Nowadays, with the continuous emergence of new technologies and the continuous increase of new demands in various industries, the pace of launching more differentiated products into the market is also accelerating. These products not only integrate more functions, but also must shorten the development cycle in order to gain an advantage in the competition with similar products. At the same time, all companies are also facing more stringent cost control requirements, and the requirements for test speed have become higher. All of these require the rapid development of efficient and flexible test systems.
The modular system architecture with software as the core is an innovative solution to the above test challenges. Test engineers can use easy-to-use, clearly structured software tools and flexible modular hardware to create a completely user-defined test system. As a professional company with more than 30 years of experience in the field of test and measurement, NI provides efficient platforms and tools for users around the world to build automated systems. The design involves industries such as electronics, semiconductors, automobiles, defense and aerospace, and has accumulated rich experience.
This article will discuss in detail how to build a modular test system with software as the core from two aspects: modular hardware platform and software tools to improve development efficiency.
Modular Hardware I/O
Today, product design is becoming increasingly complex. The emergence of new standards and protocols (such as radio frequency communication protocols) has brought many new challenges to testing. Therefore, in order to achieve better flexibility and upgradeability, the test system is gradually moving towards modularization and small size, that is, simplifying the complex test system into modular hardware I/O to implement one by one: when additional test items need to be added, only the corresponding functional modules need to be added to meet future upgrade needs. The US Department of Defense, which is considered one of the most conservative customers, also emphasized in a report submitted to Congress as early as 2002: The next generation of test systems must be modular hardware based on readily available commercial technology to facilitate the interchange and upgrade of equipment.
The construction of a complete automated test system should follow the five-layer architecture shown in Figure 1. Modular I/O is located at the bottom of the five-layer architecture of the entire automated test system. It will directly contact the actual physical signal to complete signal conditioning and signal digitization. These modular I/Os are mainly instruments based on PXI or PCI buses. With the rapid development of semiconductor technology, high-performance test and measurement work can be completed in a very small volume at a low cost. Figure 2 shows the performance comparison between modular digitizers and traditional instruments. The flexibility, user customization and scalability provided by modular instruments, combined with the powerful active role of software, reflect the huge advantages that traditional instruments cannot match.
Figure 1: The five-layer architecture of a modular test system with software as the core.
Figure 2: Modular I/O performance comparison with traditional instrumentation.
The core component of every automated test system is a computer (including desktop computers, server workstations, laptops or embedded computers, etc.). The widespread use of PCs has led to the continuous advancement of high-performance internal buses. Among them, the PCI and PCI Express buses have the lowest latency and the highest data throughput or bandwidth. The PCI Express bus further expands the bandwidth of the PCI bus to meet the growing bandwidth requirements. At the same time, it is also fully compatible with the PCI bus in software, as shown in Figure 3.
Figure 3: Comparison of data bandwidth and latency of various industrial buses.
The PXI (PCI eXtensions for Instrumentation) standard combines the CompactPCI standard with a dedicated synchronization bus and software features, adding integrated timing and synchronization functions, industrial-grade rugged design, and more channels to the PC-based automated test, measurement, and control system architecture.
In fact, PXI has become the mainstream modular test system. There are now more than 70 PXI System Alliances (PXISA) providing more than 1,500 PXI modular instruments, including many well-known companies such as NI, Agilent, ADLINK and Pickering, with products covering various I/O modules from digitizers, signal generation, RF, power supplies to switch modules.
The open PXI/PXI Express platform also provides standard hardware and software for communicating with VXI systems or discrete instruments, including GPIB, USB, LAN, serial ports and other interfaces (Figure 4). In fact, many actual test systems are not based on a single bus system, but a hybrid bus system, such as: there are both PXI devices and traditional instruments based on GPIB, but PXI is more suitable as the core of such a hybrid bus system. On the one hand, as an internal bus, PXI has the highest data transmission rate and the lowest latency, thus ensuring that it will not become a bottleneck for data transmission in the entire system; on the other hand, the hardware of the PXI platform is based on standard PC technology (such as PCI/PCI Express bus, general CPU and peripheral devices, and the mainstream Windows software architecture is also very familiar to users). The development and operation of automated test systems based on PXI systems is as convenient as using standard Windows-based PCs, and it is also easy to maintain and upgrade.
Figure 4: An automated test system built around PXI. [page]
Software tools for rapid development
The software definition of the automated test system with software as the core is self-evident in its role and status in building the entire test system. Compared with the fixed functional configuration of traditional instruments and the presentation of only "test results", software definition can meet the user's complete customization of the test system. By defining the functions of modular hardware through software, the same digitizer can realize different functions such as oscilloscope, spectrum analyzer and video analyzer; in addition, customized data analysis can be realized through software. For example, by designing different modulation and demodulation methods based on modular RF hardware, the test requirements of various RF standards can be met; customized user interfaces can also be created through software to ensure the friendliness of human-computer interaction.
It can be seen that software definition runs through the entire process of building an automated test system. Using software tools with clear structure, flexibility and ease of use can accelerate the entire development process and shorten the development cycle. As shown in Figure 1, the architecture of building an automated test system with software as the core includes three levels.
The system service and driver layer is the link between the software development environment and the hardware devices. In addition to serving as a device driver, this layer also includes functions such as hardware device management and diagnostic testing. For example, NI's Measurement and Automation Explorer (MAX) software can help developers perform unified automatic detection and configuration management for all NI hardware and many traditional instruments connected through the instrument bus. Its integrated diagnostic test function can help developers separate software and hardware for debugging and quickly find the crux of the problem. At the same time, the test panel can help users quickly check the hardware functions. System services and drivers also provide integration of the test application development software layer through the application programming interface (API). In this way, developers can easily implement device-specific programming, thereby improving development efficiency and reducing maintenance costs.
Test application development software (ADE) plays a connecting role in the test software architecture. When designing and assembling the system, system developers need to use ADE to implement specific measurement applications, display necessary information to end users, connect other applications and other functions; at the same time, ADE needs to be tightly integrated with the system service and driver layer to achieve seamless connection with the hardware. In addition, ADE used to develop measurement and automation applications needs to provide easy-to-use design models and ready-made processing algorithms for various application fields, thereby further improving developer efficiency.
As the importance of software in system implementation continues to increase, developers will spend most of their time on application development. Therefore, the quality of an application development software tool directly affects the success of the entire system development. NI graphical programming software LabVIEW provides users with efficient and intuitive test and measurement application development tools. Combined with seamlessly connected NI device drivers and built-in signal processing algorithms, users can obtain raw measurement data from instrument I/O and obtain measurement results through a variety of readily available analysis function toolkits. In addition, for users who are accustomed to text programming, they can choose NI LabWindows/CVI based on ANSI C or NI Measurement Studio software based on Microsoft Visual Studio. In addition, for specific applications, NI also provides some configuration-based development software to accelerate the user's development process. For example, NI VideoMASTER for video testing, NI VeriStand for real-time testing and hardware-in-the-loop simulation, and NI Vision Builder for Automated Inspection for automatic detection. Based on these software tools, users can achieve rapid development without programming, or combine LabVIEW for more in-depth customization. NI not only provides the development environment for these software, but also provides ready-made algorithm IPs for accelerated development for different applications, thereby further accelerating the development of engineering applications. In addition, based on NI's open software platform, you can also use ready-made algorithms developed in various third-party software environments.
The system management software layer is located at the top of the software architecture hierarchy. For an automated test system, some test tasks will vary depending on the device under test (DUT), such as instrument configuration, result analysis, etc., while some test tasks are universal, such as test process management, test report generation, etc. In order to further improve test efficiency and reduce software maintenance costs, a test strategy that separates DUT-level tasks from system-level tasks is particularly critical. By quickly creating test processes, integrating report generation and database management functions, and establishing human-machine interfaces for users at different levels, test management software can help users significantly shorten software development time and quickly reuse, modify, and maintain test programs (or modules) throughout the development cycle to meet different needs from DUT testing to entire ATE system testing. In addition to providing the above functions, professional test management software (such as NI TestStand) can also help users significantly improve test efficiency and increase system throughput with built-in parallel and automatic coordination test tools.
Conclusion
Today, tens of thousands of companies have achieved success by using software-based automated test systems. For example, Honeywell's new FCT system based on NI PXI and LabVIEW has significantly reduced the cost of test instruments, system size, and the burden on engineers; Microsoft's test system designed for the Xbox 360 controller based on LabVIEW and modular instruments is twice as fast as the previous generation of test systems; Hualu Panasonic used NI TestStand, NI LabVIEW, and modular instruments to develop a complete automated test system for the new DVD burner, greatly improving test efficiency. The modular automated test system with software as the core overcomes the shortcomings of previous solutions based on independent desktop instruments or expensive private ATE systems, allowing engineers to develop scalable test systems and tightly integrate instruments of various buses. In addition, it allows engineers to integrate existing equipment investments to reduce the initial cost of implementation, and based on this architecture, the latest commercial technologies can be introduced into the test system to create new applications. These applications include parallel testing based on multi-core processors, custom instrument design based on FPGA, high-speed streaming of test data based on PXI Express bus and disk array technology, and so on. I believe that modular architecture with software as the core will continue to be the mainstream of testing technology in the future, and will be able to continue to penetrate into each testing field and expand new application directions.
Previous article:How to perform voltage transient testing on automotive electronics
Next article:How to measure battery charge
Recommended ReadingLatest update time:2024-11-17 07:58
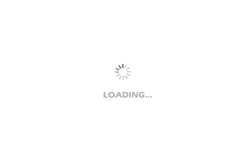
- Keysight Technologies Helps Samsung Electronics Successfully Validate FiRa® 2.0 Safe Distance Measurement Test Case
- From probes to power supplies, Tektronix is leading the way in comprehensive innovation in power electronics testing
- Seizing the Opportunities in the Chinese Application Market: NI's Challenges and Answers
- Tektronix Launches Breakthrough Power Measurement Tools to Accelerate Innovation as Global Electrification Accelerates
- Not all oscilloscopes are created equal: Why ADCs and low noise floor matter
- Enable TekHSI high-speed interface function to accelerate the remote transmission of waveform data
- How to measure the quality of soft start thyristor
- How to use a multimeter to judge whether a soft starter is good or bad
- What are the advantages and disadvantages of non-contact temperature sensors?
- Innolux's intelligent steer-by-wire solution makes cars smarter and safer
- 8051 MCU - Parity Check
- How to efficiently balance the sensitivity of tactile sensing interfaces
- What should I do if the servo motor shakes? What causes the servo motor to shake quickly?
- 【Brushless Motor】Analysis of three-phase BLDC motor and sharing of two popular development boards
- Midea Industrial Technology's subsidiaries Clou Electronics and Hekang New Energy jointly appeared at the Munich Battery Energy Storage Exhibition and Solar Energy Exhibition
- Guoxin Sichen | Application of ferroelectric memory PB85RS2MC in power battery management, with a capacity of 2M
- Analysis of common faults of frequency converter
- In a head-on competition with Qualcomm, what kind of cockpit products has Intel come up with?
- Dalian Rongke's all-vanadium liquid flow battery energy storage equipment industrialization project has entered the sprint stage before production
- Allegro MicroSystems Introduces Advanced Magnetic and Inductive Position Sensing Solutions at Electronica 2024
- Car key in the left hand, liveness detection radar in the right hand, UWB is imperative for cars!
- After a decade of rapid development, domestic CIS has entered the market
- Aegis Dagger Battery + Thor EM-i Super Hybrid, Geely New Energy has thrown out two "king bombs"
- A brief discussion on functional safety - fault, error, and failure
- In the smart car 2.0 cycle, these core industry chains are facing major opportunities!
- Rambus Launches Industry's First HBM 4 Controller IP: What Are the Technical Details Behind It?
- The United States and Japan are developing new batteries. CATL faces challenges? How should China's new energy battery industry respond?
- Murata launches high-precision 6-axis inertial sensor for automobiles
- Ford patents pre-charge alarm to help save costs and respond to emergencies
- I would like to ask how to set up Xnet in allegro
- The problem of STM8L151k4t6 with programmed code being damaged by soldering?
- DSP28335 external interrupt configuration process
- Electromagnetic compatibility design and rectification countermeasures and case analysis
- Award-winning live broadcast: TI DLP technology innovation and new applications in automobiles, 10-year DLP senior engineer explains for you
- Two Application Examples of EPROM in Single Chip Microcomputer Development
- [Erha Image Recognition Artificial Intelligence Vision Sensor] Evaluation 1: Winner Chip Level Evaluation
- What is Wi-Fi 6?
- 51 MCU software sharing, friends who want it can download it
- 【NUCLEO-L552ZE Review】+ Unboxing and lighting