In a domestic operation project of a Shenzhen Automation Co., Ltd., the project requires the control center system to send different command messages to the DC servo drive to control the start and stop and running speed of the drive, thereby controlling the rotation speed of the four servo motors connected to the lower end of the drive. The control center system uses Siemens S7-1200 PLC, which supports the Profinet bus protocol, and the DC servo drive supports the CAN protocol.
Solution:
Since the DC servo drive supports CAN protocol communication when working normally, the control center system Siemens S7-1200 PLC supports Profinet bus protocol communication. As the Profinet master station, the two protocols are different and cannot be directly connected to achieve data exchange. A third-party protocol conversion module is required to achieve data exchange between different protocols.
The Profinet to CAN gateway independently developed and produced by Beijing Bestun Technology can realize the conversion of CAN protocol to Profinet protocol, and well realize the monitoring center system through Siemens S7-1200 PLC. According to the communication command message of the DC servo drive, different commands are sent to control the start and stop and running speed of the servo motor connected to the drive, ensuring that the control center system can remotely control the operation and start and stop of the servo motor, and ensure the smooth implementation of the entire automation project!
Configuration parameter description:
Since the CAN protocol is the bottom layer protocol, the Profinet to CAN gateway has 8 dip switches. When communicating with CAN devices, you only need to use the dip switches to set the CAN baud rate and CAN2.0A or CAN2.0B and select 16 bytes of input and output to achieve CAN communication.
The data format of the Profinet to CAN gateway Profinet end (users do not need to understand, the gateway will handle it automatically) and CAN end is as follows: (refer to the Profinet to CAN manual)
Communication format of CAN device (servo drive):
Since the Profinet and CAN ends of the gateway communicate using 16-byte input and output data formats, in order to ensure the integrity and accuracy of the communication data, the corresponding input and output data lengths need to be configured in the configuration software so that the 16-byte input and output data can communicate in the data block mapped to the IQ address of the PLC, as shown in the figure below.
The data message output by the Profinet master station to the CAN device.
Conclusion:
By using the Profinet to CAN gateway of Bestun Technology Co., Ltd., the control center system can remotely monitor the DC servo drive in real time and then control the start and stop and speed of the servo motor connected to the lower end of the drive, ensuring the feasibility of the project. Profinet to CAN runs stably and reliably throughout the project!
Previous article:What is the waveform of the inverter output voltage? How to control the motor through pulse modulation technology?
Next article:PLC system power supply installation & wiring tips sharing
Recommended ReadingLatest update time:2024-11-16 09:45
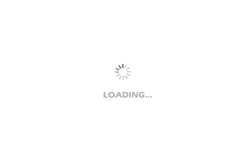
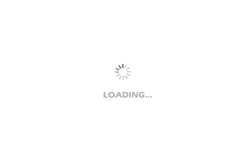
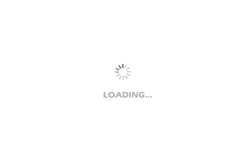
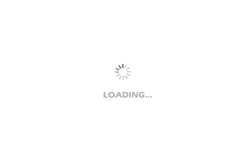
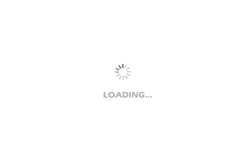
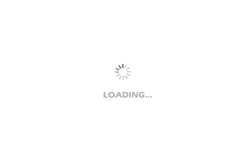
- Popular Resources
- Popular amplifiers
- Huawei's Strategic Department Director Gai Gang: The cumulative installed base of open source Euler operating system exceeds 10 million sets
- Analysis of the application of several common contact parts in high-voltage connectors of new energy vehicles
- Wiring harness durability test and contact voltage drop test method
- Sn-doped CuO nanostructure-based ethanol gas sensor for real-time drunk driving detection in vehicles
- Design considerations for automotive battery wiring harness
- Do you know all the various motors commonly used in automotive electronics?
- What are the functions of the Internet of Vehicles? What are the uses and benefits of the Internet of Vehicles?
- Power Inverter - A critical safety system for electric vehicles
- Analysis of the information security mechanism of AUTOSAR, the automotive embedded software framework
Professor at Beihang University, dedicated to promoting microcontrollers and embedded systems for over 20 years.
- Innolux's intelligent steer-by-wire solution makes cars smarter and safer
- 8051 MCU - Parity Check
- How to efficiently balance the sensitivity of tactile sensing interfaces
- What should I do if the servo motor shakes? What causes the servo motor to shake quickly?
- 【Brushless Motor】Analysis of three-phase BLDC motor and sharing of two popular development boards
- Midea Industrial Technology's subsidiaries Clou Electronics and Hekang New Energy jointly appeared at the Munich Battery Energy Storage Exhibition and Solar Energy Exhibition
- Guoxin Sichen | Application of ferroelectric memory PB85RS2MC in power battery management, with a capacity of 2M
- Analysis of common faults of frequency converter
- In a head-on competition with Qualcomm, what kind of cockpit products has Intel come up with?
- Dalian Rongke's all-vanadium liquid flow battery energy storage equipment industrialization project has entered the sprint stage before production
- Allegro MicroSystems Introduces Advanced Magnetic and Inductive Position Sensing Solutions at Electronica 2024
- Car key in the left hand, liveness detection radar in the right hand, UWB is imperative for cars!
- After a decade of rapid development, domestic CIS has entered the market
- Aegis Dagger Battery + Thor EM-i Super Hybrid, Geely New Energy has thrown out two "king bombs"
- A brief discussion on functional safety - fault, error, and failure
- In the smart car 2.0 cycle, these core industry chains are facing major opportunities!
- The United States and Japan are developing new batteries. CATL faces challenges? How should China's new energy battery industry respond?
- Murata launches high-precision 6-axis inertial sensor for automobiles
- Ford patents pre-charge alarm to help save costs and respond to emergencies
- New real-time microcontroller system from Texas Instruments enables smarter processing in automotive and industrial applications
- Silicon carbide industry chain science video: substrate and epitaxy
- Share an open source software download URL
- "Practice Together in 2021" + Looking Forward
- Senior foreigner explains the misunderstandings of high-speed PCB design and testing (video-Chinese)
- After zigbee sends data to nb-iot, nb-iot sends data to the cloud, but the data displayed on the cloud is completely wrong. How to solve it?
- Notice: The new markdown editor is now online!!
- Design of password lock using AT89S52 single chip microcomputer
- [Review of Arteli Development Board AT32F421] + Have a good understanding of the power supply voltage
- 【Development and application based on NUCLEO-F746ZG motor】4. Share information
- encryption