Hardware circuit design of UAV remote sensing platform control system
Source: InternetPublisher:念念Brown Keywords: Control system UAV hardware circuit design remote sensing Updated: 2021/09/21
Compared with satellite and manned aircraft remote sensing platforms, UAVs have the characteristics of low cost and high flexibility. In order to meet scientific remote sensing experiments, complete remote sensing tasks, coordinate the work of multiple components in the drone's electronic pod, and control the attitude of the remote sensing image sensor, the system uses AT89S52 as the main control chip and expands multi-channel serial ports and USB interfaces to implement system and peripheral devices communication, while designing a camera drive module and a three-degree-of-freedom stepper motor drive module. The UAV aerial remote sensing experiment proves that the system can meet the requirements of remote sensing experiments.
USB interface expansion circuit design
USB port expansion is implemented by CH375 chip. CH375 is a universal interface chip for USB bus produced by Nanjing Qinheng Co., Ltd. Its main features are cheap price, convenient interface and high reliability. Supports USB-HOST host mode and USB-DEVICE/SLAVE device mode. The USB host mode of CH375 supports commonly used USB full-speed devices. The external microcontroller needs to write firmware programs to communicate with USB devices according to the corresponding USB protocol. But for commonly used USB storage devices, the built-in firmware of CH375 can automatically handle the dedicated communication protocol of Mass-Storage mass storage devices. Under normal circumstances, external microcontrollers do not need to write firmware programs. You can directly read and write data in the USB storage device. There are two ways of communication between CH375 and microcontroller: parallel mode and serial mode. The schematic diagram of the USB expansion circuit is shown in Figure 3. The CH375 chip is set to built-in firmware mode and uses a 12 MHz crystal. The P0 port of the microcontroller is connected to D0~D7 of CH375 as the data bus. The decoder output Y4 is connected to the CS of CH375 to chip select the chip. The A0 of the microcontroller is connected to the A0 of CH375. The address or data input and output of CH375 can be selected. When A0 is high level, D0~D7 transmit addresses, and when A0 is low level, data is transmitted. P3.6 and P3.7 control the read and write operations of CH375 respectively. The INT of CH375 is connected to the INT1 input terminal of the microcontroller. When data is input through the USB port, an interrupt signal is generated to notify the microcontroller to process the data. When the CH375 chip is initialized and successfully connected to the host, the indicator light turns on.
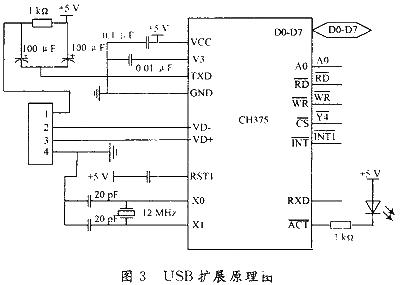
Stepper motor drive circuit
The stable pan/tilt control is a three-degree-of-freedom stepper motor control, which controls the pitch angle, roll angle and heading angle of the remote sensing sensor to keep the stable pan/tilt in a horizontal (or vertical) state. The stepper motor drive is implemented by the THB6128 chip. The single-chip microcomputer only needs to output the stepper motor running direction and pulse signal to control the stepper motor.
THB6128 is a high-subdivision two-phase hybrid stepper motor drive chip. By outputting control signals from the microcontroller, a high-performance, multi-subdivision drive circuit can be designed. It features dual full-bridge MOSFET drive, low on-resistance Ron=0.55 Ω, maximum withstand voltage 36 V, high current 2.2 A (peak), multiple subdivisions available, up to 128 subdivisions, and automatic half-current locking Function, three attenuation modes are available: fast decay, slow decay, and mixed attenuation, with built-in temperature protection and over-current protection. Figure 4 shows the yaw angle stepper motor drive circuit, and the pitch and roll angle stepper motor drives are the same. In the figure, CP1 and U/D are the driving pulse and motor running direction control signals respectively given by the microcontroller. M1, M2, and M3 are motor drive subdivision selection signal inputs, which are manually controlled by DIP switches. FDT1 and VREG1 are the attenuation mode selection voltage and current control voltage input terminals respectively. When 3.5 V, it is the slow decay mode; when it is the mixed decay mode; when FDT1 < 0.8 V, it is the fast decay mode. Adjust the VREG1 terminal voltage to set the stepper motor drive current value.
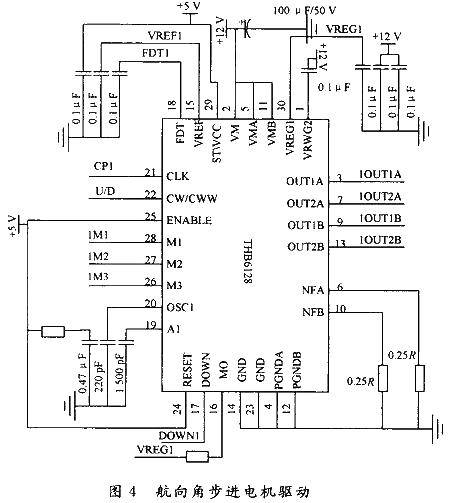
CCD/camera drive circuit design
The CCD/camera driver is implemented by a monostable trigger 74LS221 and an optocoupler P521. 74LS221 can be triggered by either falling edge or rising edge, and the output can be disabled. The output pulse width is obtained through internal compensation and is not affected by external voltage and stability. In most applications, the pulse width is only determined by external timing components. The CCD/camera drive circuit is shown in Figure 5. The high-level duration of the monostable trigger of the parameters shown in the figure is about 33 ms. The length of the steady-state time can be adjusted by changing the charging time constant RC of the circuit according to the actual exposure time of the camera. In the picture, Camera is the P3.5 port of the microcontroller. When it is on the falling edge, it triggers the monostable trigger to output a high level. This high level acts on the diode end of the optocoupler P521, thereby triggering the triode end to conduct. Trigger the camera shutter. The output end of P521 is connected in series with a 10kΩ resistor to prevent excessive current from damaging the camera during conduction.
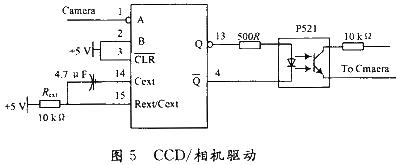
The data storage module is implemented by AT24C512. The P3.0 and P3.1 ports of the microcontroller are connected to the SCL and SDL ports of AT24C512 respectively, and the pull-up resistors are connected to simulate the I2C bus to expand the 64KB E2PROM data memory. The SRAM expansion is implemented by the IDT6116SA chip, and the expansion of 2 KB is used to cache temporary data during the calculation process of the microcontroller. The system input voltage is 12 V DC, and the power module uses two three-terminal voltage regulators, 7805 and 7805, connected in series to reduce the voltage drop at both ends of the monolithic voltage regulator and obtain a stable +5 V voltage.
Experiments have proven that this system can better meet the requirements for airborne operation control of UAV aerial remote sensing platforms. It can coordinate the work of various components of the electronic pod, control the attitude of the camera, and download airborne operation data in real time. The I/O There are fewer O ports, and the expansion of the USB interface solves the problem that many current notebook computers do not have COM ports. Photo information data in the operating system can also be processed in a timely manner during field experiments. The microcontroller still has more resources that can be utilized, which can facilitate system upgrades, but it is also limited by the data processing capabilities of the microprocessor.
- How about the boost converter TPS61299?
- TPS274C65 helps reduce downtime and increase productivity in 24 VDC power distribution plants
- A very convenient small power supply circuit to share
- How to use a simple circuit to achieve a smooth soft-start for an isolated converter
- Lithium battery overcharge, over discharge, short circuit protection circuit design
- Constant current LED lamp driver circuit with soft start and anti-shock
- Dual forward converter schematic diagram
- A novel and practical DC low voltage stabilized power supply
- Design of electric vehicle charger
- MAX1811 Lithium Battery Charger Production
- Power supply circuit design optimized for digital light projectors
- Portable device charging power circuit design
- 3-phase CPU power circuit using HIP6301 and HIP6601 chips
- Single phase thyristor slotless nickel plated power circuit
- Timing switch AC power circuit
- Additional power circuit design for USB devices
- M51971L steady speed control system
- ±15V active servo power circuit
- Common power circuits and applications 06
- Common power circuits and applications 03