advantages and disadvantages of non-contact temperature sensors?
- Innolux's intelligent steer-by-wire solution makes cars smarter and safer
- 8051 MCU - Parity Check
- How to efficiently balance the sensitivity of tactile sensing interfaces
- What should I do if the servo motor shakes? What causes the servo motor to shake quickly?
- 【Brushless Motor】Analysis of three-phase BLDC motor and sharing of two popular development boards
- Midea Industrial Technology's subsidiaries Clou Electronics and Hekang New Energy jointly appeared at the Munich Battery Energy Storage Exhibition and Solar Energy Exhibition
- Guoxin Sichen | Application of ferroelectric memory PB85RS2MC in power battery management, with a capacity of 2M
- Analysis of common faults of frequency converter
- In a head-on competition with Qualcomm, what kind of cockpit products has Intel come up with?
- Dalian Rongke's all-vanadium liquid flow battery energy storage equipment industrialization project has entered the sprint stage before production
- Allegro MicroSystems Introduces Advanced Magnetic and Inductive Position Sensing Solutions at Electronica 2024
- Car key in the left hand, liveness detection radar in the right hand, UWB is imperative for cars!
- After a decade of rapid development, domestic CIS has entered the market
- Aegis Dagger Battery + Thor EM-i Super Hybrid, Geely New Energy has thrown out two "king bombs"
- A brief discussion on functional safety - fault, error, and failure
- In the smart car 2.0 cycle, these core industry chains are facing major opportunities!
- The United States and Japan are developing new batteries. CATL faces challenges? How should China's new energy battery industry respond?
- Murata launches high-precision 6-axis inertial sensor for automobiles
- Ford patents pre-charge alarm to help save costs and respond to emergencies
- New real-time microcontroller system from Texas Instruments enables smarter processing in automotive and industrial applications
- Are there any good EDA design tool manufacturers in China?
- How do I delete a post?
- Infrared remote control
- EEWORLD University ---- Introduction to the internal structure of FPGA (Intel official tutorial)
- EEWORLD University Hall----Live Replay: Keysight High-Speed Oscilloscope Basics and Keysight's New Oscilloscope Analysis
- Micropython-Editor that can embed Micropython
- TVS Tube Selection
- Msp430f5529 car source code exchange
- Let's take a look at domestic chip tubes and imported chip tubes
- Application of Zigbee in Traffic Light Control