Preface:
After learning how to start the motor, accelerate and decelerate the motor, how do you brake the motor? Braking, also known as braking, can also be called brake braking. The function of braking is to stop the high-speed rotating motor. There is no doubt that this is an indispensable part of BLDC drive. Usually novice students will think that this is very simple. Isn't it enough to shut down the 6 power tubes? Yes, after shutting down the 6 power tubes, the motor will eventually stop. However, the question is how long does it take for medium and high-speed motors to stop like this? Looking at the motor that slowly stops, are you impatient? What do you do when you encounter a product that requires rapid braking? Therefore, the braking method of only shutting down 6 power tubes cannot meet the needs of product development. Then the question is, what are the rapid braking methods of BLDC? How to operate it specifically? This article will sort out this.
1. BLDC braking classification
BLDC braking is divided into two categories: mechanical braking and electrical braking.
Mechanical braking requires the use of a dedicated electromagnetic brake, commonly known as an "electromagnetic brake". It is generally used in scenarios where very fast braking is required. This article does not analyze it. Electrical braking uses an inverter circuit to change the electromagnetic conditions to generate a braking torque to achieve the purpose of rapid braking. Common electrical braking for BLDC includes: regenerative braking, reverse braking, and short-circuit braking.
2. Regenerative braking
Also, first look at the inverter circuit diagram, as shown in Figure 1 below.
Figure 1 As shown in Figure 3 above, the upper tubes are Q1, Q3, and Q5, and the lower tubes are Q6, Q4, and Q2. Motor coil ABC.
Regenerative braking is to use complementary output PWM to drive the motor. When braking, first reduce the PWM duty cycle, and then, when the motor decelerates to a low speed, turn off the PWM output. So, how does regenerative braking achieve the braking effect? The analysis is as follows.
Assume that AB is turned on (A upper tube Q1 and B lower tube Q4 are turned on), and the upper and lower tubes of A have complementary PWM outputs, that is, if A upper tube Q1 is turned on, then A lower tube Q6 is turned off; if A upper tube Q1 is turned off, then A lower tube Q6 is turned on. In this case, within a PWM cycle, the current flow direction of the inverter circuit is as shown in Figures 2 and 3 respectively.
A upper tube Q1 is turned on, A lower tube Q6 is turned off, and the current direction of the inverter circuit is as shown in Figure 2.
In Figure 2, the upper tube Q1 of A is turned off, and the lower tube Q6 of A is turned on. At the beginning, due to the inductance of the motor coil, the current will maintain the direction of Figure 2. However, as time goes by, due to the existence of the coil back electromotive force, the current will slowly reverse. Finally, the current direction of the inverter circuit is shown in Figure 3.
Figure 3 Comparing Figure 2 and Figure 3, it can be seen that the current in coil AB is reversed. When the current is reversed, the magnetic field is reversed; when the magnetic field is reversed, the electromagnetic torque is reversed. At this time, the electromotive torque becomes the braking torque, and the motor enters the braking state. Note that at this time, the braking ability comes from the electric energy stored in the motor coil, that is, the electric energy stored in the motor coil is used for braking.
In summary, in regenerative braking, as long as PWM is not full duty cycle output, there are two stages of driving and braking in each PWM cycle. In the acceleration stage, the PWM duty cycle gradually increases, and the braking time becomes shorter and shorter; in the deceleration stage, the PWM duty cycle gradually decreases, and the braking time becomes longer and longer.
3. Reverse braking
Reverse braking is to suddenly apply a reverse voltage according to the current direction of the coil, form a reverse current, and reverse the electromagnetic torque, so as to achieve the purpose of rapid braking.
Similarly, take the assumption that AB is turned on (A upper tube Q1 and B lower tube Q4 are turned on) as an example to illustrate the principle of regenerative braking. When AB is turned on, the current direction is as shown in Figure 2 above. What if the current is suddenly reversed? There is no doubt that BA (B upper tube Q3 and A lower tube Q6 are turned on) is turned on. In this case, the current direction is as shown in Figure 4.
Figure 4 When BA is turned on, the current is reversed, and the electromagnetic torque is reversed, which will definitely have a braking effect. However, how long should BA be turned on? On the one hand, if the time is too long, the motor will reverse; on the other hand, data show that the current will double during reverse braking (not calculated in this article). Although rapid braking can be achieved, there is also a risk of burning the motor (exceeding 2.5 times the rated current).
Therefore, during reverse braking, the motor speed cannot be too high, and the braking time needs to be controlled. Therefore, when reverse braking is actually used, the motor speed needs to be reduced first, and then the braking time needs to be adjusted in a certain medium and low speed range. The braking time needs to be repeatedly tested according to the speed to ensure that it will not reverse.
4. Short-circuit braking
Short-circuit braking is to turn on all the upper tubes (or lower tubes) of the inverter circuit, and turn off all the lower tubes (or upper tubes) to short-circuit the three sets of coils of the motor. Because the three coils are in the power generation state during the inertial rotation of the motor, short-circuiting the three coils is equivalent to short-circuiting the power supply. Because the internal resistance of the coil is usually very small, the short-circuit current will be very large. A large short-circuit current will generate a large braking torque, thereby achieving the purpose of rapid braking.
During short-circuit braking, the change in the direction of the current in the inverter circuit is relatively complex. This article will not draw a diagram to illustrate. During short-circuit braking
, the short-circuit current can be adjusted by different PWM duty cycles to avoid too large short-circuit current during the short-circuit process. When the motor is at medium and high speeds, the PWM duty cycle can be controlled within 30%; when the motor speed is at medium and low speeds, the full PWM duty cycle can be short-circuited. The short-circuit time of small PWM duty cycle and full duty cycle can be adjusted according to actual conditions.
Figure 5 below is the waveform of the short-circuit braking of the three lower tubes of the inverter circuit. Channels 1, 2 and 3 are phase voltage waveforms, which are all 0 due to short-circuiting. Channel 4 is one of the phase current waveforms.
Figure 5 As can be seen from Figure 5, during the short-circuit braking process, the short-circuit current is very large. If the short-circuit current is too large, on the one hand, the power tube may be burned; on the other hand, the motor coil will also heat up seriously. Therefore, it is necessary to strictly follow the method of first using a small PWM to decelerate the motor to a medium or low speed, and then use the full PWM duty cycle to short-circuit.
Summary:
(1) Feedback braking is the most worry-free. PWM complementary output is sufficient.
(2) Reverse braking needs to prevent reverse rotation. It is necessary to decelerate first and then reverse. The deceleration and reverse time should be adjusted according to the actual situation.
(3) Short-circuit braking needs to prevent large current. It is necessary to use a small PWM duty cycle to decelerate first, and then use the full PWM duty cycle to short-circuit. The deceleration and short-circuit time should be adjusted according to the actual situation.
Previous article:Learn about stepper motors in one article
Next article:Motor production: DC motor (II)
Recommended ReadingLatest update time:2024-11-16 11:52
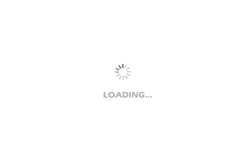
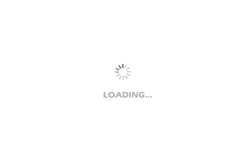
- Huawei's Strategic Department Director Gai Gang: The cumulative installed base of open source Euler operating system exceeds 10 million sets
- Analysis of the application of several common contact parts in high-voltage connectors of new energy vehicles
- Wiring harness durability test and contact voltage drop test method
- Sn-doped CuO nanostructure-based ethanol gas sensor for real-time drunk driving detection in vehicles
- Design considerations for automotive battery wiring harness
- Do you know all the various motors commonly used in automotive electronics?
- What are the functions of the Internet of Vehicles? What are the uses and benefits of the Internet of Vehicles?
- Power Inverter - A critical safety system for electric vehicles
- Analysis of the information security mechanism of AUTOSAR, the automotive embedded software framework
Professor at Beihang University, dedicated to promoting microcontrollers and embedded systems for over 20 years.
- Innolux's intelligent steer-by-wire solution makes cars smarter and safer
- 8051 MCU - Parity Check
- How to efficiently balance the sensitivity of tactile sensing interfaces
- What should I do if the servo motor shakes? What causes the servo motor to shake quickly?
- 【Brushless Motor】Analysis of three-phase BLDC motor and sharing of two popular development boards
- Midea Industrial Technology's subsidiaries Clou Electronics and Hekang New Energy jointly appeared at the Munich Battery Energy Storage Exhibition and Solar Energy Exhibition
- Guoxin Sichen | Application of ferroelectric memory PB85RS2MC in power battery management, with a capacity of 2M
- Analysis of common faults of frequency converter
- In a head-on competition with Qualcomm, what kind of cockpit products has Intel come up with?
- Dalian Rongke's all-vanadium liquid flow battery energy storage equipment industrialization project has entered the sprint stage before production
- Allegro MicroSystems Introduces Advanced Magnetic and Inductive Position Sensing Solutions at Electronica 2024
- Car key in the left hand, liveness detection radar in the right hand, UWB is imperative for cars!
- After a decade of rapid development, domestic CIS has entered the market
- Aegis Dagger Battery + Thor EM-i Super Hybrid, Geely New Energy has thrown out two "king bombs"
- A brief discussion on functional safety - fault, error, and failure
- In the smart car 2.0 cycle, these core industry chains are facing major opportunities!
- The United States and Japan are developing new batteries. CATL faces challenges? How should China's new energy battery industry respond?
- Murata launches high-precision 6-axis inertial sensor for automobiles
- Ford patents pre-charge alarm to help save costs and respond to emergencies
- New real-time microcontroller system from Texas Instruments enables smarter processing in automotive and industrial applications
- [Qinheng Trial] 2. Preparation for CH549EVT Operation
- PCB error cannot find the cause
- A brief discussion on SSI interface technology and its application in audio processing
- EEWORLD University Hall ---- Basic concepts of modern telecommunications technology Wu Deben, Beijing University of Posts and Telecommunications
- Diode packaging issues
- [RVB2601 Creative Application Development]_2_Environment Construction
- [Chuanglong TLA40i-EVM development board] +03. Storage media read and write test (zmj)
- Share BLE connection parameters and their setting points
- Photodiode Problems
- Interesting animated tutorial "Principles of Dialogue Communication"