CAN (Controller Area Network) is a local area network technology based on bus communication, which is widely used in automotive electronics, industrial control and other fields. In practical applications, the quality of CAN communication circuit has an important impact on the stability and reliability of the entire system. This article will introduce in detail how to detect the quality of CAN communication circuit, including detection methods, detection tools, detection process and common problem handling.
1. Detection method
-
Visual inspection
Before testing the CAN communication circuit, you must first conduct a visual inspection to check whether the circuit board is burned, damaged, corroded, etc., check whether the connector is loose or damaged, and check whether the cable is broken or worn.
-
Resistance detection
Use a multimeter to measure the resistance value in the CAN communication circuit, including bus resistance, terminal resistance, etc. Under normal circumstances, the resistance value of the CAN bus should be between 60-120Ω, and the terminal resistance value should be around 120Ω.
-
Voltage detection
Use a multimeter to measure the voltage value in the CAN communication circuit, including power supply voltage, signal voltage, etc. Under normal circumstances, the power supply voltage of the CAN bus should be between 9-30V, and the signal voltage should be between 0-5V.
-
Signal integrity testing
Use an oscilloscope or logic analyzer to detect the signal integrity in the CAN communication circuit, including the signal rise time, fall time, amplitude, waveform, etc. Under normal circumstances, the rise time of the CAN signal should be between 1-3μs, the fall time should be between 1-2μs, and the amplitude should be between 0.9-2.5V.
-
Communication test
Use CAN communication test tools, such as CAN card, CAN analyzer, etc. to perform communication test. The test content includes communication rate, communication distance, communication quality, etc.
2. Testing tools
-
multimeter
A multimeter is a commonly used electronic measuring tool that can measure parameters such as resistance, voltage, and current. In the detection of CAN communication circuits, the multimeter is mainly used to measure resistance and voltage.
-
Oscilloscope
An oscilloscope is an instrument used to observe and measure the waveform of electrical signals. In the detection of CAN communication circuits, the oscilloscope is mainly used to observe the waveform, amplitude, time and other parameters of the signal.
-
Logic Analyzer
A logic analyzer is an instrument used to measure and analyze digital signals. In the detection of CAN communication circuits, the logic analyzer is mainly used to measure signal parameters such as timing and frequency.
-
CAN Card
CAN card is a hardware device used to implement CAN communication, which can be inserted into the PCI slot or USB interface of the computer. In the detection of CAN communication circuit, CAN card is mainly used for communication test.
-
CAN Analyzer
CAN analyzer is a professional CAN communication test tool that can monitor and analyze the communication data on the CAN bus in real time. In the detection of CAN communication circuits, CAN analyzer is mainly used for signal integrity detection and communication testing.
3. Testing Process
-
Preparation
Before testing the CAN communication circuit, you need to prepare the corresponding testing tools, such as multimeter, oscilloscope, logic analyzer, CAN card, etc. At the same time, you also need to be familiar with the basic principles and parameter requirements of the CAN communication circuit.
-
Visual inspection
Perform a visual inspection of the CAN communication circuit as described above to check if the circuit board, connectors, cables, etc. are damaged or abnormal.
-
Resistance detection
Use a multimeter to measure the resistance value in the CAN communication circuit, including bus resistance, terminal resistance, etc. If the resistance value is not within the normal range, you need to further check whether there are problems with the circuit board, connector, cable, etc.
-
Voltage detection
Use a multimeter to measure the voltage value in the CAN communication circuit, including power supply voltage, signal voltage, etc. If the voltage value is not within the normal range, you need to check whether there are problems with the power supply, circuit board, etc.
-
Signal integrity testing
Use an oscilloscope or logic analyzer to detect the signal integrity in the CAN communication circuit, including the signal rise time, fall time, amplitude, waveform, etc. If the signal parameters are not within the normal range, you need to check whether there are problems with the circuit board, connector, cable, etc.
-
Communication test
Use a CAN card or CAN analyzer to perform communication tests, including communication rate, communication distance, communication quality, etc. If the communication test results are not ideal, further analysis of the causes is required and adjustments should be made.
-
Problem Solving
According to the test results, analyze the problems in the CAN communication circuit and take corresponding measures to deal with them. Common problems include abnormal resistance, abnormal voltage, signal integrity problems, communication failures, etc.
4. Common Problem Solving
-
Abnormal resistance
If the resistance value is not within the normal range, it may be caused by circuit board damage, poor connector contact, cable breakage, etc. You need to replace the damaged parts or reconnect the connector or cable.
-
Abnormal voltage
If the voltage value is not within the normal range, it may be caused by unstable power supply, circuit board damage, etc. It is necessary to check the power supply, circuit board and other components, and make corresponding adjustments or replacements.
-
Signal integrity issues
If the signal's rise time, fall time, amplitude, waveform and other parameters are not within the normal range, it may be caused by unreasonable circuit board design, poor connector contact, cable quality problems, etc. It is necessary to optimize the circuit board design, replace the connector or cable.
Previous article:How to measure the resistance between can high and can low
Next article:How to process the collected CAN data
Recommended ReadingLatest update time:2024-11-21 19:31
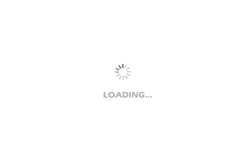
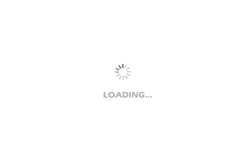
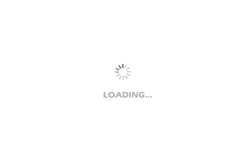
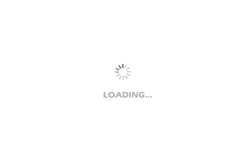
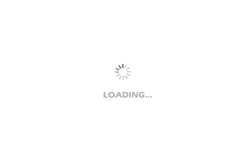
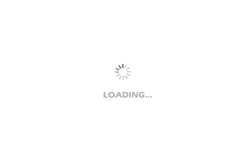
- Popular Resources
- Popular amplifiers
-
New Energy Vehicle Control System Inspection and Maintenance (Edited by Bao Pili)
-
Detailed explanation of big data technology system: principles, architecture and practice (Dong Xicheng)
-
Automotive CAN embedded intrusion detection system based on deep learning
-
Lightweight FPGA-based IDS-ECU architecture for automotive CAN networks
- Why is the vehicle operating system (Vehicle OS) becoming more and more important?
- Car Sensors - A detailed explanation of LiDAR
- Simple differences between automotive (ultrasonic, millimeter wave, laser) radars
- Comprehensive knowledge about automobile circuits
- Introduction of domestic automotive-grade bipolar latch Hall chip CHA44X
- Infineon Technologies and Magneti Marelli to Drive Regional Control Unit Innovation with AURIX™ TC4x MCU Family
- Power of E-band millimeter-wave radar
- Hardware design of power supply system for automobile controller
- Driving Automation Safety and Economic Engineering
Professor at Beihang University, dedicated to promoting microcontrollers and embedded systems for over 20 years.
- Intel promotes AI with multi-dimensional efforts in technology, application, and ecology
- ChinaJoy Qualcomm Snapdragon Theme Pavilion takes you to experience the new changes in digital entertainment in the 5G era
- Infineon's latest generation IGBT technology platform enables precise control of speed and position
- Two test methods for LED lighting life
- Don't Let Lightning Induced Surges Scare You
- Application of brushless motor controller ML4425/4426
- Easy identification of LED power supply quality
- World's first integrated photovoltaic solar system completed in Israel
- Sliding window mean filter for avr microcontroller AD conversion
- What does call mean in the detailed explanation of ABB robot programming instructions?
- Breaking through the intelligent competition, Changan Automobile opens the "God's perspective"
- The world's first fully digital chassis, looking forward to the debut of the U7 PHEV and EV versions
- Design of automotive LIN communication simulator based on Renesas MCU
- When will solid-state batteries become popular?
- Adding solid-state batteries, CATL wants to continue to be the "King of Ning"
- The agency predicts that my country's public electric vehicle charging piles will reach 3.6 million this year, accounting for nearly 70% of the world
- U.S. senators urge NHTSA to issue new vehicle safety rules
- Giants step up investment, accelerating the application of solid-state batteries
- Guangzhou Auto Show: End-to-end competition accelerates, autonomous driving fully impacts luxury...
- Lotus launches ultra-900V hybrid technology "Luyao" to accelerate the "Win26" plan
- Analysis of hot spots and trends of broadband wireless technology
- Audio: Huang Jianxiang went crazy and the owner went crazy too
- Using LM723 to provide DC adjustable voltage regulated power supply with overcurrent protection
- Please tell me the output voltage of the bidirectional thyristor circuit
- The role of microcontrollers and local interconnect networks in body control modules
- I encountered many problems in my study as shown in the figure (I am a hardware developer and just learned C)
- How to consider and design ESD of RF modules?
- Verilog module content
- How to manage lithium battery charging using TPS40060 and MCU?
- Share interactive Q&A with TI experts | Design and optimization of buck-boost charging chip compatible with USB-PD protocol