1. Sensors
According to the national standard GB7665-87, sensors are defined as devices that can sense the specified measured quantity and convert it into a usable output signal according to certain rules. As a detection tool, sensors are required to detect the physical or chemical information of the research object. Their working process requires stability, reliability and high precision. Therefore, there are several requirements for sensors:
(1) Strong ability to adapt to harsh environments - sensors generally work in a wide range of environments, from extremely cold to hot areas. Many work in open air environments. They can resist flying sand and stones, dust, and should also be resistant to moisture. They should have high resistance to salt corrosion and acid corrosion, and have the ability to resist interference from polluted gases. They can adapt to high temperature, extreme cold, strong vibration, impact and other conditions. They should also have strong noise resistance and high signal-to-noise ratio.
(2) Moderate price, suitable for mass production - sensors are required to have good consistency and be suitable for automated mass production. They have high requirements for processing equipment to eliminate inconsistencies and errors caused by manual operation.
(3) High stability and reliability - sensors are high-precision detection instruments. There are strict requirements for their application in military, aviation and aerospace. Products must undergo rigorous testing before they can be used. Therefore, sensor production is a specific application and embodiment of high-tech. Whether a sensor has a high technical added value is reflected in whether the technical content and processing technology contained in it are high-tech. Some sensors need metal packaging due to the conditions of their application environment, and generally use welding sealing, such as pressure sensors, force sensors, Hall sensors, photoelectric sensors, temperature sensors, etc. These sensors have sensitive components and integrated circuits inside, which are filled with inert gas or vacuumed to isolate them from the outside world. They have pressure resistance and airtightness requirements, as well as welding strength requirements and leakage rate requirements. They have high requirements for welding quality, and require small deformation during welding, and cannot damage internal components and microcircuits. At present, sensor sealing welding includes resistance welding, tungsten inert gas welding, plasma arc welding, electron beam welding and laser welding.
2. Laser welding
1. Principle of laser welding-Laser is the abbreviation of stimulated emission of radiation. Due to its unique high brightness, high directivity, high monochromaticity and high coherence, it has been widely used in industrial processing since its birth, and has become a common processing method for future manufacturing systems. Laser welding uses a high-intensity laser beam. After the laser beam is focused by an optical system, the power density of the laser focus is 104~107W/cm2. The workpiece is placed near the laser focus for heating and melting. Whether the melting phenomenon can occur and the intensity of the melting phenomenon mainly depends on the time, power density and peak power of the laser acting on the surface of the material. By controlling the above parameters, lasers can be used for various welding processes.
2. General characteristics of laser welding - Laser welding is a thermal processing technology that uses a laser beam as a heat source. Compared with electron beams, plasma beams and general mechanical processing, it has many advantages: (1) The laser focus spot of the laser beam is small and the power density is high, which can weld some high-melting-point, high-strength alloy materials; (2) Laser welding is a non-contact process, without problems such as tool loss and tool replacement. The laser beam energy and moving speed are adjustable, and a variety of welding processes can be performed; (3) Laser welding has a high degree of automation and can be controlled by a computer. It has a fast welding speed and high efficiency, and can easily weld any complex shape; (4) The heat-affected zone of laser welding is small, the material deformation is small, and no subsequent process processing is required; (5) Laser can weld workpieces in a vacuum container and workpieces in a complex structure through glass; (6) The laser beam is easy to guide and focus, and can achieve changes in all directions; (7) Compared with electron beam processing, laser welding does not require a strict vacuum equipment system and is easy to operate; (8) Laser welding has high production efficiency, stable and reliable processing quality, and good economic and social benefits.
3. Process characteristics of laser welding in sensor production - Laser is used to seal the metal shell of the sensor, which is currently one of the most advanced processing methods, mainly based on the following characteristics of laser welding: (1) High aspect ratio. The weld is deep and narrow, and the weld is bright and beautiful; (2) Minimum heat input. Due to the high power density, the melting process is extremely fast, the heat input to the workpiece is very low, the welding speed is fast, the thermal deformation is small, and the heat-affected zone is small; (3) High density. During the weld formation process, the molten pool is constantly stirred, and gas is easily released, resulting in a pore-free, fully penetrated weld. The high cooling rate after welding can easily make the weld microstructure finer, and the weld strength, toughness and comprehensive performance are high; (4) Strengthen the weld. The high temperature heat source and the full absorption of non-metallic components produce a purification effect, reducing the impurity content, changing the size of inclusions and their distribution in the molten pool. No electrodes or filler wires are required during the welding process, and the molten zone is less contaminated, making the weld strength and toughness at least equivalent to or even exceeding that of the parent metal; (5) Precise control. Because the focused spot is very small, the weld can be positioned with high precision, the beam is easy to transmit and control, and there is no need to frequently replace the welding torch and nozzle, which significantly reduces downtime and auxiliary time, has high production efficiency, has no inertia, and can be stopped and restarted at high speed. The use of self-controlled beam movement technology can weld complex components; (6) Non-contact, atmospheric environment welding process. Because the energy comes from the laser, there is no physical contact between the workpiece and the workpiece, so no force is applied to the workpiece. In addition, magnetism and air have no effect on lasers; (7) Due to the low average heat input and high processing accuracy, the cost of reprocessing can be reduced. In addition, the operating cost of laser welding is low, which can reduce the cost of workpieces; (8) It is easy to realize automation, and the beam intensity and fine positioning can be effectively controlled.
III. Comparison of laser welding with existing welding methods
The methods currently used for sensor sealing welding include: resistance welding, argon arc welding, electric beam welding, plasma welding, etc.
1. Resistance welding: It is used to weld thin metal parts. The workpiece to be welded is clamped between two electrodes and a large current is passed to melt the surface contacted by the electrodes, that is, welding is carried out by heating the workpiece with resistance. The workpiece is easy to deform. Resistance welding welds both sides of the joint, while laser welding is only carried out from one side. The electrodes used for resistance welding need to be maintained frequently to remove oxides and metal adhered from the workpiece. Laser welding thin metal lap joints does not contact the workpiece. Moreover, the beam can also enter areas that are difficult to weld with conventional welding, and the welding speed is fast.
2. Argon arc welding: It uses non-consumable electrodes and shielding gas. It is often used to weld thin workpieces, but the welding speed is slow, and the heat input is much greater than laser welding, which is prone to deformation. 3.
Plasma arc welding: It is similar to argon arc welding, but its welding torch will produce a compressed arc to increase the arc temperature and energy density. It is faster and has a deeper penetration than argon arc welding, but inferior to laser welding.
4. Electron beam welding: It relies on a beam of accelerated high-energy density electron flow to hit the workpiece, generating huge heat in a small area on the surface of the workpiece, forming a "pinhole" effect, thereby implementing deep melting welding. The main disadvantage of electron beam welding is that it requires a high vacuum environment to prevent electron scattering, the equipment is complex, the size and shape of the weldment are limited by the vacuum chamber, and the assembly quality requirements for Korean parts are strict. Non-vacuum electron beam welding can also be implemented, but the effect is affected by poor focusing due to electron scattering. Electron beam welding also has magnetic offset and X-ray problems. Since electrons are charged, they will be affected by magnetic field deflection, so electron beam welding workpieces are required to be demagnetized before welding. X-rays are particularly strong under high pressure, and operators need to be protected. Laser welding does not require a vacuum chamber or demagnetization of the workpiece before welding. It can be carried out in the atmosphere and has no X-ray protection problem, so it can be operated online in the production line and can also weld magnetic materials.
4. Application prospects of laser welding in sensor production
Laser welding technology is a high-tech technology. Due to its unique characteristics, it is particularly suitable for use in sensor sealing welding. At present, many foreign sensor manufacturers use laser welding technology to produce sensors, while there are not many domestic manufacturers using this technology. It is mainly some manufacturers of military sensor products and some scientific research institutions that use this technology, and most of them use foreign laser welding machines. At present, the performance of domestic laser welding machines is not far behind that of foreign products, and they are fully capable of meeting the process requirements of domestic sensor production, but the price is 1/3-1/5 of similar foreign products. In order to improve the overall level of domestic sensors and develop the national laser industry, China's sensor manufacturers should use domestic laser welding machines to produce and process sensors as soon as possible to increase product competitiveness and open up the international market.
Keywords:Sensor
Reference address:Introduction and development of laser sensor welding technology
According to the national standard GB7665-87, sensors are defined as devices that can sense the specified measured quantity and convert it into a usable output signal according to certain rules. As a detection tool, sensors are required to detect the physical or chemical information of the research object. Their working process requires stability, reliability and high precision. Therefore, there are several requirements for sensors:
(1) Strong ability to adapt to harsh environments - sensors generally work in a wide range of environments, from extremely cold to hot areas. Many work in open air environments. They can resist flying sand and stones, dust, and should also be resistant to moisture. They should have high resistance to salt corrosion and acid corrosion, and have the ability to resist interference from polluted gases. They can adapt to high temperature, extreme cold, strong vibration, impact and other conditions. They should also have strong noise resistance and high signal-to-noise ratio.
(2) Moderate price, suitable for mass production - sensors are required to have good consistency and be suitable for automated mass production. They have high requirements for processing equipment to eliminate inconsistencies and errors caused by manual operation.
(3) High stability and reliability - sensors are high-precision detection instruments. There are strict requirements for their application in military, aviation and aerospace. Products must undergo rigorous testing before they can be used. Therefore, sensor production is a specific application and embodiment of high-tech. Whether a sensor has a high technical added value is reflected in whether the technical content and processing technology contained in it are high-tech. Some sensors need metal packaging due to the conditions of their application environment, and generally use welding sealing, such as pressure sensors, force sensors, Hall sensors, photoelectric sensors, temperature sensors, etc. These sensors have sensitive components and integrated circuits inside, which are filled with inert gas or vacuumed to isolate them from the outside world. They have pressure resistance and airtightness requirements, as well as welding strength requirements and leakage rate requirements. They have high requirements for welding quality, and require small deformation during welding, and cannot damage internal components and microcircuits. At present, sensor sealing welding includes resistance welding, tungsten inert gas welding, plasma arc welding, electron beam welding and laser welding.
2. Laser welding
1. Principle of laser welding-Laser is the abbreviation of stimulated emission of radiation. Due to its unique high brightness, high directivity, high monochromaticity and high coherence, it has been widely used in industrial processing since its birth, and has become a common processing method for future manufacturing systems. Laser welding uses a high-intensity laser beam. After the laser beam is focused by an optical system, the power density of the laser focus is 104~107W/cm2. The workpiece is placed near the laser focus for heating and melting. Whether the melting phenomenon can occur and the intensity of the melting phenomenon mainly depends on the time, power density and peak power of the laser acting on the surface of the material. By controlling the above parameters, lasers can be used for various welding processes.
2. General characteristics of laser welding - Laser welding is a thermal processing technology that uses a laser beam as a heat source. Compared with electron beams, plasma beams and general mechanical processing, it has many advantages: (1) The laser focus spot of the laser beam is small and the power density is high, which can weld some high-melting-point, high-strength alloy materials; (2) Laser welding is a non-contact process, without problems such as tool loss and tool replacement. The laser beam energy and moving speed are adjustable, and a variety of welding processes can be performed; (3) Laser welding has a high degree of automation and can be controlled by a computer. It has a fast welding speed and high efficiency, and can easily weld any complex shape; (4) The heat-affected zone of laser welding is small, the material deformation is small, and no subsequent process processing is required; (5) Laser can weld workpieces in a vacuum container and workpieces in a complex structure through glass; (6) The laser beam is easy to guide and focus, and can achieve changes in all directions; (7) Compared with electron beam processing, laser welding does not require a strict vacuum equipment system and is easy to operate; (8) Laser welding has high production efficiency, stable and reliable processing quality, and good economic and social benefits.
3. Process characteristics of laser welding in sensor production - Laser is used to seal the metal shell of the sensor, which is currently one of the most advanced processing methods, mainly based on the following characteristics of laser welding: (1) High aspect ratio. The weld is deep and narrow, and the weld is bright and beautiful; (2) Minimum heat input. Due to the high power density, the melting process is extremely fast, the heat input to the workpiece is very low, the welding speed is fast, the thermal deformation is small, and the heat-affected zone is small; (3) High density. During the weld formation process, the molten pool is constantly stirred, and gas is easily released, resulting in a pore-free, fully penetrated weld. The high cooling rate after welding can easily make the weld microstructure finer, and the weld strength, toughness and comprehensive performance are high; (4) Strengthen the weld. The high temperature heat source and the full absorption of non-metallic components produce a purification effect, reducing the impurity content, changing the size of inclusions and their distribution in the molten pool. No electrodes or filler wires are required during the welding process, and the molten zone is less contaminated, making the weld strength and toughness at least equivalent to or even exceeding that of the parent metal; (5) Precise control. Because the focused spot is very small, the weld can be positioned with high precision, the beam is easy to transmit and control, and there is no need to frequently replace the welding torch and nozzle, which significantly reduces downtime and auxiliary time, has high production efficiency, has no inertia, and can be stopped and restarted at high speed. The use of self-controlled beam movement technology can weld complex components; (6) Non-contact, atmospheric environment welding process. Because the energy comes from the laser, there is no physical contact between the workpiece and the workpiece, so no force is applied to the workpiece. In addition, magnetism and air have no effect on lasers; (7) Due to the low average heat input and high processing accuracy, the cost of reprocessing can be reduced. In addition, the operating cost of laser welding is low, which can reduce the cost of workpieces; (8) It is easy to realize automation, and the beam intensity and fine positioning can be effectively controlled.
III. Comparison of laser welding with existing welding methods
The methods currently used for sensor sealing welding include: resistance welding, argon arc welding, electric beam welding, plasma welding, etc.
1. Resistance welding: It is used to weld thin metal parts. The workpiece to be welded is clamped between two electrodes and a large current is passed to melt the surface contacted by the electrodes, that is, welding is carried out by heating the workpiece with resistance. The workpiece is easy to deform. Resistance welding welds both sides of the joint, while laser welding is only carried out from one side. The electrodes used for resistance welding need to be maintained frequently to remove oxides and metal adhered from the workpiece. Laser welding thin metal lap joints does not contact the workpiece. Moreover, the beam can also enter areas that are difficult to weld with conventional welding, and the welding speed is fast.
2. Argon arc welding: It uses non-consumable electrodes and shielding gas. It is often used to weld thin workpieces, but the welding speed is slow, and the heat input is much greater than laser welding, which is prone to deformation. 3.
Plasma arc welding: It is similar to argon arc welding, but its welding torch will produce a compressed arc to increase the arc temperature and energy density. It is faster and has a deeper penetration than argon arc welding, but inferior to laser welding.
4. Electron beam welding: It relies on a beam of accelerated high-energy density electron flow to hit the workpiece, generating huge heat in a small area on the surface of the workpiece, forming a "pinhole" effect, thereby implementing deep melting welding. The main disadvantage of electron beam welding is that it requires a high vacuum environment to prevent electron scattering, the equipment is complex, the size and shape of the weldment are limited by the vacuum chamber, and the assembly quality requirements for Korean parts are strict. Non-vacuum electron beam welding can also be implemented, but the effect is affected by poor focusing due to electron scattering. Electron beam welding also has magnetic offset and X-ray problems. Since electrons are charged, they will be affected by magnetic field deflection, so electron beam welding workpieces are required to be demagnetized before welding. X-rays are particularly strong under high pressure, and operators need to be protected. Laser welding does not require a vacuum chamber or demagnetization of the workpiece before welding. It can be carried out in the atmosphere and has no X-ray protection problem, so it can be operated online in the production line and can also weld magnetic materials.
4. Application prospects of laser welding in sensor production
Laser welding technology is a high-tech technology. Due to its unique characteristics, it is particularly suitable for use in sensor sealing welding. At present, many foreign sensor manufacturers use laser welding technology to produce sensors, while there are not many domestic manufacturers using this technology. It is mainly some manufacturers of military sensor products and some scientific research institutions that use this technology, and most of them use foreign laser welding machines. At present, the performance of domestic laser welding machines is not far behind that of foreign products, and they are fully capable of meeting the process requirements of domestic sensor production, but the price is 1/3-1/5 of similar foreign products. In order to improve the overall level of domestic sensors and develop the national laser industry, China's sensor manufacturers should use domestic laser welding machines to produce and process sensors as soon as possible to increase product competitiveness and open up the international market.
Previous article:Comparison of Common Fiber Optic Sensors
Next article:Design of Photoelectric Coordinate Sensor
Recommended ReadingLatest update time:2024-11-17 00:21
DUT input power measurement solution based on directional coupler and power sensor
Directional couplers are used to sample small amounts of input signal power for measurement. Port 1 is the input port; Port 1 is the input port. Port 2 is the output port; Port 3 is the coupling port; Port 4 is the isolation/terminated port, typically terminated to 50Ω to minimize reflections. However, when we measu
[Test Measurement]
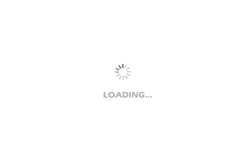
Application of Keithley SourceMeter 2450 in Biosensor/Transducer Qualification Test
Whether in the R&D laboratory or in production, rapid and accurate characterization of biosensors is an important means of verifying the quality of the biosensor/transducer interface and the ultimate operation of the bioassay system. It is often desirable to perform direct current-voltage (IV) characterization of th
[Test Measurement]
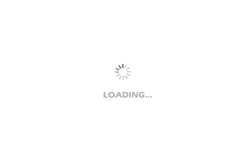
51 MCU DHT11 temperature and humidity sensor
DHT11 is a temperature and humidity sensor with calibrated digital signal output. The accuracy is +-5%RH, the temperature is +-2℃, the range is 20-90%RH, and the temperature is 0~50℃. 1. Circuit connection analysis 1. Pin diagram 2. Wiring Diagram The DHT11 device uses a simplified single bus communication. A si
[Microcontroller]
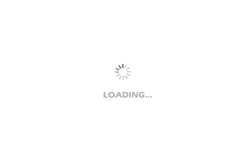
Pedometer algorithm using a three-axis acceleration sensor
Nowadays, many modern people pay great attention to their daily exercise. Pedometer, as an effective means of recording and monitoring exercise, is widely used in mobile terminal applications.
Currently, most pedometers use GPS signals to measure the distance traveled and then infer the number of steps. This metho
[Test Measurement]
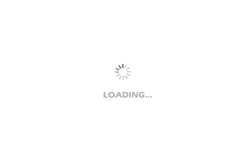
Infineon launches new CoolMOS S7T with integrated temperature sensor
[
Munich, Germany, December 19, 2023]
To
improve
the
accuracy
of junction temperature sensing, Infineon Technologies AG has launched a new CoolMOS™ S7T product family with integrated temperature sensors.
By
integrating
this series of semiconductor products in the
[Power Management]
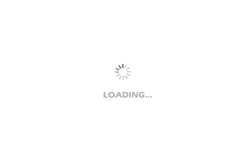
Sensors improve intersection safety
TRW Automotive Group enjoys a high reputation in the field of active and passive safety, and its design and manufacturing capabilities are world-leading. TRW Conekt, a research and consulting business unit under TRW, has made many achievements in intelligent transportation systems and has been internationally recogn
[Automotive Electronics]
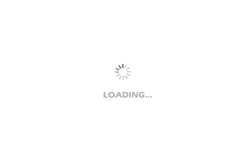
Brake fluid level sensor-Standard-Meder is here to protect you
Overview
We all know that when you step on the brake pedal while driving, the car's brake system will naturally slow down or stop. Do you know how this works? It turns out that a sealed reed sensor plays a key role. It controls the brakes by maintaining the brake fluid level. When the brake fluid level is too l
[Embedded]
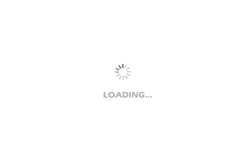
Application of oxygen sensors in energy conservation and emission reduction
With the development of global industrialization, fossil energy has been consumed in large quantities, which has also brought considerable impact on the environment. In the "12th Five-Year Plan for Energy Conservation and Emission Reduction" issued by the State Council, the state has refined and quantified the energy c
[Test Measurement]
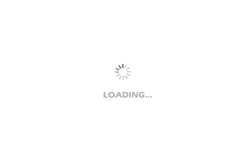
- Popular Resources
- Popular amplifiers
-
Analysis and Implementation of MAC Protocol for Wireless Sensor Networks (by Yang Zhijun, Xie Xianjie, and Ding Hongwei)
-
Introduction to Internet of Things Engineering 2nd Edition (Gongyi Wu)
-
西门子S7-12001500 PLC SCL语言编程从入门到精通 (北岛李工)
-
Modern Motor Control Technology (Wang Chengyuan, Xia Jiakuan, Sun Yibiao)
Latest sensor Articles
- Melexis launches ultra-low power automotive contactless micro-power switch chip
- Infineon's PASCO2V15 XENSIV PAS CO2 5V Sensor Now Available at Mouser for Accurate CO2 Level Measurement
- Milestone! SmartSens CMOS image sensor chip shipments exceed 100 million units in a single month!
- Taishi Micro released the ultra-high integration automotive touch chip TCAE10
- The first of its kind in the world: a high-spectral real-time imaging device with 100 channels and 1 million pixels independently developed by Chinese scientists
- Melexis Launches Breakthrough Arcminaxis™ Position Sensing Technology and Products for Robotic Joints
- ams and OSRAM held a roundtable forum at the China Development Center: Close to local customer needs, leading the new direction of the intelligent era
- Optimizing Vision System Power Consumption Using Wake-on-Motion
- Infineon Technologies Expands Leading REAL3™ Time-of-Flight Portfolio with New Automotive-Qualified Laser Driver IC
MoreSelected Circuit Diagrams
MorePopular Articles
- Innolux's intelligent steer-by-wire solution makes cars smarter and safer
- 8051 MCU - Parity Check
- How to efficiently balance the sensitivity of tactile sensing interfaces
- What should I do if the servo motor shakes? What causes the servo motor to shake quickly?
- 【Brushless Motor】Analysis of three-phase BLDC motor and sharing of two popular development boards
- Midea Industrial Technology's subsidiaries Clou Electronics and Hekang New Energy jointly appeared at the Munich Battery Energy Storage Exhibition and Solar Energy Exhibition
- Guoxin Sichen | Application of ferroelectric memory PB85RS2MC in power battery management, with a capacity of 2M
- Analysis of common faults of frequency converter
- In a head-on competition with Qualcomm, what kind of cockpit products has Intel come up with?
- Dalian Rongke's all-vanadium liquid flow battery energy storage equipment industrialization project has entered the sprint stage before production
MoreDaily News
- Allegro MicroSystems Introduces Advanced Magnetic and Inductive Position Sensing Solutions at Electronica 2024
- Car key in the left hand, liveness detection radar in the right hand, UWB is imperative for cars!
- After a decade of rapid development, domestic CIS has entered the market
- Aegis Dagger Battery + Thor EM-i Super Hybrid, Geely New Energy has thrown out two "king bombs"
- A brief discussion on functional safety - fault, error, and failure
- In the smart car 2.0 cycle, these core industry chains are facing major opportunities!
- The United States and Japan are developing new batteries. CATL faces challenges? How should China's new energy battery industry respond?
- Murata launches high-precision 6-axis inertial sensor for automobiles
- Ford patents pre-charge alarm to help save costs and respond to emergencies
- New real-time microcontroller system from Texas Instruments enables smarter processing in automotive and industrial applications
Guess you like
- MC34063 step-down circuit
- AD16.0 Copy Room Formats Problems
- The world's smallest gingerbread house
- I have a problem with using the eclipse that comes with altera. Can anyone tell me what I have used?
- The Three Realms of Oscilloscopes
- Problems with the snubber circuit
- [RVB2601 Creative Application Development] Introduction and use of cJSON for RVB2601
- I bought an ST-LINK emulator for SensorTile.box for 19 RMB
- Common RF Certification Systems
- [RVB2601 Creative Application Development] VII. RVB2601 Sound Recognition Preliminary Test