LiDAR stands for Light Detection and Ranging, which is a method of sensing distance using lasers. It measures the time it takes for the laser to reflect from an object to achieve the purpose of distance measurement. Depending on the specific application, different wavelengths can be used, but the most commonly used is infrared (IR).
Most of the time, the human brain is good at inferring the relative depth/distance and size of objects. This is an instinctive ability of humans, especially when driving a vehicle. However, imaging systems have a hard time doing this, especially since standard image sensors represent 3D scenes in 2D images. Using two image sensors in a stereoscopic arrangement similar to the human eye can extract depth data, but the ranging accuracy is limited and is affected by ambient light.
Using LiDAR to obtain depth data allows for measurements to be made independently of lighting conditions and eliminates image blur, making it possible to distinguish and understand different objects in a scene. Combining the light pulses emitted to an object and reflected back with precise timing measurements, the distance to the object can be calculated.
LiDAR is widely used in the automotive field, especially for semi-autonomous vehicles with SAE levels of L3~L5, for example, to sense objects around the vehicle; to see hundreds of meters ahead on the highway. LiDAR is also commonly used in delivery robots and other applications that require autonomous perception. The technology is also widely used in outdoor applications where processable 3D depth maps can be quickly generated with high accuracy - a process that takes days using traditional measurement techniques.
For example, in the agricultural sector, LiDAR is used to measure fields or land, map them, and assess crop conditions, enabling farmers to model and predict crop yields and choose the most appropriate pesticides/fertilizers. For grains stored in silos and liquids stored in storage tanks, simply install LiDAR on the top of the silo/storage tank to instantly measure the storage without contacting the contents.
Environmental organizations often use LiDAR to assess deforestation, measure coastal erosion, or monitor glacier retreat. In addition, in these applications, by installing LiDAR on unmanned aerial vehicles (UAVs)/drones, researchers can survey remote areas that are rarely visited by humans without having to go there in person.
Smart factories use LiDAR on automated guided vehicles (AGVs) that transport raw materials for processing and deliver finished products to shipping areas. When robots in smart factories use LiDAR, it can fully tap into the power of LiDAR itself, helping these robots perform tasks with precision and enabling them to sense whether there are people around them, so they can work in a thoughtful and safe manner.
LiDAR can be used to quickly survey large construction projects such as railways or highways. LiDAR can also be used as a security aid to protect certain areas from unwanted or unexpected intrusions. This is significant where hazardous materials are present or where large machines are working. LiDAR works effectively in all lighting conditions, meaning it can provide reliable always-on protection in these types of applications.
Types of LiDAR
The most common type of LiDAR is a direct time-of-flight (dToF) system, and the principle behind it is very simple: measure the time it takes for a pulse of light to reach a target and return to the sensor. The speed of light is a known physical constant, so calculating the distance between the emitter/detector and the reflecting target is straightforward.
Figure 1: dTOF measures the time it takes light to reach a target and return.
The technology typically uses a single very short pulse emitted by a light source (most commonly a laser), which simultaneously activates a precise timer. When the light pulse hits an object within range, it reflects back to a highly sensitive light sensor that is usually collocated with the laser. Once the return pulse is detected, the timer is stopped and the time taken to reach the object and return can be read.
As long as we know the time (t) from sending a pulse to receiving the echo, it is easy to calculate the distance (D) to the target object using the speed of light constant (c).
The dToF method is fast and efficient, and can measure multiple echoes, thus enabling the detection of multiple objects within the LiDAR field of view. It can be used for both long-range and short-range (0.1 m~300 m) applications, and maintains high and stable accuracy over the entire range.
Another LiDAR method, called indirect time of flight (iToF), also uses a continuous light wave from a laser. This method does not directly measure the passing ToF, but rather determines the ToF based on the phase difference between the transmitted and received waveforms.
iToF technology is more suitable for relatively short distance measurements (<10 m), especially indoor applications where the lighting conditions are not as challenging as outdoors, where the contrast is usually much higher. The technology can only detect the strongest echo and therefore only a single object.
The third type of LiDAR is frequency modulated continuous wave (FMCW), which is suitable for short-range and long-range ranging. This technology uses a tunable laser to generate a continuous light wave, which will be mixed with the reflected light at the detector. This mixing can produce a beat frequency between the local waveform and the reflected waveform, from which the object distance and directional velocity can be calculated.
While FMCW has excellent ranging performance and can capture directional velocity information, the use of tunable lasers with polarization control and reliance on short-wave infrared wavelengths (requiring the use of special semiconductors for the laser and detector) significantly increases the overall cost of this LiDAR system.
Figure 2: Comparison of LiDAR-based depth sensing methods
The Great Wavelength Debate
One of the most controversial topics surrounding LiDAR is which wavelength to use. The use of IR is preferred over visible light because there is much less background IR and the resulting signal-to-noise ratio (SNR) is better, making it easier to detect the returning light.
There are several suitable wavelengths in the IR spectrum, including the near infrared (NIR) spectrum (850 nm, 905 nm, 940 nm) and the short wave infrared (SWIR) spectrum (1350 nm, 1550 nm). Deciding which wavelength to use is a key issue in the “Great Wavelength Debate.” The three most important criteria to consider are system performance, availability of suitable components, and overall system cost.
The detector is one of the most basic components in any LiDAR system. CMOS silicon-based detectors can detect light with a wavelength range of 400 nm to 1000 nm, so they are sensitive to visible and NIR light, but cannot sense SWIR light. In order to detect SWIR light, III/V semiconductors such as InGaAs alloys must be used, which are very expensive compared to silicon.
Component availability is another consideration, especially for laser emitters. Edge-emitting lasers (EELs) are being replaced by vertical-cavity surface-emitting lasers (VCSELs), which are easier to package into arrays and have wavelength stability over temperature. While VCSELs are currently less efficient and more expensive, this is expected to improve as their applications expand.
Although there are multiple suppliers for SWIR EEL, there is currently only one supplier for SWIR VCSEL, while there are also multiple suppliers for NIR VCSEL. Therefore, choosing NIR is more likely to improve supply chain security.
The detection range is important because it increases the available reaction time and thus improves safety. However, lasers that are too strong can damage the eyes, so IEC 60825 specifies the maximum permissible exposure (MPE) for a 1ns laser pulse.
While NIR must have a lower MPE, the laser power can be increased if the pulse width is shortened, and a range of up to 300 m can be achieved due to the use of sensitive detectors. In good weather, the range of SWIR will exceed that of NIR, but SWIR is more susceptible to the adverse effects of moisture (such as rain or fog), so the performance of NIR-based systems will degrade at a slower rate than SWIR systems, providing more consistent performance in various weather conditions.
Based on the above, NIR is generally considered to be the wavelength of choice for automotive LiDAR. NIR allows us to use silicon-based devices instead of more expensive materials such as InGaAs, and perhaps more importantly, the components are available from multiple suppliers, which helps to establish a stronger supply chain. Although both NIR and SWIR can ensure eye safety when operating, NIR can still meet the requirements of automotive LiDAR while using lower power lasers.
From a commercial perspective, NIR is much cheaper, and cost has always been an important consideration for automotive applications. According to a survey by IHS Markit (Amsrud, 2019), the cost per channel for lasers and detectors is about $4 to $20, while for a similar SWIR system, the cost per channel is about $275. Even with further development and increased capacity, the cost of NIR is expected to be 10 to 100 times lower than SWIR.
LiDAR Composition Technology
One of the most important elements of any LiDAR system is the sensing element that captures and quantifies the reflected laser light. While a variety of technologies can be used to accomplish this, silicon photomultipliers (SiPMs) generally perform best, primarily due to their ability to detect single photons at high gains on the order of 1,000,000.
As a result, SiPMs have become increasingly popular in recent years and have become the sensor of choice for LiDAR depth sensing applications. Compared to traditional detectors such as avalanche photodiodes (APDs), which not only have much lower gain but also require integration of incoming signals, these devices are able to provide the highest SNR performance for long-distance ranging under high contrast conditions. Other advantages include lower power supply bias, better uniformity, and reduced sensitivity to temperature changes, making SiPMs an ideal upgrade option for systems using APDs. SiPMs have higher sensitivity and can use small package optical modules, making LiDAR easier to integrate into vehicles. Because SiPMs are produced using high-volume CMOS processes, these high-performance devices have the lowest detector cost, further promoting the popularity of LiDAR.
Previous article:What does the 48V mild hybrid system used by major car companies mean?
Next article:Achieve low-latency active noise reduction in the car
Recommended ReadingLatest update time:2024-11-16 09:47
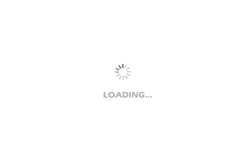
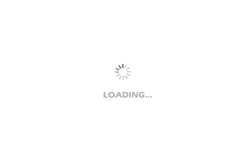
- Popular Resources
- Popular amplifiers
-
LiDAR point cloud tracking method based on 3D sparse convolutional structure and spatial...
-
GenMM - Geometrically and temporally consistent multimodal data generation from video and LiDAR
-
Comparative Study on 3D Object Detection Frameworks Based on LiDAR Data and Sensor Fusion Technology
-
Dual Radar: A Dual 4D Radar Multimodal Dataset for Autonomous Driving
- Huawei's Strategic Department Director Gai Gang: The cumulative installed base of open source Euler operating system exceeds 10 million sets
- Analysis of the application of several common contact parts in high-voltage connectors of new energy vehicles
- Wiring harness durability test and contact voltage drop test method
- Sn-doped CuO nanostructure-based ethanol gas sensor for real-time drunk driving detection in vehicles
- Design considerations for automotive battery wiring harness
- Do you know all the various motors commonly used in automotive electronics?
- What are the functions of the Internet of Vehicles? What are the uses and benefits of the Internet of Vehicles?
- Power Inverter - A critical safety system for electric vehicles
- Analysis of the information security mechanism of AUTOSAR, the automotive embedded software framework
Professor at Beihang University, dedicated to promoting microcontrollers and embedded systems for over 20 years.
- Innolux's intelligent steer-by-wire solution makes cars smarter and safer
- 8051 MCU - Parity Check
- How to efficiently balance the sensitivity of tactile sensing interfaces
- What should I do if the servo motor shakes? What causes the servo motor to shake quickly?
- 【Brushless Motor】Analysis of three-phase BLDC motor and sharing of two popular development boards
- Midea Industrial Technology's subsidiaries Clou Electronics and Hekang New Energy jointly appeared at the Munich Battery Energy Storage Exhibition and Solar Energy Exhibition
- Guoxin Sichen | Application of ferroelectric memory PB85RS2MC in power battery management, with a capacity of 2M
- Analysis of common faults of frequency converter
- In a head-on competition with Qualcomm, what kind of cockpit products has Intel come up with?
- Dalian Rongke's all-vanadium liquid flow battery energy storage equipment industrialization project has entered the sprint stage before production
- Allegro MicroSystems Introduces Advanced Magnetic and Inductive Position Sensing Solutions at Electronica 2024
- Car key in the left hand, liveness detection radar in the right hand, UWB is imperative for cars!
- After a decade of rapid development, domestic CIS has entered the market
- Aegis Dagger Battery + Thor EM-i Super Hybrid, Geely New Energy has thrown out two "king bombs"
- A brief discussion on functional safety - fault, error, and failure
- In the smart car 2.0 cycle, these core industry chains are facing major opportunities!
- The United States and Japan are developing new batteries. CATL faces challenges? How should China's new energy battery industry respond?
- Murata launches high-precision 6-axis inertial sensor for automobiles
- Ford patents pre-charge alarm to help save costs and respond to emergencies
- New real-time microcontroller system from Texas Instruments enables smarter processing in automotive and industrial applications
- How large a fifo capacity can ep4ce6 achieve?
- Introduction to the causes of TPS79633KTTR voltage instability
- 【TI recommended course】#Motor control voltage and current sampling solution#
- Allwinner heterogeneous multi-core AI intelligent vision V853 development board evaluation - separate compilation and testing of V853 SDK LVGL routines
- [Hua Diao Experience] Xingkong Board & Beetle ESP32-C3
- Low frequency power amplifier
- STTS751 High Accuracy Temperature Sensor Extension for MakeCode
- [Sipeed LicheeRV 86 Panel Review] Using crosstool-ng to build a compiler for riscv64
- "Domestic Chip Exchange" is launched! How to do it is up to you!
- [Erha Image Recognition Artificial Intelligence Vision Sensor] Evaluation of Four Face Algorithms