In the previous article on eCall, it was mentioned that Class D audio amplifiers need to pay attention to EMI issues (click to view the article "Audio Application Solutions for In-Vehicle eCall Systems"). Here we will expand on this issue and seek solutions.
1. EMI definition and classification
Electromagnetic interference (EMI) is electronic noise that interferes with cable signals and reduces signal integrity. EMI is usually generated by electromagnetic radiation sources. Electromagnetic interference EMI (Electromagnetic Interference) is divided into two types: conducted interference and radiated interference. Conducted interference refers to the coupling (interference) of a signal on an electrical network to another electrical network through a conductive medium. Radiated interference refers to the coupling (interference) of an interference source's signal to another electrical network through space. In high-speed PCB and system design, high-frequency signal lines, integrated circuit pins, various connectors, etc. may become radiated interference sources with antenna characteristics, which can emit electromagnetic waves and affect the normal operation of other systems or other subsystems within the system.
2. Vehicle system EMI requirements
CISPR25 "Limits and methods of measurement for radio disturbance characteristics of receivers used in vehicles, motor vessels and devices" This standard protects receivers used in vehicles, ships and devices from radio disturbances, and specifies limits and test methods. Currently, almost all vehicle manufacturers are required to pass this relevant standard. The following figure shows the CISPR25 test CEC related test standards and requirements.
Figure 1 CISPR25 CEC test standard description
3. Class D audio amplifier EMI noise source
① Typical application circuit
Figure 2 Typical application diagram of AW836xxTSR-Q1
② Noise source analysis
The EMI interference sources of Class D amplifiers mainly come from three places:
1) Ripple jitter on the power supply caused by the switching modulation frequency during operation 2) Change of large current over time during the switching modulation process di/dt 3) Change of voltage over time during the switching modulation process dv/dt In addition, the layout and wiring of the entire PCB board components will affect the EMI of the entire circuit system. The following will introduce the impact analysis on EMI in the schematic design, the chip design's own EMI suppression function, and the PCB design.
Figure 3 Schematic diagram of noise sources of Class D power amplifier
4. Solutions to EMI
① Schematic design
Power supply noise filtering network design
Common methods for power network noise treatment can be mainly divided into the following three types: 1) Common-mode noise suppression circuit with common-mode inductor 2) Pi-type filter network 3) High-frequency filter circuit composed of magnetic beads and capacitors The specific circuit design can be reasonably selected according to the noise treatment requirements. The main circuit structure is shown in the figure below.
Figure 4 Commonly used power supply noise filtering network Since the current pulses generated by the modulation when the Class D amplifier is working will cause a large voltage ripple on the PVCC pin, if it is not processed, it will be transmitted along the wire to the entire power supply network. As shown in Figure 4, the AW836xxTSR-Q1 power supply network has a PI type filtering design, which can effectively reduce the noise amplitude and high-frequency interference on the power supply. The waveform measured by the oscilloscope is as follows.
Figure 5 Class D modulation introduced
noise
Figure 6 After filtering network processing
noise
Switching noise shaping circuit design
Due to the existence of parasitic parameters such as chip pins, PCB routing, and device stray parameters, switch ringing will occur in the high-frequency switching circuit at the moment of switching action. The existence of ringing may cause the voltage on the switch tube to exceed its withstand voltage value and cause breakdown; on the other hand, the switch ringing is a high-frequency ringing far exceeding the switching frequency, which will be accompanied by a very high dv/dt, thereby causing EMI problems of conduction and radiation. Therefore, suppressing the switch ringing as much as possible is an important link in the design of high-frequency switching circuits. The RC-Snubber circuit composed of resistors and capacitors can effectively suppress the ringing, and thus effectively suppress EMI. Figure 7 shows the switching waveform without the RC-Snubber circuit, and Figure 8 shows the switching waveform with the RC-Snubber circuit. The comparison shows that the high-frequency oscillation is significantly improved. The impact on EMI is shown in Figures 9 and 10. The high-frequency effect is improved from not being able to pass the CLASS5 level to being able to pass the CLASS5 level, and the EMI effect is significantly improved.
Figure 7 Switch ringing caused by
High frequency oscillation
Figure 8 RC-Snubber
Circuit high frequency absorption
Figure 9 EMI test without RC
Figure 10 EMI test with RC added
LC filter circuit design
When designing medium and high power audio, considering the EMI index, it is often necessary to add an LC filter to suppress the modulation signal and high-frequency noise. The cutoff frequency of the LC filter circuit shown in Figure 2 is calculated as follows:
For the low-pass filter circuit, high-frequency signals outside the cutoff frequency will be attenuated at 40dB/Dec.
Figure 11 LC filter circuit suppresses fundamental frequency and harmonics
② Chip EMI suppression function
Modulation frequency selection
Based on the CISPR25 test standard shown in Figure 1, the frequency bands of 300k~530k, 1.8M~5.9M, etc. are not within the test requirements. The AW836xxTSR-Q1 series has launched products with a modulation frequency of 400kHz/500kHz, and will subsequently launch 2.1MHz products (smaller output inductance and output capacitance, lower cost), which can avoid the fundamental wave energy falling within the test range, thereby avoiding the situation where the fundamental wave energy is too large and exceeds the limit. Spread spectrum function
Spread Spectrum (SS) is a communication technology that spreads the spectrum of the transmission signal to a wider bandwidth than its original bandwidth, thereby spreading the energy of the original frequency band to the expanded frequency band to reduce the baseband energy. It is a common means of EMI suppression. The comparison test charts in Figure 13 and Figure 14 show the impact of the spread spectrum function on EMI.
Figure 12 Spread spectrum
Figure 13: Spread spectrum disabled
EMI Test Data
Figure 14: Enable spread spectrum
EMI Test Data
Edge adjustment function
The flip of the output edge of the Class D amplifier brings about a large change of current over time di/dt and voltage over time dv/dt; these will affect the introduction of high-frequency noise. The edge modulation function can adjust the edge rate, thereby reducing the current/voltage change within the Δt time. The comparison test diagrams of Figure 15 and Figure 16 show the impact of the edge modulation function on EMI, and the EMI at high frequencies is significantly optimized.
Figure 15 Default edge rate
EMI Test Data
Figure 16 Edge Mitigation
EMI Test Data
③ PCB design
Reasonable PCB layout, wiring and device selection are crucial to the impact of EMI. AW836xxTSR mainly explains the power network and output power signal.
1) Complete ground reference plane to minimize emission, crosstalk and noise 2) The power supply network should be as short as possible and connected in star shape with other shared voltage networks in the system, avoiding daisy chain and loop formation 3) The power supply network should be kept at a certain distance from the Class D amplifier output network to avoid interference from sensitive devices 4) Avoid 90° bends in routing; 5) The LC filter network and RC-Snubber absorption circuit at the output end should be as close to the chip as possible to reduce the network length before filtering 6) It is recommended that the high-frequency decoupling filter capacitor be placed close to the PVCC pin of the PA and within the minimum loop path to avoid high-frequency decoupling failure 7) When selecting L, try to use fully enclosed inductors to avoid interference or unnecessary loss caused by magnetic coupling due to magnetic leakage 8) Use low ESR & ESL capacitors, and it is recommended that the capacitor ground be connected to the main reference ground as close as possible, with as many vias as possible to reduce parasitic oscillations caused by vias.
Figure 17 AW836xxTSR PCB layout & wiring
Figure 18 Complete ground reference plane
Previous article:How to wirelessly debug in a smart home
Next article:Stereo balance indicator circuit diagram sharing
Recommended ReadingLatest update time:2024-11-16 12:01
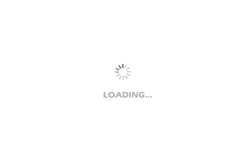
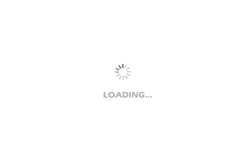
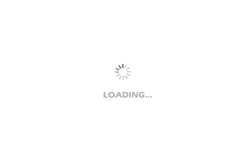
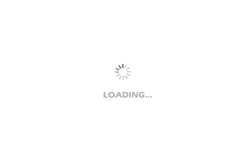
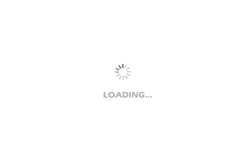
- Popular Resources
- Popular amplifiers
-
Study on the Behavioral Model of Silicon Carbide MOSFET Power Module and EMI Prediction of Low-Voltage Auxiliary Power Supply
-
Cable radiated EMI modeling considering mutual coupling effects_Junpeng Ji
-
Design of broadband hybrid active EMI filter for switching power supply_Liao Yuehong
-
Switching power supply conducted EMI simulation and filter circuit design_Jiang Yunfu
- Huawei's Strategic Department Director Gai Gang: The cumulative installed base of open source Euler operating system exceeds 10 million sets
- Analysis of the application of several common contact parts in high-voltage connectors of new energy vehicles
- Wiring harness durability test and contact voltage drop test method
- Sn-doped CuO nanostructure-based ethanol gas sensor for real-time drunk driving detection in vehicles
- Design considerations for automotive battery wiring harness
- Do you know all the various motors commonly used in automotive electronics?
- What are the functions of the Internet of Vehicles? What are the uses and benefits of the Internet of Vehicles?
- Power Inverter - A critical safety system for electric vehicles
- Analysis of the information security mechanism of AUTOSAR, the automotive embedded software framework
Professor at Beihang University, dedicated to promoting microcontrollers and embedded systems for over 20 years.
- Innolux's intelligent steer-by-wire solution makes cars smarter and safer
- 8051 MCU - Parity Check
- How to efficiently balance the sensitivity of tactile sensing interfaces
- What should I do if the servo motor shakes? What causes the servo motor to shake quickly?
- 【Brushless Motor】Analysis of three-phase BLDC motor and sharing of two popular development boards
- Midea Industrial Technology's subsidiaries Clou Electronics and Hekang New Energy jointly appeared at the Munich Battery Energy Storage Exhibition and Solar Energy Exhibition
- Guoxin Sichen | Application of ferroelectric memory PB85RS2MC in power battery management, with a capacity of 2M
- Analysis of common faults of frequency converter
- In a head-on competition with Qualcomm, what kind of cockpit products has Intel come up with?
- Dalian Rongke's all-vanadium liquid flow battery energy storage equipment industrialization project has entered the sprint stage before production
- Allegro MicroSystems Introduces Advanced Magnetic and Inductive Position Sensing Solutions at Electronica 2024
- Car key in the left hand, liveness detection radar in the right hand, UWB is imperative for cars!
- After a decade of rapid development, domestic CIS has entered the market
- Aegis Dagger Battery + Thor EM-i Super Hybrid, Geely New Energy has thrown out two "king bombs"
- A brief discussion on functional safety - fault, error, and failure
- In the smart car 2.0 cycle, these core industry chains are facing major opportunities!
- The United States and Japan are developing new batteries. CATL faces challenges? How should China's new energy battery industry respond?
- Murata launches high-precision 6-axis inertial sensor for automobiles
- Ford patents pre-charge alarm to help save costs and respond to emergencies
- New real-time microcontroller system from Texas Instruments enables smarter processing in automotive and industrial applications
- DCDC input capacitance waveform
- If anyone is willing to help improve the size of the building block library, we can share the profits in the future.
- EEWORLD University Hall ---- The second stop of the ADI Road theme tour of Shijian: Instruments
- The features of the SCI module are as follows (these functions can be set through the corresponding registers)
- How to implement a multi-protocol communication solution that meets Industry 4.0?
- A very basic question, how to understand the reading timing diagram?
- stm32f1 plays badaplle routine, modify the atomic routine, use vs1053 to decode audio, ucosII to do dual thread
- [New Year's Taste Competition] + Share your New Year's Eve dinner, wishing everyone a happy New Year! All the best!
- Based on AM335X development board ARM Cortex-A8——Acontis EtherCAT master station development case
- Practical sharing: Power management basics