High Fidelity Vibration Acquisition Platform for Condition Monitoring
High-fidelity vibration acquisition platform for condition monitoring
summary
This article explains how recent advances in MEMS technology have brought accelerometers to the forefront, competing with piezoelectric sensors in condition monitoring applications. It also discusses how to use new development platforms that make this possible.
Introduction to Condition-Based Monitoring (CbM) and Predictive Maintenance (PdM)
Condition monitoring (CbM) involves the use of sensors to measure the current state of health to monitor a machine or asset. Predictive maintenance (PdM) requires a combination of CbM, machine learning, and analytics to predict future asset maintenance cycles or possible failures. Global equipment health monitoring is expected to grow significantly, so it is imperative to know and understand key trends. More and more CbM companies are beginning to adopt PdM to improve the differentiation of their products. Maintenance and equipment managers now have new options for CbM, such as wireless devices, as well as lower-cost, high-performance devices. While the infrastructure of most CbM systems remains the same, it is now possible to integrate new MEMS technologies directly into systems that were previously dominated by piezoelectric sensors or were not monitored due to cost barriers.
Condition Monitoring—Engineering Challenges and Design Decisions
In a typical CbM signal chain design, there are many different engineering disciplines and technologies to consider, all of which are constantly improving and increasing in complexity. There are now various types of customers who may have expertise in one area, such as algorithm development (software only) or hardware design (hardware only), but not always both.
For developers who want to focus on algorithm development, they require a data repository that can accurately predict asset failures and downtime. They don't want to design hardware, or troubleshoot data integrity failures; they want to use data that is truly high-fidelity. Similarly, for hardware engineers who want to improve system reliability or reduce costs, they need a solution that can easily connect to existing infrastructure so that they can benchmark existing solutions. They need to access data in a readable format that is easy to use and export so that they don't waste time evaluating performance.
Many of the system-level challenges can be solved with a platform approach—from the sensor all the way to algorithmic development—enabling all customer types.
Many system-level challenges can be solved with a platform approach, from sensor to algorithm development, supporting all types of customers.
What is CN0549 and how does it help extend the life of your device?
CN0549 CbM Development Platform
The CN0549 Condition Monitoring Platform is a high-performance, off-the-shelf hardware and software solution that delivers high-fidelity vibration data streams from assets into algorithm/machine learning development environments. The platform provides hardware experts with a tested and proven system solution that provides highly accurate data acquisition, reliable mechanical coupling to assets, and high-performance broadband vibration sensors. All hardware design files are provided to help you easily integrate into your designed products. CN0549 is also attractive to software experts, as it outlines the hardware challenges of the condition monitoring signal chain, allowing software teams and data experts to start developing machine learning algorithms directly. Key features and benefits include:
Easy to install into the asset while maintaining the integrity of the mechanically coupled signal
Wide bandwidth MEMS accelerometer sensor with IEPE data output format
u IEPE, high-fidelity data acquisition (DAQ) solution with analog input bandwidth from DC to 54 kHz
Embedded gateway captures and stores raw data for local or networked processing
uUse ADI's IIO oscilloscope application to display frequency domain data in real time
uStream sensor data directly to popular data analysis tools such as Python and MATLAB®
The CbM development platform consists of four different components (see Figure 1), which we will introduce one by one and then introduce the entire combined solution.
Figure 1. Elements that make up a CbM development platform
Highly accurate and high-fidelity data capture and processing
With wider bandwidth and lower sensor noise, faults such as bearing problems, cavitation and gear mesh can be detected earlier. It is very important that the data acquisition electronics ensure that the measured vibration data has a high fidelity; otherwise, important fault information may be lost. Ensuring the fidelity of vibration data allows us to detect trends faster and provide predictive maintenance recommendations with high confidence, thereby reducing unnecessary wear on mechanical components and extending the life of the asset.
A cost-effective way to implement condition monitoring on less critical assets
Piezoelectric accelerometers are the highest performance vibration sensors used on the most critical assets, where performance outweighs cost. The high cost of piezoelectric sensors has historically prevented condition monitoring of less critical assets. Now that MEMS vibration sensors match piezoelectric sensors in terms of noise, bandwidth, and g-range, they are enabling maintenance and equipment managers to gain greater insight into less critical assets that were previously subject to troubleshooting or reactive maintenance programs. This is primarily due to the high performance and low cost of MEMS. We now have a cost-effective method to continuously monitor low- and medium-critical assets. We can use advanced vibration sensing technology to easily identify and repair unnecessary wear on assets, helping to extend the life of the asset. This also helps improve the overall efficiency of the equipment and reduce machine or process downtime.
Monitor assets – detect problems
For CbM and PdM, there are many different types of sensing modes that can be used. Most applications involve current sensing, electromagnetic sensing, flow monitoring, and several other modes. Vibration sensing is the most common mode used in CbM, and piezoelectric accelerometers are the most common vibration sensor. In this section, we will review how technological advances have continued to advance the field of vibration sensors and how this affects application decisions.
MEMS and Piezoelectric Accelerometers
Piezoelectric accelerometers are very high performance sensors, but achieving that performance requires many design trade-offs. For example, piezoelectric accelerometers are typically used in wired installations because they consume too much power, can be large (especially triaxial sensors), and are expensive. All of these factors make it impractical to use piezoelectric sensors throughout an entire factory, so they are generally only used on critical assets.
Until recently, MEMS accelerometers did not have sufficient bandwidth, had excessive noise, and had g-ranges that limited them to monitoring less critical assets. Recent advances in MEMS technology have overcome these limitations, enabling MEMS vibration sensors to monitor both low-end assets and very critical assets. Table 1 shows the important characteristics required of piezoelectric and MEMS sensors in CbM applications. MEMS accelerometers are quickly becoming the sensor of choice for many CbM applications due to their small size, years of battery operation, low cost, and comparable performance to piezoelectric sensors.
The CN0549 CbM Development Platform is compatible with both MEMS and IEPE piezoelectric accelerometers, allowing for benchmark comparisons between different sensor types.
Table 1. MEMS and piezoelectric accelerometers
Using MEMS accelerometers in existing IEPE infrastructure
As shown in Table 1, MEMS accelerometers now offer competitive specifications and performance compared to piezoelectric sensors, but can they replace existing piezoelectric sensors? To make it easier for designers to evaluate and use MEMS accelerometers to replace piezoelectric accelerometers, ADI has designed an interface that is compatible with the IEPE standard piezoelectric sensor interface actually used in CbM applications.
IEPE Sensor Interface and Mechanical Mounting (CN0532)
The CN0532 (shown in Figure 2) is an IEPE conversion circuit that allows MEMS accelerometers to seamlessly interface directly with IEPE infrastructure, just like existing IEPE sensors.
Figure 2. CN0532 MEMS IEPE conversion circuit
Single-axis MEMS sensors typically have three output lines: power, ground, and acceleration output. IEPE infrastructure requires only two: one line for ground and one for power/signal. Current is delivered to the sensor, and when the sensor detects vibration, a voltage is output on the same line.
Figure 3. Simplified schematic showing how a MEMS sensor can be connected to the existing IEPE infrastructure (power and data)
The CN0532 PCB is designed to be 90 mils thick to maintain the frequency response performance of the MEMS accelerometer given in the data sheet. The test fixture is screw mounted and can be tested out of the box. The mounting block, PCB, and solder paste are extensively characterized to ensure full bandwidth mechanical transfer function, maximize visibility of all types of faults within the sensor bandwidth, and extend the life of the asset by capturing these faults. These solutions allow CbM designers to easily integrate MEMS accelerometers into their assets and seamlessly connect with existing piezoelectric infrastructure.
Previous article:Mouser now stocking three ams OSRAM multi-zone time-of-flight sensors
Next article:Mouser Electronics Now Stocking Infineon's XENSIV PAS CO2 Sensor
Recommended ReadingLatest update time:2024-11-16 16:24
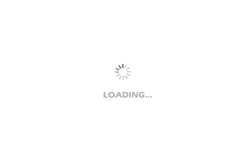
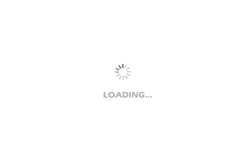
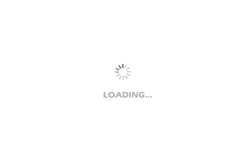
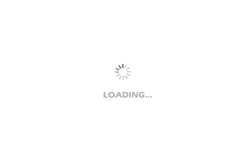
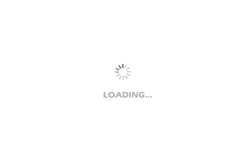
- Popular Resources
- Popular amplifiers
-
Analysis and Implementation of MAC Protocol for Wireless Sensor Networks (by Yang Zhijun, Xie Xianjie, and Ding Hongwei)
-
Introduction to Internet of Things Engineering 2nd Edition (Gongyi Wu)
-
西门子S7-12001500 PLC SCL语言编程从入门到精通 (北岛李工)
-
Modern Motor Control Technology (Wang Chengyuan, Xia Jiakuan, Sun Yibiao)
- Melexis launches ultra-low power automotive contactless micro-power switch chip
- Infineon's PASCO2V15 XENSIV PAS CO2 5V Sensor Now Available at Mouser for Accurate CO2 Level Measurement
- Milestone! SmartSens CMOS image sensor chip shipments exceed 100 million units in a single month!
- Taishi Micro released the ultra-high integration automotive touch chip TCAE10
- The first of its kind in the world: a high-spectral real-time imaging device with 100 channels and 1 million pixels independently developed by Chinese scientists
- Melexis Launches Breakthrough Arcminaxis™ Position Sensing Technology and Products for Robotic Joints
- ams and OSRAM held a roundtable forum at the China Development Center: Close to local customer needs, leading the new direction of the intelligent era
- Optimizing Vision System Power Consumption Using Wake-on-Motion
- Infineon Technologies Expands Leading REAL3™ Time-of-Flight Portfolio with New Automotive-Qualified Laser Driver IC
- Innolux's intelligent steer-by-wire solution makes cars smarter and safer
- 8051 MCU - Parity Check
- How to efficiently balance the sensitivity of tactile sensing interfaces
- What should I do if the servo motor shakes? What causes the servo motor to shake quickly?
- 【Brushless Motor】Analysis of three-phase BLDC motor and sharing of two popular development boards
- Midea Industrial Technology's subsidiaries Clou Electronics and Hekang New Energy jointly appeared at the Munich Battery Energy Storage Exhibition and Solar Energy Exhibition
- Guoxin Sichen | Application of ferroelectric memory PB85RS2MC in power battery management, with a capacity of 2M
- Analysis of common faults of frequency converter
- In a head-on competition with Qualcomm, what kind of cockpit products has Intel come up with?
- Dalian Rongke's all-vanadium liquid flow battery energy storage equipment industrialization project has entered the sprint stage before production
- Allegro MicroSystems Introduces Advanced Magnetic and Inductive Position Sensing Solutions at Electronica 2024
- Car key in the left hand, liveness detection radar in the right hand, UWB is imperative for cars!
- After a decade of rapid development, domestic CIS has entered the market
- Aegis Dagger Battery + Thor EM-i Super Hybrid, Geely New Energy has thrown out two "king bombs"
- A brief discussion on functional safety - fault, error, and failure
- In the smart car 2.0 cycle, these core industry chains are facing major opportunities!
- The United States and Japan are developing new batteries. CATL faces challenges? How should China's new energy battery industry respond?
- Murata launches high-precision 6-axis inertial sensor for automobiles
- Ford patents pre-charge alarm to help save costs and respond to emergencies
- New real-time microcontroller system from Texas Instruments enables smarter processing in automotive and industrial applications
- STEVAL-IDB0071V1_ by gs001588
- Proteus 8.9 supports STM32F401
- zd test zd test 1
- Help: Why does the pin have voltage output when the PIC microcontroller port is set as input?
- Three important rules about EMC certification
- Micro Python Web Framework: microdot
- EEWORLD University ---- Building Block DAC: System Thinking Method
- Single package six-channel digital isolator and IPM interface reference design for inverter
- [Silicon Labs Development Kit Review] + Building Simplicity Studio Development Environment
- Tiger Wish: Make a wish for 2022, usher in good luck in the new year, and take away the EEWorld New Year gift~