There are three key challenges to overcome in using wide bandgap semiconductors in aerospace and satellite power systems.
Wide bandgap (WBG) semiconductors offer several advantages in power conversion, such as higher power density and efficiency, while reducing system size and weight through high-frequency switching that allows the use of smaller passive components. These advantages may be even more important in aerospace and satellite power systems, where size and weight are more critical. This article explores the relative advantages of WBG components such as silicon carbide (SiC) and gallium nitride (GaN) in these applications.
Aircraft power conversion
-
Multi-Electric Aircraft (MEA): The goal is to replace some mechanical or hydraulically driven engine accessories with electrically driven components (such as fuel pumps).
-
Multi-Electric Propulsion (MEP): Uses generators to provide hybrid assistance to gas turbines, thereby reducing fuel consumption.
-
All-electric aircraft (AEA): Purely electric aircraft have a long way to go. The methods will first be applied to small aircraft such as helicopters, urban air mobility (UAM) vehicles and vertical take-off and landing (VTOL) aircraft, such as those planned for use as air taxis.
Key requirements and challenges for aircraft power electronics
-
Size, Weight and Power Loss (SWaP): A lower SWaP metric is key because fuel consumption, range and overall energy efficiency are directly related to it. Think of AEA. In this case, the battery system is the heaviest component of the power generation system. The required battery size depends on the efficiency of the inverter. Even a 1% increase in inverter efficiency from 98% to 99% would reduce the required battery size by several hundred kilograms for a typical battery with an energy density of 250 Wh/kg. Another key indicator is the gravimetric power density (kW/kg) of the inverter module. Likewise, the cooling systems required for the passive components and active components of the converter can be large and heavy.
-
在非增压区域中,靠近发动机安装的大功率电子器件面临许多与热和隔离有关的挑战。有源器件的温度需要显著降额,其冷却要求会给整架飞机的冷却系统造成负担。在高空,较低的电场下可能会发生局部放电,因此,半导体和模块封装以及隔离部件设计需要有足够的余量。要确保耐受宇宙辐射,还可能需要对有源器件的电压进行大幅降额。
-
Qualification and Reliability Standards: DO-160 is a rule for testing avionics hardware in different environments. Few commercial off-the-shelf (COTS) components are certified in this area, leaving OEMs and aircraft manufacturers to qualify and ensure their use.
Advantages of wide bandgap (WBG) power semiconductors in aerospace and satellite applications
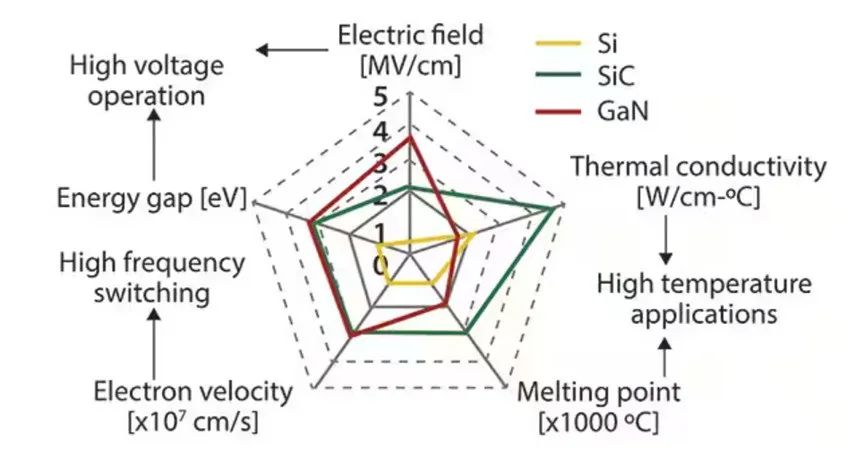
The advantages of these materials translate into numerous advantages for aircraft power electronics:
-
Higher thermal conductivity (especially SiC) makes it easier to cool components, such as those used to control engines.
-
System voltage is higher, reducing resistive losses in wiring. This is especially true for SiC, for which commercial devices operate at voltages up to 3.3 kV, and research is actively being conducted to further extend this range.
-
Improved reliability at high temperatures. For example, SiC has been shown to operate at +200 ˚ C.
-
Conduction and switching losses are low. The increased bandgap results in a smaller drift region for a given voltage rating, thereby improving conduction losses. In addition, lower parasitic capacitance reduces switching losses while speeding up the switching slew rate.
-
Low parasitics also allow operation at higher frequencies. For example, the switching frequency of a 1-5 kV SiC MOSFET can reach hundreds of kHz, while the equivalent topology in Si may only have a few tens of kHz. GaN HEMT (High Electron Mobility Transistor) devices, although mostly <700 V, are unipolar and have the added advantage of having no reverse recovery losses and being able to switch within this 100 V range at frequencies of several MHz . The biggest advantage of high frequencies is the ability to reduce the size of the magnets.
Figure 2 compares the efficiency of GaN and silicon-based 100 kHz boost converters.
Figure 2: Efficiency comparison of Si and GaN 100 kHz boost converters. (Image source:
Nexperia
)
All the above advantages directly lead to better SWaP metrics and higher power density. For example, using a higher voltage rated device produces a higher DC link voltage, resulting in a smaller capacitive RMS current in the converter DC link capacitor, which can reduce its size requirements. Higher switching frequencies allow the use of high-frequency planar magnetics in smaller form factors. In a traditional power converter, magnetic components may account for 40-50% of the total weight, a proportion that is declining with the use of WBG active devices that operate at higher frequencies. Judging from the mass power density of the inverter, the power density of silicon-based air-cooled converters is approximately 10 kW/kg. With the use of WBG, this indicator has exceeded 25 kW/kg in many system demonstrations, and in theory, densities up to 100 kW/kg can be achieved by optimizing the topology, DC link voltage and switching frequency.
Challenges and possible solutions for using wide bandgap (WBG) power semiconductors
-
Higher power density directly leads to increased heat generation. High temperatures reduce the efficiency of power conversion and can cause reliability issues, especially when temperature cycling involves high temperature changes. Thermomechanical stress can affect the packaging reliability of power modules, destabilize heat dissipation devices such as thermal interface materials (TIMs) (such as thermal paste that connects active device substrates and heat sinks), and increase their thermal resistance. Some solutions currently being explored include:
-
Improved packaging: Using a silver-sintered direct-cooled aluminum nitride (DBA) substrate provides double-sided cooling, allowing the package to achieve better heat dissipation. Other methods include selective laser melting (SLM) of powdered alloy heat sinks directly on DBA substrates.
-
As power requirements increase, so does the size of active chips, and using parallel chips to achieve the same net effective area is beneficial for heat dissipation.
-
WBG's switching transition is faster, which is beneficial to reducing switching losses, but also brings more risks of electromagnetic interference (EMI). Solutions for this include:
-
Distributed filter units improve performance and provide redundancy.
-
With an active-passive hybrid filter, using an amplifier to boost low frequencies reduces the net size of the filter and improves performance.
-
As the voltage rating increases, the specific resistance of the power supply device (RDS(ON) x A, where RDS(ON) is the on-resistance and A is the active area) increases because a thicker drift region is necessary. For example, while the high-temperature specific resistance of a 1200 V SiC MOSFET may be 1 mOhm-mm2, for a device rated at 6 kV, it can reach 10 mOhm-mm2. To reach the RDS(ON) target, larger devices or more devices in parallel are needed, which means higher chip cost, greater switching losses and more cooling requirements. Possible solutions:
-
3-level or multi-level converter topologies allow the use of devices with lower voltage ratings than the DC link voltage. This is particularly relevant for GaN devices rated in the kilovolt range, where a series-in-parallel-out (SIPO) configuration distributes the input voltage across many devices, allowing their use.
GaN and satellite communications
-
栅电极下的 AlGaN 层不会像 MOSFET 中的 SiO2 栅氧化层那样收集电荷。因此,增强型 GaN HEMT 的总电离剂量 (TID) 性能得以显著改善,有报告称工作时超过 1 Mrad,而在 Si/SiC 中通常为几百 krad。
-
Secondary electron effects (SEE) can also be improved using GaN HEMTs. Since there are no holes, the risk of secondary electron disturbance (SEU) is minimized, as is the risk of gate fracture (SEGR) on Si and SiC.
Summarize
Editor's words
Continuous learning of secret skills and endless enjoyment of exclusive benefits
Just waiting for you to join!
Earn points and redeem gifts
China (RMB) Customer Service




China (USD)/Hong Kong Customer Service

400-882-4440



↙
Click "Read the original text" below to see more
