Hair pin motors are also called flat copper wire winding motors. They change the stator of a traditional motor from a strand of copper wires to a copper bar with a rectangular cross section. It looks much better. What role does it play to make this technology receive so much attention in the past two years? Compared with the round wire in the round wire motor, due to the shape characteristics, the flat wire with the same cross-sectional area occupies less space than the round wire when arranging the wire. Therefore, the same winding slot space can be wound with a flat wire with a larger cross-sectional area. However, since the bending strength of the flat wire is much higher than that of the round wire composed of multiple strands of the same cross-sectional area, it cannot be wound on the iron core as conveniently as the round wire, especially when the first layer of winding is completed and the wire needs to be crossed to the second layer of winding, the traditional round wire winding is relatively easy to wind, and can be completed using automated equipment, while it is difficult to complete the flat wire winding through automated equipment. Even if the cross-sectional area is wound manually, it is difficult to arrange the winding neatly, resulting in greater waste of space in the iron core slot.
In 2014, the hairpin drive motor project was approved, and SAIC Jieneng and Huayu Electric were responsible for jointly carrying out technical research and development. At that time, there was still a blank in the research and development of mass-produced drive motors in China. After many rounds of efforts, SAIC Jieneng and Huayu Electric found a breakthrough. They not only mastered the key design technology of hairpin windings, but also established technical standards for corona-resistant flat enameled wires, and solved the technical difficulties of flat wire manufacturing, forming, plugging, twisting, and welding. The existing technology usually makes the flat wire into a shape similar to a U-shaped hairpin in advance, then inserts the hairpin wire from one end of the core slot, bends the end of the hairpin conductor, and finally welds all adjacent endpoints to form coils. This method is extremely complex, and due to the presence of a large number of welding points, the production cost is high, the difficulty is great, and the quality is difficult to control; other existing technologies also include designing the stator into a separate structure, pre-pressing the flat wire conductor into shape, and then inserting it into a separate stator, and finally combining it into a complete stator. This method has a complex process and affects the overall dimensional accuracy of the stator. In addition, the separated stator has a great influence on the motor magnetic circuit, which will increase the motor loss.
1. Hair pin segmented hairpin winding manufacturing process
The DOE project was completed in 2011, and the first Chevrolet model equipped with a flat wire motor was also released. Different from ordinary round wire motors, such as (Figure 1.1), this motor uses the hairpin winding technology with a half-open parallel slot structure.
This hairpin needs to be inserted first, and then use a twisting device to twist the open end into a "foot"-like structure, weld the different feet together, and finally wrap it with epoxy resin (Figure 1.2) to achieve insulation enhancement. This technology reduces DC resistance by 30~40%.
Production process: inserting insulating paper - hairpin forming - inserting wire - end separation (expansion) - twisting - welding - dripping paint/powder coating - electrical testing
Insert insulating paper: Currently, the most popular drive motor is O-type, and double C-type is also useful. B-type and S-type can improve the insulation performance of the product, but will reduce the pure copper slot fill rate and increase the manufacturing difficulty, especially when there are 6 or 8 layers of wire, the difficulty will increase significantly and the manufacturing stability will be worse.
Hairpin forming: the paint peeling process is used to cut and form the hairpin, and the hairpin is first formed into a U-shape by splitting, punching or bending. We call the formed end a crown shape, and the other end a welding shape. Currently, punching is the most popular process, so how to reduce the damage to the copper wire during the forming process has become a very important issue.
Insert the wire: pre-insert the PIN into the contoured tooling and firmly insert it into the core, pressing it into the corresponding design size. Automatic insertion of cross-layer wires is a difficult point, and the difficulty of automatic insertion of 6-layer and 8-layer wires will also increase significantly.
End separation (flaring): Increase the distance between each circle of solder joints to ensure the normal twisting and the creepage distance of the solder joints inside and outside the same slot; the consistency of the size after flaring is the basis for ensuring the smooth twisting of the subsequent sequence.
Twist: After twisting, the two wires to be welded should be flush; after twisting, the copper wire should not be damaged and the slot paper should not be broken. What form of cutting should be adopted is a problem worth studying. At present, most domestic equipment has obvious step difference on the end face of copper wire after cutting.
Welding: Welding itself is not difficult, but the difficulty lies in fast clamping and testing. Currently, the two most popular welding processes for flat wire motors are TIG welding and laser welding. Of course, some companies are also testing CMT cold welding or other welding methods. Regardless of the welding process used, how to determine the quality of so many welds in such a small space is currently a difficult topic.
Dripping paint/powder coating: Different choices of materials determine different process sequences: if powder materials are selected, the process sequence is coating first and then dipping paint; if liquid materials are selected, the process sequence is dipping paint first and then coating; the specific process requirements are carried out according to the material requirements. There are currently two main types of coating materials: powder and liquid, and both of these materials are controlled by foreign companies. Similarly, there are many types of dipping paint processes, such as traditional dipping paint, vacuum dipping paint, vacuum pressure dipping paint, dripping paint, etc., as well as the latest EUV dipping paint. This has a lot to do with the selection of paint materials. Different paint processes are also different and need to be tested and verified. At present, dripping paint may be more commonly used.
2. Advantages of Hair Pin
High efficiency and high power density Compared with traditional round wire motors, the bare copper slot fill rate of Hair pin motors can be increased by 20%~30%, effectively reducing winding resistance and copper loss. Under the same conditions, more wires are stuffed in, the thicker the wires are, the lower the resistance is, and the less energy is lost in the wires due to heat. With the same loss, Hair pin motors can output higher power and torque.
Stronger heat dissipation capability The Hair pin motor has a more regular shape and fits tightly in the stator slot, providing better contact with the stator core teeth and yoke, reducing the thermal resistance in the slot and improving the heat conduction efficiency, further improving the peak and continuous performance of the motor.
Better NVH performance As the winding has better rigidity, the whole machine will also have better rigidity. At the same time, the Hair pin winding is inserted through the end of the core, and there is no need to insert the wire from the slot. The electromagnetic design can choose a smaller slot design to effectively reduce the cogging torque pulsation.
Shorter winding ends The coil ends are more compact. Compared to loose windings, the height of the ends is much lower.
Minimized size The motor diameter is reduced by 10%, and the axial length (height) is reduced by 15%. The power density is significantly improved.
3. Disadvantages of Hair Pin
The process is complex and there are many steps. Each step requires high precision and has low fault tolerance. In order to reduce the number of conductors per slot, the number of slots is generally large, and the Remi motor has 60 slots, which increases the difficulty of winding manufacturing.
Large skin effect The higher the frequency, the higher the AC copper loss of the flat copper wire winding. It is also related to electromagnetic design, such as the magnetic flux amplitude in the slot, the slot height, etc. It is also related to the size of the flat copper wire, and the best width-to-thickness ratio needs to be found.
Difficult to serialize The number of turns of the hairpin motor is small, and it is difficult to adjust the matching of voltage and speed, and it is difficult to serialize. However, there are not many models of new energy vehicle motors, so it may not be a big problem.
High requirements for copper wire. The insulation layer of flat copper wire is easily damaged after bending, resulting in gaps or cracks, which puts higher requirements on the quality of copper wire. In addition, the hairpin motor is not like the traditional flat copper wire motor, which can be wrapped and insulated after the winding is formed.
The equipment has high requirements for complex procedures, high precision requirements, high quality requirements, and large output. Some OEMs and foundries have introduced production lines for hairpin motor winding equipment, but due to the high cost of the production line, it has not yet been popularized.
IV. Conclusion
In the past two years, hair-pin motors have become the development direction of passenger car drive motors that the industry has resolutely pursued. Domestic top motor suppliers have also begun to invest in building more advanced x-pin automated production lines.
Previous article:Analysis of Siemens PLC communication technology based on TCP/IP
Next article:What kind of motor is best?
Recommended ReadingLatest update time:2024-11-16 09:29
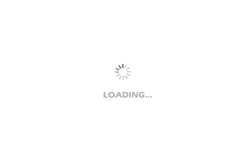
- Huawei's Strategic Department Director Gai Gang: The cumulative installed base of open source Euler operating system exceeds 10 million sets
- Analysis of the application of several common contact parts in high-voltage connectors of new energy vehicles
- Wiring harness durability test and contact voltage drop test method
- Sn-doped CuO nanostructure-based ethanol gas sensor for real-time drunk driving detection in vehicles
- Design considerations for automotive battery wiring harness
- Do you know all the various motors commonly used in automotive electronics?
- What are the functions of the Internet of Vehicles? What are the uses and benefits of the Internet of Vehicles?
- Power Inverter - A critical safety system for electric vehicles
- Analysis of the information security mechanism of AUTOSAR, the automotive embedded software framework
Professor at Beihang University, dedicated to promoting microcontrollers and embedded systems for over 20 years.
- Innolux's intelligent steer-by-wire solution makes cars smarter and safer
- 8051 MCU - Parity Check
- How to efficiently balance the sensitivity of tactile sensing interfaces
- What should I do if the servo motor shakes? What causes the servo motor to shake quickly?
- 【Brushless Motor】Analysis of three-phase BLDC motor and sharing of two popular development boards
- Midea Industrial Technology's subsidiaries Clou Electronics and Hekang New Energy jointly appeared at the Munich Battery Energy Storage Exhibition and Solar Energy Exhibition
- Guoxin Sichen | Application of ferroelectric memory PB85RS2MC in power battery management, with a capacity of 2M
- Analysis of common faults of frequency converter
- In a head-on competition with Qualcomm, what kind of cockpit products has Intel come up with?
- Dalian Rongke's all-vanadium liquid flow battery energy storage equipment industrialization project has entered the sprint stage before production
- Allegro MicroSystems Introduces Advanced Magnetic and Inductive Position Sensing Solutions at Electronica 2024
- Car key in the left hand, liveness detection radar in the right hand, UWB is imperative for cars!
- After a decade of rapid development, domestic CIS has entered the market
- Aegis Dagger Battery + Thor EM-i Super Hybrid, Geely New Energy has thrown out two "king bombs"
- A brief discussion on functional safety - fault, error, and failure
- In the smart car 2.0 cycle, these core industry chains are facing major opportunities!
- The United States and Japan are developing new batteries. CATL faces challenges? How should China's new energy battery industry respond?
- Murata launches high-precision 6-axis inertial sensor for automobiles
- Ford patents pre-charge alarm to help save costs and respond to emergencies
- New real-time microcontroller system from Texas Instruments enables smarter processing in automotive and industrial applications
- ASM330LHH automotive 6-axis inertial module data sheet, application notes, driver code, schematic library, PCB library
- Development board based on TI AM5728 (floating point dual DSP C66x + dual ARM Cortex-A15)
- Agitek High-tech Joint Electronics Laboratory fully supports the National Undergraduate Electronics Design Competition
- Signals and Systems (3rd Edition)
- Can a 100A current flow through a PCB? Tips for setting up high current paths
- hcnr201 isolation circuit problem
- recruitment
- Boot hardware settings
- 2.5V to 6V Input 1.5MHz 2A DC Step-Down Circuit
- 【CODING TALK】How would you implement a queue?