How to choose between a programmable logic controller (PLC) and a distributed control system (DCS) requires specific analysis of the specific situation, because different application scenarios have different requirements for control systems. When we communicate with customers, we can start from the following aspects!
PLC and DCS
PLC
1. From switch quantity control to sequence control and transportation processing, it is a multi-function such as continuous PID control from bottom to top, and PID is in the interrupt station.
2. One PC can be used as the master station and multiple PLCs of the same type can be used as slave stations.
3. One PLC can be the master station and multiple PLCs of the same type can be slave stations to form a PLC network. This is more convenient than using a PC as the master station: when the user is programming, he does not need to know the communication protocol, but only needs to write according to the manual format.
4. PLC grid can be used as both an independent DCS and a subsystem of DCS.
5. PLC is mainly used for sequential control in industrial processes, and new PLCs also have closed-loop control functions.
DCS
1. Distributed Control System DCS
Monitoring technology that integrates 4C (Communication, Computer, Control, CRT) technology.
2. A large system with a tree topology from top to bottom, where communication is the key.
3. PID is in the interrupt station. The interrupt station connects the computer with the field instruments and control devices in a tree topology and a parallel continuous link structure. There are also a large number of cables running in parallel from the interrupt station to the field instruments.
4. Analog signal, A/D---D/A, mixed with microprocessor.
5. A pair of wires of an instrument is connected to I/O, and the control station is connected to the LAN
6. DCS is a three-level structure of control (engineer station), operation (operator station), and field instrument (field measurement and control station). It is used for large-scale continuous process control, such as petrochemical, etc.
How to choose between PLC and DCS system
The choice between a programmable logic controller (PLC) and a distributed control system (DCS) requires a case-by-case analysis, because different applications have different requirements for the control system.
The control system platform has an impact on how the automation system meets the needs of optimizing production, maintaining availability and acquiring data. Lack of foresight in the selection of control systems may also affect future expansion, process optimization, user satisfaction and company profits.
In addition to basic guidelines, such as how to control the process, the design team must also consider installation, scalability, maintenance, and other factors.
At present, although PLC systems may be the most cost-effective for small equipment, DCS systems provide more economical scalability and are more likely to achieve a higher return on initial investment.
A PLC is an industrial computer used to control manufacturing processes such as robotics, high-speed packaging, bottling, and motion control. Over the past 20 years, PLCs have added more features and created more benefits for small factories and installations. PLCs usually operate as stand-alone systems, but can also be integrated with other systems and connected to each other via communications. Since each PLC has its own database, integration requires some degree of mapping between controllers. This makes PLCs particularly suitable for small applications that do not have much demand for expansion.
The DCS system disperses the controllers in the automation system and provides common interfaces, advanced control, system-level databases, and easy-to-share information. Traditionally, DCS is mainly used in process technology and larger plants. Large system applications are easier to maintain throughout the life cycle of the plant.
PLC is developed from the principle of relay control. It stores instructions for executing logical operations, sequential control, timing, counting and calculation, and controls various machines or production processes through digital input and output operations. The control program compiled by the user expresses the process requirements of the production process and is stored in the user program memory of the PLC in advance. During operation, the stored program is executed one by one to complete the operations required by the process flow.
Comparison of Engineering Analysis between PLC and DCS
The CPU of the PLC has a program counter that indicates the storage address of the program step. During the program running process, the counter automatically increases by 1 after executing a step. The program is executed from the starting step (step number is zero) to the final step (usually the end instruction), and then returns to the starting step for loop operation. The time required for the PLC to complete a loop operation is called a scan cycle. The loop scan cycle of different models of PLCs ranges from 1 microsecond to tens of microseconds. The program counter has such a loop operation, which is not available in the DCS. This is also the reason why the redundancy of the PLC is not as good as that of the DCS.
DCS was developed on the basis of operational amplifiers. All functions and relationships between process variables are made into functional blocks (some DCS systems call them expanded blocks). The main difference between DCS and PLC is in the logical solution of switch quantities and the operation of analog quantities. Even though the two have been somewhat intertwined, there are still differences.
After the 1980s, in addition to logical operations, the algorithm function of the control loop of PLC has been greatly enhanced. However, PLC uses ladder diagram programming, and the operation of analog quantity is not very intuitive during programming, which is more troublesome. However, in terms of solving logic, it has the advantage of being fast, at the microsecond level, solving 1k logic program in less than 1 millisecond. It treats all inputs as switch quantities, and 16 bits (or 32 bits) is an analog quantity.
DCS treats all inputs as analog quantities, and 1 bit is a switch quantity. It takes hundreds of microseconds to several milliseconds to solve a logic. For PLC, it takes tens of milliseconds to solve a PID operation, which is comparable to the operation time of DCS.
In terms of grounding resistance, the requirements for PLC may not be high, but for DCS it must be below a few ohms (usually below 4 ohms). Analog isolation is also very important.
For systems with the same number of i/o points, the cost of using PLC is lower than that of using DCS (about 40% can be saved). PLC does not have a dedicated operation station, and the software and hardware it uses are universal, so the maintenance cost is much lower than that of DCS. If the controlled objects are mainly equipment interlocking and the loops are relatively few, it is more appropriate to use PLC.
If the control is mainly analog and there are many function operations, it is best to use DCS. DCS is much better than PLC in terms of redundancy of controllers, I/O boards, communication networks, some advanced operations, and special requirements of the industry. PLC is easier to design the management information system of the enterprise because it uses general monitoring software.
PLC and DCS systems are generally applicable to discrete and process manufacturing, respectively. Discrete manufacturing facilities that use PLC systems are generally composed of separate production units, mainly used to complete the assembly of parts, such as labeling, filling or grinding. Process manufacturing facilities usually use automation systems to produce according to recipes rather than pieces in a continuous and batch manner. Large continuous processing equipment, such as refineries and chemical plants, use DCS automation systems. Hybrid applications often use both PLC systems and DCS systems. When selecting a controller for an application, many factors need to be considered, such as the scale of the process, scalability and future update plans, integration requirements, functionality, high availability, and return on investment over the entire life cycle of the plant facility.
Factors that influence your decision
Process size: How many input/output (I/O) points are needed? Small systems (<300 I/O points) may have a smaller budget, so a PLC system is more suitable. It is not easy to apply a DCS system to a smaller project. On the contrary, it can better play its role in large factory applications. Because it has a global database, the DCS system is easier to manage and upgrade, and any changes are global.
Upgrade plan: Smaller industrial processes can be adapted to PLC systems, but if the process needs to be expanded or upgraded, more PLC hardware and databases will need to be added and maintained separately. This is a time-consuming, labor-intensive process that is prone to errors. DCS systems are easier to upgrade, such as user trust can be managed from a central hub, so they are easier to maintain and maintain (see Figure 1).
Figure 1: DCS system architecture with a single database that allows users to maintain and operate the system from a central control station
Integration requirements: For stand-alone devices, PLC systems are ideal. When a plant is equipped with multiple PLC systems, there is a need for interconnection. This is generally difficult to achieve because data mapping is usually required using communication protocols. Integration is of course no problem, but when there is a need for change, the user's trouble comes: once a PLC system is changed, it may cause the two PLCs to not communicate properly because the data mapping is affected. For DCS systems, there is no need for mapping at all, and configuration changes are just a simple process; the controller is built into the system.
Previous article:Scaling and standardization of Siemens S7-1200PLC data processing instructions
Next article:A brief analysis of KUKA robot system variables and system files
Recommended ReadingLatest update time:2024-11-16 12:47
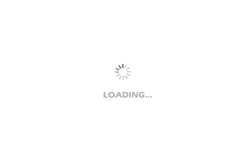
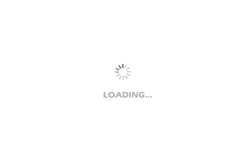
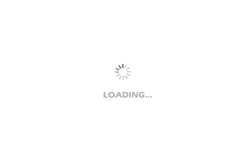
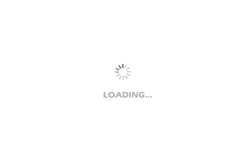
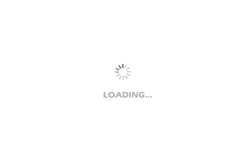
- Popular Resources
- Popular amplifiers
- Huawei's Strategic Department Director Gai Gang: The cumulative installed base of open source Euler operating system exceeds 10 million sets
- Analysis of the application of several common contact parts in high-voltage connectors of new energy vehicles
- Wiring harness durability test and contact voltage drop test method
- Sn-doped CuO nanostructure-based ethanol gas sensor for real-time drunk driving detection in vehicles
- Design considerations for automotive battery wiring harness
- Do you know all the various motors commonly used in automotive electronics?
- What are the functions of the Internet of Vehicles? What are the uses and benefits of the Internet of Vehicles?
- Power Inverter - A critical safety system for electric vehicles
- Analysis of the information security mechanism of AUTOSAR, the automotive embedded software framework
Professor at Beihang University, dedicated to promoting microcontrollers and embedded systems for over 20 years.
- Innolux's intelligent steer-by-wire solution makes cars smarter and safer
- 8051 MCU - Parity Check
- How to efficiently balance the sensitivity of tactile sensing interfaces
- What should I do if the servo motor shakes? What causes the servo motor to shake quickly?
- 【Brushless Motor】Analysis of three-phase BLDC motor and sharing of two popular development boards
- Midea Industrial Technology's subsidiaries Clou Electronics and Hekang New Energy jointly appeared at the Munich Battery Energy Storage Exhibition and Solar Energy Exhibition
- Guoxin Sichen | Application of ferroelectric memory PB85RS2MC in power battery management, with a capacity of 2M
- Analysis of common faults of frequency converter
- In a head-on competition with Qualcomm, what kind of cockpit products has Intel come up with?
- Dalian Rongke's all-vanadium liquid flow battery energy storage equipment industrialization project has entered the sprint stage before production
- Allegro MicroSystems Introduces Advanced Magnetic and Inductive Position Sensing Solutions at Electronica 2024
- Car key in the left hand, liveness detection radar in the right hand, UWB is imperative for cars!
- After a decade of rapid development, domestic CIS has entered the market
- Aegis Dagger Battery + Thor EM-i Super Hybrid, Geely New Energy has thrown out two "king bombs"
- A brief discussion on functional safety - fault, error, and failure
- In the smart car 2.0 cycle, these core industry chains are facing major opportunities!
- The United States and Japan are developing new batteries. CATL faces challenges? How should China's new energy battery industry respond?
- Murata launches high-precision 6-axis inertial sensor for automobiles
- Ford patents pre-charge alarm to help save costs and respond to emergencies
- New real-time microcontroller system from Texas Instruments enables smarter processing in automotive and industrial applications
- 【Silicon Labs Development Kit Review】+ Get familiar with the development environment and download the breathing light routine
- EEWORLD University ---- Interoperability of isolated CAN FD nodes
- Horizontal evaluation of 39 mainstream synchronous rectification DCDC chips on the market
- How are soft-start circuits for power supplies, motors, and other equipment usually implemented?
- The clock signal is followed by an inverter.
- EEWORLD University Hall----Live Replay: TI Wireless Product Update: Wi-Sun Standard Helps Smart City Construction
- TI automotive solution puzzle, do you dare to challenge it?
- [SAMR21 new gameplay] 8. Serial communication-1
- Mobile station update development board, welcome to borrow it!!
- 3. "Wanli" Raspberry Pi car - Python learning (timing task)